Abstract: Aiming at the problem that the electrolytic capacitor in the existing LED driving circuit limits the life, a design method for LED driving circuit without electrolytic capacitor is proposed. This method uses Panasonic MIP553 chip with built-in PFC dimmable LED driving circuit, and synthesizes it with external non-isolated bottom-side chopper circuit as the basic circuit structure, outputting stable current to meet the needs of LED operation. At the same time, a protection circuit is designed to protect the load. Experimental results show that the controller chip can work stably and can achieve 27V constant voltage output and 350mA constant current output.
LED (light emitting diode) has become a new generation of green lighting source with its many advantages such as energy saving, environmental protection, high brightness and long life. As LED lighting technology matures, it will eventually be used in all aspects of life and become the new favorite of lighting sources. However, high efficiency, low cost, high power factor and long life driving power supply are the key to the luminous quality and overall performance of LED lamps.
LED lamps that replace ordinary light bulbs on the market now have a lifespan of about 40 times that of incandescent bulbs, equivalent to 40,000 hours. Since LEDs are DC current driven components, they directly convert electrical energy into light energy through the current flowing through them, so they are also called photoelectric converters. Because there is no friction or mechanical loss, they are more efficient than ordinary light sources in terms of energy saving. However, when the AC power is turned on, a DC stabilized power supply with a rectifier component and a smoothing circuit is generally used. The electrolytic capacitors required in the smoothing circuit will rise by 10°C due to the surrounding temperature and the heat generated by the capacitors themselves, resulting in a halving of the lifespan. Therefore, the electrolytic capacitors hinder the lifespan of LED lighting fixtures.
In order to increase the life of the driving power supply, simplify the circuit, reduce the cost and increase the power density, it is necessary to remove the electrolytic capacitor. For this reason, this paper proposes a high-brightness LED driving power supply without electrolytic capacitor.
1 Basic working principle of LED power supply
The BUCK converter and IPD control are used to realize the switching power supply, output constant current and voltage, and drive the LED lamp. The overall block diagram of the circuit is shown in Figure 1.
In the main circuit part, a filter is connected immediately after the mains power, which is used to filter out the high-order harmonics and surges in the power supply, so that the control circuit is less disturbed by the power supply. The input rectifier part adopts an integrated rectifier bridge, which converts the AC power with a level floating above and below the zero point into a unidirectional pulsating DC power through the unidirectional conduction characteristics of the diode, and then outputs the DC voltage under the action of the filter capacitor and inductor. After being adjusted and controlled by the MIP553 and BUCK circuit, the voltage for LED use is output.
2 Specific design of LED power supply
2.1 Input circuit design
In order to extend the service life of the LED driver and make it match the LED, the electrolytic capacitor in the circuit must be removed.
The design indicators of the circuit are: input AC voltage Vm: 198-264VAC/50Hz; output voltage Vo: 27VDC; output current Io: 0.35A.
The input circuit includes a noise filtering device, a safety insurance device and an input rectifying device, as shown in FIG2 .
The noise filter device is mainly composed of capacitors C1/C2/C3 and inductor L1. Its function is to reduce electromagnetic interference (EMI) in the frequency band less than 1MHz. This device can also be connected after the AC alternating current and before the rectifier, and its filtering effect is the same. The safety insurance device is composed of a fuse and ZNR1. The fuse is mainly used to prevent the circuit from being cut off quickly to protect the load when a spike current that is harmful to the circuit is generated; ZNR1 is a surge absorber, which absorbs static electricity and surges from the input end to protect the subsequent circuit. The input rectifier converts AC power into DC power. The selection of the input rectifier bridge: The voltage stress of the rectifier bridge diode is:
Considering the margin, TSC GBL205 (VR=600V, IFAN=1A) is selected.
2.2 Design of output circuit
The output circuit consists of a basic BUCK circuit and a voltage regulator diode DD1, as shown in Figure 3.
2.2.1 BUCK converter and its advantages
Buck converter, also known as step-down converter, series switching regulator, three-terminal switching step-down regulator, is a single-tube non-isolated DC/DC converter with an output voltage equal to or less than the input voltage.
The input current is in operation, when the switch is closed, is>0; when the switch is open, is=0, so is is pulsating, but the output current io is continuous and stable under the action of inductance, diode and capacitor. It is particularly suitable for providing working current for LED.
Selection criteria for FRD1: rated current greater than 2 times of output current, rated voltage greater than input voltage, reverse recovery time less than 100ns, considering margin, parameters of FRD1 are: 15A, 600V, trr=50ns. Use similar method to select T1 and Cout, then their parameters are: T1: 680μH; Cout: 1μF, 50V.
2.2.2 Zener diode DD1
Within a certain range of low input voltage, if there is no reverse device like DD1, a reverse current will flow through the IPD at the moment the switch is turned off, and the IPD does not allow such a current because the reverse current will cause damage to the IPD.
The stresses on DD1 are: IDD>2·Io=2×0.35=0.7A, UDD>Uo, and reverse recovery time trr<100ns. Considering the margin, the selected parameters are: 3A/60V/75ns.
2.2.3 Protection Circuit
MIP553 has built-in protection circuits for overvoltage, overcurrent, overheating, and LED short circuit, but there is no design for protection circuit when LED is open circuit. The main ideas of protection circuit when LED is open circuit include voltage zener diode protection, transistor protection, bias coil protection, etc. Considering the cost and structure, the protection circuit with voltage zener diode is selected in this paper. Its circuit diagram is shown in Figure 3. When the LED is open circuit, the output voltage rises. If the output circuit has a voltage zener diode protection circuit, the voltage zener diode will embed the LED voltage below the voltage drop of the diode, thus preventing the output capacitor from being destroyed.
2.3 Design of control circuit
The control circuit consists of MIP553 and its peripheral circuits, as shown in Figure 4.
The MIP553 chip realizes wide voltage 85~277V/AC input, built-in MOS, simple and stable structure, no need for electrolytic capacitors, supports isolation or non-isolation solutions, single power supply output power 6~30W, constant current output <1A. The power supply has overvoltage, overcurrent, and overheating protection functions, high safety and stability, small size, low heat generation, power efficiency ≥80%, power factor ≥95%, THD <20%.
The drain current of MIP553 is controlled by pins CL and EX, so the setting of resistors RCL and REX connecting these two pins will directly affect the size of the drain current. The maximum drain current can be determined by REX, and considering that this maximum drain current will flow through the LED, care should be taken when setting the reference value.
REX=(VDD(ON)-VEXH)/IEX=(6.5-2.8)/103=36kΩ (3)
Here, assume the input voltage is 100V, the output voltage is 28V, the current is 400mA, and the maximum drain current is set to 1.0A.
The functions of CVDD, CEX, and CCL are to stabilize the operation of MIP553 and suppress external noise. Therefore, their values should be properly selected. CVDD stabilizes the voltage of VDD and suppresses the flickering of LED. Its characteristics are not affected by temperature and do not generate additional noise. The reference standard value is between 1 and 10μF. CEX suppresses external noise from entering the EX pin. Its reference standard value is between 470 and 1000pF. CCL suppresses external noise from entering the CL pin. If its value is too large, the pF value will be seriously affected. Therefore, its value should be less than 1000pF.
2.4 Simulation Results
The circuit is simulated using Multisim, and the results are shown in Figure 5.
As can be seen from Figure 5, the output voltage is stable at 27V and the current is stable at 0-35A, which meets the design requirements.
3 Challenges of LED Power Supply
As a new type of electric light source, LED has obvious advantages in making large luminous three-dimensional characters and luminous signs. It has low control voltage, low cost and high reliability. Although LED products have an increasingly strong development trend in the domestic and foreign markets, LED lighting is an emerging industry after all and has not yet been widely popularized. Therefore, LED driver power supply inevitably has challenges in various aspects: First, since the forward voltage of the LED will change with the current and temperature, its "color point" will also drift with the current and temperature. In order to ensure the normal operation of the LED, its driver is required to limit the current regardless of the input conditions and forward voltage changes. Secondly, if LED dimming is required, pulse width modulation dimming technology is usually used, and the typical PWM frequency is 1~3kHz. Finally, the power handling capacity of the LED driver circuit must be sufficient and the function must be strong, able to withstand a variety of fault conditions, and easy to implement.
4 Conclusion
LED is a kind of energy-saving, efficient and environmentally friendly green lighting, so the research on its driving circuit is very important. This paper introduces the LED driving power supply designed by MIP553, and proves the stability of its output current through simulation, which has a good application prospect.
Previous article:IC Troubleshooting and Failure Analysis: Find the Facts and Avoid Guesswork
Next article:Difficulties in LTE Testing
Recommended ReadingLatest update time:2024-11-16 16:01
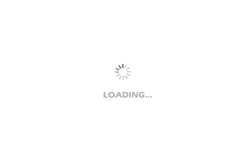
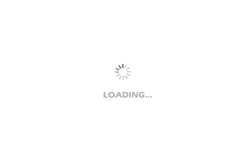
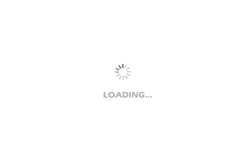
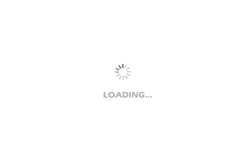
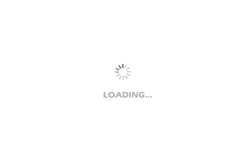
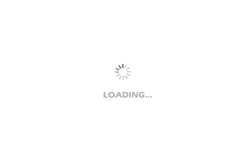
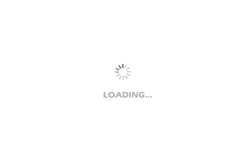
- Popular Resources
- Popular amplifiers
-
MCU C language programming and Proteus simulation technology (Xu Aijun)
-
100 Examples of Microcontroller C Language Applications (with CD-ROM, 3rd Edition) (Wang Huiliang, Wang Dongfeng, Dong Guanqiang)
-
Research on three-phase all-solid-state high-efficiency LED tunnel lighting system based on chip drive_Li Jian
-
Follow me Season 2 Episode 1 All Code + Library
- High signal-to-noise ratio MEMS microphone drives artificial intelligence interaction
- Advantages of using a differential-to-single-ended RF amplifier in a transmit signal chain design
- ON Semiconductor CEO Appears at Munich Electronica Show and Launches Treo Platform
- ON Semiconductor Launches Industry-Leading Analog and Mixed-Signal Platform
- Analog Devices ADAQ7767-1 μModule DAQ Solution for Rapid Development of Precision Data Acquisition Systems Now Available at Mouser
- Domestic high-precision, high-speed ADC chips are on the rise
- Microcontrollers that combine Hi-Fi, intelligence and USB multi-channel features – ushering in a new era of digital audio
- Using capacitive PGA, Naxin Micro launches high-precision multi-channel 24/16-bit Δ-Σ ADC
- Fully Differential Amplifier Provides High Voltage, Low Noise Signals for Precision Data Acquisition Signal Chain
- Innolux's intelligent steer-by-wire solution makes cars smarter and safer
- 8051 MCU - Parity Check
- How to efficiently balance the sensitivity of tactile sensing interfaces
- What should I do if the servo motor shakes? What causes the servo motor to shake quickly?
- 【Brushless Motor】Analysis of three-phase BLDC motor and sharing of two popular development boards
- Midea Industrial Technology's subsidiaries Clou Electronics and Hekang New Energy jointly appeared at the Munich Battery Energy Storage Exhibition and Solar Energy Exhibition
- Guoxin Sichen | Application of ferroelectric memory PB85RS2MC in power battery management, with a capacity of 2M
- Analysis of common faults of frequency converter
- In a head-on competition with Qualcomm, what kind of cockpit products has Intel come up with?
- Dalian Rongke's all-vanadium liquid flow battery energy storage equipment industrialization project has entered the sprint stage before production
- Allegro MicroSystems Introduces Advanced Magnetic and Inductive Position Sensing Solutions at Electronica 2024
- Car key in the left hand, liveness detection radar in the right hand, UWB is imperative for cars!
- After a decade of rapid development, domestic CIS has entered the market
- Aegis Dagger Battery + Thor EM-i Super Hybrid, Geely New Energy has thrown out two "king bombs"
- A brief discussion on functional safety - fault, error, and failure
- In the smart car 2.0 cycle, these core industry chains are facing major opportunities!
- The United States and Japan are developing new batteries. CATL faces challenges? How should China's new energy battery industry respond?
- Murata launches high-precision 6-axis inertial sensor for automobiles
- Ford patents pre-charge alarm to help save costs and respond to emergencies
- New real-time microcontroller system from Texas Instruments enables smarter processing in automotive and industrial applications
- 【AT32F421 Review】+ COMP Comparator Usage
- Communication protocol conversion
- New live broadcast calendar
- LOTO Practice [Dry Goods] 2- Quick Application of Voltage Comparator
- GD32E230C Test 2: I2C and EEPROM
- 【XMC4800 Relax EtherCAT Kit Review】+DAVE integrated development environment construction and demo operation
- Design of data acquisition card based on FPGA.pdf
- Xunwei 4412 development board cross-compiles Qt application code
- Actual development and experience of the first phase
- 【National Technology N32G430】02 Small expansion, communication from top to bottom