In line with the noble DIY spirit of not seeking the best, but the most rustic. Grit your teeth and stomp your feet, grab your tools, and make a heat transfer machine!
Although they are available on the market, I don’t know whether the finished heat transfer machines are easy to use. I might as well make it myself and make it whatever I want!
Materials: The thermal transfer machine requires rubber rollers, heaters, gear boxes and other components. But it is not worth it to make all these by yourself, so I set my sights on the nearly scrapped laser printer at home (model HP4LC). Whether in terms of structure layout or size, this machine is the best choice. Dismantle!
The heater is an independent component with two springs on the side. After removing them, the entire component can be completely disassembled. The HP4LC machine uses a ceramic heater with a total of 4 leads, 2 of which are used to power the heater and the other 2 are temperature sensors. This makes temperature control very convenient.
This machine is good, but it's a pity that it's too big to be directly converted into a thermal transfer machine. Let me reduce its weight!
Tools: A Type 87 bow. The gearbox assembly and the main frame are all divided into two parts. It looks so good now. Clean it, apply some butter, and assemble it together. It looks like it's made!
The next job is the circuit. (The temperature control circuit of the original machine is dizzy, so I just made it myself) [page]
Part of the stepper motor drive circuit can be retained, but the stepper pulse generator still needs to be made by yourself. The reason for using a stepper motor is mainly because its speed is stable and will not slow down due to increased load, which is conducive to transferring circuit boards.
(Step pulse generation)
(Temperature control)
I originally planned to use a single chip microcomputer to complete the circuit, but later I found that the function was quite simple, so I just used three 40 series integrated circuits and an op amp. 4069 is used to generate square wave pulses; 4013 is a dual D flip-flop, which divides the square wave pulse by 2 and generates two step drive signals with a phase difference of 90 degrees.
I was lazy and directly sawed off the driver chip of the Epson inkjet, and led out 5 leads, namely +5V, GND, +12V, Phase1, Phase2. Doesn’t it have a bit of thick film integration flavor? It is still inserted upright on the circuit board.
The temperature control circuit is connected with 358 op amp and RS trigger. It is similar to the 555 circuit except that the wires are connected, which is more convenient. The upper and lower limits of the temperature can be controlled independently by two potentiometers. The whole board is made of perforated board, and it is soldered as soon as it is received, without drawing any pictures.
In the end it looks like this, very rustic, right? That’s right!
OK, first power on the stepper motor and test it. There is no problem, it runs normally, but the speed feels a bit fast. Increasing the oscillation capacitor will solve the problem.
Strange, why is the direction of the motor's rotation random, sometimes forward, sometimes reverse? This is not OK, analyze the reason: the pulse sent to the D flip-flop is uncertain whether the rising edge comes first or the falling edge comes first, resulting in an uncertain order of the two D flip-flops flipping. - Add a RC delay network to the enable end of the D flip-flop. OK, now it's normal.
The temperature control circuit was tested successfully at one time. The most critical moment has come! All the circuits are connected and powered on. No smoke or explosions were seen. The optimal temperature was reached by repeatedly adjusting the potentiometer. Take a look at the transfer effect. The lines are much smoother than those transferred by iron. I will make a case when I have time.
Previous article:Ubyte2 speaker cable DIY diagram + actual operation
Next article:Ten years of hard work to make a DIY LM4702 amplifier
Recommended ReadingLatest update time:2024-11-16 16:35
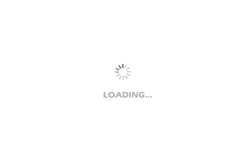
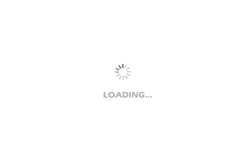
- Popular Resources
- Popular amplifiers
-
Maker Electronics Production Examples-36 Interesting Electronics DIY Projects-Love Making-Charles Platt-2016-
-
Maker Electronics Production Examples: 36 Interesting Electronics DIY Projects (Love Making) (Charles Platt)
-
Fall in love with drones: principle structure, aerial photography control and DIY examples.pdf
-
Diffusion Model from Principle to Practice (Li Xinwei, Su Busheng, Xu Haoran, Yu Haiming)
- High signal-to-noise ratio MEMS microphone drives artificial intelligence interaction
- Advantages of using a differential-to-single-ended RF amplifier in a transmit signal chain design
- ON Semiconductor CEO Appears at Munich Electronica Show and Launches Treo Platform
- ON Semiconductor Launches Industry-Leading Analog and Mixed-Signal Platform
- Analog Devices ADAQ7767-1 μModule DAQ Solution for Rapid Development of Precision Data Acquisition Systems Now Available at Mouser
- Domestic high-precision, high-speed ADC chips are on the rise
- Microcontrollers that combine Hi-Fi, intelligence and USB multi-channel features – ushering in a new era of digital audio
- Using capacitive PGA, Naxin Micro launches high-precision multi-channel 24/16-bit Δ-Σ ADC
- Fully Differential Amplifier Provides High Voltage, Low Noise Signals for Precision Data Acquisition Signal Chain
- Innolux's intelligent steer-by-wire solution makes cars smarter and safer
- 8051 MCU - Parity Check
- How to efficiently balance the sensitivity of tactile sensing interfaces
- What should I do if the servo motor shakes? What causes the servo motor to shake quickly?
- 【Brushless Motor】Analysis of three-phase BLDC motor and sharing of two popular development boards
- Midea Industrial Technology's subsidiaries Clou Electronics and Hekang New Energy jointly appeared at the Munich Battery Energy Storage Exhibition and Solar Energy Exhibition
- Guoxin Sichen | Application of ferroelectric memory PB85RS2MC in power battery management, with a capacity of 2M
- Analysis of common faults of frequency converter
- In a head-on competition with Qualcomm, what kind of cockpit products has Intel come up with?
- Dalian Rongke's all-vanadium liquid flow battery energy storage equipment industrialization project has entered the sprint stage before production
- Allegro MicroSystems Introduces Advanced Magnetic and Inductive Position Sensing Solutions at Electronica 2024
- Car key in the left hand, liveness detection radar in the right hand, UWB is imperative for cars!
- After a decade of rapid development, domestic CIS has entered the market
- Aegis Dagger Battery + Thor EM-i Super Hybrid, Geely New Energy has thrown out two "king bombs"
- A brief discussion on functional safety - fault, error, and failure
- In the smart car 2.0 cycle, these core industry chains are facing major opportunities!
- The United States and Japan are developing new batteries. CATL faces challenges? How should China's new energy battery industry respond?
- Murata launches high-precision 6-axis inertial sensor for automobiles
- Ford patents pre-charge alarm to help save costs and respond to emergencies
- New real-time microcontroller system from Texas Instruments enables smarter processing in automotive and industrial applications
- Communication between EMIF and FPGA of TMS320C6455
- 【GD32L233C-START Review】12. Hardware IIC drive OLED
- EEWORLD University Hall----Live Replay: TI 60G mmWave Sensor Overview and Application Introduction
- Short Range Communication Protocol
- Full-wave precision rectifier circuit composed of comparators
- NUCLEO-474 Download the official example prompt No debug probe... Solution
- SERDES interface circuit design
- TMS320C55x DSP Library
- Antenna Basics and Introduction to 40+ Antennas
- Brief analysis: RF power meter principle, classification, index and application