0. Introduction
Fans are general-purpose machines, which are widely used in various sectors of the national economy. Fans are widely used in ventilation, dust removal and cooling of factories, mines, vehicles, buildings, household appliances, etc.; drying and selection of grains; wind tunnel wind sources and inflation and propulsion of hovercraft, etc. In addition, in some places with special requirements for ambient temperature, the temperature change is required to be below 1°C, which requires a fan temperature control system that can determine the rotation and stop of the fan according to the external ambient temperature.
The fan micro-temperature control system designed in this paper can achieve a temperature detection accuracy of 0.01℃, and the upper and lower temperature limits can be set manually, and it has an automatic sound and light alarm function.
1. Design requirements
This system uses a PT1000 temperature sensor to detect the ambient temperature (temperature detection accuracy 0.01°C), controls the fan cooling according to the ambient temperature changes, and has the functions of manually setting the upper and lower limits of the temperature, sound and light alarm, etc. The schematic diagram of its control panel is shown in Figure 1.
Specific technical requirements and functional descriptions are as follows:
(1) When the ambient temperature is within the set temperature range, the green LED is on and the fan does not work;
(2) When the ambient temperature approaches the set temperature upper limit (within 5°C), the yellow LED lights up, the fan operates at a low speed, and the buzzer emits three 500Hz alarm sounds;
(3) When the ambient temperature is higher than the set upper temperature limit, the red LED lights up, the fan runs at full speed, and the buzzer sounds for a long time.
(4) Dual fans are used to work in time-sharing mode, which is convenient for maintenance.
2. Design of fan temperature control system based on single chip microcomputer
2.1 System Hardware Design
2.1.1 System hardware composition
According to the design requirements, we adopt a modular design scheme for the fan control system, and divide the entire fan temperature control system into nine functional modules, namely: power module, fan control module, main control circuit module, display circuit module, key module, alarm module, temperature detection module, EEPROM module, serial communication module, etc. The relationship between each functional module is shown in Figure 2.
2.1.2 Introduction to each functional module of the system
(1) Power module
System power supply: external 12V/2A DC power supply Digital power supply: 51 single-chip microcomputer, AD conversion chip, photocoupler. Use 1 7805 three-terminal voltage regulator. Analog power supply: The fan is directly connected to the 12V power supply, and the PT1000 sensor is powered by 1 7805 three-terminal voltage regulator. Device requirements: 1 12V/2A DC power supply, 2 7805 three-terminal voltage regulators, 1 power indicator light, and 1 power switch.
(2) Fan control module (fan control adopts master-slave mode) This module uses a single-chip microcomputer IO port to output PWM signals, and controls the fan's stop and start and speed through an optocoupler and MC1413 drive circuit. The fan is powered directly by a 12V power supply. The circuit diagram is shown in Figure 3.
Device requirements: 2 0.8A fans, 1 MC1413 driver control chip, 2 6N137 optocouplers.
(3) Main control circuit module
The minimum system consists of STC11F16XE.
Device requirements: STC1 1F16XE chip, 11.0592MHz crystal oscillator, 22PF\1OuF\104 capacitor, 1K\10K resistor, 1 reset button. The schematic diagram is shown in Figure 4.
2.2.2 System software design source code
The system software development environment uses Keil uVision3.
Taking the fan control module as an example, the system software design source program is given:
3. Conclusion
This paper designs a fan temperature control system based on a single-chip microcomputer. It can collect data through a temperature sensor according to slight changes in ambient temperature and control the fan's action after signal processing. The control system adopts a modular design, has high reliability and is easy to maintain. It has been verified by experiments that it can achieve the intended function.
Previous article:Design of high-precision time interval measurement module based on single-chip microcomputer
Next article:Improved design of infrared pump based on SPCE061A control
Recommended ReadingLatest update time:2024-11-16 22:44
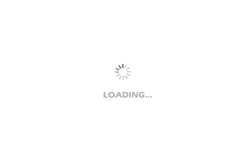
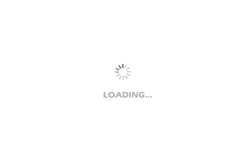
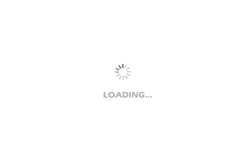
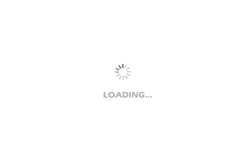
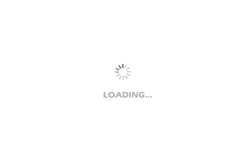
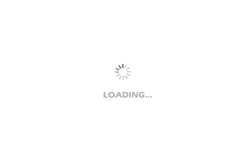
- Popular Resources
- Popular amplifiers
-
Wireless Sensor Network Technology and Applications (Edited by Mou Si, Yin Hong, and Su Xing)
-
Modern Electronic Technology Training Course (Edited by Yao Youfeng)
-
Modern arc welding power supply and its control
-
Small AC Servo Motor Control Circuit Design (by Masaru Ishijima; translated by Xue Liang and Zhu Jianjun, by Masaru Ishijima, Xue Liang, and Zhu Jianjun)
- High signal-to-noise ratio MEMS microphone drives artificial intelligence interaction
- Advantages of using a differential-to-single-ended RF amplifier in a transmit signal chain design
- ON Semiconductor CEO Appears at Munich Electronica Show and Launches Treo Platform
- ON Semiconductor Launches Industry-Leading Analog and Mixed-Signal Platform
- Analog Devices ADAQ7767-1 μModule DAQ Solution for Rapid Development of Precision Data Acquisition Systems Now Available at Mouser
- Domestic high-precision, high-speed ADC chips are on the rise
- Microcontrollers that combine Hi-Fi, intelligence and USB multi-channel features – ushering in a new era of digital audio
- Using capacitive PGA, Naxin Micro launches high-precision multi-channel 24/16-bit Δ-Σ ADC
- Fully Differential Amplifier Provides High Voltage, Low Noise Signals for Precision Data Acquisition Signal Chain
- Innolux's intelligent steer-by-wire solution makes cars smarter and safer
- 8051 MCU - Parity Check
- How to efficiently balance the sensitivity of tactile sensing interfaces
- What should I do if the servo motor shakes? What causes the servo motor to shake quickly?
- 【Brushless Motor】Analysis of three-phase BLDC motor and sharing of two popular development boards
- Midea Industrial Technology's subsidiaries Clou Electronics and Hekang New Energy jointly appeared at the Munich Battery Energy Storage Exhibition and Solar Energy Exhibition
- Guoxin Sichen | Application of ferroelectric memory PB85RS2MC in power battery management, with a capacity of 2M
- Analysis of common faults of frequency converter
- In a head-on competition with Qualcomm, what kind of cockpit products has Intel come up with?
- Dalian Rongke's all-vanadium liquid flow battery energy storage equipment industrialization project has entered the sprint stage before production
- Allegro MicroSystems Introduces Advanced Magnetic and Inductive Position Sensing Solutions at Electronica 2024
- Car key in the left hand, liveness detection radar in the right hand, UWB is imperative for cars!
- After a decade of rapid development, domestic CIS has entered the market
- Aegis Dagger Battery + Thor EM-i Super Hybrid, Geely New Energy has thrown out two "king bombs"
- A brief discussion on functional safety - fault, error, and failure
- In the smart car 2.0 cycle, these core industry chains are facing major opportunities!
- The United States and Japan are developing new batteries. CATL faces challenges? How should China's new energy battery industry respond?
- Murata launches high-precision 6-axis inertial sensor for automobiles
- Ford patents pre-charge alarm to help save costs and respond to emergencies
- New real-time microcontroller system from Texas Instruments enables smarter processing in automotive and industrial applications
- Increase the frequency range of the RC voltage-controlled oscillator
- How do you guys choose whether to use a 4-layer board or a 2-layer board?
- Thank you for being there + thank you for your wife's protection
- The electrical engineer blew up the company because of a resignation dispute...
- Sharing joy with others is worse than enjoying it alone——TI training’s “recommended courses” function is now available for public testing. We invite you to make suggestions and participate in the competition!
- Seeking advice from hardware experts: PWM control transistor buck-boost output waveform
- November 24 live broadcast review: NXP's embedded human machine interface solution detailed explanation (including video playback, ppt, Q&A)
- BLDC Motor Control Algorithm - FOC Brief Introduction
- PyPortal weather and clock display
- TL437x-EVM Evaluation Board Test Manual (1)