Zhou Weiping, vice president of Hua Hong Semiconductor, delivered a report titled "Dual-core Engine, Green Intelligent Manufacturing, Winning the Chip Future" at the 23rd China Integrated Circuit Manufacturing Annual Conference and Guangdong Integrated Circuit Industry Development Forum in 2020, comprehensively analyzing Hua Hong Group's "8+12" dual-core engine strategy.
Hua Hong Group currently has Jinqiao Base, Zhangjiang Base, Kangqiao Base and Wuxi Base, with a total of 7 factories, of which Hua Hong Grace has 3 8-inch factories and 1 12-inch factory. The total monthly production capacity of 8-inch is 178,000 pieces, and the monthly production capacity of 12-inch is 65,000 pieces. Hua Hong Group's ranking in the global integrated circuit foundry industry has risen from 7th in 2016 to 6th in 2017, and entered 5th for the first time in 2019.
Vice President Zhou Weiping emphasized that HHG has responded to the country's green development strategy by building a green enterprise that integrates green technology, green production, and green construction to achieve environmentally friendly and sustainable development.
Hua Hong "core" speed
In August 2017, Huahong Group signed an agreement with the Wuxi Municipal Government. The first phase of the project will build a 12-inch integrated circuit production line (Huahong Plant 7) with a process level of 90-65/55 nanometers and a monthly output of 40,000 pieces, supporting applications in emerging fields such as 5G and the Internet of Things. This is the first R&D and manufacturing base of Huahong Group to be integrated into the high-quality development strategy of the Yangtze River Delta and to be deployed outside Shanghai and in the Yangtze River Delta. It has a symbolic significance in Huahong's development strategy. Huahong Wuxi Project is the most advanced special process production line in the country, the first 12-inch power device foundry production line in the country, and the first self-controlled 12-inch production line in Jiangsu Province. The project construction speed is very fast, and it was started and capped in the same year, and completed and put into production in 17 months. Based on the group's own technology, the R&D team tackled the key problems one year in advance, and the R&D results were accelerated to the production line. The special process R&D was smoothly promoted, and the product process was successfully put into production at one time. In terms of market development, it has good cooperation with many design companies at home and abroad. The 12-inch Wuxi base is committed to creating diversified and comprehensive customer solutions, and the development of the base has begun to accelerate. While steadily advancing the certification of multiple technology platforms, we have also achieved high-yield shipments. As of the second quarter of 2020, the products delivered to customers by the 12-inch production line of the Wuxi base include smart card chips, power devices, and CIS products; in the second half of the year, super-junction products will also begin to be shipped to meet the needs of emerging markets such as new energy vehicles. We have also accelerated the construction of production capacity and production operations, and have formed a monthly production capacity of 10,000 pieces, and are about to form a monthly production capacity of 20,000 pieces.
Focus on special crafts
Hua Hong Grace started to create its own "core" road in 2002, and established the first 8-inch Trench MOSFET foundry production line in China. It is the world's first 8-inch pure wafer foundry that provides power device foundry services. From 2002 to 2010, it completed the development of advanced trench-type medium and low voltage MOSFET/SGT/TBO and other power device technologies; in 2010, the high-voltage 600V-700V trench and planar MOSFET processes entered the mass production stage; in 2011, the first 8-inch IGBT foundry production line was mass-produced, and the first-generation deep trench super junction process entered the mass production stage in the same year. In the same year, the 1200V trench NPT IGBT process also completed research and development and entered the mass production stage; in 2013, the second-generation deep trench super junction process was launched on the market, and the 600V-1200V trench field stop IGBT (FDB process) was also successfully mass-produced. In 2020, 12-inch power products will be put into mass production.
Cumulative shipments of power devices exceeded 8 million 8-inch wafers; monthly production capacity exceeded 100,000 pieces (equivalent to 8-inch wafers) in 2020; the proportion of high-end power devices (super junction SJ and IGBT) increased rapidly, with sales and shipments from 2015 to 2019
The annual compound growth rate exceeds 50%. In the field of power device manufacturing, the company has 341 invention patents, including 18 US invention patents; among them, there are 25 IGBT back-side processes, 67 front-side processes, 94 low-voltage MOSFETs and 155 super junction SJs.
As one of Hua Hong Grace's core businesses, the company focuses on the following aspects in terms of power devices:
First, in terms of DMOS/SGT, it has a variety of process structures such as trench gate MOSFET, bottom thick gate oxide (BTO) MOSFET, top-bottom structure SGT, left-right structure SGT, etc. Silicon-based MOSFET is the basis of power device technology. Subsequent processes are continuously upgraded and improved based on this process platform. Hua Hong Hongli is committed to optimizing pitch size, improving cell density, and has the industry's leading on-resistance. Hua Hong Hongli's MOSFET products have passed automotive certification and cooperated with customers to complete the application of relatively core key components such as automotive oil pumps and power steering systems.
The second is super junction (SJ). Super junction MOSFET is the mainstay of Hua Hong Hongli's power semiconductor process platform. In 2011, the first generation of super junction MOSFET process began mass production; in 2013, through technological innovation, the pitch size became smaller and smaller, while the pitch verticality became larger and larger, reducing the junction resistance, and launching the second generation of super junction MOSFET process; in 2015, further optimization was carried out and the 2.5 generation of super junction MOSFET process was launched; in 2017, the third generation of super junction MOSFET process was trial-produced.
Hua Hong Hongli has an original deep trench super junction technology solution with independent intellectual property rights, which can significantly reduce the on-resistance. At the same time, it can significantly shorten the processing cycle and reduce production costs during the manufacturing process. Super junction MOSFET is suitable for the 150V-900V voltage range and the current range of 1-100A. It has lower resistance, higher efficiency and relatively low heat dissipation, so it has a large number of applications in demanding switching power supplies, which is highly consistent with the current popular high-power fast charging power supply, LED lighting power supply and new energy vehicle charging piles and other application requirements.
The third is IGBT. Hua Hong Hongli is the first company in China to have the most complete and perfect IGBT thin wafer backside processing technology. It is also the first company in China to mass produce deep trench field-stop IGBT products. As the core of electric vehicles, silicon-based IGBT is a great test of the ability and experience of wafer manufacturing. From the perspective of device structure, the front of the IGBT chip is similar to an ordinary MOSFET, and the difficulty lies in realizing the backside structure. As the earliest company in China, Hua Hong Hongli has the most perfect and complete set of IGBT thin wafer backside processing technology, including backside thin slices, backside high-energy ion implantation, backside laser annealing, and backside metallization, so that customers' products can be comparable to the mainstream international IDM products in the industry.
The voltage range of Hua Hong Hongli's IGBT product line covers 600~1700V; the current range covers 10~400A, gradually moving from consumer to industrial and commercial, new energy vehicles and other fields.
Vice President Zhou Weiping believes that the future prospects of the power device field are promising. The company has put forward four points in terms of becoming bigger and stronger: First, based on the "8+12" strategy, we will deeply cultivate the power device field, continuously update and iterate in technology, and pursue the higher power density and lower loss required by power devices; second, give full play to the 12-inch smaller line width characteristics, continue to develop and optimize DMOS, SGT, super junction SJ, IGBT technology, and accelerate entry into the high-end power device market; third, "8+12" go hand in hand to provide customers with more sufficient production capacity and more advantageous green "core" foundry solutions; fourth, deepen strategic cooperation, fully support the construction of the industrial ecosystem, and promote the synergy and win-win situation of the global integrated circuit manufacturing supply chain.
Developing the automotive market
The development trend of smart electric vehicles has strongly driven a substantial increase in the number of semiconductor components in automotive electronics. In the field of automotive electronics, the three major categories of semiconductor chips, microcontrollers, analog chips, and power devices, have large market scales and good future growth potential, which is also the focus of Hua Hong Semiconductor's layout in the field of automotive electronics under Hua Hong Group.
Hua Hong Semiconductor has achieved a large number of applications in automotive electronics such as on-board power/engine data storage, engine and airbag control, oil pump system, AC/DC converter, body stability (ESP) system, electric vehicle inverter, infotainment system, voice system, etc. Industry and automobiles have become the company's second largest application market, accounting for about 25% of the company's total revenue.
Previous article:2020 Automotive Cockpit SoC Research Report: More Displays, AI Functions, and ADAS Integration
Next article:CATL's global throne lost? LG Chem competes for power battery dominance
Recommended ReadingLatest update time:2024-11-16 04:17
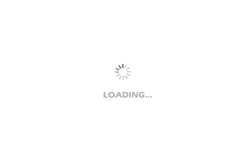
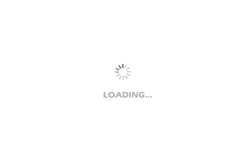
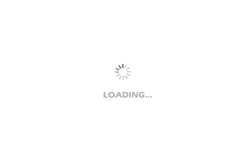
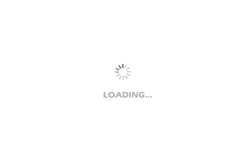
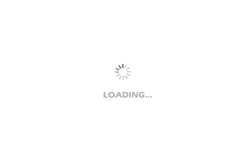
- Huawei's Strategic Department Director Gai Gang: The cumulative installed base of open source Euler operating system exceeds 10 million sets
- Analysis of the application of several common contact parts in high-voltage connectors of new energy vehicles
- Wiring harness durability test and contact voltage drop test method
- Sn-doped CuO nanostructure-based ethanol gas sensor for real-time drunk driving detection in vehicles
- Design considerations for automotive battery wiring harness
- Do you know all the various motors commonly used in automotive electronics?
- What are the functions of the Internet of Vehicles? What are the uses and benefits of the Internet of Vehicles?
- Power Inverter - A critical safety system for electric vehicles
- Analysis of the information security mechanism of AUTOSAR, the automotive embedded software framework
Professor at Beihang University, dedicated to promoting microcontrollers and embedded systems for over 20 years.
- LED chemical incompatibility test to see which chemicals LEDs can be used with
- Application of ARM9 hardware coprocessor on WinCE embedded motherboard
- What are the key points for selecting rotor flowmeter?
- LM317 high power charger circuit
- A brief analysis of Embest's application and development of embedded medical devices
- Single-phase RC protection circuit
- stm32 PVD programmable voltage monitor
- Introduction and measurement of edge trigger and level trigger of 51 single chip microcomputer
- Improved design of Linux system software shell protection technology
- What to do if the ABB robot protection device stops
- Allegro MicroSystems Introduces Advanced Magnetic and Inductive Position Sensing Solutions at Electronica 2024
- Car key in the left hand, liveness detection radar in the right hand, UWB is imperative for cars!
- After a decade of rapid development, domestic CIS has entered the market
- Aegis Dagger Battery + Thor EM-i Super Hybrid, Geely New Energy has thrown out two "king bombs"
- A brief discussion on functional safety - fault, error, and failure
- In the smart car 2.0 cycle, these core industry chains are facing major opportunities!
- The United States and Japan are developing new batteries. CATL faces challenges? How should China's new energy battery industry respond?
- Murata launches high-precision 6-axis inertial sensor for automobiles
- Ford patents pre-charge alarm to help save costs and respond to emergencies
- New real-time microcontroller system from Texas Instruments enables smarter processing in automotive and industrial applications
- VICOR "Bidirectional 48V/12V Converter Module" evaluation board is now available for free!
- FPGA introductory series experimental tutorial——
- Grounding of electronic equipment
- What is the difference between the full-port and half-port of Zhongying SH367309 5-16 series lithium battery protection chip?
- 【DIY Creative LED】The soldered board has normal charging function
- ESP32 SD/MMC hardware connection method
- Domestic chips are amazing. I just applied for a board. CH579 is so small but it integrates network, USB, and Bluetooth.
- Embedded System Design and Examples.pdf
- [GD32L233C-START Review] Development environment construction and download test
- Gallium nitride substrate production technology and equipment