In view of the characteristics of PID control, this paper designs a control method of integral separation, that is, when the system error is large, the integral link is cancelled to avoid large overshoot of the system due to integral accumulation; when the system error is small, the integral link is introduced to eliminate the error and improve the control accuracy. This integral separation PID control is applied to the real-time position control of the AC servo system, so that the static and dynamic performance indicators of the control process are more ideal.
2 System Structure Design
The structure of the integral separation PID control AC servo system is shown in Figure 1. In the figure, θd is the given angular displacement, θ is the actual angular displacement of the motor shaft, and e is the deviation obtained by comparing θd and θ. Then:

In Figure 1, u is the expected speed value of PID control; ωd is the expected motor speed; ω is the actual motor speed; the deviation between ωd and ω generates the expected motor electromagnetic torque Td through the speed regulator. Since the deficiency of the inner loop can be compensated by the outer loop control, the speed regulator can use a general PI regulator, and the electromagnetic torque control of the motor adopts the direct torque control method.
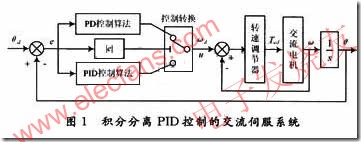
3 Integral separation PID controller
PID control is a mature and widely used control method with a simple structure and good control effect on most processes. The discrete PID control law is:

Where u(k) is the output of the controller at time k; KP, KI, and KD are the proportional coefficient, integral coefficient, and differential coefficient, respectively; e(K) is the difference between the position of the AC servo system at the current moment and the expected value; and e(k-1) is the difference between the position of the AC servo system at the last sampling moment and the expected value.
From formula (2), we can get the increment between the control quantity u(k) at the kth cycle and the control quantity u(k-1) at the k-1th cycle:

In PID control, the role of the integral link is to eliminate static errors and improve the control accuracy of the system. If the integral link is introduced in the initial stage when the error is large, it will cause the integral accumulation of PID, thereby causing a large overshoot of the system. Therefore, this paper designs a control method of integral separation based on the characteristics of PID control. The flowchart of the integral separation PID control algorithm is shown in Figure 2.
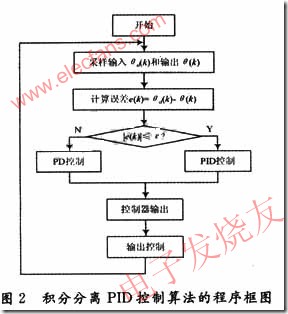
When the system error is large, the integral link is cancelled and PD control is adopted to avoid large overshoot of the system due to integral accumulation; when the system error is small, the integral link is introduced and PID control is adopted to eliminate the error and improve the control accuracy. That is:
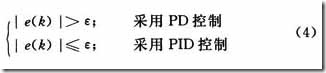
In the formula, ε>0 is an artificially set threshold.
The integral separation control algorithm can be expressed as:

Where T is the sampling time and a is the switching coefficient of the integral term, namely:
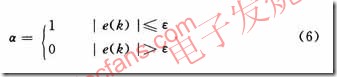
4 Experimental studies
The parameters of the AC motor used in the experiment are Pn=2.2 kW, Un=220 V, In=5 A, nn=1 440 r/min, r1=2.91 Ω, r2=3.04 Ω, Is=0.456 94 H, Ir=0.456 94 H, Im=O.444 27 H, Ten=14 N.
The experiment shows that the integral separation PID control gives full play to the advantages of high regulation accuracy of PID control and improves the control accuracy of the system.
5 Conclusion
This paper proposes an AC servo system based on integral separation PID control. When the system error is large, the integral link is cancelled; when the error is small, the integral link is introduced, so that the static and dynamic performance indicators of the system are more ideal. This control method improves the accuracy of the system. The simulation experimental results show that the controller has good dynamic and static performance and is an effective controller.
Previous article:Phase loss protection of three-phase squirrel cage asynchronous motor
Next article:Principle and Application of Buck PWM Controller APl510
- Popular Resources
- Popular amplifiers
- High signal-to-noise ratio MEMS microphone drives artificial intelligence interaction
- Advantages of using a differential-to-single-ended RF amplifier in a transmit signal chain design
- ON Semiconductor CEO Appears at Munich Electronica Show and Launches Treo Platform
- ON Semiconductor Launches Industry-Leading Analog and Mixed-Signal Platform
- Analog Devices ADAQ7767-1 μModule DAQ Solution for Rapid Development of Precision Data Acquisition Systems Now Available at Mouser
- Domestic high-precision, high-speed ADC chips are on the rise
- Microcontrollers that combine Hi-Fi, intelligence and USB multi-channel features – ushering in a new era of digital audio
- Using capacitive PGA, Naxin Micro launches high-precision multi-channel 24/16-bit Δ-Σ ADC
- Fully Differential Amplifier Provides High Voltage, Low Noise Signals for Precision Data Acquisition Signal Chain
- Innolux's intelligent steer-by-wire solution makes cars smarter and safer
- 8051 MCU - Parity Check
- How to efficiently balance the sensitivity of tactile sensing interfaces
- What should I do if the servo motor shakes? What causes the servo motor to shake quickly?
- 【Brushless Motor】Analysis of three-phase BLDC motor and sharing of two popular development boards
- Midea Industrial Technology's subsidiaries Clou Electronics and Hekang New Energy jointly appeared at the Munich Battery Energy Storage Exhibition and Solar Energy Exhibition
- Guoxin Sichen | Application of ferroelectric memory PB85RS2MC in power battery management, with a capacity of 2M
- Analysis of common faults of frequency converter
- In a head-on competition with Qualcomm, what kind of cockpit products has Intel come up with?
- Dalian Rongke's all-vanadium liquid flow battery energy storage equipment industrialization project has entered the sprint stage before production
- Allegro MicroSystems Introduces Advanced Magnetic and Inductive Position Sensing Solutions at Electronica 2024
- Car key in the left hand, liveness detection radar in the right hand, UWB is imperative for cars!
- After a decade of rapid development, domestic CIS has entered the market
- Aegis Dagger Battery + Thor EM-i Super Hybrid, Geely New Energy has thrown out two "king bombs"
- A brief discussion on functional safety - fault, error, and failure
- In the smart car 2.0 cycle, these core industry chains are facing major opportunities!
- The United States and Japan are developing new batteries. CATL faces challenges? How should China's new energy battery industry respond?
- Murata launches high-precision 6-axis inertial sensor for automobiles
- Ford patents pre-charge alarm to help save costs and respond to emergencies
- New real-time microcontroller system from Texas Instruments enables smarter processing in automotive and industrial applications
- TI MSP430 series microcontroller serial communication baud rate calculation method
- [Atria AT32WB415 Series Bluetooth BLE 5.0 MCU Review] 3.1 MCU generates events and sends commands to Bluetooth APP
- What are the differences in the working principles of military radios and mobile phones? Are their power the same?
- 【Qinheng Trial】Four overall system designs (1/2)——Function integration of ch549 modules
- Share: Solution to BQ40Z80's constant hiccups
- Altium Designer v21.2.0.30
- Pre-registration for the celebrity live show | Arrow-ADI multi-parameter optical water quality analysis platform
- LM2575, DC24V to DC12V, there is a howling sound during debugging?
- Raspberry Pi high-resolution square display PIMORONI HYPERPIXEL 4.0 SQUARES
- Easy-to-use nine-channel RGB LED driver