introduction
The power amplifier has entered the digital age. The key integrated circuits of digital power amplifiers have reached a relatively high level. For example, the TDA8902J digital power amplifier effectively reduces the interference between signals and can achieve high fidelity. Although the core technology has been solved, it is difficult to achieve the desired effect if the printed circuit board (PCB) is not properly wired. The author has summarized some experience in the PCB design process of the TDA8902J digital power amplifier. Now, a brief analysis and introduction is made on the wiring principles, anti-interference design requirements and electromagnetic compatibility requirements that should be followed in PCB design.
1 PCB layout and wiring principles
PCB provides electrical connections between components of the power amplifier circuit. To achieve the best performance of the power amplifier circuit, the layout of components and the arrangement of printed conductors are key.
1.1 Layout principles
(1) The power tube of the digital amplifier works in the switching state, with high frequency, large current, and close to the power supply part. Since the power amplifier (as shown in Figure 1-1) is powered by a switching power supply (not shown in the figure), the interference and ripple coefficient are large. Therefore, the arrangement of components on the PCB should take into account anti-electromagnetic interference, and the leads between the components should be as short as possible. In terms of layout, the three parts of analog signals, digital signals and noise sources should be reasonably separated to minimize the coupling between them. That is, the analog input part connected to the LM4651⑩ pin should be separated from other digital parts, and the power input and decoupling filter components should also be separated from the digital processing part. In addition, the directionality of the power transformer should also be considered to minimize the radiation to the circuit.

(2) The components should be arranged in the order of output filter, H-bridge circuit, comparator, oscillator generator, and voltage amplifier. If the various levels are arranged crosswise, they are likely to affect each other and cause self-excitation or absorption.
(3) Components with strong electromagnetic field radiation (such as L3, L2) and components that are sensitive to electromagnetic induction (R1, C1, R5, C3) should be shielded or kept away from electromagnetic field radiation sources to reduce interference.
(4) Shorten the connection between high-frequency components (such as R5 and C3) as much as possible, and try to reduce their distributed parameters and mutual electromagnetic interference. Components susceptible to interference should not be too close to each other, and input and output components should be kept as far away as possible.
(5) Some components or wires have a high potential difference, so the distance between them should be increased to avoid accidental short circuits caused by discharge. For example, the ⑤ and ⑦ pins of TDA8902J and the ① and ③ pins of LH4652 should not be too close to each other. Components with high voltage (such as power switches) should be placed where they are not easily touched by hands during debugging.
1.2 Wiring Principles
(1) The wires used for the input and output terminals (such as R8 and L1) should be kept away from being parallel to each other. It is best to add a ground wire between the wires to avoid feedback coupling.
(2) The routing of each level should be as short as possible, and the components should be as close as possible. Pay more attention to the routing of large signals and high impedance. For example, the routing of R11 and C18 should be as short as possible, and the audio input (C1, R1) and output (L1, L2) lines should not be too long, otherwise it is easy to sense AC signals.
(3) The minimum width of the wire is mainly determined by the adhesion strength between the wire and the insulating substrate and the current value flowing through them. When the copper foil thickness is 0.05mm and the width is 1-15mm, the temperature will not be higher than 3°C when a current of 2A passes through it. The amplifier can select a wire width of 0.5-5mm. The minimum spacing of the wires is mainly determined by the insulation resistance and breakdown voltage between the wires in the worst case, and the spacing can be as small as 5-8mm.
(4) The bends of printed conductors are generally in the shape of arcs, while right angles or included angles will affect the electrical performance in high-frequency circuits. Figure 1-2 (a), (b), and (c) show three types of corner lines. The transmission performance and reflection performance of the 45° external bevel corner line in Figure (C) are better than those of the other two types of corner lines. The performance of the arc corner line is better than these three types of routing, but the engraving of the arc has relatively high requirements for the board making process, which will increase the production cost. The power amplifier uses a 45° external bevel corner routing to meet the design requirements.

2 Anti-interference design measures
The anti-interference design of PCB has different requirements for different circuits. The following discusses the PCB anti-interference design measures of the power amplifier from three aspects.
2.1 Power Cord Design
In the DC power supply loop, changes in load will cause power supply noise. According to the size of the PCB current, try to increase the width of the power line to reduce the loop resistance. The power supply routing of the LM4651L part of the power amplifier circuit can meet the requirements with a wire width of 1.5mm, while the LM4652 part requires 3 to 5mm. At the same time, the direction of the power line and the ground line is consistent with the direction of data transmission, which helps to enhance the anti-noise ability.
2.2 Ground wire design
The ground wire is more important than the power wire. The most important means to overcome electromagnetic interference is the design of the ground wire. The wiring of the ground wire is particularly particular, and the single-point grounding method is usually adopted. The analog ground, digital ground and high-power device ground are separated and finally gathered to the power ground. The ground wire structure of the power amplifier includes system ground, chassis ground, digital ground and analog ground. The design principles of the ground wire are:
(1) Separate the digital ground from the analog ground. The amplifier has both logic circuits and linear circuits, which should be separated as much as possible and connected to the ground wire of the power supply end respectively, and the grounding area of the linear circuit should be increased as much as possible. The analog audio ground should be connected to the ground at a single point as much as possible.
(2) The ground wire should be as thick as possible. If the ground wire is very thin, the ground potential will change with the change of current, causing the signal level of the power amplifier circuit to be unstable and the anti-noise performance to deteriorate. Usually, the ground wire can pass three times the current. The ground wire of the power amplifier should be more than 3 to 6 mm.
(3) Correctly choose single-point grounding and multi-point grounding. The analog part of the power amplifier has a low operating frequency, and its wiring and the inductance between the devices have little effect, while the loop current formed by the grounding circuit has a greater impact on interference, so single-point grounding should be used. When the operating frequency of the digital part is greater than 10MHz, the ground impedance becomes very large. At this time, the ground impedance should be reduced as much as possible and multiple points should be grounded nearby. When the operating frequency is between 1-10MHz, if single-point grounding is used, the ground length should not exceed 1/20 of the wavelength, otherwise multi-point grounding should be used. Although the switching frequency of the digital part of the power amplifier is 125kHz, it is better to use multi-point grounding due to the influence of harmonics.
(4) Make the ground wire a closed loop. For the PCB of a digital power amplifier, designing the ground wire into a closed loop can significantly improve the anti-noise ability. The reason is that there are many power-consuming components in the circuit. Due to the limitation of the thickness of the ground wire, a large potential difference will be generated on the ground wire, causing the anti-noise ability to decrease. If the ground wire is formed into a loop, the potential difference will be reduced, thereby improving the anti-noise ability of the power amplifier circuit.
2.3 Signal Line Design
When connecting to weak signals outside the PCB, shielded cables are usually used. For high-frequency and digital signals, both ends of the shielded cable are grounded. The shielded cable used for the analog audio signal of this amplifier is preferably grounded at one end. The signal traces in the PCB should be as short as possible and avoid interference sources.
3 Electromagnetic compatibility (EMC) design
A simple electromagnetic interference model consists of three parts, as shown in Figure 3-1. The power amplifier contains a switching power supply and a high-power, high-current drive circuit, as well as a system containing a weak analog signal circuit and a high-precision A/D conversion circuit. Electromagnetic interference is inevitable. The purpose of EMC design is to enable the power amplifier to suppress various external interferences while reducing its own electromagnetic interference to other electronic equipment.

3.1 EMC measures in PCB design
The amplifier pays attention to different layout areas, making the routing width of the dedicated zero-volt line and power line ≥1mm, the power supply and ground are distributed in a "well" shape, the distribution line current is balanced, and a zero-volt line is provided for the analog circuit. In order to reduce crosstalk between lines, the printed line spacing is increased, and several zero-volt lines are inserted as line isolation. The PCB plug also arranges two more zero-volt lines as line isolation. Special attention is paid to the size of the wire loop in the current flow.
3.2 EMC of switching power supplies for PCB
While supplying power to the amplifier, the power supply also adds noise to the circuit. The signal input, oscillation and control parts of the amplifier circuit are most susceptible to interference from external noise. Strong interference on the power grid enters the circuit through the power supply, and the analog signal in the circuit is most susceptible to interference from the power supply. The conducted and radiated interference of the power supply to the power grid is the common mode noise generated at the power input end by the nonlinear flow and the coupling between the power transistor housing and the heat sink in the primary circuit.
The power supply has trimmed the switching voltage waveform, installed an insulating gasket with a shielding layer between the transistor and the heat sink, added a mutual inductance filter to the AC input end, reduced the loop area, and connected a polyester film capacitor in parallel to the soft recovery diode used in the secondary rectification circuit, thereby greatly improving the switching voltage waveform.
3.3 EMC of transmission lines
Coaxial cable has good anti-electromagnetic interference ability. The coaxial cable used in the power amplifier signal line is from the United States AUDIOOUEST (Line Saint), which adopts single-end grounding to reduce the loop current for magnetic induction and enhance the magnetic field shielding performance.
4 Conclusion
The digital power amplifier based on TDA8902J has high power, low heat loss, good sound quality and small size. After electromagnetic compatibility design of its PCB, the sound quality is better, the signal-to-noise ratio is higher, and the anti-interference ability is also significantly enhanced. It can be applied to many audio devices, such as sound cards, active speakers, car audio, etc., and has broad prospects.
Previous article:Design of weak signal amplification circuit
Next article:Multi-mode Class K amplifier with super strong TDD suppression
Recommended ReadingLatest update time:2024-11-16 15:53
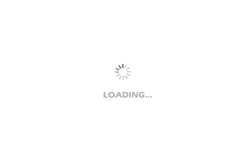
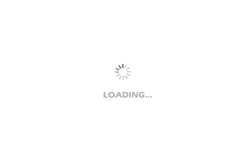
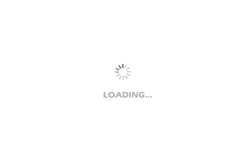
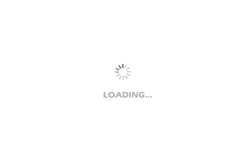
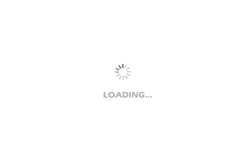
- High signal-to-noise ratio MEMS microphone drives artificial intelligence interaction
- Advantages of using a differential-to-single-ended RF amplifier in a transmit signal chain design
- ON Semiconductor CEO Appears at Munich Electronica Show and Launches Treo Platform
- ON Semiconductor Launches Industry-Leading Analog and Mixed-Signal Platform
- Analog Devices ADAQ7767-1 μModule DAQ Solution for Rapid Development of Precision Data Acquisition Systems Now Available at Mouser
- Domestic high-precision, high-speed ADC chips are on the rise
- Microcontrollers that combine Hi-Fi, intelligence and USB multi-channel features – ushering in a new era of digital audio
- Using capacitive PGA, Naxin Micro launches high-precision multi-channel 24/16-bit Δ-Σ ADC
- Fully Differential Amplifier Provides High Voltage, Low Noise Signals for Precision Data Acquisition Signal Chain
- Innolux's intelligent steer-by-wire solution makes cars smarter and safer
- 8051 MCU - Parity Check
- How to efficiently balance the sensitivity of tactile sensing interfaces
- What should I do if the servo motor shakes? What causes the servo motor to shake quickly?
- 【Brushless Motor】Analysis of three-phase BLDC motor and sharing of two popular development boards
- Midea Industrial Technology's subsidiaries Clou Electronics and Hekang New Energy jointly appeared at the Munich Battery Energy Storage Exhibition and Solar Energy Exhibition
- Guoxin Sichen | Application of ferroelectric memory PB85RS2MC in power battery management, with a capacity of 2M
- Analysis of common faults of frequency converter
- In a head-on competition with Qualcomm, what kind of cockpit products has Intel come up with?
- Dalian Rongke's all-vanadium liquid flow battery energy storage equipment industrialization project has entered the sprint stage before production
- Allegro MicroSystems Introduces Advanced Magnetic and Inductive Position Sensing Solutions at Electronica 2024
- Car key in the left hand, liveness detection radar in the right hand, UWB is imperative for cars!
- After a decade of rapid development, domestic CIS has entered the market
- Aegis Dagger Battery + Thor EM-i Super Hybrid, Geely New Energy has thrown out two "king bombs"
- A brief discussion on functional safety - fault, error, and failure
- In the smart car 2.0 cycle, these core industry chains are facing major opportunities!
- The United States and Japan are developing new batteries. CATL faces challenges? How should China's new energy battery industry respond?
- Murata launches high-precision 6-axis inertial sensor for automobiles
- Ford patents pre-charge alarm to help save costs and respond to emergencies
- New real-time microcontroller system from Texas Instruments enables smarter processing in automotive and industrial applications
- [National Technology N32G457 Review] RT_Thread solves the problem that SPI NSS cannot be pulled low
- [Silicon Labs BG22-EK4108A Bluetooth Development Review] 1: IoT product introduction and BLE environment construction
- How does the company evaluate working from home?
- Advanced FPGA Design is a must-read for beginners of FPGA
- LM358 pin diagram, function description and working principle detailed explanation
- IIC protocol based on STM8--Example--Clock module (DS3231) reading
- A Implementation of Serial Interface Based on PCI Bus
- How to quickly design an infrared thermometer? Texas Instruments gives you tips!
- 【McQueen Trial】Blink
- EEWORLD University Hall----Design using TI's series capacitor buck converter