Common misconceptions and exaggerated myths about isolation technology
▲ For more exciting content, please click on the blue words above and follow us!
As the demand for reliable signal isolation continues to grow in industrial, automotive, communications, and personal electronics applications, recent design trends have shifted from traditional isolation technologies such as optocouplers to digital isolators. Despite the prevalence of digital isolation, there are still several common misconceptions about its effectiveness compared to optocouplers. Similarly, there are also some misconceptions or myths about the reliable performance and lifespan of optocouplers. In this article, I will explain the common misconceptions about these two devices.
What is an optocoupler? What is a digital isolator?
Before exploring these, let’s review the differences between these technologies:
Optocouplers use logic inputs to generate current on the input side, which is converted into light by an LED, then transmitted through isolation to the other side, where it is converted into an electrical signal by a photodetector.
Digital isolators use silicon-based CMOS technology with two integrated circuits and a high-voltage dielectric built into the silicon process. Digital isolators convert digital signals to the high-frequency domain and send RF signals through a capacitor-based high-voltage silicon dioxide dielectric barrier.
Optocoupler Myth 1: Optocouplers are Very Reliable
There is a common misconception that optocouplers always fail in an “open” circuit when the high voltage destroys the device. Although optocouplers can fail in a variety of ways, optocouplers can also fail in a “short” circuit, depending on the different failure modes in high voltage systems.
In the first failure mode, the isolation barrier can fail as a short circuit for both optocouplers and digital isolators when the voltage applied across the barrier exceeds the isolator’s rated limits. Texas Instruments (TI) tested the first failure mode in its labs; the white paper “Understanding Failure Modes in Isolators” specifically describes the observations of the failure short results.
The second failure mode, where high voltage and current within the isolator damage the circuitry, can cause a fault-to-open condition. These high voltage events can damage more circuitry to the point where it no longer functions properly, but the isolation barrier remains intact.
Figure 1a shows a high voltage event on an optocoupler, and Figure 1b shows a similar event on a digital isolator. Depending on the type of high voltage event and the strength of the barrier, varying degrees of degradation may occur. To prevent short circuit failures caused by the first failure mode, isolators must be selected that meet or exceed electrical safety standards.
Figure 1: Cross-section of a high voltage event on (a) the optocoupler side and (b) the digital isolator side. (Source: TI)
Optocoupler misunderstanding 2: The life of an optocoupler is predictable and has little variation
For all electronic designs, ensuring that the IC will last throughout the product’s lifetime is critical. This is especially true for isolation devices, as they protect signals across multiple voltage domains. While you might expect two identical optocouplers to have very similar high-voltage lifetimes, in reality there can be significant differences in high-voltage performance between different devices, often because the optocoupler’s isolation barrier is created at the packaging stage.
Digital isolator manufacturers typically build their isolation barriers in a more tightly controlled silicon chip manufacturing process. Figure 2 illustrates the difference in high voltage lifetime and variation, where the high voltage lifetime is longer and more tightly distributed for the TI digital isolators used in this test. To learn more about this topic, see the white paper “Improve System Performance by Replacing Optocouplers with Digital Isolators.”
Figure 2: Time-dependent dielectric breakdown characteristics of optocouplers and digital isolators. (Source: TI)
Optocoupler misunderstanding 3: Optocoupler datasheet specifications will strictly comply with the device's service life
You may not realize that the light output of the LED in an optocoupler will degrade over time, which has a direct impact on parameters such as the current transfer ratio (CTR). The plastic material inside the optocoupler will yellow over time, resulting in less light passing through the isolation barrier, further reducing the transfer rate. Eventually, the CTR will drop to a level where the device no longer operates properly, resulting in high failure rates and low mean time between failures.
To offset this, designers often design margins to account for expected degradation over time, which can result in higher initial power consumption. These issues are not always mentioned in optocoupler datasheets, making them difficult to account for in isolation designs. For example, TI digital isolators use highly controlled manufacturing processes, and the datasheets account for aging with minimum or maximum specifications, helping to set performance expectations over the life of the device.
Optocoupler misunderstanding 4: The maximum operating temperature of the optocoupler is higher
Typical optocouplers are rated for a maximum operating temperature of 85°C. Although optocouplers with higher temperature ratings are available on the market, the selection is limited and they are generally more expensive. In contrast, digital isolators can easily support operating temperatures up to 125°C. For automotive designs that require temperature support up to 150°C, digital isolators such as TI's Grade-0 certified ISO7741E-Q1 can help provide reliable system operation at high peak ambient temperatures. For high-temperature designs where every component needs to operate reliably above 110°C, lower temperature ratings can be problematic. Otherwise, system performance or device life may be affected.
Optocoupler Myth 5: No primary-side power supply means lower power consumption
When configuring a system to reduce power consumption, it is important to consider how the inputs of the isolator are driven. Optocouplers are driven by current inputs, while digital isolators are driven by voltage inputs—either CMOS or transistor logic.
Optocouplers can drive digital device inputs such as microcontrollers, analog-to-digital converters, and digital-to-analog converters through a series resistor that controls voltage and current. Input currents of up to 10 mA are required to activate the LED and meet reliability over the product lifecycle, which can result in high power dissipation at the input.
Digital isolators such as TI's ISO7041 typically require less than 10 µA of standby current at the input. Figure 3 shows the current consumption vs. data rate for the ISO7041. In this test, all four channels of the device consumed less than 20 µA.
Figure 3: Current consumption vs. data rate for the ISO7041. (Source: TI)
Digital Isolator Myth 1: Smaller DTI of Digital Isolators Indicates Weak Isolation Performance
The distance across the insulation (DTI) of an isolator is the distance or thickness of the dielectric used to insulate between the high-voltage side and the low-voltage side. For optocouplers, the DTI is the distance between the LED and the photodetector. For capacitor-based digital isolators, the DTI is the distance between the two plates of the capacitor.
Because historical safety standards set minimum DTI requirements based on optocoupler technology, there is a misconception that all isolators must have a DTI greater than 0.4 mm to meet today’s stringent reinforced isolation certification requirements. However, in reality, the strength of the isolator barrier is a combination of the DTI and the dielectric material.
Optocouplers have a much lower dielectric strength and therefore require a larger DTI. Capacitor-based digital isolators use silicon dioxide with a higher dielectric strength and can support reinforced isolation with a DTI as low as 21 µm.
Over time, the organizations that govern safety standards for the operation of equipment have taken this into account and updated regulations to allow for the use of thinner dielectrics based on the technology being evaluated. Table 1 lists the dielectric strength of different insulating materials.
Table 1: Dielectric strength of common insulating materials. (Source: TI)
Digital isolator misunderstanding 2: The cost of digital isolators is much higher than that of optocouplers
Despite the historical significance of this myth, digital isolator technology has made significant advances in the past decade, achieving higher performance at lower costs. The ability to achieve multiple channel counts in the same package also helps reduce overall system density and cost. For example, the ISO6741 provides four reinforced isolation channels in the same package, providing a robust isolation solution at a reasonable per-channel cost.
Digital Isolator Myth 3: Digital Isolator Integration and Board Space Savings Come at a Cost
One of the biggest advantages of digital isolators is their ability to integrate other system requirements into the same package. Isolation interfaces such as COM, RS-485, I2C, and LVDS signals are good examples. You may be concerned about the impact on your budget when purchasing a digital isolator with an integrated transceiver, but the truth is that integrated digital isolators have many benefits, especially when compared to similar discrete optocoupler solutions.
The biggest drawback of discrete optocoupler solutions is the cost of the many discrete components (resistors, capacitors, diodes, Schmitt buffers, transistors) and their PCB area. Figure 4 compares the size of the optocoupler and ISO1500 integrated RS-485 digital isolator. For more information on this comparison, see the technical article “The Hidden Cost of Optocouplers for Isolated RS-485 Designs.”
Figure 4: PCB comparison between discrete and fully integrated isolation solutions for RS-485 (Source: TI)
in conclusion
Digital isolation has come a long way over the past few decades and is now the isolation solution of choice for many designers. Keep in mind the myths and facts described in this article when your design requires a reliable signal isolation solution.
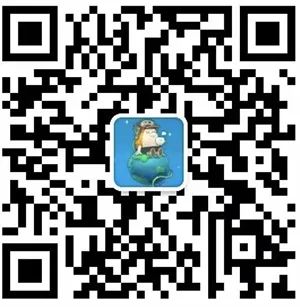
Add WeChat and reply " join group"
Invite you to join the technical exchange group!
Domestic chips|Automotive electronics|Internet of Things|New energy|Power supply|Industry|Embedded...
Reply to any content you want to search in
the
official
, such as problem keywords, technical terms, bug codes, etc.,
and you can easily get relevant professional technical content feedback
. Go and try it!
If you want to see our articles more often, you can go to our homepage, click the "three dots" in the upper right corner of the screen, and click "Set as Star".