1. Introduction
As the core equipment of converter steelmaking, the safe, efficient and stable operation of the primary extraction fan is related to whether the entire steelmaking system is stable and smooth. At the same time, as the key equipment for steelmaking gas recovery, the primary extraction fan also affects the environmental protection, energy recovery and negative energy steelmaking of the entire steelmaking. Therefore, ensuring the stability and efficiency of the primary extraction fan has become the first issue to be considered by a steelmaking plant. The Third Steelmaking Plant of Jigang Group currently has three 120-ton converters, corresponding to which are three primary extraction fans. In actual application, due to various failures of the primary extraction fans, the normal production of the converter is affected. In order to completely solve this problem that plagues production, the Third Steelmaking Plant decided to install a new spare primary extraction fan as a backup fan for the other three fans. The three converters of the Third Steelmaking Plant of Jigang were put into production in two phases. Due to engineering reasons, the industrial Ethernet used in the two phases is not on the same network segment, and the new backup fan must be a backup for all fans, so we must realize PLC cross-segment communication. Template, power supply and baseboard. The CPU is a high-performance programmable controller system based on 486, 586 and Pentium processors, compatible with Unit
2, QUANTUM automatic control platform introduction
2, 1 Hardware platform introduction
Quantum system is a special computer system with digital quantity processing capabilities. Quantum has a modular and scalable architecture for real-time control of industrial and manufacturing processes. It includes Quantum series CPU, I/O templates, I/O interfaces, and communication Pro software. Some of the features implemented in the CPU are:
● Superior scan time and I/O throughput.
● Ability to handle timed interrupts and I/O-based interrupts.
● Can handle fast tasks and main tasks.
● Memory expansion can be carried out through PCMCIA memory expansion cards.
● Multiple communication interfaces are built into the CPU.
● On the front panel of high-end models, it is equipped with a user-friendly diagnostic and operation LCD display.
The Quantum system provides a variety of options for open, standard-based network connections and fieldbus connections. The networks supported by Quantum include: Modbus Plus, Modbus, TCP/IP, SY/MAX Ethernet modules, remote I/O modules, hot standby modules (Concept/ProWORX), etc. The combination of these networks can be used to ensure a simple, high-performance communication structure that closely meets the integration requirements of computer and controller connections.
TCP/IP Ethernet is the communication method used by our fan system. Cross-segment system communication is the focus of our electrical system transformation. The Quantum automatic control platform provides us with a powerful Ethernet template, NOE771XX series products. This series is compatible with Unity Pro, Concept, ProWORX and other software, and has standard web pages, Modbus TCP messages, I/O Scanning services, FDR clients, SNMP management and other functions.
2.2 Software Platform
Schneider's Concept software platform is a PLC configuration and programming software based on the Schneider Quantum hardware platform. It is practical and powerful and is a mature software platform.
Concept complies with the international standard IEC 1131-3 and provides a unified configuration environment. The guiding principle in the development of Concept was that all system configuration programs as well as all editors should have the same look and feel. Most steps of the configuration, especially program creation, are designed independently of the PLC to be programmed. The entire program is divided into sections corresponding to the logical structure, and the Concept configuration tool allows objects (such as function blocks, steps and transitions) to be easily selected, placed or moved in a graphical manner. The feasibility test already takes place in the SFC (Sequential Function Chart/Sequential Language) editor during object placement, because most of the connections between objects are automatically generated during placement. In the FBD editor (Function Block Diagram/Function Block Language) and the LD editor (Ladder Diagram), the feasibility test takes place when the blocks are connected to each other. Unauthorized connections, such as those between different data types, are deleted during configuration. The feasibility test also takes place during placement in the LL984 editor (Ladder Logic 984). In the IL editor (Instruction List) and the ST editor (Structured Text), unauthorized instructions can be identified by a colored outline. After the first successful run of the program, the program can be optimized in graphical mode by moving connected blocks and text to improve the display.
3. Implementation of cross-segment control using the QUANTUAM platform
3.1 Analysis of the actual situation
Figure 2: Ideal ring network topology
In the Concept hardware configuration table, configure as shown in Figure 2:
Figure 3: PLC NOE module configuration table
For the two NOE network modules configured in the table, configure different network addresses respectively, as shown in Figure 4, to realize the cross-segment hardware link of PLC.
Figure 4: NOE module IP configuration
In this way, we have completed the cross-segment connection at the PLC level in the hardware link. After actual testing, the network is unobstructed and data exchange is normal.
3.2.2 Software programming to realize
the interlocking PLC related to converter No. 1 and fan
Interlocking PLC related to converter No. 2 and fan
Standby fan start register 400001
Interlocking PLC related to converter No. 3 and fan
After the hardware is realized, we need to realize the normal exchange of data flow in the two network segments in software programming. The key registers in the standby fan, such as fan start and stop, need to be connected with the main control PLC in different network segments, as shown in Figure 5.
Figure 5: Key data communication method
In this case, the standby fan needs to establish a channel with each master PLC on each network segment, which means that the number of channels required by the standby fan is three times that of the online fan. Each master PLC needs to establish a channel with both the standby fan and the online fan at the same time, and the programs of each system need to be modified, which is impossible to achieve without affecting normal production. For this reason, we let the standby fan only establish a data exchange channel with the online fan, and use the original fan's channel to communicate with other master PLCs when the standby fan is in operation, as shown in Figure 6. This greatly reduces the impact of the transformation on each master PLC and also reduces the risk of transformation.
Figure 6: Data channel implementation
After actual application tests, this method has stably and reliably realized the backup of the online fans on different network segments and ensured the continuity of converter production.
4. Conclusion
Through this transformation, the backup primary extraction fan of the Third Steelmaking Plant of Jigang was successfully put into use, laying a solid foundation for the stable and high production of the Third Steelmaking Plant. How to use the existing automation control platform more flexibly and efficiently and maximize its role has become the main topic of our next study.
Previous article:Direct-drive wind power grid-connected converter device
Next article:Research on CCM Control Strategy of Three-Phase Dual-Switch Four-Wire PFC Circuit
Recommended ReadingLatest update time:2024-11-16 19:52
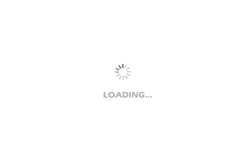
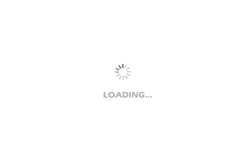
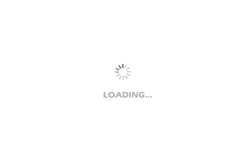
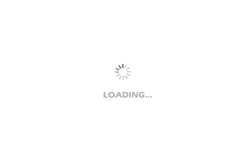
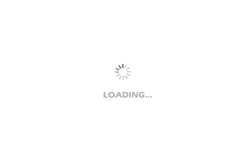
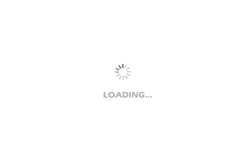
- Popular Resources
- Popular amplifiers
- Molex leverages SAP solutions to drive smart supply chain collaboration
- Pickering Launches New Future-Proof PXIe Single-Slot Controller for High-Performance Test and Measurement Applications
- CGD and Qorvo to jointly revolutionize motor control solutions
- Advanced gameplay, Harting takes your PCB board connection to a new level!
- Nidec Intelligent Motion is the first to launch an electric clutch ECU for two-wheeled vehicles
- Bosch and Tsinghua University renew cooperation agreement on artificial intelligence research to jointly promote the development of artificial intelligence in the industrial field
- GigaDevice unveils new MCU products, deeply unlocking industrial application scenarios with diversified products and solutions
- Advantech: Investing in Edge AI Innovation to Drive an Intelligent Future
- CGD and QORVO will revolutionize motor control solutions
- Innolux's intelligent steer-by-wire solution makes cars smarter and safer
- 8051 MCU - Parity Check
- How to efficiently balance the sensitivity of tactile sensing interfaces
- What should I do if the servo motor shakes? What causes the servo motor to shake quickly?
- 【Brushless Motor】Analysis of three-phase BLDC motor and sharing of two popular development boards
- Midea Industrial Technology's subsidiaries Clou Electronics and Hekang New Energy jointly appeared at the Munich Battery Energy Storage Exhibition and Solar Energy Exhibition
- Guoxin Sichen | Application of ferroelectric memory PB85RS2MC in power battery management, with a capacity of 2M
- Analysis of common faults of frequency converter
- In a head-on competition with Qualcomm, what kind of cockpit products has Intel come up with?
- Dalian Rongke's all-vanadium liquid flow battery energy storage equipment industrialization project has entered the sprint stage before production
- Allegro MicroSystems Introduces Advanced Magnetic and Inductive Position Sensing Solutions at Electronica 2024
- Car key in the left hand, liveness detection radar in the right hand, UWB is imperative for cars!
- After a decade of rapid development, domestic CIS has entered the market
- Aegis Dagger Battery + Thor EM-i Super Hybrid, Geely New Energy has thrown out two "king bombs"
- A brief discussion on functional safety - fault, error, and failure
- In the smart car 2.0 cycle, these core industry chains are facing major opportunities!
- The United States and Japan are developing new batteries. CATL faces challenges? How should China's new energy battery industry respond?
- Murata launches high-precision 6-axis inertial sensor for automobiles
- Ford patents pre-charge alarm to help save costs and respond to emergencies
- New real-time microcontroller system from Texas Instruments enables smarter processing in automotive and industrial applications
- Analyzing the basic steps of FPGA power supply design
- [RVB2601 Creative Application Development] Audio Playback
- MSP430F5529&LCD1602 Program
- Bluetooth Direction Finding Technology Overview
- How to automatically fan out BGA in Kicad
- Crazy Shell AI open source drone flight control firmware burning
- Problems affecting IC card reading distance
- How to design hollow fonts
- Three considerations for selecting Ethernet for harsh industrial environments
- dB, why is it so important for RF engineers?