Samsung Electronics' investment plans and ambitious goals
On April 24, 2019, Samsung Electronics announced its future investment plans and goals. Samsung Electronics' investment plan is to invest 133 trillion won (about 120 billion U.S. dollars) in the next 12 years (1999 to 2030) to strengthen the competitiveness of system LSI and wafer foundry business and expand non-memory business. Among them: 73 trillion won (about 66 billion U.S. dollars) in domestic research and development, 60 trillion won (about 54 billion U.S. dollars) in production infrastructure, and an average annual investment of 11 trillion won (about 10 billion U.S. dollars) is expected.
In general, Samsung Electronics' goal is to maintain its number one position in the world in memory chips, while dethroning TSMC in the foundry field, defeating Sony in the CMOS image sensor field, maintaining its lead over Intel in terms of revenue, and securing its position as the world's largest semiconductor manufacturer.
Development History of Samsung Electronics Semiconductor Division
The Semiconductor Business Division of Samsung Electronics Co., Ltd. refers to the Memory Department, System LSI Department and Foundry Department under the Device Solution Business Group; the memory includes DRAM and NAND Flash, and the system logic chips include system-on-chip SOC, image sensor CIS, display driver chips, smart card chips, and power management chips.
Samsung Electronics' semiconductor business division's annual revenue accounts for approximately 30% of Samsung Electronics' total revenue. For the terminal products of Samsung Electronics' two major business divisions, IT & Mobile and Consumer Electronics, it plays an important role in widening the gap with lagging competitors, narrowing the gap with leading companies, and strengthening the differentiation of key terminal products.
Samsung Electronics was founded in 1969. In 1974, it acquired 50% of Hankook Semiconductor's shares and established the Semiconductor Division, entering the semiconductor industry. In 1975, it developed watch chips. In July 1977, it began to produce bipolar transistors. In 1979, it acquired a wholly-owned subsidiary of Hankook Semiconductor and changed its name to Samsung Semiconductor. In 1983, it officially entered the memory industry and developed Korea's first 64K DRAM. In 1988, the semiconductor business and the electronics and wireless communications business were merged to form Samsung Electronics. In 1994, it began to develop DSP. In 1995, it launched the first 8-bit MCU. In 1997, it launched the 700MHz Alpha processor. In 2000, it released the 0.25µm 66MHz mobile phone application processor S3C44B0X. In 2002, it established the SoC R&D Center. In 2005, it entered the CMOS sensor field and started the wafer foundry business.
Samsung Semiconductor has seven major production bases around the world, located in Giheung, South Korea, Hwaseong, South Korea, Anyang, South Korea, Pyeongtaek, South Korea, Austin, the United States, Suzhou, China, and Xi'an, China.
Samsung Electronics' semiconductor division is currently the world's largest memory chip manufacturer, ranking first in global revenue in 2018.
Strengthening wafer foundry and replacing TSMC
1. Development History of Samsung Electronics Foundry
In 2005, Samsung Electronics began to enter the 12-inch logic process wafer foundry field, and it has been 15 years since then. By focusing on advanced process nodes and striving to provide customers with the most optimized products and services, the wafer foundry business has now grown into one of the low-power, high-performance SOC foundry companies for the global FABLESS industry.
From 2005 to 2009, Samsung Electronics' foundry revenue was less than $400 million. In 2010, it took on Apple and began to manufacture Apple's A series processors (including A4, A5, A6, and A7). The foundry operating income increased dramatically, and in 2010, the overall foundry revenue surged to $1.2 billion (of which the foundry revenue of Apple's A series processor products reached $800 million). Due to the surge in shipments of mobile terminal products such as Apple mobile phones, Samsung Electronics' wafer foundry revenue also rose, reaching $3.95 billion in 2013. In that year, Apple's foundry revenue accounted for 86% of the company's total foundry revenue. It can be said that Samsung Electronics' foundry revenue from 2010 to 2013 was completely supported by Apple.
Due to the inability to break through the yield rate of the 20nm process and other reasons, Samsung Electronics lost Apple's A series processor orders in 2014, and Apple's A8 processors were all outsourced to TSMC. In 2015, Samsung finally got some orders for the A9 processors, but because the yield rate and power consumption control were not as good as TSMC, the A10 processors in 2016 were all outsourced to TSMC. Due to the loss of Apple as a major customer, the wafer foundry revenue declined in 2014 and 2015.
In order to fill the capacity, Samsung Electronics' foundry department actively attacked and grabbed orders for Qualcomm's application processors and server chips, AMD's microprocessor chips, Nvidia's graphics processing chips, Ambarella's visual processing chips, and Tesla's self-driving system chips, making up for Apple's lack of orders. In 2016, the revenue reached US$4.4 billion, exceeding the level of 2013, setting a new record for Samsung Electronics' wafer foundry revenue.
2. Wafer foundry split
On May 12, 2017, Samsung Electronics announced the adjustment of its business divisions, separating the foundry business division from the system LSI business division to form Samsung Electronics Foundry. It is reported that the new division is mainly responsible for manufacturing non-memory chips for global customers such as Qualcomm and Nvidia, thereby competing with pure foundry companies led by TSMC.
According to data from market research firm IC Insights, Samsung Electronics' wafer foundry revenue reached US$4.6 billion in 2017, ranking fourth in the global wafer foundry market with a 6% market share. The top three are TSMC with 56%, GlobalFoundries with 9%, and UMC with 8.5%. In 2018, the wafer foundry revenue reached US$10 billion, with a market share of 14%, ranking second in the world.
Samsung Electronics ranked second in the world in 2018, not because of a big increase in performance, but because of the split of departments. The reason is that the foundry department has become an independent company and is no longer affiliated with the system LSI business. Therefore, the production revenue of processor chips (Exynos, etc.), CIS image sensors, display driver chips, and power management chips are now counted as the revenue of the foundry department, so the revenue has been rising all the way, and the market share has soared overnight.
But don’t underestimate Samsung’s wafer foundry because of this.
Next, let’s talk about Samsung Electronics’ wafer foundry production capacity and processes.
3. Wafer foundry and production capacity
As of the end of 2018, Samsung Electronics had five dedicated wafer foundry lines, including four 12-inch lines and one 8-inch line.
S1 in Kiheung, South Korea, was built in 2005 and is Samsung's first 12-inch logic foundry production line. It currently mass-produces 65-nanometer to 8-nanometer low-power chips. Its products are mainly used in computer networks, smartphones, automobiles, and the growing Internet of Things market.
S2 in Austin, USA, was transformed from an original 8-inch plant. Cleanroom construction began in August 2010, and 12-inch logic product production began in April 2011, reaching a production capacity of 43,000 pieces that year. Currently, 65-nanometer to 14-nanometer products are in mass production. In 2010, a research and development center was established to develop high-performance, low-power, complex CPU and system IP architecture and design for the system LSI department.
S3 in Hwasung, South Korea, is a 12-inch logic production line that was completed and put into production in 2018. It currently mainly produces 10nm to 8nm products and will be the main production plant for Samsung's 7nm products.
S4 in Hwaseong, South Korea, is a transformation of the original DRAM production line FAB11, and is currently a dedicated production line for CMOS image sensors (CIS). The 12-inch DRAM production line FAB13 in Hwaseong is also being transformed into a dedicated production line for CMOS image sensors.
The EUV dedicated production line in Hwaseong, South Korea, has been under construction since it started construction in February 2018. The plant will invest $6 billion, will be completed in the second half of next year, and will be officially put into production in 2020. In the initial stage, it will focus on 7-nanometer products, supplemented by EUV lithography machines.
South Korea's Giheung's 8-inch wafer foundry line FAB 6 was opened in 2016, covering nodes from 180 nanometers to 70 nanometers. Its process technologies include embedded flash memory (eFlash), power components, image sensors CIS, and high-voltage process production, mainly targeting South Korea's local FABLESS.
Currently, Samsung Electronics' foundry business can provide 65nm, 45nm, 32/28nm HKMG, 14nm FinFET, 10nm FinFET, and 7nm FinFET EUV processes. Its customers include Apple, Qualcomm, AMD, Xilinx, NVIDIA, NXP, and Korean local company Telechips.
By the end of 2019, Samsung Electronics' dedicated wafer foundry lines will increase to seven, including six 12-inch lines and one 8-inch line.
4. Wafer foundry technology: the pursuit of advanced processes never stops
Samsung Electronics entered the foundry industry in 2005; signed a 65nm contract with its first customer in 2006; started taking orders for 45nm process in 2009, and established a logic process development team at the Semiconductor Research Institute in November of the same year to strengthen its foundry business; and launched the first 32nm HKMG process in January 2010.
Due to the loss of Apple orders, Samsung has increased its investment in process research and development in an attempt to prove its technological leadership.
Previous article:Shiqiang Components e-commerce launched clock customization burning service
Next article:Lam Research Sets New Productivity Record for Self-Maintained Equipment
Recommended ReadingLatest update time:2024-11-15 16:28
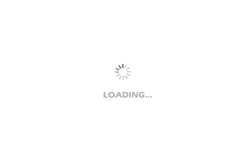
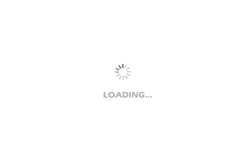
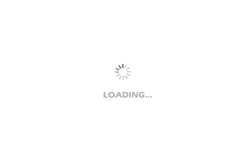
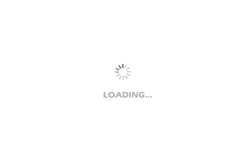
- Popular Resources
- Popular amplifiers
- Vietnam's chip packaging and testing business is growing, and supply-side fragmentation is splitting the market
- The US asked TSMC to restrict the export of high-end chips, and the Ministry of Commerce responded
- ASML predicts that its revenue in 2030 will exceed 457 billion yuan! Gross profit margin 56-60%
- ASML provides update on market opportunities at 2024 Investor Day
- It is reported that memory manufacturers are considering using flux-free bonding for HBM4 to further reduce the gap between layers
- Intel China officially releases 2023-2024 Corporate Social Responsibility Report
- Mouser Electronics and Analog Devices Launch New E-Book
- AMD launches second-generation Versal Premium series: FPGA industry's first to support CXL 3.1 and PCIe Gen 6
- SEMI: Global silicon wafer shipment area increased by 6.8% year-on-year and 5.9% month-on-month in 2024Q3
- LED chemical incompatibility test to see which chemicals LEDs can be used with
- Application of ARM9 hardware coprocessor on WinCE embedded motherboard
- What are the key points for selecting rotor flowmeter?
- LM317 high power charger circuit
- A brief analysis of Embest's application and development of embedded medical devices
- Single-phase RC protection circuit
- stm32 PVD programmable voltage monitor
- Introduction and measurement of edge trigger and level trigger of 51 single chip microcomputer
- Improved design of Linux system software shell protection technology
- What to do if the ABB robot protection device stops
- Huawei's Strategic Department Director Gai Gang: The cumulative installed base of open source Euler operating system exceeds 10 million sets
- Download from the Internet--ARM Getting Started Notes
- Learn ARM development(22)
- Learn ARM development(21)
- Learn ARM development(20)
- Learn ARM development(19)
- Learn ARM development(14)
- Learn ARM development(15)
- Analysis of the application of several common contact parts in high-voltage connectors of new energy vehicles
- Wiring harness durability test and contact voltage drop test method
- You must master this picture when doing RF
- Could you please tell me the meaning and function of near and far in rl78 microcontroller?
- Recommended: Domestically designed chips AD and DA, currently the highest 6-bit 32G chip
- Introduction of 5v-30v conversion circuit
- Interrupt Types of TMS320C6000 Series DSP
- Review summary: DIY creative show based on USB PD power receiving protocol chip CH224
- pads95 bus wiring
- What type of device is the silk screen printed on the picture?
- It’s almost the end of the year, do you have any new plans for the New Year?
- Huawei Ethernet Clock Synchronization Technology_Clock Transmission Technology White Paper