Motors contribute nearly 50% of energy consumption in the United States, so reducing motor energy consumption can effectively improve energy utilization, and using advanced microcontroller (MCU) technology to achieve motor control is an effective method. This article introduces the latest developments in motor control MCU technology and its applications.
A major target for energy reduction is the motor, which consumes about 50% of total energy consumption in the U.S. A home can easily contain more than 50 motors, and typically 70 to 80. In the industrial sector, motors are also widely used in factory automation.
Today, recent advances in MCU technology allow motors to operate more efficiently at lower costs. In certain markets, this can accelerate the transition from electromechanical to electronic control, enabling variable speed motor control to optimize motor efficiency and reduce costs for all applications at the device level.
Low-cost brushless DC motor control MCU
Compared with brushed motors often used in motor control, MCU-controlled brushless DC (BLDC) motors eliminate brush wear and arc mechanisms, so that the life of the motor is essentially limited only by the life of the bearings. In addition, the advantages of MCU-based BLDC motor systems include high efficiency, high torque-inertia ratio, higher speed performance, low noise, better thermal efficiency and low EMI characteristics.
Utilizing high-volume 8-bit MCUs designed specifically for motor control is a very low-cost approach to solving digital motor control problems. With performance up to 10MIPS and dedicated hardware for motion control (including center-aligned 14-bit PWM, a motion feedback module, and a high-speed ADC), applications that previously required expensive processors can now be solved using low-cost 8-bit MCUs.
Figure 1: Example of MCU application in washing machine
An 8-bit microcontroller drives a three-phase ACIM variable frequency drive.
The three-phase PWM control in some MCUs, such as the PIC18F4431, can provide all three controls of a BLDC in hardware, minimizing the software that must be developed and debugged. With up to 8 available PWM channels, typically only 6 are needed to drive a three-phase motor. Therefore, the remaining two channels can be used for other functions without the need for additional devices. The motion feedback module with an integral encoder interface as an integral part of the MCU reduces the number of components and system cost.
An MCU with an ADC sampling rate of 200K per second can provide the speed necessary for closed-loop control. The simultaneous use of two different channels makes it possible to sample voltage and current simultaneously. Such fast conversion is required when measuring the rear electromotive force (EMF) in closed-loop motor control, and the ability to synchronize the ADC with the PWM on the rising or falling edge minimizes switching noise. In short, these modules eliminate the need for external motor control devices such as high-speed ADCs and position encoders.
In many motor control applications, fail-safe operation is very important. MCUs with fail-safe clock monitors (an internal RC oscillator that can be used as a backup clock in the event of a crystal failure) allow designers to use digital control that provides high reliability. Programmable deadtime delays such as on the PWM minimize switching noise, which can save weeks of development time and meet critical program deadlines to get new products to market. In all cases, MCUs with reliable flash memory provide the potential for fast time to market and the flexibility to adjust as requirements change before installation or during use.
Market drivers and solutions
Electronic motor control requirements in home electronics, industrial and automotive markets are driving the demand for MCUs with advanced motor control peripherals.
In the appliance market segment, improved motor control is needed to meet government program standards, such as the U.S. Environmental Protection Agency's Energy Star program, which encourages manufacturers to launch energy-efficient appliances. Washing machines are an important area for high-performance motor control. Direct-drive washing machines eliminate the drive belt between the motor shaft and the washing machine agitator, allowing different speeds and agitator modes.
One manufacturer's completely redesigned washing machine consumes 38% less electricity and 17% less water than a conventional washing machine. The motor control MCU adjusts the motor power according to the amount and type of laundry. However, appliance users are still very sensitive to the initial purchase price, so manufacturers must continue to reduce their development and production costs to make more advanced appliances acceptable to more consumers.
In home appliances, 8-bit MCUs designed specifically for low-cost motor control applications integrate functions that minimize the number of additional components. With on-board motor PWM, fail-safe clock monitors, and highly reliable flash memory, the latest MCUs simplify the design of home appliance motor control and achieve low-cost goals.
In industrial applications, electricity costs and downtime of assembly operations can reduce manufacturers' profits. An industrial example of how improved control of motor performance can directly affect efficiency and profits is replacing the valve in an industrial water pump with one with an MCU-based variable speed (VSD) system.
For pumps or fans, power consumption is proportional to the cube root of shaft speed, when shaft speed is reduced by 10%, flow rate is reduced by 10%, and power consumption is reduced by 27%. If speed is reduced by 20%, power consumption is reduced by 49%. By using MCU variable speed motor control instead of constant speed motor valve to reduce flow, it has been proven that 25-40% energy savings can be obtained for centrifugal pumps, fans and blowers in industrial applications.
The benefits for industrial applications are clear, and variable speed motor control using MCU drivers relies on other factors, such as flexibility and reliability - factors that can avoid downtime due to failure or maintenance. MCUs with flash and EEPROM provide the flexibility to address industrial user requirements through reprogrammable features when upgrades are needed or control program requirements change. MCUs with 16KB flash and 256B EEPROM provide enough memory in an 8-bit MCU to handle the many changes that may be required in an industrial environment. Equally important, the PMOS electronically erasable cell process technology used in Microchip's flash memory generally has data storage cells that can withstand 1 million erase/write cycles, and data can be retained for more than 40 years.
Existing automotive motor applications include using motors to open and close windows and doors, and to position seats. Since these applications are used at low frequencies, they are not sensitive to low efficiency, but high-usage applications, such as passenger temperature environmental control and engine compartment fans, continue to consume the car's limited electrical energy. The motor control MCU allows the environmental control fan to run only at a speed that maintains a comfortable temperature, thus minimizing noise and reducing power consumption.
In many cases, the motor control MCU must use a control area network (CAN) or a local interconnect network (LAN) to connect to the vehicle network. For body electronics, the low-cost LIN protocol is now used to reduce overall system costs. In some MCU families, a USART module supporting LIN1.2 can be found, while providing automatic wake-up and baud detect on the start bit.
As control algorithms become more complex in all market segments, the performance of digital motor controllers has risen from the MCU to the DSP level. Digital signal controllers (DSCs) bring higher performance and affordable, designer-friendly MCU technology to more mature motor control designs, including those with vector control applications. DSCs operate at speeds up to 30MIPS, with up to 144KB of flash memory and integrated peripherals dedicated to motor control to enable more advanced and new motor control applications. With electronic motor control based on DSP and DSC, home appliance industrial control and automotive not only work more efficiently, provide more functions, but also are affordable.
Previous article:Breaking through the shackles of circuit design, 32-bit MCU power consumption is further reduced
Next article:Fujitsu Semiconductor Launches New Microcontroller for Automotive Applications
Recommended ReadingLatest update time:2024-11-15 22:39
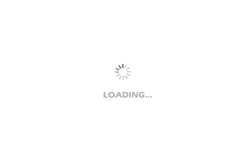
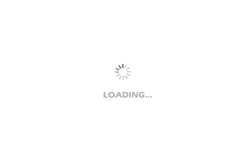
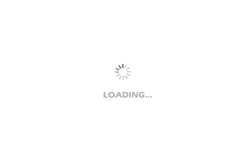
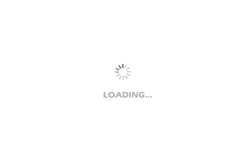
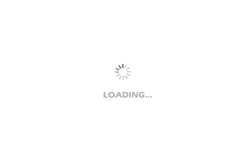
- Popular Resources
- Popular amplifiers
-
Wireless Sensor Network Technology and Applications (Edited by Mou Si, Yin Hong, and Su Xing)
-
Modern Electronic Technology Training Course (Edited by Yao Youfeng)
-
Modern arc welding power supply and its control
-
Small AC Servo Motor Control Circuit Design (by Masaru Ishijima; translated by Xue Liang and Zhu Jianjun, by Masaru Ishijima, Xue Liang, and Zhu Jianjun)
- High signal-to-noise ratio MEMS microphone drives artificial intelligence interaction
- Advantages of using a differential-to-single-ended RF amplifier in a transmit signal chain design
- ON Semiconductor CEO Appears at Munich Electronica Show and Launches Treo Platform
- ON Semiconductor Launches Industry-Leading Analog and Mixed-Signal Platform
- Analog Devices ADAQ7767-1 μModule DAQ Solution for Rapid Development of Precision Data Acquisition Systems Now Available at Mouser
- Domestic high-precision, high-speed ADC chips are on the rise
- Microcontrollers that combine Hi-Fi, intelligence and USB multi-channel features – ushering in a new era of digital audio
- Using capacitive PGA, Naxin Micro launches high-precision multi-channel 24/16-bit Δ-Σ ADC
- Fully Differential Amplifier Provides High Voltage, Low Noise Signals for Precision Data Acquisition Signal Chain
- LED chemical incompatibility test to see which chemicals LEDs can be used with
- Application of ARM9 hardware coprocessor on WinCE embedded motherboard
- What are the key points for selecting rotor flowmeter?
- LM317 high power charger circuit
- A brief analysis of Embest's application and development of embedded medical devices
- Single-phase RC protection circuit
- stm32 PVD programmable voltage monitor
- Introduction and measurement of edge trigger and level trigger of 51 single chip microcomputer
- Improved design of Linux system software shell protection technology
- What to do if the ABB robot protection device stops
- Allegro MicroSystems Introduces Advanced Magnetic and Inductive Position Sensing Solutions at Electronica 2024
- Car key in the left hand, liveness detection radar in the right hand, UWB is imperative for cars!
- After a decade of rapid development, domestic CIS has entered the market
- Aegis Dagger Battery + Thor EM-i Super Hybrid, Geely New Energy has thrown out two "king bombs"
- A brief discussion on functional safety - fault, error, and failure
- In the smart car 2.0 cycle, these core industry chains are facing major opportunities!
- The United States and Japan are developing new batteries. CATL faces challenges? How should China's new energy battery industry respond?
- Murata launches high-precision 6-axis inertial sensor for automobiles
- Ford patents pre-charge alarm to help save costs and respond to emergencies
- New real-time microcontroller system from Texas Instruments enables smarter processing in automotive and industrial applications
- Fluke High Resolution Thermal Imager - Even the smallest details are captured! Free trial registration is open
- The capacitor on the PCBA cracked and short-circuited. How could it be the design's fault?
- 【Bluesun AB32VG1 RISC-V Evaluation Board】Development of example programs
- 2nd day to go!! Pre-registration for the prize live broadcast | ON Semiconductor image sensors help the automotive, machine vision and artificial intelligence fields....
- 【AT-START-F425 Review】USB to CAN Preview Post
- Abnormal sound from the front transformer of the power factor circuit
- Packaging issues of double-row pluggable connectors
- Japanese auto parts giant exposed to large-scale fraud for 20 years! Affecting 10 Japanese automakers...
- 【AT32WB415 Review】03 SPI Drive TFT LCD Screen
- [Environmental Experts on Smart Watches] Part 2: ON Semiconductor IDE Environment Construction