1 Introduction
At present, the research level of semiconductor integrated circuits at home and abroad has basically acquired the ability to integrate some complex electromechanical systems on chips. Almost the entire industrial infrastructure of 100 billion US dollars can be used to support MEMS technology. MEMS, which are mass-produced and consist of electronic and mechanical components with sizes ranging from nanometers to millimeters, have become a new direction for the development of microelectronic system integration in the world. Multi-category practical MEMS demonstration samples are evolving into early products. The commercialization of micro-accelerometers, force-sensitive sensors, micro-gyroscopes, digital micro-mirror devices, optical switches, etc. that can be mass-produced is becoming more mature, and a market size of 10 billion US dollars has been initially formed, with an annual growth rate of more than 30%. When MEMS is integrated with other technologies, some new MEMS devices are often born, providing a very large market and innovation opportunities for microelectronics technology, which may trigger an industrial revolution in the next few decades. However, there are still many challenges in achieving the commercialization and marketization of MEMS. There are still many technical problems in industrialization that need to be studied and solved in depth, especially the relatively lagging development of MEMS packaging technology, which has formed packaging barriers in some aspects, making the research and development of many MEMS devices still temporarily remain in the laboratory stage. It has become a consensus among all sectors to first solve this bottleneck leading to the market and promote the acceleration of the operation of the industrial chain.
2 Characteristics of MEMS packaging
MEMS technology is a typical multidisciplinary cross-penetration, comprehensive, and fashionable research and development field, involving almost all natural and engineering disciplines, with single-crystal silicon Si, SiO2, SiN, SOI, etc. as the main materials. Si has excellent mechanical and electrical properties, and its strength, hardness, and Young's modulus are comparable to Fe, its density is similar to Al, and its thermal conductivity is comparable to Mo and W. When manufacturing complex device structures, various mature surface micro-bD processing technologies and bulk micro-machining technologies are currently used, and are expanding to three-dimensional processing represented by LIGA (the German abbreviation for deep x-ray etching, micro-electroforming, and plastic molding) technology, micro-powder casting, and instant mask EFAB. Therefore, MEMS packaging has its own particularity that is significantly different from IC chip packaging:
(1) Specificity
MEMS usually have some movable parts or suspended structures, silicon cup cavities, beams, grooves, diaphragms, and even fluid components and organic components, which basically work by surface effects. The packaging architecture depends on the MEMS device and its use. For MEMS devices of various structures and uses, the packaging design should be adapted to local conditions, synchronized with the manufacturing technology, and highly specialized.
(2) Complexity
Depending on the application, most MEMS packaging shells need to have non-electrical signal paths directly connected to the outside world, for example, inputs that transmit one or more information such as light, magnetism, heat, force, and chemistry. The input signal interface is complex, and special requirements are placed on chip passivation and packaging protection. The packaging and technology of some MEMS are newer than MEMS, not only are the technical difficulties high, but also the cleanliness requirements for the packaging environment must reach Class 100.
(3) Spatiality
In order to provide enough movable space for the movable parts of MEMS, it is necessary to etch or leave certain grooves or other shaped spaces on the shell. The potted MEMS requires clearance on the surface, which can provide a very effective protective cavity during packaging.
(4) Protective
MEMS made on the wafer is always extremely sensitive to environmental influences before it is packaged. Each operation process of MEMS packaging, dicing, sintering, interconnection, sealing, etc. requires special processing methods, corresponding protection measures, and grid frames to prevent mechanical damage to movable parts. The circuit part of the system must also be isolated and protected from the environment to avoid affecting the performance of the processing circuit. It is required that the packaging and its materials should not have adverse effects on the use environment.
(5) Reliability
MEMS has a wide range of applications, which places higher reliability requirements on its packaging, especially ensuring that the product can work safely under harsh conditions, be protected from harmful environmental corrosion, and that the hermetic package can dissipate excess heat.
(6) Economical
MEMS packaging is mainly developed in a customized manner and is currently in its early stages of development, far from being serialized and standardized. Its packaging accounts for 40%-90% of the entire product price, and reducing packaging costs is a hot topic.
In summary, the biggest difference between IC packaging and MEMS packaging is that MEMS generally needs to contact the outside world, while IC is just the opposite. The main function of its packaging is to protect the chip and complete the electrical interconnection. IC packaging cannot be directly transplanted to more complex MEMS. But in a broad sense, MEMS packaging is mostly based on the standardized IC chip packaging architecture. Most of the current technologies use mature microelectronic packaging processes, and improve and evolve them to adapt to the special signal interface, shell, inner cavity, reliability, cost reduction and other requirements of MEMS.
3 Development of MEMS packaging
The development goal of MEMS is to explore new principles, new functional components and systems through miniaturization and integration, and to open up a new technology field and industry. Its packaging plays a vital role in ensuring the realization of this goal. Almost every international MEMS conference will have a heated discussion on its packaging technology, and diversified research and development will take a different approach. Various improved MEMS packages continue to emerge, among which the more representative ideas are integrated microsensors and array chip systems involving physics, chemistry, biology, micromechanics, and microelectronics. After the MEMS system-on-chip is realized, it is packaged; the other is to make the processing circuit into a dedicated chip and assemble it with the MEMS on the same substrate, and finally perform multi-chip component MCM packaging and system-level packaging SIP. In commercial MEMS products, packaging is the key technology that ultimately determines its volume, reliability, and cost, and the expectations are extremely high.
MEMS packaging can be roughly divided into multiple levels, including wafer level, monolithic full integration level, MCM level, module level, SIP level, etc. The wafer level provides a technical bridge for the front-end and back-end processes of MEMS production, integrates resources, has the characteristics of flip-chip packaging and chip size packaging, and performs special passivation protection on sensitive and fragile components and actuators to protect them from harmful working media and moisture erosion, and not or less affected by other irrelevant factors, avoiding reduced accuracy, and completing the welding and bonding of the MEMS chip and the base (or tube shell); the monolithic fully integrated level packaging must seal a microstructure and microcircuit integrated on the same substrate to make it a complete system product available for application, with small size, short internal interconnection length, good electrical characteristics, and high output/input contact density. It is an ideal solution for the development of MEMS packaging; the MCM level assembles MEMS and signal processing chips in a housing, and often uses mature deposited thin film multi-chip modules MCM-D, hybrid multi-chip modules MCM-C/D, and thick film ceramic multi-chip modules MCM-C processes and structures to achieve high-density and high-reliability packaging, which can make full use of existing conditions and equipment to produce different parts of MEMS separately. This type of packaging has advantages in small size, multi-function, high density and improved production efficiency; module-level packaging aims to provide some modular external interfaces for MEMS design, which are generally divided into optical interface, fluid interface and electrical interface. The interface data is transmitted by the bus system, so that MEMS can be mass-produced using unified and standardized packaging, reducing investment in packaging equipment, reducing costs, shortening production cycles, and requiring that the packaging can be freely expanded and connected in two-dimensional space to form modules, complete certain functions, and ensure the highest possible packaging density; SiP is called a super-integration strategy, which provides maximum flexibility in integrating heterogeneous components and is suitable for RF-MEMS packaging. In the current communication system, a large number of RF off-chip discrete units are used, and passive components (capacitors, inductors, resistors, etc.) account for 80%-90% of the number of RF system components and 70%-80% of the substrate area. These can be MEMS-ized to improve system integration and electrical performance, but there is often no ready-made packaging available, and SiP is a good choice to complete the assembly and final packaging of the entire product.
In MEMS packaging technology, flip chip interconnect packaging is unique for its high I/O density, low coupling capacitance, small size, high reliability and other characteristics. Several MEMS chips with different functions can be assembled on the same substrate through flip chip interconnection to form an independent system. The flip chip is facing down, and the downward-facing optoelectronic MEMS can flexibly select the light source to be received without being affected by other light sources. Studies have shown that the equipment requirements for the process of forming bumps on the chip by chemical plating and deposition of flexible under-bump metal layer UBM, solder paste printing and bump transfer are not high. It is used as a flip chip packaging structure for force-sensitive MEMS, especially for single-piece small-batch flip chip packaging developed by various research institutions for MEMS. However, the UBM formed by photolithography mask, electroplating and reflow is suitable for industrial mass production of MEMS pressure sensors. MEMS packaging using flip chip interconnect technology has made progress in many aspects and has become a hot spot for research and development.
In practical applications, MEMS packaging may be a combination of multiple technologies. Strictly speaking, some packaging technologies have no obvious differences and definitions, while others are closely related to or similar to microelectronic packaging. High-density packaging, large-cavity tube shell and airtight packaging, wafer bonding, chip isolation and channels, flip chips, thermal processing, flexible bumps, quasi-sealed packaging technologies, etc. have attracted much attention. The materials used for MEMS packaging are mainly ceramics, metals, molded plastics, etc. The shells of high-reliability products mostly adopt ceramic-metal, ceramic-glass, metal-glass and other structures, each with its own characteristics, meeting the special signal interface and shell performance requirements of MEMS packaging.
4 Applications of MEMS packaging
MEMS is one of the major frontiers of scientific and technological exploration that has attracted international attention. Newly developed MEMS samples are constantly being disclosed, expanding from sensitive MEMS to optical MEMS for all-optical communications, RF-MEMS for mobile communication front-ends, microfluidic systems and other information MEMS. Optical MEMS include micromirror arrays, optical switches, variable attenuators, passive interconnect couplers, optical cross-connectors, optical add/drop multiplexers and wavelength division multiplexers, etc. MEMS has a natural affinity with optical signals; RF-MEMS includes key components such as radio frequency switches, adjustable capacitors, inductors, resonators, filters, phase shifters, antennas, etc.; microfluidic systems include micropumps, microvalves, micromixers, microfluidic sensors, etc., which can transport trace fluids, analyze and separate components, and measure and control parameters such as pressure, flow, and temperature online. MEMS is in a period of vigorous development. The formation of the industrial chain and value chain requires the joint efforts and close cooperation of all links in the chain, and packaging is indispensable.
4.1 Micro-accelerometer
The most successful product of MEMS is the micro accelerometer, which is usually composed of a cantilever, with one end of the beam fixed and a mass block of about 10μg hanging on the other end. The mass block is sensitive to acceleration and converted into an electrical signal, which is output after C/V conversion, amplification, and phase-sensitive demodulation. Some manufacturers have a monthly output of 2 million units and have developed more than 20 types of products, which are mainly used for inertial measurement of automobile airbag systems and stability systems. The annual demand in the international market is more than 100 million units. The reason for the rapid commercialization progress in the market compared with other types of MEMS is that it is more suitable to use standard IC packaging, provide a corresponding micromechanical protection environment, and do not need to develop a special shell structure. It has evolved from the XL50 round ceramic package to the XL276 8-pin ceramic dual in-line package and the XL202 14-pin ceramic surface mount package. It is now gradually replaced by the smaller XL202E 8-pin ceramic surface mount package, which can withstand high temperature and strong mechanical vibration, acid and alkali corrosion. Low-G series products adopt the popular square flat leadless QFN-16 package, and some adopt 16-pin dual in-line or single in-line plastic package. The use of MCM technology can usually incorporate more complex signal conditioning function chips in a MEMS package.
4.2 Micro Gyroscope
MEMS micro-gyroscopes mostly use vibration to detect the angular velocity signal of rotation. They are accelerating the development of high-precision, low-cost, integrated, and high-impact resistant products, studying the manufacture of fiber-optic gyroscopes on chips, and small-batch production of silicon MEMS gyroscopes (commonly known as chip gyroscopes) and MEMS quartz piezoelectric rate gyroscopes for signal compensation of precision guidance of global satellite positioning systems, automotive navigation systems, aircraft, antenna stabilization systems, etc. There are micro-gyroscopes that use leadless ceramic chip carrier LCCC packaging, hybrid integrated packaging, MCM packaging, and single tube shell system packaging, which package the inertial sensor and the control dedicated circuit into one, and require the internal vacuum airtight conditions.
4.3 Force Sensor
Miniaturized, multifunctional, integrated, and intelligent force-sensitive sensors based on MEMS technology have been commercially applied. Among them, silicon MEMS pressure sensors are the most widely used. The basic process flow is divided into two major processes: force-sensitive elastic diaphragm (silicon cup) and assembly. How to avoid the generation of additional stress in assembly is the key to the packaging process. The use of electrostatic sealing is unique. The force-sensitive elastic diaphragm and the glass ring are sealed together through an electrostatic sealing machine to form a diaphragm matrix. The back side receives the pressure structure to increase the fixed support thickness of the diaphragm, and then the inner leads are bonded, bonded, the outer leads are welded, aging treatment, zero point compensation, sealing, electrostatic calibration, etc. are completed to complete the entire packaging process: packaging technology is developing towards low-temperature glass sealing and laser silicon-glass sealing.
4.4 Surface Mount Microphone
The world's first surface-mount Si Sonic micro-microphone is manufactured using MEMS technology and integrated with a CMOS charge pump IC and two RF filter capacitors in a package to form a surface-mount device. This surface-mount packaging format is suitable for mass automatic assembly production, which greatly improves production efficiency. The current traditional condenser microphone ECM is manually mounted and lacks economies of scale. The former is only half the size of the ECM overall, with a smaller projected area of 8.61mm2, and is expected to replace the ECM that has always dominated portable applications.
4.5 Digital Micromirror Device
The main chip of the digital micromirror device DMD (DIGITAL Micromirror DEVICE) contains more than 1.5 million micromirrors that can be precisely controlled and rotated independently. It can be used in optical communications, digital projection devices, rear-projection color TVs, etc. Its imaging principle is that the rotation of the micromirror ±10° controls the on and off of the light signal, and the lens forms an image and projects it onto the screen. Its advantages are high light efficiency, rich and realistic colors, brightness that can easily reach 2000 lumens or even higher, contrast ratio of 2000:1, good reliability, and an average lifespan of about 50 years. The current sales volume exceeds 3 million sets. DMD adopts a sealed package with a transparent window, using ceramic as the substrate and glass as the window. At the same time, a getter is used to remove moisture, hydrogen and other material particles that may harm the reliability of the device. Its packaging can ensure that the device is dry and sealed and has a transparent window to ensure the smooth flow of the light path.
4.6 MEMS Optical Switches
The optical switch made by MEMS technology integrates the optomechanical structure, microbrake, and micro-optical element on the same substrate. It has the characteristics of traditional optomechanical switches and waveguide switches. Two-dimensional and three-dimensional MEMS optical switches have commercial products on the market. Research on one-dimensional MEMS optical switches is mostly packaged in the form of components or isolated sealed or modules. The typical representative is the MEMS-5200 series switch module. Some products can accept input signals from dozens of optical fibers and route them to hundreds of other optical fibers. The main reason for using such products is to avoid expensive and difficult-to-handle large amounts of optical-to-electrical conversion and electrical-to-optical conversion. To achieve this goal, it is required to make hundreds or even thousands of connections between the optical fiber and other devices, and use packaging that is compatible with the optical fiber. The packaging and joint technology is even more novel than MEMS, and the impact of temperature, humidity, vibration and other environmental factors on the packaged optical switch should be minimized as much as possible. There is still a lack of common packaging technology standards in the MEMS optical switch market. Due to small batches and high technical difficulties, the price is particularly expensive. The continuous improvement of packaging technology, packaging materials, performance testing, etc. is a hot topic. Packaging technology still needs further development to fully demonstrate the key characteristics of MEMS optical switches in scalably completing various optical exchanges in all-optical networks.
4.7 RF-MEMS
RF-MEMS can make up for the shortcomings of CMOS technology. Passive components made by MEMS technology are beneficial to the improvement of system integration and electrical performance, and the reduction of costs. They have become the research and development direction of the world's top semiconductor manufacturers to expand the application range of silicon chips. The practical application of RF-MEMS switches has made considerable progress. There is often no ready-made package that can be used directly, so it is necessary to seek solutions, and SIP is the first to bear the brunt. SIP considers packaging issues from the RF-MEMS design stage. The integration method of passive components, the design of packaging structure, the packaging process flow, the interconnection between chips in the system, and the selection of packaging materials are particularly critical. SIP contains surface mount devices, integrated passive components, memory chips, CMOS chips, and GaAs high-performance power amplifiers. High-density interconnection technology can be used on the substrate to make buried passive components, transmission lines, etc., simplifying the system structure, reducing parasitic effects and losses, increasing the application frequency range, and shortening product development time.
5 Conclusion
The research and development of MEMS, micro-optical electromechanical systems (MOEMS), and nano-electromechanical systems (NEMS) provide a lot of opportunities for the new technological revolution. Different MEMS require specific corresponding packaging structures, and the packaging technology is highly specific, which leads to a large number of packaging problems that need to be solved urgently. According to statistics from SPC, an authoritative foreign statistical company, the research of MEMS in China ranks among the top eight in the world, and MEMS force-sensitive sensors can be mass-produced. Various principle samples such as MEMS optical switches, RF-MEMS switches, and microfluidic systems have been successfully developed. From the overall level, the gap with foreign countries is mainly reflected in industrialization technology. Select some MEMS and their packaging with large applications and wide range as the development and market entry points, form an industry, meet market demand, lay the foundation for the development of other MEMS, and explore the rules, so that half of the success is achieved. No MEMS research and development will ignore packaging technology, and it is unrealistic without packaging follow-up.
From the development trend abroad, MEMS packaging categories generally follow the standardized IC packaging structure, or improve it to meet the requirements of MEMS, and strive to use more existing IC packaging architectures to achieve MEMS packaging. Another development trend is to use new packaging structures and technologies, establish a MEMS packaging unit library, and further integrate the cost-conscious new packaging structure with MEMS research and development.
On the issue of MEMS, if we fully discuss its packaging, everyone has their own way. In the market competition, we must choose the right products. It is worth looking forward to building a complete MEMS industry chain under the guidance of the market.
Previous article:Development and application of MEMS packaging technology
Next article:Advantages of SOI Technology and Its Manufacturing Technology
Recommended ReadingLatest update time:2024-11-16 15:24
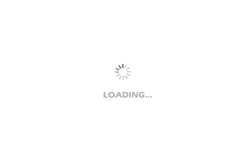
- Melexis launches ultra-low power automotive contactless micro-power switch chip
- Infineon's PASCO2V15 XENSIV PAS CO2 5V Sensor Now Available at Mouser for Accurate CO2 Level Measurement
- Milestone! SmartSens CMOS image sensor chip shipments exceed 100 million units in a single month!
- Taishi Micro released the ultra-high integration automotive touch chip TCAE10
- The first of its kind in the world: a high-spectral real-time imaging device with 100 channels and 1 million pixels independently developed by Chinese scientists
- Melexis Launches Breakthrough Arcminaxis™ Position Sensing Technology and Products for Robotic Joints
- ams and OSRAM held a roundtable forum at the China Development Center: Close to local customer needs, leading the new direction of the intelligent era
- Optimizing Vision System Power Consumption Using Wake-on-Motion
- Infineon Technologies Expands Leading REAL3™ Time-of-Flight Portfolio with New Automotive-Qualified Laser Driver IC
- Innolux's intelligent steer-by-wire solution makes cars smarter and safer
- 8051 MCU - Parity Check
- How to efficiently balance the sensitivity of tactile sensing interfaces
- What should I do if the servo motor shakes? What causes the servo motor to shake quickly?
- 【Brushless Motor】Analysis of three-phase BLDC motor and sharing of two popular development boards
- Midea Industrial Technology's subsidiaries Clou Electronics and Hekang New Energy jointly appeared at the Munich Battery Energy Storage Exhibition and Solar Energy Exhibition
- Guoxin Sichen | Application of ferroelectric memory PB85RS2MC in power battery management, with a capacity of 2M
- Analysis of common faults of frequency converter
- In a head-on competition with Qualcomm, what kind of cockpit products has Intel come up with?
- Dalian Rongke's all-vanadium liquid flow battery energy storage equipment industrialization project has entered the sprint stage before production
- Allegro MicroSystems Introduces Advanced Magnetic and Inductive Position Sensing Solutions at Electronica 2024
- Car key in the left hand, liveness detection radar in the right hand, UWB is imperative for cars!
- After a decade of rapid development, domestic CIS has entered the market
- Aegis Dagger Battery + Thor EM-i Super Hybrid, Geely New Energy has thrown out two "king bombs"
- A brief discussion on functional safety - fault, error, and failure
- In the smart car 2.0 cycle, these core industry chains are facing major opportunities!
- The United States and Japan are developing new batteries. CATL faces challenges? How should China's new energy battery industry respond?
- Murata launches high-precision 6-axis inertial sensor for automobiles
- Ford patents pre-charge alarm to help save costs and respond to emergencies
- New real-time microcontroller system from Texas Instruments enables smarter processing in automotive and industrial applications
- Two-way BUCK
- Miniaturized millimeter wave sensors using CMOS technology
- What is the motor principle corresponding to the STM measurement of the motor's electrical angle?
- Audio Amplifier Distortion and Common Improvement Methods
- Several standards for selecting splicing screens
- LM46002AQ
- [TI millimeter wave radar evaluation]_1_AWR1843BOOST unboxing
- IX. Some suggestions for training on “control” questions
- TI full range of component libraries (component library, package library, 3D library) collection
- [NXP Rapid IoT Review] Week 2: Get familiar with the online GUI Rapid IoT Studio