DSP (digital signal processor) is a unique microprocessor that processes large amounts of information using digital signals. Its working principle is to receive analog signals and convert them into digital signals of 0 or 1. It then modifies, deletes, and strengthens the digital signals, and interprets the digital data back into analog data or actual environment formats in other system chips. It is not only programmable, but its real-time running speed can reach tens of millions of complex instruction programs per second, far exceeding general-purpose microprocessors. It is an increasingly important computer chip in the digital electronic world. Its powerful data processing capabilities and high operating speed are the two most commendable features.
Ice and snow accumulation are constant threats to the safe operation of power and communication networks [1-4]. The de-icing robot is an automated device for removing ice from transmission lines. The robot needs to perform servo control on multiple motors, such as the walking motor, joint motor, and clamping and tightening motor. The types and number of motors are relatively large, so the robot control system is relatively complex. This paper mainly studies the servo control of the walking motor of the de-icing robot. The walking motor needs to drive the robot to walk on the line. When the line is heavily covered with ice, it needs to drive the de-icing blade to complete the ice breaking work. When the robot encounters a thick ice layer and cannot move forward continuously during operation, it automatically completes the back movement, accelerates forward, and performs intermittent de-icing.
The walking motor servo control adopts a fully digital brushless DC motor control system with the motor control dedicated chip TMS320LF2407 as the core. The use of a fully digital control method can effectively avoid the interference of unstable factors in analog control. Since the robot works in a strong electromagnetic environment, the fully digital control method can effectively avoid electromagnetic interference. Since the brushless DC motor has a series of advantages of AC motors such as simple structure and reliable operation, and has the advantages of DC motors such as high speed, high efficiency, and high dynamic response, the system chooses a brushless DC motor as the robot axis drive [5].
1 Overall structure design of control system
By analyzing the motion equation of the DC motor, we know that the motor acceleration is proportional to its torque, and the torque is proportional to its current. Therefore, to achieve high-precision and high-dynamic performance control of the motor, it is necessary to detect and control the motor speed, current and position at the same time. The system includes position detection and current detection links, which detect the speed and current of the motor respectively. The hardware circuit of the system mainly includes DSP system, power drive circuit, isolation circuit, position detection circuit and current detection circuit. The structural principle of the system is shown in Figure 1.
Digital Signal Processing (DSP) is an emerging discipline that involves many disciplines and is widely used in many fields. Since the 1960s, with the rapid development of computer and information technology, digital signal processing technology has emerged and developed rapidly. Digital signal processing is a method of processing real signals represented by digital sequences by using mathematical techniques to perform conversions or extract information. In the past two decades, digital signal processing has been widely used in fields such as communications. Semiconductor manufacturers such as Texas Instruments and Freescale have strong strength in this field.
2-speed closed loop control
The deviation is formed according to the input set value and feedback amount, and the control amount of PWM duty cycle is formed through a series of digital adjustments, thereby controlling the rotation speed or speed change of the servo motor.
The speed closed-loop control is mainly responsible for the robot's walking speed and speed change control during deicing. Figure 2 shows the brushless DC motor speed and current dual closed-loop control system. When the BLDCM forms a speed closed-loop control, the motor's rotation direction and angle are detected by the photoelectric encoder and fed back to the DSP system.
in,
is the time constant of the first-order inertia link
is the back electromotive force constant of the motor under rated excitation; K1 and K2 are the proportional coefficients of current and speed feedback respectively; K3=R is the phase resistance of the motor; υg is the given speed of the motor; υs is the feedback speed of the motor; ig is the output of the speed regulator, that is, the given current value; if is the feedback current; ie is the current error signal; Uc is the PWM control signal; Ud is the DC terminal voltage of the motor; E is the amplitude of the back electromotive force of the motor; id is the phase current of the motor; and n is the actual speed of the motor.
3 System Hardware Design
3.1 Phase current detection
Since the power electronic main circuit adopts the two-by-two energization mode, the current only flows into two phases of the three-phase winding at any time, so only one phase current detection sensor is needed to complete the phase current detection. A bypass resistor is used to detect the current of each phase. The resistor is located between the lower power bridge arm and the ground of the three-phase full-controlled power conversion circuit, and also serves as an overcurrent protection. After the voltage drop signal on the resistor is amplified, it is sent to the A/D conversion channel on the TMS320F240 7 chip, and the appropriate current signal is obtained through A/D conversion. After the A/D conversion is completed, the A/D conversion module will send an interrupt request signal to the CPU, waiting for the CPU to detect the current signal. Finally, according to the current error, the duty cycle of the PWM pulse is adjusted at the beginning of each PWM cycle [6].
3.2 Rotor position and speed detection
TMS320LF2407A is selected to realize the control and drive circuit of three-phase brushless DC motor speed regulation. Three Hall sensors with 120° intervals are used. The rotor position signal output by the Hall device is sent to the power conversion circuit and then directly to the capture unit of TMS320LF2407A for processing. By detecting the status of the three capture ports, the combined status of the current three position signals can be obtained, thereby obtaining the rotor position. Each jump captured by the capture ports CAP1~CAP3 triggers a capture interrupt, and 6 capture interrupts are generated for each rotation of the rotor. The motor speed is obtained by measuring the time interval between two adjacent interrupts.
3.3 Driving Circuit Design
The motor control driver uses the IR2130 chip. The IR2130 chip controls the on and off sequence of the six power tubes to control the forward and reverse rotation of the motor. This driver chip itself provides overvoltage protection for the power devices. It contains a logic protection circuit. When the level-through logic appears, the chip immediately outputs a low level and turns off all MOSFET tubes. In addition, there is a detection resistor in the power circuit protection device. When the current is too large, the detection signal is logically judged and PDPINT is set to a low level. The internal counter of the DSP stops counting, and all PWM outputs are low, turning off the drive circuit to achieve overcurrent protection [7].
4 System software design
The main program mainly completes DSP initialization, and the flowchart is shown in Figure 3. The A/D conversion interrupt subroutine completes the speed and current adjustment, and the flowchart is shown in Figure 4. The experimental clock frequency is 20 MHz and the PWM frequency is 20 kHz. The A/D conversion is started by the timer 1 cycle match event, so that the current is sampled once in each PWM cycle, and the current is adjusted in the A/D conversion interrupt handler to control the PWM output. The capture interrupt program completes the counting of the position quantity and the calculation of the speed reference quantity. The program flowchart is shown in Figure 5. Every time the rotor rotates 60°, a capture interrupt is triggered to perform phase switching and speed calculation [8].
This paper uses TI's TMS320LF2407A DSP to design a DC brushless motor control system for ice-covering robots when walking and deicing. After analysis, the system is not only low-cost and easy to implement, but also has stable performance and convenient expansion, which is of great significance to engineering practice and motor speed regulation.
Previous article:DSP video processing via open source API
Next article:Application of Fuzzy PID Control in DMF Recovery Control System
Recommended ReadingLatest update time:2024-11-16 22:46
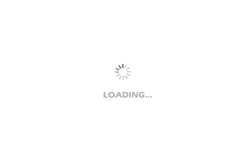
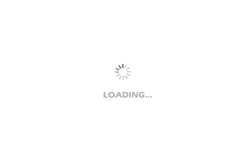
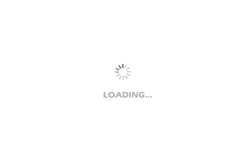
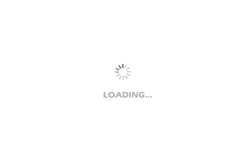
- Popular Resources
- Popular amplifiers
- Molex leverages SAP solutions to drive smart supply chain collaboration
- Pickering Launches New Future-Proof PXIe Single-Slot Controller for High-Performance Test and Measurement Applications
- CGD and Qorvo to jointly revolutionize motor control solutions
- Advanced gameplay, Harting takes your PCB board connection to a new level!
- Nidec Intelligent Motion is the first to launch an electric clutch ECU for two-wheeled vehicles
- Bosch and Tsinghua University renew cooperation agreement on artificial intelligence research to jointly promote the development of artificial intelligence in the industrial field
- GigaDevice unveils new MCU products, deeply unlocking industrial application scenarios with diversified products and solutions
- Advantech: Investing in Edge AI Innovation to Drive an Intelligent Future
- CGD and QORVO will revolutionize motor control solutions
- Innolux's intelligent steer-by-wire solution makes cars smarter and safer
- 8051 MCU - Parity Check
- How to efficiently balance the sensitivity of tactile sensing interfaces
- What should I do if the servo motor shakes? What causes the servo motor to shake quickly?
- 【Brushless Motor】Analysis of three-phase BLDC motor and sharing of two popular development boards
- Midea Industrial Technology's subsidiaries Clou Electronics and Hekang New Energy jointly appeared at the Munich Battery Energy Storage Exhibition and Solar Energy Exhibition
- Guoxin Sichen | Application of ferroelectric memory PB85RS2MC in power battery management, with a capacity of 2M
- Analysis of common faults of frequency converter
- In a head-on competition with Qualcomm, what kind of cockpit products has Intel come up with?
- Dalian Rongke's all-vanadium liquid flow battery energy storage equipment industrialization project has entered the sprint stage before production
- Allegro MicroSystems Introduces Advanced Magnetic and Inductive Position Sensing Solutions at Electronica 2024
- Car key in the left hand, liveness detection radar in the right hand, UWB is imperative for cars!
- After a decade of rapid development, domestic CIS has entered the market
- Aegis Dagger Battery + Thor EM-i Super Hybrid, Geely New Energy has thrown out two "king bombs"
- A brief discussion on functional safety - fault, error, and failure
- In the smart car 2.0 cycle, these core industry chains are facing major opportunities!
- The United States and Japan are developing new batteries. CATL faces challenges? How should China's new energy battery industry respond?
- Murata launches high-precision 6-axis inertial sensor for automobiles
- Ford patents pre-charge alarm to help save costs and respond to emergencies
- New real-time microcontroller system from Texas Instruments enables smarter processing in automotive and industrial applications
- Filter Design——FilterSolutions
- Android driver learning 1-driver development process (Android.mk)
- Asking for advice: Question about TMS320C5509A low power mode
- Based on PSOC6 development board simulation I2C solution X-NUCLEO-IKS01A3's STTS751;
- Apply for VICOR DCM DC-DC converter module related evaluation board for free!
- MATLAB offline seminar | Assisting the development of artificial intelligence and electronic products (March 30, Nanjing)
- Dear seniors, please help me choose a chip
- [EasyARM-RT1052 Review] + Serial port idle reception to implement modbus host
- The significance of choosing high current spring micro-needle module for mobile phone connector testing
- Using debug macro definition to turn on/off debug output in C/C++