Why should you care about power management?
Power management is becoming very important due to a variety of factors. For mobile handheld embedded systems, there is always pressure to provide more functions while increasing battery life. When the battery itself cannot improve but needs to meet this requirement, the pressure falls on chip vendors to provide chips with lower power consumption and better performance. At the same time, in order to meet the requirements of shortening design cycles and accelerating time to market, flexible and programmable devices with lower power consumption are needed. In addition, the green movement requires reducing battery waste, which in embedded systems translates into fewer battery replacements. Similarly, government regulations around the world (such as Energy Star) also require reducing standby current in electrical equipment. The next generation of embedded systems will require extremely low power consumption in both active and sleep modes, and the flexibility and programmability required to meet time-to-market requirements will also need to be improved.
In addition to lower current consumption, there is also a need for lower system voltages. A few years ago, the minimum standard operating voltage was 3.3 volts. Today, the minimum standard operating voltage is 1.8 volts. Graphing this trend, it will become a reality in the future that the minimum standard operating voltage of devices will extend into the sub-volt range. This will make it possible to build SoC-based designs with a single AA or AAA battery (the battery voltage ends at about 0.9 volts). Although some SoC-based designs can run at 1.8 volts today, more often the analog performance is degraded at such low voltages. For handheld battery-powered designs that require good analog performance, being able to run at less than 1 volt and still meet analog performance requirements can allow the use of a single AA or AAA battery. This means fewer batteries are needed and reduced costs for the customer.
How to achieve sub-volt operation?
Sub-volt operation is possible when an embedded SoC device has a built-in boost converter that can boost an input voltage (e.g., 0.9 volt input voltage) to a higher system voltage level (e.g., 3.3 volts). In this mode, it is important that the noise from the boost converter does not affect the performance of analog peripherals. Figure 1 shows the system-level connections for an integrated boost converter that is part of a PSoC 3 programmable system-on-chip from Cypress Semiconductor.
Figure 1 System-level connection from an external low voltage to an internal higher voltage
Having an integrated boost converter capable of accepting sub-volt input voltages has the following advantages:
1. Ability to operate the system from a single AA or AAA battery
2. Ability to provide a minimum guaranteed system voltage even with a varying supply voltage
3. Ability to use the boosted output voltage to run other circuits in the system that require a higher voltage. For example: LCD, sensor circuits, etc.
Wide supply voltage range:
A wide voltage range spanning from 1.8V (0.9V to activate boost) to 5.5V provides the user with maximum flexibility for the following reasons:
1. Ability to span from standard battery voltage to end of life voltage for most common batteries as shown in Table 1
2. Compatible with legacy system voltages of 3.3V and 5V
3. 5.5V upper limit provides more than 5V margin for rail-to-rail measurements of signals from legacy systems
By providing a built-in low-dropout linear regulator inside the device, a wide range of external power supply voltages can be provided. This wide range of external power supply voltages can maintain a stable low core voltage for the chip. In addition, both the digital domain and the analog domain have separate independent internal regulators to ensure that the analog performance will not be damaged by noise from the digital power rail. Figure 2 shows the system-level connection and the internal regulator that can accommodate a wide power supply voltage range.
Figure 2 System-level connections for the internal regulator
In Figure 2, Vddd and Vdda can vary from 1.71 volts to 5.5 volts while the built-in analog and digital regulators ensure that the core still runs at a stable low voltage. If properly designed, this system can also ensure the same analog performance over the entire supply voltage range.
Independent power supply for I/O group
To allow connection to other devices in the system that may have different system voltages, an SoC needs to have separate I/O supplies that can be independently set to any voltage within a wide voltage range. As shown in Figure 3, an SoC with four I/O groups, each of which can be driven by any voltage from 1.8 volts to 5 volts, can provide seamless connection to other devices on the PCB.
Figure 3 Independent supply voltage for each I/O bank provides seamless connectivity to devices that may operate at different voltages.
Flexible power modes
While low power consumption in programmable systems is still a myth, well thought out programmable SoCs are now capable of world class currents that match standalone MCUs. Keeping in mind the end customer’s application, the desirable power modes and their currents are shown in Table 2.
It is the mode in which the system operates normally when the user actively uses the operating modes shown in Table 1. A programmable SoC will allow the selective disabling of unneeded peripherals in this mode.
In alternate operation mode, a smaller number of selected peripherals are actively operating. This provides a reduced power mode that can be entered from normal operation. Once exited from this mode, the system returns to normal operation. An example of this is an embedded system with a display, where the power to the display can be turned off separately while the embedded system continues to run. When the display needs to be turned off, the system enters alternate operation mode, where the power to the peripherals required by the display is turned off.
Sleep mode is often used in battery powered embedded systems. This is an extreme low power mode where all peripherals are in a low power state, while a real time clock is maintained. This mode is also used in systems that need to cycle between active and sleep modes frequently. An example of this is a temperature sensor that needs to update its reading every minute. The system would wake up every minute, take a reading and go back to sleep mode. The result is lower average power consumption.
Hibernate is the lowest power mode for a device, while still maintaining memory contents and configuration. It can wake the device from an I/O source, which also provides the ability for the user or another device in the system to wake the device. Hibernate mode can also be used to eliminate the need for a power switch in a handheld device (since pressing any button can wake the device).
in conclusion
Programmable System-on-Chip (PSoC) provides high integration and provides users with the ability to build their own custom peripherals using an efficiently configurable and programmable system. A well-designed programmable SoC can provide world-class power management capabilities that not only meet the power requirements of the MCU but also provide a configurable power management system that also provides accurate analog performance.
Cypress Semiconductor's PSoC 3 and PSoC 5 series are field-programmable embedded SoCs with programmable digital blocks and configurable analog blocks. These devices are designed to provide users with the greatest possible flexibility and programmability while consuming very little sleep current and operating current. It also provides precise analog performance (16-bit to 20-bit accuracy). PSoC Creator is an integrated development environment software that can be used to quickly develop designs for the PSoC 3 and PSoC 5 series from end to end, including device selection, configuration/programming of digital and analog peripherals, configuration of the power system, firmware development, debugging and programming.
Previous article:InfineonICE2QS03G36W (12V3A) power supply solution
Next article:Application of S3C4480 in the design of high-precision DC switching power supply
Recommended ReadingLatest update time:2024-11-17 04:32
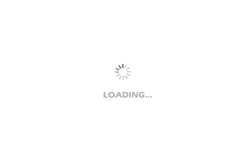
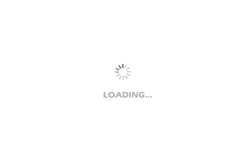
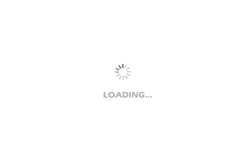
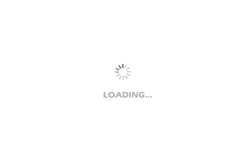
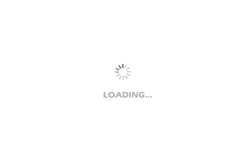
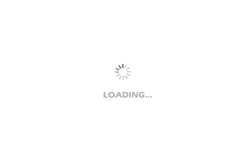
- Popular Resources
- Popular amplifiers
-
Analysis and Implementation of MAC Protocol for Wireless Sensor Networks (by Yang Zhijun, Xie Xianjie, and Ding Hongwei)
-
MATLAB and FPGA implementation of wireless communication
-
Intelligent computing systems (Chen Yunji, Li Ling, Li Wei, Guo Qi, Du Zidong)
-
Summary of non-synthesizable statements in FPGA
- MathWorks and NXP Collaborate to Launch Model-Based Design Toolbox for Battery Management Systems
- STMicroelectronics' advanced galvanically isolated gate driver STGAP3S provides flexible protection for IGBTs and SiC MOSFETs
- New diaphragm-free solid-state lithium battery technology is launched: the distance between the positive and negative electrodes is less than 0.000001 meters
- [“Source” Observe the Autumn Series] Application and testing of the next generation of semiconductor gallium oxide device photodetectors
- 采用自主设计封装,绝缘电阻显著提高!ROHM开发出更高电压xEV系统的SiC肖特基势垒二极管
- Will GaN replace SiC? PI's disruptive 1700V InnoMux2 is here to demonstrate
- From Isolation to the Third and a Half Generation: Understanding Naxinwei's Gate Driver IC in One Article
- The appeal of 48 V technology: importance, benefits and key factors in system-level applications
- Important breakthrough in recycling of used lithium-ion batteries
- Innolux's intelligent steer-by-wire solution makes cars smarter and safer
- 8051 MCU - Parity Check
- How to efficiently balance the sensitivity of tactile sensing interfaces
- What should I do if the servo motor shakes? What causes the servo motor to shake quickly?
- 【Brushless Motor】Analysis of three-phase BLDC motor and sharing of two popular development boards
- Midea Industrial Technology's subsidiaries Clou Electronics and Hekang New Energy jointly appeared at the Munich Battery Energy Storage Exhibition and Solar Energy Exhibition
- Guoxin Sichen | Application of ferroelectric memory PB85RS2MC in power battery management, with a capacity of 2M
- Analysis of common faults of frequency converter
- In a head-on competition with Qualcomm, what kind of cockpit products has Intel come up with?
- Dalian Rongke's all-vanadium liquid flow battery energy storage equipment industrialization project has entered the sprint stage before production
- Allegro MicroSystems Introduces Advanced Magnetic and Inductive Position Sensing Solutions at Electronica 2024
- Car key in the left hand, liveness detection radar in the right hand, UWB is imperative for cars!
- After a decade of rapid development, domestic CIS has entered the market
- Aegis Dagger Battery + Thor EM-i Super Hybrid, Geely New Energy has thrown out two "king bombs"
- A brief discussion on functional safety - fault, error, and failure
- In the smart car 2.0 cycle, these core industry chains are facing major opportunities!
- Rambus Launches Industry's First HBM 4 Controller IP: What Are the Technical Details Behind It?
- The United States and Japan are developing new batteries. CATL faces challenges? How should China's new energy battery industry respond?
- Murata launches high-precision 6-axis inertial sensor for automobiles
- Ford patents pre-charge alarm to help save costs and respond to emergencies
- Which is more effective in eliminating the back EMF of inductive loads, TVS or varistor?
- The chip cannot be removed
- A must-read summary of drone principles (IV) Professional terminology for drones
- MicroPython Hands-on (36) - MixPY Hello world
- 【i.MX6ULL】Driver Development 12——Capacitive Touch Driver Practice (Part 1)
- MicroPython now supports STM32F413 controller
- Sofa stickers
- Introduction to the ports of MSP430 microcontroller
- Two highlights of EFM32PG22
- Application of ROOM in AD software