0 Introduction
Pollution from the papermaking industry is one of the main sources of industrial pollution in the world. More than 80% of the pollution load in the pulp and paper industry comes from pulping black liquor. If black liquor cannot be effectively treated, it will not only seriously pollute the environment, but also cause a large amount of waste of resources. Alkali recovery is currently the most effective and mature means of treating black liquor. It can not only effectively recover the alkali in black liquor, but also use the heat generated by the combustion of black liquor to produce steam, and the steam and alkali can be reused in other production processes in the papermaking industry. Therefore, the alkali recovery system is an indispensable part of solving the black liquor pollution and resource recycling of pulping enterprises, and has good environmental and economic benefits. It can be seen that alkali recovery has a very important position and significance in the pulp and paper industry. [1]
The alkali recovery workshop is generally divided into three sections: evaporation, combustion and causticization. The new alkali recovery system is listed as one of the important frontier issues in the papermaking industry.
Fieldbus technology is a new control technology that is currently emerging. The most popular fieldbus technologies are: Profibus, Foundation Fieldbus FF, etc. Profibus is an international, open, and manufacturer-independent bus standard. It consists of three compatible parts: ①ProfibusS2DP; the master station and the slave station communicate in a round-robin manner, which is used for device-level control systems and distributed I/O communications; ②Profibus2PA, power supply and communication data are transmitted in parallel through the bus, which allows sensors and actuators to be connected through a bus, mainly used for unit-level and field-level communications; ③Profibus2FMS, used for workshop-level monitoring networks, is a token-structured, real-time multi-master network.
This paper briefly introduces the control scheme of computer distributed control implemented by the author in the alkali recovery section of a paper mill in Henan Province using ProfiBus fieldbus.
1 Process flow and control strategy
The main equipment of the evaporation section is the evaporator, which is connected in series to form an evaporation station. The evaporation station controlled in this design is a typical five-body five-effect evaporation system. In addition to the relevant control of the evaporator, there are also some auxiliary evaporation equipment, such as plate falling film evaporator, warm water tank, black liquor tank, condensate flash tank, liquid level tank, etc. The goal of system control is to maintain the stability of the concentration of the concentrated black liquor, the stability of the total effective temperature difference and the stability of the condensate tank level. It can generally be divided into steam subsystem, black liquor subsystem and condensate system. The main control objectives of this section are to ensure the concentration of the black liquor, the stability of the total effective temperature difference and the stability of the condensate system. This section has 11 pressure measurement links including the steam pressure and vacuum degree of each effect, 17 liquid level measurement links including the black liquor level of each effect evaporator, condensate flash tank and liquid level tank and black liquor storage tank, 18 temperature measurement links including steam and black liquor temperature, and 8 flow measurement links including steam, black liquor and clean water.
The combustion section uses flue gas and waste heat to further concentrate the concentrated black liquor brought by the evaporation section to a concentration of 65% to 70% for combustion. Its main equipment is the alkali recovery jet boiler, and its operation determines the production efficiency of the entire section. On the one hand, its function is to recover the effective calorific value of a large amount of organic matter (delignification) in the black liquor to generate steam for power generation or paper drying in the whole plant; on the other hand, it recovers inorganic alkali salts in the black liquor. This section also includes some other supporting equipment, such as air heaters, disc evaporators, electrostatic precipitators, etc. It can generally be divided into black liquor subsystem, air supply subsystem, water supply and steam subsystem and green liquor subsystem. In the combustion process, the three systems are interrelated. Here, the first thing to determine is the fuel/air ratio. The appropriate ratio can obtain the best boiler efficiency. In this system, the black liquor and air entering the furnace are metered, so during the debugging process, after a period of time, the appropriate proportional relationship can be obtained. The induced air volume is adjusted according to the negative pressure of the furnace. When the other two parameters mentioned above change, the induced air volume must also respond and be adjusted accordingly. In this system, frequency converters are used for both air supply and air extraction, which can be finely adjusted. This section is equipped with 17 pressure measurement links, 11 liquid level measurement links, 21 temperature measurement links, and 8 flow measurement links.
The main equipment of the causticizing section is the lime digestion slag extractor and the causticizer. The auxiliary equipment includes the white liquor clarifier, emulsion clarifier, white mud detergent, vacuum filter, pre-hanging filter, etc. This section mainly controls the concentration, flow rate and ratio of lime addition of green liquor as well as the time and temperature of the causticizing reaction. This section is equipped with 1 pressure measurement link, 10 liquid level measurement links, 12 temperature measurement links and 3 flow measurement links.
2 System Hardware Design
The framework of the entire control system consists of three parts: distributed process control device, operation management unit and communication system. Its structure is shown in Figure 1.

(1) Distributed process control device
The core part adopts Siemens S7-300/400 series modules, including CPU414-2DP, CPU315-2DP, power supply PS407, PS307, communication module CP443-1, CP343-1, ET200M, SM331, SM332, SM321, SM322 modules, etc. The SM31 module mainly completes the data acquisition of temperature, pressure, flow, liquid level and other analog quantities in the system. The SM332 module mainly completes the analog drive signal output of the actuator. The SM321 module mainly completes the acquisition of digital input signals in the system (such as motor status feedback, shut-off valve position feedback, etc.); the SM322 module mainly completes the output of digital signals in the system (such as motor start and stop, electric valve switch drive signal, etc.). See Table 1 for specific module configuration.
Table 1 Siemens module configuration table

(2) Operation management unit
The engineer station consists of a DELL notebook, and the programming platform adopts Siemens Step7 V5.3, which mainly completes the programming work of data acquisition, loop control, interlocking control, flow accumulation, etc.
The operator station consists of 5 DELL industrial control computers, 2 for each of the evaporation section and the combustion section, and 1 for the causticizing section. The 5 computers are redundant and can exchange data with the three CPUs. The production status of each section of the entire alkali recovery can be monitored in real time on each computer, avoiding the blind area where data cannot be exchanged and displayed between sections. The configuration software uses Siemens WinCC V6.0 SP1.
The system mainly includes the following functional screens:
Control main screen. The control main screen displays the detection values of each control link and the operating status of the equipment in the order of the process. At the same time, a pop-up control panel is designed for each control loop. The user clicks the corresponding control link in the main screen to pop up the control panel of the control loop. The operator uses this panel to perform on-site control, including changes in set values, manual operations, etc.
Historical curve display: The system displays historical curves for major control quantities, including liquid level, flow, temperature, pressure, etc.
Alarm screen. For any faults that occur in the system, the system will display corresponding alarm information. Fault information includes hardware faults and software faults of the system. Hardware faults include communication faults between the computer and the PLC, failure of the motor to start, signal module faults in the DCS system, etc. Software faults are user-defined faults, including detection value exceeding the limit, too long adjustment time, etc.
Parameter centralized display screen: This screen displays important process data in a table format according to user needs, allowing users to quickly understand the on-site operation status.
Parameter setting screen. This screen is only set in the engineer, and you need to enter the password to enter. It is mainly used to modify important parameters such as PID control parameters.
Report printing screen: This screen provides the cumulative production flow by shift and can be printed at any time.
(3) Communication system
CPU414-2DP and CPU317 each have two network communication ports, one MPI/DP integrated communication port and one DP dedicated communication port. Each section CPU is connected to its own EM200M slave station through the ProfiBus fieldbus, the interface is the DP dedicated communication port, and the communication rate is set to 1.5Mbps. The process control level and the operation management level are also connected through the ProfiBus fieldbus, the interface is the MPI/DP integrated communication port, the configuration is ProfiBus-DP communication, and the communication rate is 1.5Mbps. Each CPU and ET200M slave station has a ProfiBus-DP station address. Note that each must be assigned an independent station address and cannot be repeated. Each operation management station is equipped with a CP5611 communication card, configured as ProfiBus-DP communication, with a communication rate of 1.5Mbps and an independent station address. The ProfiBus network of each section and the ProfiBus network between the operation management level belong to the same network, but belong to different network segments, so the bus communication problem within the section will not affect the normal operation of other sections. The communication rate is much higher than that of MPI (multi-point interface) network, which is conducive to real-time display of data. The network communication line adopts Siemens special DP line, which ensures the communication rate and communication distance of the system.
In addition to the above-mentioned main hardware framework, the system hardware also includes a voltage-stabilized power supply and UPS for each section subsystem. The evaporation section and combustion section both use a 6KVA voltage-stabilized power supply and a 6KVA/30min (effective load/effective power supply time) UPS, and the causticizing section uses a 3KVA voltage-stabilized power supply and a 3KVA/30min UPS. For digital input signals such as motor status feedback, optoelectronic isolators are used to isolate field signals from signals in the control cabinet, preventing abnormal interference voltage on site from affecting the operation of the Siemens module. For ordinary digital output signals, Omron intermediate isolators are used for isolation; and for the control signals of electric valve switches, zero-voltage (Z) SSRs (solid-state relays) are used for isolation, eliminating signal oscillations caused by frequent actions. [3]
3 System Software Design
According to the characteristics of the alkali recovery process, sampling, filtering, PID control, scale conversion, alarm, accumulation and other subroutines are compiled for each work section. Since the structured programming method has the advantages of clear program structure, generalization and standardization of some programs, easy modification and simplified program debugging, we use this method to compile the control program here.
The following is an explanation of the basic function blocks of the control system program. The system control program is constructed by calling these basic function blocks in organization blocks such as OB1, OB32, OB33, OB34, OB35 (different control cycles).
1) Sampling subroutine: reads the analog input and stores it in sequence into the data block. The starting address of the analog input module, the number of channels, the block number of the data block, and the storage location of the data in the data block are variable and can be determined when calling.
2) Filtering subroutine: The sampling part samples each channel 8 times in succession and stores them in the data block in sequence. The 8 sampling values are averaged. When calling, the data block number, the first address of the data storage, and the interval between two adjacent sampling values in the data block need to be specified.
3) PID control program: There is a general PID control subroutine in the STEP7 program library. A background data block must be specified for each subroutine when it is called. When it is called, the parameter value is passed to the logic block. At the end of the call, it is used to save the result data output by the logic block.
4) Scale conversion: After the analog input is converted by A/D, the nominal range of the digital result is 0-27648. When setting the given value, the operator uses a specific value or a percentage for intuitiveness. The sampling value of PID has two forms: Word type or Float type. The range of Word type is 0-27648, but it is not intuitive. Therefore, in order to compare the given value with the measured value, the scale of the measured value and the set value should be consistent, so a scale conversion is required. The values of the two scales correspond one to one.
5) Alarm subroutine: judge whether the analog quantity exceeds the upper limit or the lower limit. If so, set the over-limit flag. To prevent the over-limit flag output from jittering, set the judgment dead zone.
6) Flow accumulation subroutine: In order to evaluate the efficiency of each shift, important flows (such as black liquor flow in the process section, etc.) are usually accumulated. The flow sampling signal is accumulated over time, and is counted into the morning shift, the middle shift, and the evening shift according to the shift, and the total for the day, yesterday, and this month is accumulated.
7) Motor control: The start and stop control of the motor is the most basic control application of the system. When the ready signal is in place, the motor can be started and stopped directly; when the ready signal is not received, the motor will stop automatically. When the motor current is too large, the motor alarm will sound.
Each section is assigned different parameter values when calling the subroutine according to the actual situation of the section. For the control of the drum liquid level in the combustion section, simple PID control cannot be used, and three-impulse control is generally used. The liquid level is sent to the regulator as the main impulse, and the steam and feed water flow signals are used as auxiliary impulses. When the boiler system is in material balance, the liquid level is stable. Since the feed water flow and steam flow signals are equal in size, the positive and negative signs introduced into the adder and subtractor are opposite, and they cancel each other out, so the control signal of the regulation system does not change. When one of the auxiliary impulses changes suddenly (for example, the steam consumption increases), the material balance is destroyed. The difference between the two auxiliary impulses with opposite signs acts on the regulation system to change the control signal in time, increase the feed water, and restore the balance of the boiler system materials. It can be seen that the three-impulse regulation system can overcome the fluctuation interference from the steam flow or feed water flow before it affects the drum liquid level, thereby reducing the large fluctuation of the liquid level and thus reducing the "false phenomenon" of the liquid level. The boiler feed water valve should use an air-closed valve. At this time, the integral regulator is set to the positive (+) action, the liquid level signal is positive (+), the steam flow signal is negative (-), and the feed water flow signal is positive (+).
Each section is also set with certain interlocking subroutines according to the process requirements. The steam pressure regulation of the evaporation section is interlocked with the black liquor circulation pump of effect I. When there is no operation feedback signal of the black liquor circulation pump of effect I, the steam pressure regulation is automatically switched to manual mode and the steam valve is closed. The upper drum liquid level of the combustion section is the key to the entire system. It is interlocked with the feed water pump, the first, second and third fans and the induced draft machine. When the drum liquid level exceeds the upper limit, the feed water pump is automatically stopped and an alarm is sounded; when the drum liquid level exceeds the lower limit, the induced draft fan, the third fan, the secondary fan and the primary fan are automatically shut down.
4 Conclusion
This system was designed by the Microcomputer Application Research Institute of Shaanxi University of Science and Technology for the alkali recovery workshop of a paper mill in Henan Province. Its features are:
(1) Update and expand the functions of DCS. The addition of fieldbus to traditional DCS not only maintains the stability of DCS, but also introduces the flexibility of fieldbus; at the same time, it can reduce the amount of hardware, and the workload of installation and maintenance is reduced accordingly.
(2) Improved system sensitivity and accuracy. Signals related to this fieldbus no longer need to be repeatedly converted between digital and analog/analog during the sending and receiving process like traditional DCS, but can be directly communicated between CPUs, thereby improving the quality of signal acquisition and system control quality.
(3) Reduced DCS load and improved system control quality. Since part of the regulation task is assigned to the CPU of the field intelligent instrument or actuator, the CPU load in the relevant automatic processing unit in the DCS is reduced and the regulation quality of the relevant equipment is improved.
(4) Since the fieldbus has self-diagnosis and simple fault handling capabilities, and sends relevant diagnostic and maintenance information to the control room through digital communication, users can query the operating status and diagnostic and maintenance information of the bus equipment.
The system is low-cost, easy to use, highly reliable, has strong communication capabilities, and has strong analog computing capabilities and digital logic processing functions. It realizes network monitoring of evaporation, combustion, and causticization production process control. At present, the system is running stably, the algorithm in the system is effective and feasible, and has achieved satisfactory control effects and created good economic value.
Previous article:Data Communication between DCS and MATLAB for Vehicle Powertrain Simulation
Next article:Design and simulation of quad-redundant communication board based on CAN core
Recommended ReadingLatest update time:2024-11-16 19:57
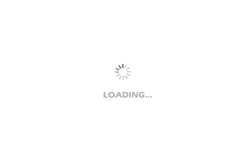
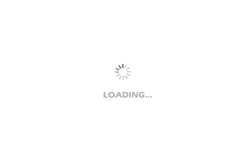
- Molex leverages SAP solutions to drive smart supply chain collaboration
- Pickering Launches New Future-Proof PXIe Single-Slot Controller for High-Performance Test and Measurement Applications
- CGD and Qorvo to jointly revolutionize motor control solutions
- Advanced gameplay, Harting takes your PCB board connection to a new level!
- Nidec Intelligent Motion is the first to launch an electric clutch ECU for two-wheeled vehicles
- Bosch and Tsinghua University renew cooperation agreement on artificial intelligence research to jointly promote the development of artificial intelligence in the industrial field
- GigaDevice unveils new MCU products, deeply unlocking industrial application scenarios with diversified products and solutions
- Advantech: Investing in Edge AI Innovation to Drive an Intelligent Future
- CGD and QORVO will revolutionize motor control solutions
- Innolux's intelligent steer-by-wire solution makes cars smarter and safer
- 8051 MCU - Parity Check
- How to efficiently balance the sensitivity of tactile sensing interfaces
- What should I do if the servo motor shakes? What causes the servo motor to shake quickly?
- 【Brushless Motor】Analysis of three-phase BLDC motor and sharing of two popular development boards
- Midea Industrial Technology's subsidiaries Clou Electronics and Hekang New Energy jointly appeared at the Munich Battery Energy Storage Exhibition and Solar Energy Exhibition
- Guoxin Sichen | Application of ferroelectric memory PB85RS2MC in power battery management, with a capacity of 2M
- Analysis of common faults of frequency converter
- In a head-on competition with Qualcomm, what kind of cockpit products has Intel come up with?
- Dalian Rongke's all-vanadium liquid flow battery energy storage equipment industrialization project has entered the sprint stage before production
- Allegro MicroSystems Introduces Advanced Magnetic and Inductive Position Sensing Solutions at Electronica 2024
- Car key in the left hand, liveness detection radar in the right hand, UWB is imperative for cars!
- After a decade of rapid development, domestic CIS has entered the market
- Aegis Dagger Battery + Thor EM-i Super Hybrid, Geely New Energy has thrown out two "king bombs"
- A brief discussion on functional safety - fault, error, and failure
- In the smart car 2.0 cycle, these core industry chains are facing major opportunities!
- The United States and Japan are developing new batteries. CATL faces challenges? How should China's new energy battery industry respond?
- Murata launches high-precision 6-axis inertial sensor for automobiles
- Ford patents pre-charge alarm to help save costs and respond to emergencies
- New real-time microcontroller system from Texas Instruments enables smarter processing in automotive and industrial applications
- Showing goods + NVIDIA AI small board
- Circuit diagram of two-wheeled electric vehicle
- [Domestic RISC-V Linux Board Fang·Starlight VisionFive Trial Report] Python output HELLOWORLD
- Solutions for control loop design
- Data size transferred after power failure
- About DMX dimming system
- What is UWB?
- Solution to blind area communication of intercom
- Xunwei i.MX8MM Development Board Linux Android 9.0 Crotex-M4 Data Update
- Commonly used algorithms for drones - Kalman filter (Part 3)