1 Introduction
When the vehicle drive motor adopts decentralized drive, the motor speed asynchronism may cause the vehicle body to run uncoordinatedly, and then the motor speed may deviate from the normal value, which may cause equipment damage in severe cases. Therefore, it is of practical significance to solve the problem of motor speed asynchronism caused by decentralized drive of vehicle drive motors.
This paper introduces an advanced and practical control method using PLC to solve the motor speed synchronization when the vehicle is decentralized driven.
2 Problem Statement
At present, vehicle operation equipment generally adopts two modes: centralized drive (see Figure 1) and decentralized drive (see Figure 2). The relationship between the centralized drive inverter and the motor is "one to many"; the relationship between the two in decentralized drive is "one to one".
The advantages of "one-to-many" are simple control, easy operation and maintenance, but the centralized drive layout requires a large space in the vehicle body. When the vehicle load is large or the vehicle body space is limited, the "one-to-one" decentralized drive method is usually adopted because of its compact structure and simple layout. However, one-to-one has high requirements for the inverter and motor, especially the synchronization problem is difficult to solve. If the motor speed is inconsistent, the inverter will work in the opposite direction, and the output current will be too large to cause tripping, affecting the working efficiency of the vehicle and the service life of the electrical equipment. If the speed deviation is too large, it will cause the vehicle body to deform, affecting the use.
3 Solutions
The PLC and inverter control method is adopted to realize the synchronous operation of multiple decentralized drive motors. The PLC adopts Siemens S7400 series. Figure 3 is the network topology diagram.
In order to achieve the speed synchronization of the two traction motors, two variable frequency motors are used for traction, and the frequency converter speed is respectively used for vector closed loop control, and the two frequency converters are directly controlled by PLC. In the control, the PLC and the frequency converter are connected by Profibus to ensure the synchronization of the output signal source. The speed of traction motor 1 is taken as the target speed, and the frequency converter of traction motor 2 adjusts its speed to track the speed of traction motor 1. Two incremental rotary encoders are coaxially connected to the motor, so that encoder 1 and encoder 2 respectively collect the speed pulse signals of the two motors and send the signals to the high-speed counting module of PLC. PLC uses these two speed signal data as input control quantity to perform proportional integral control operation (PID), and the operation result is sent to the analog module of PLC as the output signal to control the frequency converter of traction motor 2. In this way, it can be ensured that the speed of traction motor 2 tracks and changes with the change of the speed of traction motor 1. Keep the two speeds synchronized.
The pulse signal collected by the encoder enters the PLC through the high-speed counting module FM350-1 and is converted into motor speed data. The signals of the two motor encoders are compared, and the motor speed difference is adjusted through the PID adjustment module to give the speed value of motor 2 MW1000.
MW1000 needs to be converted into a signal that the inverter can accept. Since the corresponding 4-20mA value of PLC is 0-27648, and the inverter receiving range value is 0-8192, MW1000/27648×8192 is sent to the analog output channel and converted into a current signal that the inverter can accept to control the inverter of traction motor 2. The PID algorithm is the most commonly used mathematical algorithm in industrial control. Its basic formula is as follows:
Pou (tt) = Kp × (et) + Ki × Σ (et) + Kd × [ (et) - (et-1) ]
In the formula: Kp is the proportional adjustment coefficient. It reflects the deviation of the system in proportion. Once the system has a deviation, the proportional adjustment will immediately take effect to reduce the error.
Ki —Integral adjustment coefficient. It enables the system to eliminate steady-state errors and improve the degree of non-difference. The strength of the integral action depends on the integral time. The smaller the constant Ti is, the stronger the integral action is. Kd —Differential adjustment coefficient. The differential action reflects the rate of change of the system deviation signal. It is predictive and can predict the trend of deviation change. Therefore, it can produce advanced control effects. Before the deviation is formed, it has been eliminated by the differential adjustment action. In order to reduce external interference caused by factors such as power system fluctuations, when compiling the control algorithm, it is necessary to consider the use of integral links, that is, using a continuous and stable input signal over a period of time instead of a certain instantaneous value input signal for PID operation to eliminate cumulative errors and make the number of revolutions adjustable within a certain range. In this way, traction motor 1 and traction motor 2 can be well synchronized and controlled with high synchronization accuracy, thereby ensuring the stability of the operating mechanism.
4 Control results
The PLC host computer monitoring program is compiled using STEP7, and Wincc collects speed values and draws curves. The time interval for data extraction is 15ms. In fact, the speeds of traction motor 1 and traction motor 2 are the same, but in order to reflect the tracking and fluctuation of traction motor 2, they are specially separated here. The upper one is the speed curve of traction motor 1, and the lower one is the speed curve of traction motor 2 (see Figure 4). When the speed of traction motor 1 changes, traction motor 2 can respond in time, track, and quickly reach stability. Experiments show that the control method using PLC and inverter can meet higher synchronization requirements, fast response, and small speed fluctuation.
5 Conclusion
This control method has been applied in various furnace vehicles. In actual application, the synchronous start effect is obvious and the vehicle runs smoothly. Practice has proved that the control method of using PLC to solve the motor speed synchronization when the vehicle is decentralized driven has a good application effect. It is an ideal speed control method, which meets the production process requirements, reduces the maintenance cost of equipment, ensures the normal production efficiency of the vehicle, and has significant economic benefits. With the widespread application of PLC and inverter control methods, the reliability and flexibility of the transmission system for speed control will be better improved.
Previous article:Application of SVF3000 inverter in double frequency wire drawing machine
Next article:Metallographic cutting machine control system based on touch screen and PLC
Recommended ReadingLatest update time:2024-11-16 22:50
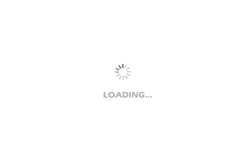
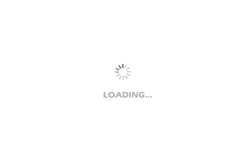
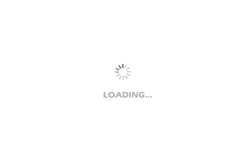
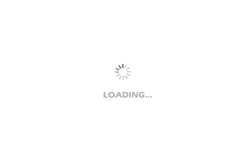
- Popular Resources
- Popular amplifiers
- Molex leverages SAP solutions to drive smart supply chain collaboration
- Pickering Launches New Future-Proof PXIe Single-Slot Controller for High-Performance Test and Measurement Applications
- CGD and Qorvo to jointly revolutionize motor control solutions
- Advanced gameplay, Harting takes your PCB board connection to a new level!
- Nidec Intelligent Motion is the first to launch an electric clutch ECU for two-wheeled vehicles
- Bosch and Tsinghua University renew cooperation agreement on artificial intelligence research to jointly promote the development of artificial intelligence in the industrial field
- GigaDevice unveils new MCU products, deeply unlocking industrial application scenarios with diversified products and solutions
- Advantech: Investing in Edge AI Innovation to Drive an Intelligent Future
- CGD and QORVO will revolutionize motor control solutions
- Innolux's intelligent steer-by-wire solution makes cars smarter and safer
- 8051 MCU - Parity Check
- How to efficiently balance the sensitivity of tactile sensing interfaces
- What should I do if the servo motor shakes? What causes the servo motor to shake quickly?
- 【Brushless Motor】Analysis of three-phase BLDC motor and sharing of two popular development boards
- Midea Industrial Technology's subsidiaries Clou Electronics and Hekang New Energy jointly appeared at the Munich Battery Energy Storage Exhibition and Solar Energy Exhibition
- Guoxin Sichen | Application of ferroelectric memory PB85RS2MC in power battery management, with a capacity of 2M
- Analysis of common faults of frequency converter
- In a head-on competition with Qualcomm, what kind of cockpit products has Intel come up with?
- Dalian Rongke's all-vanadium liquid flow battery energy storage equipment industrialization project has entered the sprint stage before production
- Allegro MicroSystems Introduces Advanced Magnetic and Inductive Position Sensing Solutions at Electronica 2024
- Car key in the left hand, liveness detection radar in the right hand, UWB is imperative for cars!
- After a decade of rapid development, domestic CIS has entered the market
- Aegis Dagger Battery + Thor EM-i Super Hybrid, Geely New Energy has thrown out two "king bombs"
- A brief discussion on functional safety - fault, error, and failure
- In the smart car 2.0 cycle, these core industry chains are facing major opportunities!
- The United States and Japan are developing new batteries. CATL faces challenges? How should China's new energy battery industry respond?
- Murata launches high-precision 6-axis inertial sensor for automobiles
- Ford patents pre-charge alarm to help save costs and respond to emergencies
- New real-time microcontroller system from Texas Instruments enables smarter processing in automotive and industrial applications
- LTC3105 will not start
- Huawei is so poor that it has no money to buy keyboards and mice? Do you bring your own office supplies?
- [Evaluation of EC-01F-Kit, the NB-IoT development board of Essence] + Unboxing
- Review summary: BearPi-HM Micro foldable development board
- NeoPixel Infinity Cube
- [STM32F769Discovery development board trial] Discussion and application of DMA2D screen refresh efficiency
- Compilation of TI DM8148 multi-core DSP SDK
- Thank you for being here + my proactive change
- Using Energia to develop MSP430F5529LP under Windows 10 Basic process and problems encountered
- Wi-Fi 6E has been launched. What is the difference between it and ordinary Wi-Fi?