0 Introduction
Aluminum alloy is an important civil and strategic metal material, and its mechanical properties are closely related to the grain size and morphology of the alloy. However, the crystallized aluminum alloy without refinement has coarse grains, well-developed columnar crystals, and poor deep drawing performance, which seriously affects its quality. Studies have shown that during the casting production process, introducing a special low-frequency composite electromagnetic field in the casting area can effectively refine the grains and improve the surface quality of the ingot.
Aiming at the control requirements of special composite magnetic field in aluminum electromagnetic casting, and based on the actual operation of aluminum electromagnetic field rapid casting and rolling controller in Fujian Ruimin Aluminum Plate and Strip Plant which was studied and designed in the previous stage, this paper studies and designs a composite magnetic field controller based on DSP (TMS320F2808) + single chip computer (C8051F410) + CPLD (EPM7128).
1 Overall system design
The composite magnetic field control system uses DSP (TMS320F2808) as the main control processing core and single-chip microcomputer as the dedicated human-machine interface control core. The DSP and single-chip microcomputer use the synchronous serial SPI interface for communication. The CPLD completes the formation of the thyristor trigger pulse. This paper specially designs a triggering method using a high-frequency double narrow pulse train. The acquisition of each analog quantity uses an external bipolar 16-bit AD based on the consideration of improving accuracy. The overall block diagram of the system is shown in Figure 1.
1.1 System Hardware Design
(1) System main circuit design
The electromagnetic induction device that generates a special composite magnetic field is one of the key technologies for aluminum electromagnetic field semi-continuous casting. According to the special process requirements of electromagnetic semi-continuous casting and the special structure of the composite magnetic field sensor, the AC-AC frequency conversion method is selected as the frequency conversion method of the composite magnetic field controller, and the main circuit structure different from the traditional AC-AC frequency conversion method is designed, as shown in Figure 2.
L and L' are two load coils wrapped around the same iron core inside the electromagnetic induction device (note that there is no electrical connection between the two). Both the VF group and VR group converters use three-phase bridge full-controlled rectification. When the VF group is working, the coil L obtains the corresponding positive half-wave current, and when the VR group is working, the coil L' obtains the corresponding negative half-wave current. Superimposing the two on the same iron core is equivalent to introducing a special current required for a complete electromagnetic casting into the load coil, thereby ultimately obtaining a special electromagnetic field to achieve the control purpose.
(2) Thyristor trigger pulse design
A new driving scheme is proposed for the currently commonly used method of driving thyristors with double narrow pulses. A high-frequency double narrow pulse train is used to replace the ordinary double narrow driving pulse. According to the energy transmission theory of pulse transformers, the new scheme has higher energy transmission efficiency and can greatly save the volume of pulse transformers.
The conventional method of generating high-frequency double narrow pulse trains is to use double narrow pulses to control the output of a high-frequency oscillator to obtain high-frequency double narrow pulse trains. This method has the defect that the pulse leading edge of the high-frequency double narrow pulse train and the double narrow pulse are inconsistent, which will lead to inaccurate trigger angles, which needs to be improved in the drive control of high-power thyristors. This paper designs a method that uses CPLD to generate double narrow pulses and, through certain processing, turns them into high-frequency double narrow pulse trains. After simulation and practice, significant results have been achieved. The principle block diagram of the formation of high-frequency double narrow pulse trains is shown in Figure 3.
(3) SCI to RS485 circuit
The three-way high-speed photoelectric isolation (TLP113) is to prevent the interference signal on the bus from entering the DSP controller and improve the anti-interference ability of the system communication. The low-power RS485 half-duplex transceiver (SP3485) completes the RS485 communication interface circuit. The specific implementation is shown in Figure 4. The light-emitting diode in the figure is used to display the sending and receiving status of the communication data. A 120W matching resistor is connected between the two output leads of RS485, and a first-order low-pass filter is performed respectively. It should be noted that the power supply and ground at both ends of the optical isolator must be absolutely insulated to achieve true isolation.
(4) Ferroelectric storage and watchdog circuit design
Aluminum electromagnetic casting composite magnetic field controller involves a series of parameter settings and storage, and may be frequently modified repeatedly. In addition, the on-site working environment is harsh. In order to improve the anti-interference ability of the system, an external system watchdog must be installed. In view of the above reasons, the component FM31256 with serial non-volatile memory (ferroelectric memory-unlimited read and write times, power-off data retention for 10 years), real-time clock/calendar, low voltage reset, watchdog, and fast two-wire serial interface (I2C) is selected. The specific circuit is shown in Figure 5.
When making the PCB board, in order to improve the stability and reliability of communication between DSP and FM312561, the two should be as close as possible, the I2C communication line should be as short as possible, and a low-pass filter (100W, 100p) can be considered.
(5) Human-machine interface design
The human-machine interface is managed by a dedicated single-chip microcomputer. The single-chip microcomputer and the system's main control core DSP communicate in the form of SPI bus, which is simple to program and easy to implement. The single-chip microcomputer mainly completes the functions of keyboard scanning (parameter setting, etc.) and LCD display (parameter display of operation detection). According to the needs of the human-machine interface function and considering the cost performance, the C8051F410 single-chip microcomputer launched by Xinhualong is selected, and the display device is the LCM128×64 blue backlight LCD of Beijing Qingyun Company. According to the overall design plan, 6 buttons are set, and a matrix structure is adopted. The human-machine interface block diagram is shown in Figure 6.
[page]
1.2 System software design
(1) System software architecture
In view of the fact that the whole system has to realize many tasks, all DSP peripherals are used, and the real-time processing requirements are relatively high. In addition, the DSP (TMS320F2808) platform supports and can carry the development of RTOS, so the system software is designed using mC/OS-II. mC/OS-II is a real-time multi-tasking operating system with open source, portable, ROMable, scalable, preemptive, and preemptive [3, 5]. The whole system software is divided into two steps: a. porting μC/OS-II to DSP; b. writing software on the μC/OS-II platform. Porting μC/OS-II to DSP only requires modifying the code of the three files OS_CPU.H, OS_CPU_C.C and OS CPU A.A related to the processor, and the workload of porting is relatively small. Since μC/OS-II is a priority-based preemptive real-time multi-tasking operating system, before writing the code, the number of tasks in the system and the priority level of each task should be confirmed, and a certain amount of stack space should be allocated to each task for runtime calling. In other words, the functional modules of the composite magnetic field control system software must be managed first.
According to the particularity of the composite magnetic field control system, the control software is divided into ten levels from 0 to 9. Table 1 shows the functional modules of the software and their corresponding task names and task priority levels.
The flow of the control program is: first, initialize the CPU and program data; then initialize the operating system, mainly completing the initialization of the task control block (TCB), the initialization of the TCB priority table, the initialization of the TCB linked list, the initialization of the event control block (ECB) linked list, the creation of an empty task, etc.; then create task DTKST, and create other tasks in task DTKST; finally start multi-task scheduling. After the multi-task scheduling starts, start the clock beat source to start timing. This beat source provides the system with a periodic clock interrupt signal to achieve delay and timeout confirmation. When the clock interrupt comes, the system suspends the currently executing task, protects the scene, performs interrupt processing, and determines whether the task delay expires. If so, the task is put into the ready state, and the priorities of all tasks that have entered the ready state are compared. The highest priority task is executed through task switching. If no other task enters the ready state, the scene is restored to continue to execute the original task. Tasks communicate with each other through semaphores and message mailboxes, and tasks and interrupts communicate with each other through message mailboxes.
On the basis of ensuring the realization of functions, in order to further improve the reliability of the system, a system monitoring task is added. The function of this task is to monitor the operation of other tasks in the system. When the monitored task is about to finish running, the monitoring task sends a message to indicate that it is running normally. When the monitored task is running, the monitoring task waits for the monitored task to send it a message, and the waiting time is set to the maximum time required for the normal operation of the task. If the monitoring task receives a message within the waiting time, it is considered that the task sending the message is running normally, and the next task starts to run according to the execution order of each task, and the monitoring task waits for the message sent by the next task. If the waiting time has passed and the monitoring task still has not received the message, the system's time management function will force the monitoring task to be considered as ready. Because the monitoring task has the highest priority, it will seize the control of the CPU and take corresponding error correction plans to ensure the stable operation of the system.
(2) Human-computer interface programming
The human-machine interface includes microcontroller initialization, keyboard scanning subroutine, LCD subroutine, and SPI communication subroutine. The specific software implementation flow chart is shown in Figure 7. Serial communication is used between LCD and microcontroller. In view of the unique serial communication protocol of LCD itself, the microcontroller uses I/O port to simulate this protocol. Each data line is processed with first-order low-pass filter (100W, 100p) to improve communication stability and anti-interference ability. Software anti-shake processing is performed in the actual keyboard scanning program.
(3) High-frequency dual narrow pulse train software design
According to the specific requirements of high-frequency dual narrow pulse train and the principle block diagram designed above, the three functional modules of timing counter, 2-to-1 switch (initial state output '1'), and logic AND gate are constructed by VHDL programming through QuartusII software platform and connected according to the principle diagram. The simulation results can well achieve the required leading edge consistency. The simulation waveform is shown in Figure 8. The designed program is downloaded to CPLD (Altera development board) and observed by analog oscilloscope and virtual instrument respectively, achieving the expected design purpose. The waveform observed by virtual instrument is shown in Figure 9. (In the simulation waveform: Duble clk-dual narrow pulse; out_serial-high-frequency dual narrow pulse train; in the virtual instrument waveform; yellow line (bottom)-dual narrow pulse; green line (top)-high-frequency dual narrow pulse train.)
2 Conclusion
Aiming at the control requirements of the special composite magnetic field of aluminum electromagnetic semi-continuous casting, this paper designs an improved magnetic field controller based on the aluminum electromagnetic fast continuous casting and rolling composite magnetic field controller (which has been in operation in Fuzhou Ruimin Aluminum Strip Factory). The dual-core (DSP+single-chip microcomputer) processing form facilitates the realization of the overall function and improves the stability and reliability of the system. The high-frequency pulse train, which is a trigger pulse mode of high-power thyristors, is realized by CPLD, which has high stability and flexible application. In view of the harsh working environment of the special composite magnetic field controller, the EMC and EMI processing measures are fully considered in the production of PCB boards, such as A/D signal separation, good design and management of power modules, separation of large/small signals, processing of A/D sampling signal lines, and photoelectric isolation of I/O. After testing, the effect is good.
Previous article:Wavelet Processing of EEG Signal Based on DSP Builder
Next article:Implementation of High-Speed Clock Data Recovery Circuit Based on FPGA
Recommended ReadingLatest update time:2024-11-16 19:32
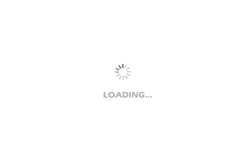
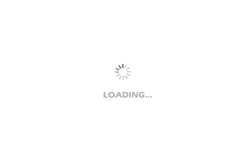
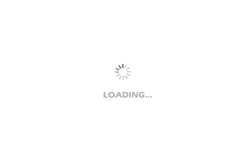
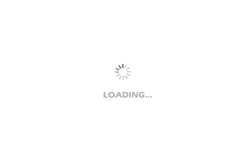
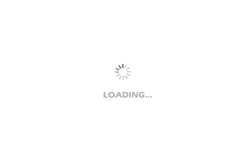
- Popular Resources
- Popular amplifiers
- Huawei's Strategic Department Director Gai Gang: The cumulative installed base of open source Euler operating system exceeds 10 million sets
- Analysis of the application of several common contact parts in high-voltage connectors of new energy vehicles
- Wiring harness durability test and contact voltage drop test method
- Sn-doped CuO nanostructure-based ethanol gas sensor for real-time drunk driving detection in vehicles
- Design considerations for automotive battery wiring harness
- Do you know all the various motors commonly used in automotive electronics?
- What are the functions of the Internet of Vehicles? What are the uses and benefits of the Internet of Vehicles?
- Power Inverter - A critical safety system for electric vehicles
- Analysis of the information security mechanism of AUTOSAR, the automotive embedded software framework
Professor at Beihang University, dedicated to promoting microcontrollers and embedded systems for over 20 years.
- Innolux's intelligent steer-by-wire solution makes cars smarter and safer
- 8051 MCU - Parity Check
- How to efficiently balance the sensitivity of tactile sensing interfaces
- What should I do if the servo motor shakes? What causes the servo motor to shake quickly?
- 【Brushless Motor】Analysis of three-phase BLDC motor and sharing of two popular development boards
- Midea Industrial Technology's subsidiaries Clou Electronics and Hekang New Energy jointly appeared at the Munich Battery Energy Storage Exhibition and Solar Energy Exhibition
- Guoxin Sichen | Application of ferroelectric memory PB85RS2MC in power battery management, with a capacity of 2M
- Analysis of common faults of frequency converter
- In a head-on competition with Qualcomm, what kind of cockpit products has Intel come up with?
- Dalian Rongke's all-vanadium liquid flow battery energy storage equipment industrialization project has entered the sprint stage before production
- Allegro MicroSystems Introduces Advanced Magnetic and Inductive Position Sensing Solutions at Electronica 2024
- Car key in the left hand, liveness detection radar in the right hand, UWB is imperative for cars!
- After a decade of rapid development, domestic CIS has entered the market
- Aegis Dagger Battery + Thor EM-i Super Hybrid, Geely New Energy has thrown out two "king bombs"
- A brief discussion on functional safety - fault, error, and failure
- In the smart car 2.0 cycle, these core industry chains are facing major opportunities!
- The United States and Japan are developing new batteries. CATL faces challenges? How should China's new energy battery industry respond?
- Murata launches high-precision 6-axis inertial sensor for automobiles
- Ford patents pre-charge alarm to help save costs and respond to emergencies
- New real-time microcontroller system from Texas Instruments enables smarter processing in automotive and industrial applications
- iTOP-iMX6ULL development board-Using UVC camera under Qt5
- How to achieve high-performance mobile phone design? The mobile phone college evaluation seminar will reveal the answer for you!
- When checking the PCB using Altium Designer, I found that the signal line is segmented. What's going on?
- MicroPython Hands-on (26) - OneNET of the Internet of Things
- MSP430F5342 uses MAX31856 to collect multiple thermocouples
- Just to meet you, Fuchang Electronics WeChat recruitment is now online
- Begging
- EEWORLD University ---- FPGA design and FPGA application based on Verilog HDL (Intel official tutorial)
- Showing off the goods + the first wave of development boards
- RF Circuit Engineering Design