With the continuous development of semiconductor technology and deep pressure micron process, the switching speed of IC has increased from tens of MHz to hundreds of MHz, and even to several GHz. In high-speed PCB design, engineers often encounter signal integrity problems such as false triggering, damped oscillation, overshoot, undershoot, and crosstalk. This article will explore their causes, calculation methods, and how to use the IBIS simulation method in Allegro to solve these problems. 1 Definition of Signal Integrity Signal Integrity (SI) refers to the signal quality on the signal line. Poor signal integrity is not caused by a single factor, but by a combination of multiple factors in board-level design. The reasons for destroying signal integrity include reflection, ringing, ground bounce, crosstalk, etc. With the continuous increase in signal operating frequency, signal integrity issues have become the focus of high-speed PCB engineers. 2 Reflection 2.1 Formation and calculation of reflection Impedance discontinuity on the transmission line will cause signal reflection. When the impedance of the source end and the load end does not match, the load reflects part of the voltage back to the source end. Differential line transmission signals solve many problems.
What is a differential signal? In layman's terms, the driver sends two signals of equal value and opposite phase, and the receiver determines the logic state "0" or "1" by comparing the difference between the two voltages. The pair of lines that carry the differential signal is called the differential line. How to calculate the impedance of the differential line? The impedance of various differential signals is different. For example, the differential line impedance of USB D+ D- is 90ohm, and the differential line impedance of 1394 is 110ohm. It is best to read the specification or related information first. There are many impedance calculation tools now, such as polar's si9000. The factors that affect the differential impedance include line width, differential line spacing, dielectric constant, and dielectric thickness (the thickness of the dielectric between the differential line and the reference plane). Generally, the differential impedance is controlled by adjusting the differential line spacing and line width. When making the board, you should also tell the manufacturer which lines need to control the impedance. A differential signal uses a numerical value to represent the difference between two physical quantities. Strictly speaking, all voltage signals are differential, because one voltage can only be relative to another voltage. In some systems, the system ground is used as a voltage reference point. When ground is used as a reference for voltage measurements, the signal arrangement is called single-ended. We use this term because the signal is represented by the voltage on a single conductor.
The first benefit of differential signaling is that you can easily identify small signals because you are controlling the 'reference' voltage. In a ground reference, single-ended signaling system, the exact value of the measured signal depends on the consistency of the 'ground' within the system. The farther the signal source and signal receiver are, the greater the possibility that there will be differences in the voltage values of their local grounds. The signal value recovered from differential signaling is largely independent of the exact value of the 'ground', but within a certain range.
The second benefit of differential signaling is that it is highly immune to external electromagnetic interference (EMI). An interference source affects each end of the differential signal pair to almost the same extent. Since the difference in the PADSLOGIC voltage in the PADS determines the signal value, any identical interference that appears on the two conductors will be ignored. In addition to being less sensitive to interference, differential signals generate less EMI than single-ended signals.
The third benefit of differential signal is that the timing positioning is accurate. Since the switching change of differential signal is located at the intersection of two signals, unlike ordinary single-ended signal which relies on two threshold voltages, it is less affected by process and temperature, can reduce the timing error, and is more suitable for circuits with low amplitude signals. The currently popular LVDS (low voltage differential signaling) refers to this small amplitude differential signal technology.
Differentials do not need to consider crosstalk, because their crosstalk results will be offset at the final reception. In addition, differentials must be balanced in routing, and parallelism is only part of the balance.
I think the coupling of differential pairs should still be required. For single-line matching, although it is very mature in theory, there is still an error of about 5% in the actual PCB line (on a material, I have not done it myself). On the other hand, the differential line can be regarded as a self-loop system, or the signals on its two signal lines are related. Too loose coupling may cause interference from other places, and for some interface circuits, the equal length of the differential pair is an important factor in controlling the line delay. Therefore, I think the differential line should still be tightly coupled.
For most current high-speed PCB boards, it is beneficial to maintain good coupling
However, I hope everyone will not mistakenly believe that coupling is a necessary condition for differential pairs, as this may sometimes limit design ideas.
When doing high-speed design or analysis, you should not only know how most people do it, but also understand why others do it, and then understand and improve based on others' experience, and constantly exercise your creative thinking ability.
Matching is necessary, but the reason for matching is not reflection, but to reduce the degree of crosstalk interference. If the reduction is related to the matching method, if a series resistor is used, there will be no effect. However, if a termination matching method of grounding or connecting to the power supply is used, the crosstalk is reduced because the line impedance of the two lines is reduced...
For PCB LAYOUT engineers, the most important thing is how to ensure that these advantages of differential routing can be fully utilized in actual routing. Perhaps anyone who has been exposed to Layout will understand the general requirements of differential routing, which is "equal length and equal distance" in PCB design. Equal length is to ensure that the two differential signals always maintain opposite polarity and reduce common mode components; equal distance is mainly to ensure that the differential impedance of the two is consistent and reduce reflection. The "principle of being as close as possible" is sometimes also one of the requirements for differential routing. Differential routing can also be routed in different signal layers, but this method is generally not recommended because the differences in impedance and vias generated by different layers will destroy the effect of differential mode transmission and introduce common mode noise. In addition, if the coupling between the two adjacent layers is not tight enough, the ability of the differential routing to resist noise will be reduced, but if the appropriate spacing with the surrounding routing can be maintained, crosstalk will not be a problem. At normal frequencies (below GHz), EMI is not a serious problem. Experiments show that the radiation energy attenuation of differential traces 500 mils apart at 3 meters has reached 60dB, which is enough to meet the FCC electromagnetic radiation standards. Therefore, designers do not need to worry too much about electromagnetic incompatibility caused by insufficient differential line coupling. However, all these rules are not meant to be applied mechanically. Many engineers do not seem to understand the essence of high-speed differential signal transmission. The following focuses on several common misunderstandings in PCB differential signal design.
It is believed that differential traces must be very close. The purpose of bringing differential traces close is to enhance their coupling, which can not only improve immunity to noise, but also make full use of the opposite polarity of the magnetic field to offset the electromagnetic interference to the outside world. Although this approach is very beneficial in most cases, it is not absolute. If we can ensure that they are fully shielded and not interfered with by the outside world, then we do not need to achieve the purpose of anti-interference and EMI suppression through strong coupling with each other. How can we ensure that the differential traces have good isolation and shielding? Increasing the spacing with other signal traces is one of the most basic ways. The electromagnetic field energy decreases in a square relationship with the distance. Generally, when the line spacing exceeds 4 times the line width, the interference between them is extremely weak and can be basically ignored. In addition, the isolation of the ground plane can also play a good shielding role. This structure is often used in high-frequency (above 10G) IC package PCB design. It is called CPW structure, which can ensure strict differential impedance control (2Z0).
It is believed that differential signals do not need a ground plane as a return path, or that differential traces provide return paths for each other. The reason for this misunderstanding is that people are confused by surface phenomena or do not have a deep enough understanding of the mechanism of high-speed signal transmission. Differential circuits are insensitive to noise signals such as ground bounce and other noise signals that may exist on the power supply and ground planes. The partial return offset of the ground plane does not mean that the differential circuit does not use the reference plane as a signal return path. In fact, in signal return analysis, the mechanism of differential traces and ordinary single-ended traces is the same, that is, high-frequency signals always return along the loop with the smallest inductance. The biggest difference is that in addition to coupling to the ground, differential lines also have mutual coupling. The one with stronger coupling becomes the main return path. In PCB circuit design, the coupling between differential traces is generally small, often accounting for only 10~20% of the coupling degree, and more is coupling to the ground, so the main return path of differential traces still exists in the ground plane. When the ground plane is discontinuous, the coupling between the differential traces in the area without the reference plane will provide the main return path. Although the discontinuity of the reference plane does not have as serious an impact on the differential trace as it does on the ordinary single-ended trace, it will still reduce the quality of the differential signal and increase EMI, so it should be avoided as much as possible. Some designers also believe that the reference plane under the differential trace can be removed to suppress some common-mode signals in differential transmission, but theoretically this approach is not advisable. How to control the impedance? Not providing a ground impedance loop for the common-mode signal will inevitably cause EMI radiation, and this approach has more disadvantages than advantages.
It is believed that maintaining equal spacing is more important than matching line length. In actual PCB wiring, the requirements of differential design cannot often be met at the same time. Due to factors such as pin distribution, vias, and routing space, proper winding must be used to achieve the purpose of line length matching, but the result is that some areas of the differential pair cannot be parallel. The most important rule in the design of PCB differential routing is to match the line length, and other rules can be flexibly handled according to design requirements and actual applications.
Previous article:PROE's Engineering Management Experience
Next article:MPS Integrated Circuit Naming Method
Recommended ReadingLatest update time:2024-11-16 21:32
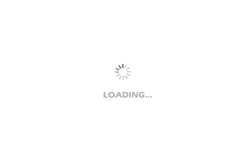
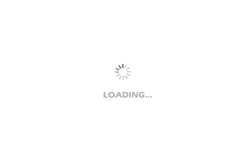
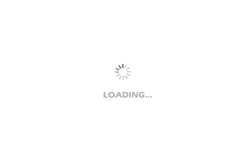
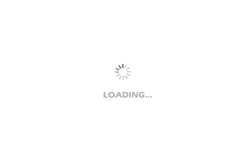
- High signal-to-noise ratio MEMS microphone drives artificial intelligence interaction
- Advantages of using a differential-to-single-ended RF amplifier in a transmit signal chain design
- ON Semiconductor CEO Appears at Munich Electronica Show and Launches Treo Platform
- ON Semiconductor Launches Industry-Leading Analog and Mixed-Signal Platform
- Analog Devices ADAQ7767-1 μModule DAQ Solution for Rapid Development of Precision Data Acquisition Systems Now Available at Mouser
- Domestic high-precision, high-speed ADC chips are on the rise
- Microcontrollers that combine Hi-Fi, intelligence and USB multi-channel features – ushering in a new era of digital audio
- Using capacitive PGA, Naxin Micro launches high-precision multi-channel 24/16-bit Δ-Σ ADC
- Fully Differential Amplifier Provides High Voltage, Low Noise Signals for Precision Data Acquisition Signal Chain
- Innolux's intelligent steer-by-wire solution makes cars smarter and safer
- 8051 MCU - Parity Check
- How to efficiently balance the sensitivity of tactile sensing interfaces
- What should I do if the servo motor shakes? What causes the servo motor to shake quickly?
- 【Brushless Motor】Analysis of three-phase BLDC motor and sharing of two popular development boards
- Midea Industrial Technology's subsidiaries Clou Electronics and Hekang New Energy jointly appeared at the Munich Battery Energy Storage Exhibition and Solar Energy Exhibition
- Guoxin Sichen | Application of ferroelectric memory PB85RS2MC in power battery management, with a capacity of 2M
- Analysis of common faults of frequency converter
- In a head-on competition with Qualcomm, what kind of cockpit products has Intel come up with?
- Dalian Rongke's all-vanadium liquid flow battery energy storage equipment industrialization project has entered the sprint stage before production
- Allegro MicroSystems Introduces Advanced Magnetic and Inductive Position Sensing Solutions at Electronica 2024
- Car key in the left hand, liveness detection radar in the right hand, UWB is imperative for cars!
- After a decade of rapid development, domestic CIS has entered the market
- Aegis Dagger Battery + Thor EM-i Super Hybrid, Geely New Energy has thrown out two "king bombs"
- A brief discussion on functional safety - fault, error, and failure
- In the smart car 2.0 cycle, these core industry chains are facing major opportunities!
- The United States and Japan are developing new batteries. CATL faces challenges? How should China's new energy battery industry respond?
- Murata launches high-precision 6-axis inertial sensor for automobiles
- Ford patents pre-charge alarm to help save costs and respond to emergencies
- New real-time microcontroller system from Texas Instruments enables smarter processing in automotive and industrial applications
- MSP430 MCU Development Record (12)
- [The answer has been announced] "I draw and you guess" and become a happy big kid!
- How to find the pspise simulation model of pt1000 thermistor? ? Help!!
- [Review SGP40] Intelligent ambient air quality tracking model #5 A board suitable for edge computing of sensors
- Several key points of TI's official two-phase LLC interleaving parallel procedure (to be continued)
- Python Qt GUI Quick Programming——PyQt Programming Guide
- Why does an RC filter circuit need a resistor? Can't a capacitor filter be used without a resistor?
- Received samples of SC8721 etc. that the forum helped to apply for
- Single-tube ADS-based simulation steps "Basic process"
- DJI Drone Phantom 3 remote control transmits frequency hopping signal