Keywords: high-speed acquisition; pipeline storage; FPGA
0 Introduction
In order for the computer to process the analog quantity input by the data acquisition system, the analog quantity must be converted into digital quantity through the data acquisition system. FPGA is developed on the basis of logic devices such as CPLD. Its high integration can greatly reduce the size of the circuit board, reduce the system cost, improve the system performance and reliability, and is suitable for the application of timing, combinational and other logic circuits. A complete detection system usually has a collection and storage part. Whether it is an electrical signal, an optical signal, or a sound signal, after being received by the detector, most of them need to be converted into digital signals before being transmitted to the processor to complete the analysis and judgment process. Some of the current high-speed and large-capacity acquisition systems are often expensive. This paper mainly discusses a low-cost, high-speed, multi-channel, and reliable data acquisition system that uses FPGA and other devices for control and uses multiple Nandflash storage. This paper mainly discusses the hardware design and storage design.
1 System overall design plan
The working principle of the data acquisition system is: various information is converted into analog electrical quantity signals after passing through the sensor, and the analog quantity is converted into digital quantity signals through ADC, and then transmitted, stored, and processed. In this system, under the control of software and hardware, the system converts the collected analog signal through the A/D conversion device, and then caches the conversion result to FIFO, and then transfers it to the non-volatile Nandtlash array. Among them, FIFO can not only realize the cache function, but also solve the contradiction between the number of data bits after A/D conversion and the number of data line bits of Nandflash memory. As shown in the block diagram of the overall system design scheme in Figure 1, this system uses the microblaze processor inside the FPGA as the main controller, i.e., the software controller, while the internal logic resources of the FPGA are used to generate hardware control timing. The entire system collects and transmits data under the coordination of the two.
2 Design of Hardware Controller
The entire data acquisition system contains a data acquisition module and a data transmission module. The data acquisition module consists of an AD data conversion module and a Nandflash data storage module. The system uses a USB interface as a data transmission module, which is not the focus of this paper. In the data transmission part, this system uses DMA transmission technology. The FPGA internal circuit function module is shown in Figure 2.
Among them, ALE and WR are connected to the address latch and WR pin of the processor respectively. The processor is set to the mode of time-sharing multiplexing of the address bus and the data bus. In this way, the FPGA can latch the address of the processor through the ALE signal. The control command generator is used to decode and generate corresponding commands and operations. The DMA controller is a specific controller written by us. It needs to make DMA_EN valid when receiving the DMA enable command of the processor, and then start DMA to transfer data once after receiving the DMA start signal DMA_restart. Each time it is started, a page of 2K data is transmitted. During the transmission process, because it is a read of multiple FIFOs, in order to prevent the data from being messed up, we use a specific controller to match DMA_FLASH_WE and DMA_FIFO_RD of multiple FIFOs to unify them, resulting in a multi-chip FIFO rotation read operation.
In the design of sampling rate selection, we first use the software system of the microprocessor to give the hardware system of the FPGA a sampling rate selection value, and then the hardware system of the FPGA will decode the frequency value given by the microprocessor. The frequency selector will generate the corresponding frequency output according to this value, and the frequency output by the frequency selector will be input into the state machine controlling the AD conversion. In this way, the state machine controlling the AD conversion will perform corresponding frequency acquisition, data reading and data writing to the FIFO according to the input frequency.
3 Control and storage module
This system adopts pipeline operation mode when designing the storage mode. There are two stages in the writing of Nandflash memory: data loading stage (that is, writing data to the page data register through the I/O port) and programming stage (inside the chip, transferring the data in the page data register to the non-volatile storage unit). The data programming stage is automatic and does not require other operations of the external system, but it takes a long time, and its typical value is 200μs. If the pipeline storage method is used, the disadvantage of the slow writing speed of the Nandflash chip can be overcome. The principle of the writing operation process of the Nandflash memory using the pipeline operation method is shown in Figure 3. First, load the data to the first Nandflash. After the data is loaded, the first Nandflash will then enter the automatic data programming stage; then load the data to the second Nandflash. After the data is loaded, the second Nandflash will also enter the automatic data programming stage; then perform the same operations on the third Nandflash and the fourth Nandflash in turn. When the data of the fourth Nandflash is loaded, the first Nandflash has just finished automatically programming the data, and then repeat the loading and automatic programming of data stages at the beginning from the first Nandflash. This cycle continues until the data collection is completed. This is the storage method of the pipeline. From the overall time point of view, the entire system is constantly transmitting and storing data.
During data loading, this system applies DMA transfer control, that is, whenever the FIFO half-full flag signal HF generates a valid level, the processor starts an interrupt. In the interrupt program, the processor will complete the Nandflash write command and address, as well as the start of the DMA controller. Once the DMA controller is started, the processor will go to the background to perform effective address calculations and other operations without participating in the data transmission process. The entire data transmission process from FIFO to Nandilash memory is completed by the DMA controller written inside the FPGA. Start the DMA controller once to transfer a page of 2048 bytes of data, and one interrupt will complete the transfer of 16K bytes. The timing oscilloscope waveform of the DMA transfer is shown in Figure 4: Channels 0, 1, 2, and 3 are the FIFO read data timing waveforms, and channel 4 is the Nandflash write timing waveform. After a DMA transfer is completed, the processor must also determine whether the current page is the last page, page 64. If it is not the last page, the page address is increased by 1, and the DMA transfer sampling data operation continues. If the current page is the last page, page 64, determine whether the current block is the last block of this file. If it is not the last block, add 1 to the block address and compare it with the invalid block table to determine whether this block is a valid block. If it is, set the page address to 0 and continue the DMA transfer sampling data operation. If the current block is the last block of this file, the data acquisition operation of this file is completed, that is, this acquisition is completed.
4 Conclusions
The test results show that the acquisition system has stable performance and the acquisition speed can be maintained above 10 Mb/s, which meets the design requirements. The system has practical value for hardware design with low cost, high speed and reliability.
Previous article:Design of an Ultrasonic Thickness Measurement System Based on CPLD
Next article:Application of Ferrite Beads in Small Portable Devices
Recommended ReadingLatest update time:2024-11-16 17:52
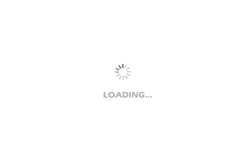
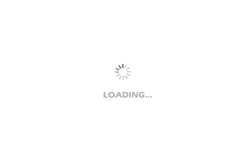
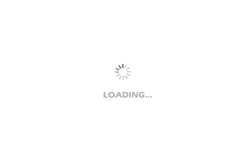
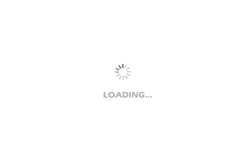
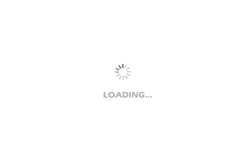
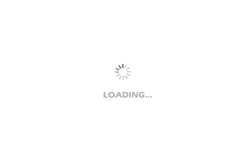
- Popular Resources
- Popular amplifiers
-
Analysis and Implementation of MAC Protocol for Wireless Sensor Networks (by Yang Zhijun, Xie Xianjie, and Ding Hongwei)
-
MATLAB and FPGA implementation of wireless communication
-
Intelligent computing systems (Chen Yunji, Li Ling, Li Wei, Guo Qi, Du Zidong)
-
Summary of non-synthesizable statements in FPGA
- Huawei's Strategic Department Director Gai Gang: The cumulative installed base of open source Euler operating system exceeds 10 million sets
- Analysis of the application of several common contact parts in high-voltage connectors of new energy vehicles
- Wiring harness durability test and contact voltage drop test method
- Sn-doped CuO nanostructure-based ethanol gas sensor for real-time drunk driving detection in vehicles
- Design considerations for automotive battery wiring harness
- Do you know all the various motors commonly used in automotive electronics?
- What are the functions of the Internet of Vehicles? What are the uses and benefits of the Internet of Vehicles?
- Power Inverter - A critical safety system for electric vehicles
- Analysis of the information security mechanism of AUTOSAR, the automotive embedded software framework
Professor at Beihang University, dedicated to promoting microcontrollers and embedded systems for over 20 years.
- Innolux's intelligent steer-by-wire solution makes cars smarter and safer
- 8051 MCU - Parity Check
- How to efficiently balance the sensitivity of tactile sensing interfaces
- What should I do if the servo motor shakes? What causes the servo motor to shake quickly?
- 【Brushless Motor】Analysis of three-phase BLDC motor and sharing of two popular development boards
- Midea Industrial Technology's subsidiaries Clou Electronics and Hekang New Energy jointly appeared at the Munich Battery Energy Storage Exhibition and Solar Energy Exhibition
- Guoxin Sichen | Application of ferroelectric memory PB85RS2MC in power battery management, with a capacity of 2M
- Analysis of common faults of frequency converter
- In a head-on competition with Qualcomm, what kind of cockpit products has Intel come up with?
- Dalian Rongke's all-vanadium liquid flow battery energy storage equipment industrialization project has entered the sprint stage before production
- Allegro MicroSystems Introduces Advanced Magnetic and Inductive Position Sensing Solutions at Electronica 2024
- Car key in the left hand, liveness detection radar in the right hand, UWB is imperative for cars!
- After a decade of rapid development, domestic CIS has entered the market
- Aegis Dagger Battery + Thor EM-i Super Hybrid, Geely New Energy has thrown out two "king bombs"
- A brief discussion on functional safety - fault, error, and failure
- In the smart car 2.0 cycle, these core industry chains are facing major opportunities!
- The United States and Japan are developing new batteries. CATL faces challenges? How should China's new energy battery industry respond?
- Murata launches high-precision 6-axis inertial sensor for automobiles
- Ford patents pre-charge alarm to help save costs and respond to emergencies
- New real-time microcontroller system from Texas Instruments enables smarter processing in automotive and industrial applications
- Single-button, double-button touch
- Does the IR21X series have a half-bridge driver chip with an output phase difference of 180°?
- BasicRF Simple Wireless Point-to-Point Transmission Protocol
- After this test, the source code can run normally. The trajectory planning of the robot arm can be realized in MATLAB
- Ultra-high precision level conversion circuit diagram
- ESP-Box: Espressif's open source 3D printing project based on ESP32-S3
- About the problem that the C51 microcontroller program cannot be downloaded in the HC6800 development board
- How to improve EMI on PCB by component placement?
- Huawei Hongmeng + Alibaba Pingtou Ge, Runhe Neptune Review (Part 2)
- If you don’t understand, ask how to get download points