LEDs can generate light in 5 nanoseconds, while the reaction time of an incandescent light bulb is 200 milliseconds, so the automotive industry has applied LEDs to brake lights. This article will introduce the characteristics of LEDs and the trade-offs of driving LEDs, and will delve intovarious switching power supply topologies suitable for LED driving and dimming, and explain the related advantages in detail.
Stable current drives LED to maintain constant brightness
LED driving still faces many challenges. To maintain a fixed brightness, the LED needs to be driven with a stable current that is not affected by the input voltage. This is a greater challenge than simply connecting an incandescent bulb to a battery as a power source.
LEDs have forward VI characteristics, similar to diodes. The turn-on threshold of white LEDs is about 3.5 volts, below which very little current flows through the LED. Beyond this threshold, the current increases exponentially, causing the forward voltage to increase, and the LED becomes a voltage source model with a series resistor. However, it should be noted that this model is only valid for a single operation of DC current. If the DC current in the LED changes, the resistor in the model should also change to reflect the new operating current. In the case of a large amount of forward current, the power consumed in the LED will increase the device temperature, change the forward voltage drop and dynamic impedance, and be sure to consider the heat of the environment when determining the LED impedance.
If the LED is driven by a buck regulator, in addition to the DC current, the LED often conducts the AC ripple current of the inductor, depending on the selected output filter arrangement. This increases the RMS intensity of the current in the LED, which also increases its power consumption and increases the junction temperature, which has a significant impact on the LED life. If a 70% limit is set on the light output as the service life of the LED, the LED life can be increased from 15,000 hours at 74°C to 40,000 hours at 63°C. The power loss in the LED is determined by multiplying the LED resistance by the square of the RMS current and adding the value of the average current multiplied by the forward voltage drop. Since the junction temperature is determined by the average power, even large ripple currents have little effect on the power consumption. For example, in a buck regulator, a peak-to-peak ripple current equal to the DC output current (Ipk-pk=Iout) will increase the total power loss by less than 10%. If it is much greater than this, the AC ripple current supplied must be reduced to maintain the junction temperature and operating life. There is a practical basic principle here, that is, if the junction temperature is reduced by 10°C, the life of the semiconductor will be doubled. In fact, most designs tend to use much lower ripple currents due to inductance limitations. In addition, the peak current in the LED should not exceed the maximum safe operating rating specified by the manufacturer.
LEDs are used in a variety of fields and require a variety of power supply topologies
The information in Table 1 can be used as a reference for selecting the best switching topology for LED drivers . In addition to these topologies, simple current limiting resistors or linear regulators can also be used, but these methods usually consume too much power. Input voltage range, number of LEDs driven, LED current, isolation, electromagnetic interference (EMI) limitations, and efficiency are all relevant design parameters. Most LED driver circuits can be divided into the following topology categories: buck, boost, buck-boost, SEPIC, and flyback.
Figure 1 shows three examples of basic power topologies. The first figure shows a buck regulator that can be used when the output voltage is always less than the input voltage. In Figure 1, the buck regulator varies the on-time of a metal oxide semiconductor field effect transistor (MOSFET) to control the current into the LED. Current sensing is performed by measuring the voltage across a resistor that is in series with the LED. Driving the MOSFET is a significant design challenge for this approach. From a cost and performance perspective, it is recommended to use an N-channel FET that requires a floating gate drive. N-channel FETs require the use of either a drive transformer or a floating drive circuit, both of which can maintain a voltage higher than the input voltage.
Figure 1 also shows an alternative buck regulator (Buck #2). In this circuit, the MOSFET is driven relative to ground, greatly reducing the need for driver circuitry. This circuit senses the LED current by monitoring the FET current or by placing a current sensing resistor in series with the LED. If the latter is used, a level shifting circuit is required to send this information to the ground supply, complicating a simple design. The boost converter, also shown in Figure 1, is used when the output voltage is always greater than the input. This topology is easy to design because the MOSFET is driven relative to ground and the current sensing resistor is also ground referenced. The disadvantage of this circuit is that it does not limit the current through the inductor in the event of a short circuit. A fuse or circuit breaker can be used as a fault protection device. There are also more complex topologies that provide this type of protection.
Figure 2 shows two buck-boost circuits that can be used in situations where the input voltage may be greater or less than the output voltage. These circuits share the same trade-off characteristics as the two previous buck topologies, related to the location of the current sensing resistor and gate drive. The buck-boost topology of Figure 2 shows a ground-referenced gate drive. This topology requires a level-shifted current sensing signal, but the inverting boost-buck topology has ground-referenced current sensing and a level-shifted gate drive. If the control IC is associated with the negative output and the current sensing resistor is swapped with the LED , the inverting boost-buck topology can be configured in an efficient manner. With appropriate control of the IC, the output current can be measured directly, and the MOSFET can also be driven directly.
The buck-boost topology has relatively high currents. For example, if the input and output voltages are the same, the inductor and power switch currents are more than twice the output current, which has a negative impact on performance and power consumption. The "boost or buck" topology in Figure 3 can alleviate these problems. In this circuit, there is a boost power stage followed by a buck power stage. If the input voltage is higher than the output voltage, the boost power stage provides voltage regulation, while the buck power stage only delivers power. If the input voltage is lower than the output voltage, the buck power stage provides voltage regulation and the boost power stage delivers power. Usually, there is some overlap in the operation of the buck and boost, so there is no dead-band when switching modes.
If the input and output voltages are nearly the same, this circuit has the advantage that the switch and inductor currents are nearly equal to the output current, and the inductor ripple current tends to be less. Even with four power switches in this circuit, there is usually still a significant performance improvement, which is key for battery applications. The SEPIC topology shown in Figure 3 requires fewer FETs, but more passive components. The advantage of the SEPIC topology is the simplicity of the ground-referenced FETs and control circuitry. In addition, the dual-channel inductors can be combined into a single coupled inductor, saving area and cost. However, like the buck-boost topology, the switch currents of the SEPIC topology are higher than the buck or boost and the pulsed output currents, requiring capacitors that can handle large RMS currents.
Safety considerations may dictate isolation between the offline voltage and the output voltage. The most cost-effective solution for this application is to use a flyback converter (Figure 4), which requires the fewest components of all isolation topologies. The transformer turns ratio can be used to step down, step up, or step down and step up the output voltage, which provides great design flexibility, but the disadvantage is that the power transformer is essentially a custom component. In addition, high component stress will occur in the FETs and input and output capacitors. When applying fixed lighting, a "slow" feedback control loop can be used to adjust the LED current to be in phase with the input voltage for power factor correction (PFC). This can adjust the required average LED current and adjust the input current to be in phase with the input voltage to provide a high power factor.
LED dimming technology uses PWM to reduce brightness better
LEDs often need to be dimmed. For example, you may need to adjust the brightness of displays or architectural lighting . There are two ways to achieve this goal. One is to reduce the LED current, and the other is to turn the LED on and off quickly to average its brightness to the naked eye. The worst way is to reduce the current because the relationship between light output and current is not completely linear. In addition, the color spectrum of LEDs tends to shift when the current is below the maximum rating. Human perception of brightness is an exponential relationship, so if you want to adjust the brightness, you may need to change the current significantly, which has a great impact on circuit design. Because a 3% regulation error at maximum current may result in more than 30% error at 10% load due to circuit tolerance. Reducing the brightness by affecting the current through pulse width modulation (PWM) is a more correct approach, but there is still a problem of response speed. When lighting or displaying, pulse width modulation of more than 100Hz is required so that the human eye will not notice the flicker. The 10% pulse width is in the millisecond range, so the bandwidth of the power supply needs to be greater than 10kHz.
Various power supply topologies have emerged for different LED applications
LEDs have been widely used in various fields, so many types of power supply topologies are needed to support LED applications. Generally speaking, the input voltage, output voltage and isolation requirements must be considered to make an appropriate choice.
If the input voltage must be greater or less than the output voltage, the choice is clear: buck or boost. But if the relationship is unclear, it is difficult to make a choice, and there are many trade-offs, including performance, cost, and reliability.
Previous article:Analysis of LED power supply elimination: general technical route to reduce flicker
Next article:Experts share: Many useful tips for LED driver design
Recommended ReadingLatest update time:2024-11-23 07:58
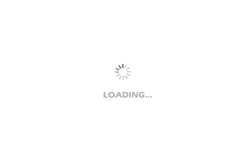
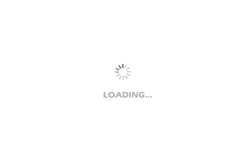
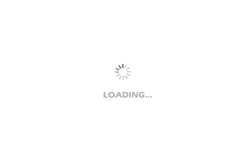
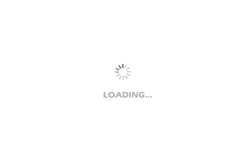
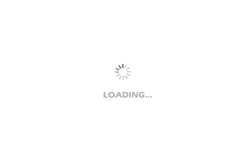
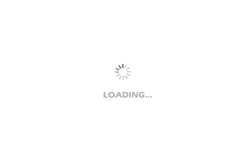
- Popular Resources
- Popular amplifiers
-
MCU C language programming and Proteus simulation technology (Xu Aijun)
-
100 Examples of Microcontroller C Language Applications (with CD-ROM, 3rd Edition) (Wang Huiliang, Wang Dongfeng, Dong Guanqiang)
-
Research on three-phase all-solid-state high-efficiency LED tunnel lighting system based on chip drive_Li Jian
-
Follow me Season 2 Episode 1 All Code + Library
- RAQ #223: How to measure and determine soft-start timing without a soft-start equation?
- Vicor high-performance power modules enable the development of low-altitude avionics and EVTOL
- Bourns Launches Two Thick Film Resistor Series with High Power Dissipation Capabilities in Compact TO-220 and DPAK Package Designs
- Bourns Launches New High-Pulse Brake Resistor Series with Superior Energy Dissipation Capabilities
- Nexperia launches new 120 V/4 A half-bridge gate driver to further improve robustness and efficiency in industrial and automotive applications
- Vishay's New 150 V MOSFETs Offer Industry-Leading Power Loss Performance
- The first generation of SGT MOSFET series from Qiangmao: innovative trench technology, automotive-grade 60 VN channel, breakthrough in high-efficiency performance of automotive electronics
- DC/DC Power Supplies for Automotive Applications
- MathWorks and NXP Collaborate to Launch Model-Based Design Toolbox for Battery Management Systems
- Intel promotes AI with multi-dimensional efforts in technology, application, and ecology
- ChinaJoy Qualcomm Snapdragon Theme Pavilion takes you to experience the new changes in digital entertainment in the 5G era
- Infineon's latest generation IGBT technology platform enables precise control of speed and position
- Two test methods for LED lighting life
- Don't Let Lightning Induced Surges Scare You
- Application of brushless motor controller ML4425/4426
- Easy identification of LED power supply quality
- World's first integrated photovoltaic solar system completed in Israel
- Sliding window mean filter for avr microcontroller AD conversion
- What does call mean in the detailed explanation of ABB robot programming instructions?
- STMicroelectronics discloses its 2027-2028 financial model and path to achieve its 2030 goals
- 2024 China Automotive Charging and Battery Swapping Ecosystem Conference held in Taiyuan
- State-owned enterprises team up to invest in solid-state battery giant
- The evolution of electronic and electrical architecture is accelerating
- The first! National Automotive Chip Quality Inspection Center established
- BYD releases self-developed automotive chip using 4nm process, with a running score of up to 1.15 million
- GEODNET launches GEO-PULSE, a car GPS navigation device
- Should Chinese car companies develop their own high-computing chips?
- Infineon and Siemens combine embedded automotive software platform with microcontrollers to provide the necessary functions for next-generation SDVs
- Continental launches invisible biometric sensor display to monitor passengers' vital signs
- How to use pointers
- MaixSense R329 Development Board Unboxing and Introduction
- [MIL MYC-JX8MPQ Review] 2. UVC Camera Image Acquisition
- A question about limit switches
- [Synopsys IP Resources] Why In-Memory Computing Will Disrupt AI SoC Development
- MM32F103 development board evaluation and suggestions for the development of domestic MCUs
- Verilog Basic Syntax - Module.zip
- Basics of Model-Based GaN PA Design: GaN Transistor S-Parameters, Linear Stability Analysis, and Resistor Stability
- How to set the minimum area of Solid Region in Altium
- LIS3DH sensor high-pass filter question and data refresh rate consultation