NI is developing new technologies that target industries and applications that require scalable sensor measurement systems that can scale to thousands of channels.
Traditional sensor measurement systems are often pre-customized and inflexible, with limited ability to expand channel counts and upgrade to new computing technologies as application requirements change. The new NI SC Express product family introduces sensor measurement technology that provides a scalable, simplified architecture for scalable sensor measurement systems based on the industry-standard PXI platform. In addition to reducing complexity, these new products offer three key benefits: better measurement accuracy, more flexible synchronization, and higher data throughput.
1) Use integrated signal conditioning to provide better measurement accuracy
Many sensors require signal conditioning before accurately digitizing their output. Some examples of signal conditioning include amplifiers, excitation, isolation, and filtering. Typically, you might implement signal conditioning through other front-end systems that connect to the data acquisition system to convert the conditioned analog signal into a digital signal. New technologies and miniaturization have helped companies integrate signal conditioning and analog-to-digital converters into the same device, providing higher measurement accuracy by eliminating cables and connectors that can introduce errors. Integrated signal conditioning also reduces the number of components in the measurement system, simplifying installation, maintenance, and calibration, and also reducing the size and cost of high-channel-count measurement systems.
The new SC Express modules use an integrated signal conditioning architecture to provide high-precision sensor measurements for the PXI platform. With more than 1,500 available modules from more than 70 manufacturers, the PXI platform helps you develop a highly flexible single measurement system that meets the different needs of most measurement applications while avoiding the risks of using dedicated form factors or dedicated data buses. Welcome to reprint, this article comes from Electronics Fans Network (http://www.elecfans.com )
An example of an application that can benefit from the new SC Express technology is scalable, high-precision measurements in advanced temperature chambers. The instruments in a temperature chamber must measure hundreds of thermocouples with high accuracy so you can precisely measure and control the temperature distribution of the chamber. With the NI PXIe-4353 SC Express module, you can measure up to 544 thermocouple channels using a single PXI chassis.

Table 1: Comparison of modules in the new NI SC Express product family
2) Flexible and high-performance synchronization
To use and analyze data effectively, you must know how the data is time-correlated. The complexity of correlating and synchronizing data increases significantly when acquiring multiple devices from different sensor types or when the sensors are spatially distributed over a large area. The need for synchronization is the most important aspect when selecting a measurement system.
For more than a decade, the PXI platform has provided world-class synchronization performance for measurement systems. PXI Express is the latest evolution of the PXI platform, designed to provide high synchronization for measurement I/O devices while maintaining backward compatibility. Using the 100 MHz differential clock in the PXI Express backplane, multiple instruments can base their sample clocks on the same reference source. The backplane trigger lines allow all devices in the chassis to be triggered in unison to the same 100 MHz clock edge. As with previous PXI chassis, timing and synchronization modules can replace the backplane clock to provide a higher accuracy clock in the same PXI Express chassis, and you can also use it to synchronize measurement devices in multiple PXI Express chassis. If the application requires synchronization of multiple chassis distributed over long distances, multiple chassis can be synchronized using a common clock signal using GPS or IRIG-B modules.
SC Express modules use the PXI Express bus to provide tight synchronization between devices in one chassis or across multiple chassis. For example, the NI PXIe-4330 bridge sensor input module has less than 100 ns channel-to-channel skew within a single module or between modules in a single chassis. In addition, NI has enhanced the NI-DAQmx driver software with a new way to configure multiple SC Express modules in a single chassis for synchronization. As shown in the figure below, you can use a single NI-DAQmx multi-device task in the NI LabVIEW graphical programming environment or a common text-based language such as .NET to configure and read data from multiple devices in the system, greatly simplifying the required code. If you use this programming method, the driver automatically configures all timing and triggering lines without sacrificing performance.
Structural test applications often require synchronized measurements from strain gauges and accelerometers to accurately compare measured stresses to values derived from finite element analysis models. You can simply use a single NI-DAQmx multi-device task to read synchronized stress and vibration measurements obtained with the new NI PXIe-4330 bridge sensor input module and NI PXIe-4496 accelerometer input module to accurately measure stress. Unlike traditional instrumentation, the SC Express module has the flexibility to adapt to changing requirements for structural testing that evolves over time with increasingly complex designs, such as wings made of stronger and lighter materials.
3) High data throughput
High channel count measurement systems must transfer large amounts of data to a host controller so you can analyze the data in real time or stream it to disk for later analysis. In the past, the communication bus bandwidth was the limiting factor for the number of channels or the maximum acquisition speed in a system. The only way to get around this limitation was to add onboard memory to the acquisition device, allowing for higher acquisition speeds for a limited time. In addition to being more expensive, this approach also adds complexity to the acquisition software and prevents users from viewing the data in real time.
The SC Express module is based on the PXI Express bus and provides a bandwidth of 250 MB/s per channel to transmit data to the controller. As shown in Figure 2, the new SC Express module can be expanded to a higher channel count without exceeding the communication bus bandwidth.
While the communication bus is not the limiting factor in measurement speed or number of channels, processing speed or write-to-disk performance may affect system performance. Using the NI-DAQmx driver, you can stream data directly into the Technical Data Management Stream (TDMS) file format, which provides up to 400 MB/s of logging throughput, enabling fast processing of terabytes of data. You can easily manage, analyze, visualize, and report useful information from these large data sets using the LabVIEW Data Search Toolkit or NI DIAdem data management software.
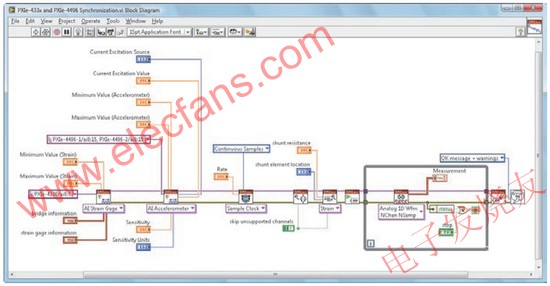
Figure 1: The NI-DAQmx multi-device task reads synchronized strain and accelerometer data from the NI PXIe-4330 bridge sensor input module and the NI PXIe-4496 accelerometer input module.
Many military and aerospace test engineers need to measure hundreds of analog signals at different voltages or ground levels. In addition to the flexibility to scale to hundreds of channels, the measurement system must have analog inputs with channel-to-channel isolation to safely measure the signals from these test cells. The new NI PXIe-4300 high-voltage analog input module and NI DAQmx with TDMS capabilities are well suited to meet the challenges of these test cells.
Quickly and easily build scalable high-channel-count sensor management systems
SC Express modules provide integrated signal conditioning and data acquisition on the PXI Express bus, providing higher-precision measurements with world-class synchronization and high data throughput. If you combine measurement modules with NI-DAQmx features (including TDMS and multi-device tasks), you can easily build a scalable sensor measurement system to meet the unique needs of your high-channel-count measurement applications.
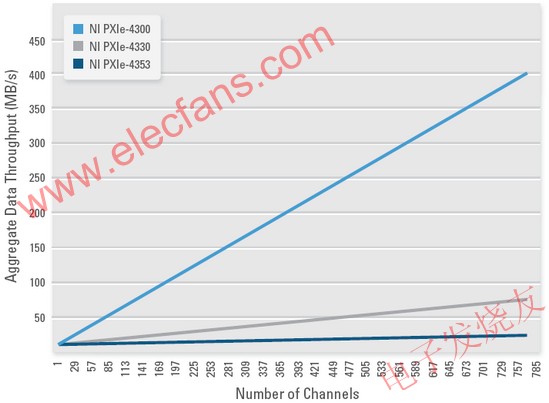
Figure 2: The total throughput of SC Express modules increases as the number of channels increases.
– Andy Deck
Andy Deck is a measurement and conditioning manager at NI. He received his bachelor’s degree in mechanical engineering from the University of Texas at Austin.
New PXI Express Data Acquisition Module with Built-in Signal Conditioning
New high-performance PXI Express data acquisition (DAQ) modules with built-in signal conditioning are ideal for strain, full-bridge, thermocouple, and high-voltage measurements. These SC Express modules provide higher measurement accuracy, higher data throughput, and tighter synchronization for high-channel-count measurement applications. The NI PXIe-4330 bridge input module features a 24-bit ADC for each channel and up to 25 kS/s per channel sampling rate. The NI PXIe-4353 thermocouple input module features 24-bit resolution, 0.3 degrees Celsius accuracy, and 300 V board-level isolation. The NI PXIe-4300 high-voltage analog input module provides channel-to-channel isolation and synchronized ADC chips that can measure up to 300 V per channel. As part of the PXI platform, SC Express modules can be easily synchronized with other PXI modules, such as NI X Series data acquisition devices, NI DSA modules, and other modular instruments.
Previous article:Overview of LEM's HTT Series Current Sensors
Next article:Silicon Labs' infrared proximity sensor series Si1143
Recommended ReadingLatest update time:2024-11-16 19:51
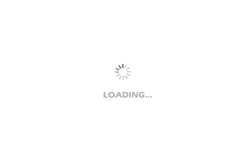
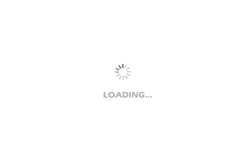
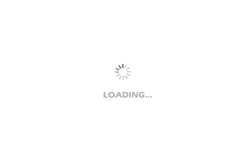
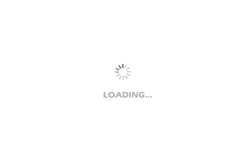
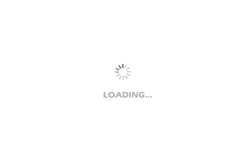
- Popular Resources
- Popular amplifiers
-
Analysis and Implementation of MAC Protocol for Wireless Sensor Networks (by Yang Zhijun, Xie Xianjie, and Ding Hongwei)
-
Introduction to Internet of Things Engineering 2nd Edition (Gongyi Wu)
-
西门子S7-12001500 PLC SCL语言编程从入门到精通 (北岛李工)
-
Modern Motor Control Technology (Wang Chengyuan, Xia Jiakuan, Sun Yibiao)
- High signal-to-noise ratio MEMS microphone drives artificial intelligence interaction
- Advantages of using a differential-to-single-ended RF amplifier in a transmit signal chain design
- ON Semiconductor CEO Appears at Munich Electronica Show and Launches Treo Platform
- ON Semiconductor Launches Industry-Leading Analog and Mixed-Signal Platform
- Analog Devices ADAQ7767-1 μModule DAQ Solution for Rapid Development of Precision Data Acquisition Systems Now Available at Mouser
- Domestic high-precision, high-speed ADC chips are on the rise
- Microcontrollers that combine Hi-Fi, intelligence and USB multi-channel features – ushering in a new era of digital audio
- Using capacitive PGA, Naxin Micro launches high-precision multi-channel 24/16-bit Δ-Σ ADC
- Fully Differential Amplifier Provides High Voltage, Low Noise Signals for Precision Data Acquisition Signal Chain
- Innolux's intelligent steer-by-wire solution makes cars smarter and safer
- 8051 MCU - Parity Check
- How to efficiently balance the sensitivity of tactile sensing interfaces
- What should I do if the servo motor shakes? What causes the servo motor to shake quickly?
- 【Brushless Motor】Analysis of three-phase BLDC motor and sharing of two popular development boards
- Midea Industrial Technology's subsidiaries Clou Electronics and Hekang New Energy jointly appeared at the Munich Battery Energy Storage Exhibition and Solar Energy Exhibition
- Guoxin Sichen | Application of ferroelectric memory PB85RS2MC in power battery management, with a capacity of 2M
- Analysis of common faults of frequency converter
- In a head-on competition with Qualcomm, what kind of cockpit products has Intel come up with?
- Dalian Rongke's all-vanadium liquid flow battery energy storage equipment industrialization project has entered the sprint stage before production
- Allegro MicroSystems Introduces Advanced Magnetic and Inductive Position Sensing Solutions at Electronica 2024
- Car key in the left hand, liveness detection radar in the right hand, UWB is imperative for cars!
- After a decade of rapid development, domestic CIS has entered the market
- Aegis Dagger Battery + Thor EM-i Super Hybrid, Geely New Energy has thrown out two "king bombs"
- A brief discussion on functional safety - fault, error, and failure
- In the smart car 2.0 cycle, these core industry chains are facing major opportunities!
- The United States and Japan are developing new batteries. CATL faces challenges? How should China's new energy battery industry respond?
- Murata launches high-precision 6-axis inertial sensor for automobiles
- Ford patents pre-charge alarm to help save costs and respond to emergencies
- New real-time microcontroller system from Texas Instruments enables smarter processing in automotive and industrial applications
- RISC-V MCU Development (I): MounRiver Studio Integrated Development Environment
- Design of filter circuit
- Experience TouchGFX with rewards and start your creative GUI journey
- EVAL-M3-TS6-665PN board review
- Remove the vicor module power supply
- IoT Gateways - A Simple Guide to IoT
- Help with MS41908M lens driver chip driver
- Wideband digital receiver based on real signal processing and FPGA implementation
- RISC-V MCU Development (V): Debug Configuration
- I want to ask about the difference between EL357 and LTV354, two optocouplers.