introduction
Capacitive sensors have a series of advantages such as simple structure, high sensitivity, good temperature stability, strong adaptability, good dynamic performance, etc. At present, they are widely used in detection technology not only for the measurement of mechanical quantities such as displacement, vibration, angle, acceleration, but also for the measurement of thermal aspects such as liquid level, pressure, component content, etc. However, since the initial capacitance of the capacitive sensor is very small, generally at the pico-farad level, the parasitic capacitance formed by the lead cable capacitance connecting the sensor and the electronic circuit, the stray capacitance of the electronic circuit, and the capacitance formed by the internal plate of the sensor and the surrounding conductor is relatively large, which not only reduces the sensitivity of the sensor, but also these capacitances change randomly, making the instrument very unstable, thus affecting the measurement accuracy, and even making the sensor unable to work properly, so it is necessary to try to eliminate the influence of parasitic capacitance on the capacitive sensor. The following analyzes several methods for eliminating parasitic capacitance of capacitive sensors.
Increase initial capacitance value method
By increasing the initial capacitance value, the parasitic capacitance can be reduced relative to the capacitance of the capacitive sensor.
It can be seen that by reducing the spacing d0 between the pole pieces or pole cylinders, such as the flat plate spacing can be reduced to 0.2 mm, the cylindrical spacing can be reduced to 0.15 mm; or covering a layer of glass medium between the two electrodes to increase the relative dielectric constant, it is found through experiments that the initial capacitance C0 of the sensor is not only significantly improved, but also prevents the short circuit between the two electrodes when overloaded; In addition, increasing the working area A or the working length can also increase the initial capacitance value C0. However, this method is subject to the limitations of processing technology and assembly technology, accuracy, indication range, breakdown voltage, etc., and the general capacitance change value is between 10-3 and 103pF.
Use "drive cable" technology to reduce parasitic capacitance
As shown in Figure 1: A double-layer shielded cable is used between the piezoelectric sensor and amplifier A, and connected to a drive amplifier with a gain of 1. This connection method can make the inner shield and the core wire have the same potential, thereby eliminating the capacitive leakage of the core wire to the inner shield and overcoming the influence of parasitic capacitance. The capacitance Cx between the inner and outer layers becomes the load of the drive amplifier. Due to the limitation of geometric size, the capacitance of the capacitive sensor is very small, generally only a few pF to tens of pF. Because C is too small, the capacitive reactance XC=1/ωc is very large, which is a high impedance component; therefore, the drive amplifier can be regarded as a common-mode amplifier with a high input impedance, capacitive load, and an amplification factor of 1.
Figure 1
Operational amplifier driving method
Using the "drive cable" method to eliminate parasitic capacitance means strictly achieving the drive amplifier's gain of 1 over a wide frequency band, and the input and output phase shift is zero, which is a difficult design problem. The operational amplifier drive method can effectively solve this problem. As shown in Figure 2: (-Aa) is the drive cable amplifier, its input is the output of the (-A) amplifier, and the input capacitance of the (-Aa) amplifier is the load of the (-A) amplifier. Therefore, there is no additional capacitance in parallel with Cx, and the voltage across the sensor capacitance Cx is
The output voltage of the amplifier (-Aa) is
To achieve equal potential between the cable core and the inner shield, UCX = Uo3, so we can get: (1 + A) *Uo1 = A*Aa*Uo1,
Right now
The operational amplifier driving method does not require any additional capacitance and is particularly suitable for detection circuits where the sensor capacitance is very small.
Figure 2
Overall shielding method
Shielding technology is to use the good absorption and reflection ability of metal materials for electromagnetic waves to resist interference. According to the characteristics of electromagnetic interference, good low-resistance conductive materials or magnetic materials are selected to form a suitable shield. The role of the shield is like connecting a short circuit line in parallel at both ends of an equivalent resistor. When useless signals are connected in series, they directly pass through the short circuit line and have no effect on the equivalent resistor. Now take the differential capacitive sensor as an example to illustrate the application of the overall shielding method. In Figure 3, CX1 and CX2 are used as differential capacitors, U is the power supply, and A is the amplifier. The overall shielding method is to shield the entire bridge (including power cables, etc.) in the figure together. The key point of this method design lies in the reasonable setting of the grounding point. The grounding point is placed between the two balancing resistors R1 and R2, and is shared with the overall shield. In this way, the parasitic capacitance C1 between the common plate of the sensor and the shield is connected in parallel with the input impedance of the measuring amplifier, so that C1 can be regarded as the input capacitance of the amplifier. Since the input impedance of the amplifier should have a very large value, the parallel connection of C1 is not desirable, but it only affects the sensitivity of the sensor and has no effect on other performance. The other two parasitic capacitors C3 and C4 are connected in parallel to the two bridge arms R1 and R2 respectively, which will affect the initial balance and overall sensitivity of the bridge, but will not affect the normal operation of the bridge. Therefore, the influence of parasitic parameters on the sensor capacitance can be basically eliminated. The overall shielding method is a good way to solve the parasitic capacitance problem of capacitive sensors, but its disadvantage is that it makes the structure more complicated.
Figure 3
In addition, the integration method is also an effective way to eliminate the parasitic capacitance interference of capacitive sensors. This method is to encapsulate the sensor and the pre-stage of the electronic circuit in a shell, eliminating the cable from the sensor to the pre-amplifier stage. In this way, the parasitic capacitance can be greatly reduced and kept fixed, so that the instrument is in a stable working state. However, this method cannot be used normally in places with relatively high temperatures or harsh environments due to the presence of electronic components. The integration process can also be used to integrate the sensor and the conditioning circuit into the same chip to form an integrated capacitive sensor.
In short, the capacitance value of capacitive sensors is very small, generally in the picofarad level, and the distributed capacitance generated by the connecting wire is also in the picofarad level, which will affect the measurement accuracy. Therefore, we require that the connecting wire between the sensor and the conversion circuit use high-frequency cables with extremely small distributed capacitance, and try to shorten the distance between the sensor and the conversion circuit. If conditions permit, the sensor, connecting wire, and conversion circuit can be shielded as a whole.
Previous article:The principle and method of filtering harmonic interference by active power filter on DC side
Next article:Best Design Solution for ESD Protection of High-Speed Circuits
Recommended ReadingLatest update time:2024-11-16 20:58
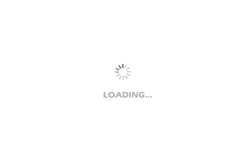
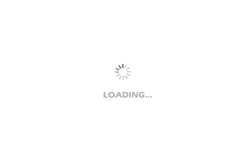
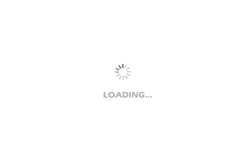
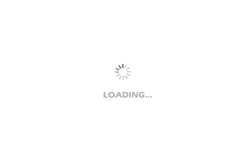
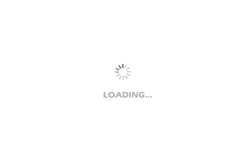
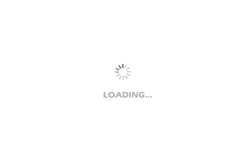
- Popular Resources
- Popular amplifiers
-
Analysis and Implementation of MAC Protocol for Wireless Sensor Networks (by Yang Zhijun, Xie Xianjie, and Ding Hongwei)
-
Introduction to Internet of Things Engineering 2nd Edition (Gongyi Wu)
-
西门子S7-12001500 PLC SCL语言编程从入门到精通 (北岛李工)
-
Modern Motor Control Technology (Wang Chengyuan, Xia Jiakuan, Sun Yibiao)
- High signal-to-noise ratio MEMS microphone drives artificial intelligence interaction
- Advantages of using a differential-to-single-ended RF amplifier in a transmit signal chain design
- ON Semiconductor CEO Appears at Munich Electronica Show and Launches Treo Platform
- ON Semiconductor Launches Industry-Leading Analog and Mixed-Signal Platform
- Analog Devices ADAQ7767-1 μModule DAQ Solution for Rapid Development of Precision Data Acquisition Systems Now Available at Mouser
- Domestic high-precision, high-speed ADC chips are on the rise
- Microcontrollers that combine Hi-Fi, intelligence and USB multi-channel features – ushering in a new era of digital audio
- Using capacitive PGA, Naxin Micro launches high-precision multi-channel 24/16-bit Δ-Σ ADC
- Fully Differential Amplifier Provides High Voltage, Low Noise Signals for Precision Data Acquisition Signal Chain
- Innolux's intelligent steer-by-wire solution makes cars smarter and safer
- 8051 MCU - Parity Check
- How to efficiently balance the sensitivity of tactile sensing interfaces
- What should I do if the servo motor shakes? What causes the servo motor to shake quickly?
- 【Brushless Motor】Analysis of three-phase BLDC motor and sharing of two popular development boards
- Midea Industrial Technology's subsidiaries Clou Electronics and Hekang New Energy jointly appeared at the Munich Battery Energy Storage Exhibition and Solar Energy Exhibition
- Guoxin Sichen | Application of ferroelectric memory PB85RS2MC in power battery management, with a capacity of 2M
- Analysis of common faults of frequency converter
- In a head-on competition with Qualcomm, what kind of cockpit products has Intel come up with?
- Dalian Rongke's all-vanadium liquid flow battery energy storage equipment industrialization project has entered the sprint stage before production
- Allegro MicroSystems Introduces Advanced Magnetic and Inductive Position Sensing Solutions at Electronica 2024
- Car key in the left hand, liveness detection radar in the right hand, UWB is imperative for cars!
- After a decade of rapid development, domestic CIS has entered the market
- Aegis Dagger Battery + Thor EM-i Super Hybrid, Geely New Energy has thrown out two "king bombs"
- A brief discussion on functional safety - fault, error, and failure
- In the smart car 2.0 cycle, these core industry chains are facing major opportunities!
- The United States and Japan are developing new batteries. CATL faces challenges? How should China's new energy battery industry respond?
- Murata launches high-precision 6-axis inertial sensor for automobiles
- Ford patents pre-charge alarm to help save costs and respond to emergencies
- New real-time microcontroller system from Texas Instruments enables smarter processing in automotive and industrial applications
- [RVB2601 Creative Application Development] + A Preliminary Study on Connecting to Alibaba Cloud
- [RVB2601 Creative Application Development] Practice 3 - External DHT11 Display of Temperature and Humidity
- Top 5 Microcontroller Board Features
- MSA-AIAG-Manual 4
- Solution to power supply problem of MCU based on SE8510
- Basics | Learn the basics of "amplifier" in 5 minutes
- LC filter circuit parameter design verification
- Fresh and hot, aircraft cabin pressure and temperature data recorded by SensorTile.box
- 2020 TI Cup Analog Electronic System Design Invitational Competition
- Qorvo UWB helps Shenzhentong enter the era of smart travel