1 Introduction
Traditional data acquisition systems generally use single-chip microcomputers, and most systems complete data transmission through the PCI bus. Its disadvantages are poor mathematical computing capabilities; limited by the number of computer slots and interrupt resources; inconvenient to connect and install; and susceptible to the electromagnetic environment in the chassis. These problems have curbed the further development and application of data acquisition systems based on the PCI bus. Therefore, a simpler and more universal way is needed to complete the interaction between the acquisition system and computer data.
The performance of the data acquisition system mainly depends on its accuracy and speed. The sampling speed should be increased as much as possible under the condition of ensuring accuracy to meet the requirements of real-time acquisition, real-time processing and real-time control. Practice shows that the data acquisition system composed of ARM 32-bit embedded microprocessor as controller and USB (Universal Serial Bus) and host computer connection can greatly improve the system data processing capability and reduce the dependence on PC and interface speed.
2 System Hardware Design
The basic idea of realizing the system function is to use CPLD/FPGA to realize the digital platform of the instrument, and to realize the intelligent control and high-speed data processing of the whole machine together with the ARM embedded processor and single-chip microcomputer.
2.1 System Block Diagram
The system principle block diagram is shown in Figure 1. The system is mainly composed of modules such as microprocessor, digital logic platform, input control, A, B channel input processing, C channel input processing, shaping, A/D conversion, sampling timing control, keyboard LCD display , and memory expansion.
2.2 System Structure Diagram
The system hardware is shown in Figure 2. A small-scale CPLD and a large-scale FPGA are combined to form the digital logic platform of the system. The CPLD is mainly used for input control, and the FPGA connects other parts of the system. CPLD/FPGA can realize on-site programming. Using CPLD/FPGA can make the design convenient. Its flexibility, fast verification and design can be changed at will can greatly shorten the development time.
2.3 Main functions
2.3.1 Microprocessor
The system uses the ARM 32-bit microprocessor LPC2105 produced by Philips as the main CPU for high-speed data processing, and uses the 8-bit microcontroller P89C51RD2 as the auxiliary CPU for slower data processing, controlling other peripheral chips and modules to realize the data acquisition functions of A and B channel analog bandwidth 100 MHz, peak voltage ±100 V and C channel diode on/off, voltage, current, and resistance value.
2.3.2 A, B channel part
The measured analog signal is conditioned to a range suitable for sampling by the ADC chip (AD9288) through an automatic gain circuit (AGC), i.e., a program-controlled amplifier. According to the frequency and triggering mode, the conditioned analog signal is sampled (A/D conversion) using real-time sampling or equivalent sampling. The sampled data is stored in a high-speed FIFO memory (IDT72V261LA10A).
Combined with keyboard operation and system settings, mathematical operations are performed on the sampled data, and the restored waveform data and parameters are sent to the LCD display for display or stored in the flash memory or transmitted to the PC through the USB interface, thereby realizing the function of high-speed data acquisition of A and B channels.
2.3.3 C channel part
The C input channel is a multifunctional input channel. The system selects different modules to measure voltage, current or the on/off and resistance of diodes by controlling the relay matrix. After the measured component parameters or voltage and current are processed by the multifunctional conversion circuit, the signals are sent to the 24b A/D converter ADS1211 for sampling and then sent to the single-chip microcomputer P89C51RD2 to analyze the parameter values of the measured component or voltage and current, thus realizing the function of high-precision data acquisition of the C channel.
2.3.4 Keyboard and LCD display interface circuit
This system uses a 4×8 keyboard and a 320×240 LCD display module without a driver. The driver and video memory are designed in the FPGA. The above system communicates with the PC through the USB interface and realizes a visual human-computer interaction interface under the control of the host computer. At the same time, the system also retains the traditional RS 232 interface, but it is only used for programming and downloading of ARM and single-chip microcomputers.
3 Software Design Process
The LPC2105 chip serves as the main control center and data processing center of the system. The operation of the entire system is controlled by it, such as responding to user key operations, issuing channel control, A/D sampling clock control, FIFO write clock selection, menu and system status display, FIFO data processing, automatic testing of signals or parameters, etc.
The software program structure of the data acquisition card is shown in Figure 3, which can be divided into system initialization module, key analysis module, system core control module, channel control module, trigger control module, A/D sampling control module, FIFO read and write control module, frequency word reading module, parameter test module, status display module, waveform display module, storage control module, and other functional modules.
The system initialization module includes power-on self-test, hardware parameter initialization, system status initialization (such as channel waveform display status initialization), etc. The key analysis module analyzes and processes the user input on the panel, calls the corresponding function processing module through the core control module, and realizes the processing function from the key analysis by calling the channel control module, trigger control module, A/D sampling control module, FIFO read and write control module, frequency word reading module, parameter test module, status display module, waveform display module, storage control module, and other function modules. The status display module displays various states of the program when it is running, such as the current data acquisition scanning rate, the vertical sensitivity of the channel, etc. The waveform display module displays the acquired waveform.
The program of the whole system can be divided into the bottom layer driver and the upper layer software. The bottom layer driver refers to the program part that directly controls or accesses other peripherals or devices of the system, including the initialization of LPC2105 and the microcontroller (i.e., the operation assignment of each core register in the chip, the initialization assignment of the on-chip peripherals, and the control operation of each peripheral interrupt in the chip and the external interrupt). The upper layer software mainly refers to: menu design and display, data processing, waveform recovery and smoothing, etc.
4 System Performance Indicators
4.1 Performance indicators of A and B channels
(1) Analog signal bandwidth: 100 MHz (40 dB);
(2) Maximum real-time sampling rate: 100.MS/s;
(3) Maximum equivalent sampling rate: 5 GS/s;
(4) Vertical resolution: 8 b;
(5) Vertical sensitivity: 5 mV/div~25 V/diV;
(6) Horizontal scan: 5 ns/div~10 s/div;
(7) Maximum input voltage: (AC+DC) ±100 Vpp;
(8) Input RC: 1 MΩ ± 1.5% / 20 pF ± 3 pF;
(9) Coupling mode: DC, AC, grounding;
(10) Trigger mode: AC, DC, high frequency suppression, low frequency suppression;
(11) Trigger source: A, B;
(12) Storage depth: 16K/channel;
(13) Display mode: A, -A, B, -B, AB, A+B;
(14) Measurement signal parameters: period, frequency, average value, effective value, peak value, root mean square value, minimum value, maximum value, rise time, fall time, positive bandwidth, negative bandwidth, duty cycle;
(15) Measurement accuracy: ±5%;
(16) Calibration signal: 1 kHz/3.3 V.
2 C channel performance indicators
(1) Measuring resistance: 100 Ω, 1 kΩ, 10 kΩ, 100 kΩ, 1 MΩ;
(2) Measurement voltage: 10 mV, 30 mV, 1 V, 3 V, 10 V, V:
(3) Measurement current: 200 mA, 1 A;
(4) Diode: on-off measurement;
(5) Measurement accuracy: ±3%.
5 Conclusion
This system adopts the design of ARM+single-chip microcomputer+CPLD/FPGA. Its high-speed data processing task can be completed independently by the lower computer, and the system has a large-screen LCD display, so it can be used normally without the PC in the case of power failure. The acquisition card has the functions of real-time acquisition, automatic storage, instant display, instant feedback, automatic processing, automatic transmission, etc. It provides a guarantee for the authenticity, validity, immediacy and availability of field data, and can be easily input into the computer. It can be applied to intelligent instrumentation, industry, agriculture, commerce, transportation, logistics, warehousing and other industries.
Previous article:Integrating analog components with Arm microcontroller cores to solve embedded system problems
Next article:A Brief Analysis of Three Widely Used Embedded Operating Systems on ARM CPU
Recommended ReadingLatest update time:2024-11-23 03:15
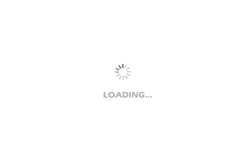
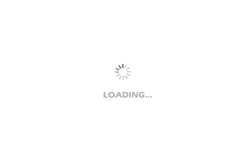
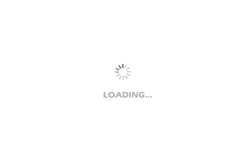
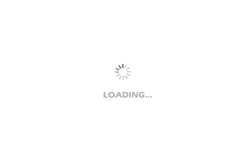
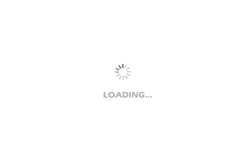
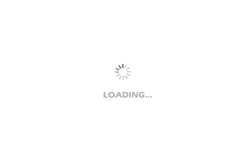
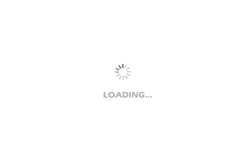
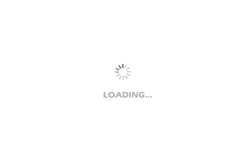
- Popular Resources
- Popular amplifiers
-
FPGA implementation of FIR filter
-
Analysis and Implementation of MAC Protocol for Wireless Sensor Networks (by Yang Zhijun, Xie Xianjie, and Ding Hongwei)
-
Wireless Sensor Network Technology and Applications (Edited by Mou Si, Yin Hong, and Su Xing)
-
MATLAB and FPGA implementation of wireless communication
- Naxin Micro and Xinxian jointly launched the NS800RT series of real-time control MCUs
- How to learn embedded systems based on ARM platform
- Summary of jffs2_scan_eraseblock issues
- Application of SPCOMM Control in Serial Communication of Delphi7.0
- Using TComm component to realize serial communication in Delphi environment
- Bar chart code for embedded development practices
- Embedded Development Learning (10)
- Embedded Development Learning (8)
- Embedded Development Learning (6)
Professor at Beihang University, dedicated to promoting microcontrollers and embedded systems for over 20 years.
- Intel promotes AI with multi-dimensional efforts in technology, application, and ecology
- ChinaJoy Qualcomm Snapdragon Theme Pavilion takes you to experience the new changes in digital entertainment in the 5G era
- Infineon's latest generation IGBT technology platform enables precise control of speed and position
- Two test methods for LED lighting life
- Don't Let Lightning Induced Surges Scare You
- Application of brushless motor controller ML4425/4426
- Easy identification of LED power supply quality
- World's first integrated photovoltaic solar system completed in Israel
- Sliding window mean filter for avr microcontroller AD conversion
- What does call mean in the detailed explanation of ABB robot programming instructions?
- STMicroelectronics discloses its 2027-2028 financial model and path to achieve its 2030 goals
- 2024 China Automotive Charging and Battery Swapping Ecosystem Conference held in Taiyuan
- State-owned enterprises team up to invest in solid-state battery giant
- The evolution of electronic and electrical architecture is accelerating
- The first! National Automotive Chip Quality Inspection Center established
- BYD releases self-developed automotive chip using 4nm process, with a running score of up to 1.15 million
- GEODNET launches GEO-PULSE, a car GPS navigation device
- Should Chinese car companies develop their own high-computing chips?
- Infineon and Siemens combine embedded automotive software platform with microcontrollers to provide the necessary functions for next-generation SDVs
- Continental launches invisible biometric sensor display to monitor passengers' vital signs
- Vehicle Occupant Detection Reference Design
- TMS320VC33 Study Notes Development Environment
- SPI communication between FPGA and STM32
- ST bluDFU, can you provide the source code of this upgrade app?
- What benefits can 5G bring? Welcome to leave a message and give points for good posts
- About energy conservation and emission reduction of new energy vehicles...
- ZYNQ cannot be burned to NAND Flash via JTAG
- Qorvo based small PA introduction series
- .Power amplifier circuit
- Watch for free: How to solve the 32.0 GT/s PCIe5 test? Two experts reveal the secrets for you