The battery is the main power source of electric vehicles. In order to ensure the normal and safe driving of electric vehicles, the battery management system must monitor the voltage data of the electric vehicle battery in real time. The voltage data is obtained through the voltage acquisition circuit and A/D conversion. In order to avoid safety problems caused by local overcharge/overdischarge caused by battery imbalance, the monitoring system is required to accurately measure the voltage of each cell or several cells. If the traditional multi-channel voltage collection method is used, when the number of battery cells is large, the design and implementation of the entire management system will have shortcomings such as high cost and poor consistency. This paper designs a novel multi-channel voltage acquisition circuit based on lead-acid batteries for electric vehicles.
Hardware structure of voltage inspection in battery monitoring system
Generally, electric vehicles are equipped with 10 to 30 batteries, and the single (module) voltage range is 3 to 20V. When the batteries are used in series, the battery terminal voltage will reach more than 200V.
Figure 1 Voltage acquisition method of battery management system using circuit gating loop
Figure 2 Part of the voltage signal conditioning circuit
This article proposes a design idea as shown in Figure 1. The design uses a shift switch circuit to sequentially select the circuit under test, and collects single-channel data through A/D to complete data collection. This design method has the following advantages:
1. The circuit is simple. Simplify the process of making PCB boards and wiring.
2. Fewer devices are used and the cost is low. The main cost in the acquisition circuit comes from the ADC, and this circuit only requires one ADC.
3. It can solve the problem of poor consistency caused by uneven parameters of chips such as operational amplifiers.
Acquisition circuit description:
The acquisition object is lead-acid batteries for electric vehicles, which requires real-time voltage, current and temperature monitoring of the 26-cell battery module. The voltage range of the measurement module is 8V~20V, and the batteries are connected in series. According to the design idea in Figure 1, the inspection circuit is used to manage the collection of voltage data.
Circuit Overview
The signal inspection part of the circuit is shown in Figure 2. The circuit has a total of 26 inputs, of which only two are shown in Figure 2.
In the circuit, U 1 ~ U 3 are the input terminals of the voltage signal of the series module.The potential gradually decreases from U 1 to U 3. There is a battery module (12V) between each two adjacent input terminals. After the voltage signal passes through this circuit, it is connected to the subsequent voltage dividing circuit and ADC. C 1 ~ C 2 are control signals. When the control signal is '0', the optocoupler P521 is in a closed state, causing the PNP and NPN transistors to be in a closed state. At this time, the channel for the voltage signal output to the ADC is closed; when the control signal is ' 1', the optocoupler is turned on, and the bases of the PNP and NPN transistors in the circuit generate reverse voltages. At this time, the base current I b of the transistor in the circuit is: Referring to the data in the circuit in Figure 2, the current I ce
of the emitter and collector of the circuit can be obtained: Since I b · β >>I ce , so the PNP in the input circuit and the NPN transistor is in saturation. The channel for outputting the voltage signal to the ADC is opened to realize the gating of the module voltage data. In this design, there are 26 channels in total, and the selection of acquisition signal transmission is realized through 26 signal controls. This design uses Xilinx's CPLD chip XC9572 to control the high and low levels of the signal, so that the 26 control signals are in the signal '1' state in sequence. Whenever one circuit is turned on, the other circuits are in a closed state to realize the on/off control of the circuit. After the voltage signal is output from U OUT , it is passed through a 20V bidirectional transient diode to remove burrs and then connected to the voltage divider circuit. The output of the voltage divider circuit is directly connected to the ADC to complete the sampling of the signal. The output of the CPLD and the sampling period of the system are controlled by the microcontroller, and the data is sampled 2ms after the CPLD turns on each control signal.
Acquisition circuit simulation and analysis
In actual application, the following problems will occur:
4-channel 9V battery module is connected, and the circuit works normally. Connect 26 16V battery modules to the circuit in sequence, totaling 400V. When connected to No. 22, the triode is broken down.
Use Electronics Workbench simulation software to analyze the circuit through circuit simulation. The analysis is mainly carried out in two steps. First, the cause of the spike during the single-channel conduction process is analyzed, and then the spike process during the continuous conduction of the entire circuit is analyzed.
Single-channel simulation
The single-channel simulation model is shown in Figure 3.
Figure 3 Single-channel simulation model
There is a small peak on the rising edge and falling edge of each square wave of the simulated waveform. After amplifying the waveform, the peak value of the peak is 500mV. Analysis of the causes of spikes includes the following two points:
1. The influence of inductive components in the circuit.
Generally, the wires in the circuit are inductive. When changes occur, the inductive components in the circuit will generate induced electromotive force, which may cause spikes in the circuit. Build a model as shown in Figure 3, and analyze the impact of inductive components on the circuit by changing the inductive reactance of the inductor.
Through simulation, it can be found that the peak value of the circuit with an inductive reactance of 4.7 mH is 500mV, while the peak value of the circuit with an inductive reactance of 100 mH is about 3V. By conducting multiple sets of simulations, it can be obtained that the greater the inductance reactance in the circuit, the higher the peak value of the peak.
2. Influence of the switching time characteristics of the triodes.
There are two triodes, PNP and NPN, in each circuit, and the difference in the conduction time of the triodes also affects the generation of spikes.
As shown in Figure 4, analyze the conduction process of two transistors in a single circuit. When the conduction time of the two transistors is different, if one transistor is in the conductive state and the other is not yet conductive, at this time, one end of U OUT and GND is at the same potential as the input voltage (U 1 or U 2 ) due to the conduction of the transistor. The same, while the other end is in an unknown level state because the transistor is not conducting. If this unknown level is less than the input low level, a spike may occur at the moment the transistor is conducting. The same is true when both transistors are turned off.
In the model built in Figure 3, observe the waveform at both ends of the NPN transistor in the loop. When the NPN transistor is turned off, there is a -250mV voltage drop across the ce poles of the triode, and when the triode is turned on, there is a 250mV voltage drop between the ce poles. It can be seen from this that in Figure 4, there is a voltage drop of 250mV between point B and GND when the transistor is turned off. Therefore, when Q 1 is turned on and Q 2 is not turned on, the voltage ratio between U OUT and GND is between U 1 and U 2. The voltage is 250mV higher. Through the above analysis, when Q2 is turned on, a 250mV spike will be generated.
For a single circuit, the value affected by the transistor switching characteristics is a fixed value, which is 0.25V. As can be seen in Figure 4, when the inductor reactance is 100mH, the peak value of the circuit is 3V. It can be seen that the inductive components in the circuit have a dominant influence on the circuit.
Multi-channel simulation
The multi-channel simulation model is shown in Figure 5.
Figure 4 Conducting
circuit Figure 5 Multi-channel simulation model
The model has a total of 4 channels, each with a voltage of 12V. A current switch is used to control the gating of the acquisition channel, and the control circuit is a 74LS138 chip select chip. The three input terminals of the chip select are pulse signals with frequencies of 1000Hz, 500Hz and 250Hz. In this way, low-level signals are generated from Y 0 to Y 7 at the output terminal . The model selects 4 of them as control signals for the current switch.
When the first channel of the model is turned on, the output waveform has a relatively obvious peak (the peak value is about 10V). When other channels are turned on, the peak value of the output waveform is relatively small (the peak value is about 1V). From the single-channel simulation, it can be seen that the peak caused by inductive reactance in the circuit generally does not reach 10V.
Observe the waveform on the first PNP tube, see Figure 6. In the figure, the lower curve is the waveform of the c pole (the waveform at point B in Figure 7), and the upper curve is the waveform of the e pole (the waveform at point A in Figure 7). As can be seen from the figure, when all four transistors are turned off, the voltage at output point B is about 24V lower than input point A, that is, the voltage at point D is about 24V lower than point A (when the triodes are turned off, the voltage at point B and D The voltages are the same, see Figure 6). When the conduction time of the PNP tube is shorter than that of the NPN tube, the voltage at point A before the path is opened in Figure 7 is about 24V higher than that of point D. When the PNP tube is turned on and the NPN tube is not turned on, the voltage drop of the output circuit UBD is 24V, and when the NPN tube is turned on to form a loop, the output voltage drop is required to drop to the voltage value at both ends of the battery input, that is, 12V. At this time, the output loop reaches the requirement after discharge, and a spike occurs at the moment when the first channel is turned on.
Since the circuits are turned on sequentially, when the previous circuit is turned off, the potential at the output end is maintained at the state before it was turned off, thus preventing excessive spikes. The generation of small spikes is mainly caused by circuit inductance.
When there are many input channels, when all loops are closed, the output loop is at an unknown level. When the triode switching time characteristics are different, a spike will appear in the output waveform at the moment of conduction. The higher the potential of the end corresponding to the PNP tube in the input circuit, the higher the output spike.
Next, measure the waveform of the actual circuit. First, connect about 6 16V battery packs, and use an oscilloscope to observe the voltage between U OUT and the ground wire in the output loop. When the first battery pack is turned on, a peak appears at the left end of the output level. The actual waveform is consistent with the analysis, and the simulation model is valid.
Improvement plan and the accuracy of the improved circuit measurement data
. According to the simulation results, it is determined that there are two main reasons for problems
in the circuit: 1. The influence of inductive components in the loop;
2. The influence of the switching characteristics of the triode, which is the main reason.
Improvement plan based on the analysis results
In the design of this system, the following improvement measures have been taken:
1. Parallel capacitor
In order to eliminate the influence of the inductance on the circuit, capacitors are connected in parallel at both ends of the output loop. The parallel capacitance is basically proportional to the inductance of the loop, making the circuit purely resistive.
2. Series current-limiting resistor:
A series-connected current-limiting resistor in each pair of transistor and diode can protect the transistor from breakdown due to overcurrent. At the same time, because the current limiting resistor also has a voltage dividing effect, the voltage on the transient diode is further reduced, making the transient diode less likely to be broken down.
Figure 6 Waveforms at both ends of the 1st PNP transistor
Figure 7 Simulation model of the 1st channel
Improved circuit
By adding a current-limiting resistor in series to the circuit, the safety of the circuit is guaranteed. However, the consistency and linearity of the circuit require further testing.
Consistency
Measurement The main problem in measuring consistency is the error in the resistance values of the series current-limiting resistors in the circuit. The current limiting resistor in series in the circuit is 20k and the error is 1%. Input the voltage to be measured at 9V and 16V respectively, and connect to 26 input terminals respectively. The measurement data obtained are not detailed here.
It can be seen from the data that the measurement results of channels 22, 23, 25 and 26 are relatively small, with a maximum measurement error of 1.25%, and the measurement consistency is good.
Linear measurement
Since nonlinear components such as transistors are used in the circuit, the linearity of the measurement needs to be verified. During verification, a channel is randomly selected, the input voltage is between 2.0V and 20.0V, and the data is measured every 1V. The measurement data are not detailed here.
It can be seen from the data that when the input voltage is below 5V, the measurement data is unreliable. When the input voltage is higher than 5V, the measured data has a basically linear relationship with the input voltage. Since this system is mainly used for the measurement of nickel-metal hydride batteries, the module voltage is about 12V, and the circuit can meet the measurement requirements.
Conclusion:
This article proposes a design method for the multi-channel voltage acquisition circuit commonly used in A/D sampling and measurement circuits. In view of the problems that arise during the use of the circuit, a model simulation circuit is built using the Electronics Workbench circuit simulation software, and a method for improving the circuit is proposed. After verification, the consistency and linearity of the circuit are good, and it also has the advantages of simple circuit and fewer components.
Previous article:High Power Design Analysis for Power over Ethernet
Next article:TinySwitchⅡ and its application in standby power supply
Recommended ReadingLatest update time:2024-11-16 19:43
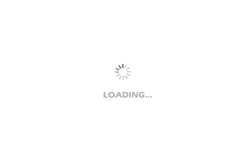
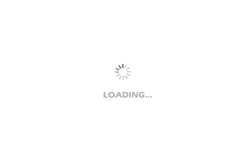
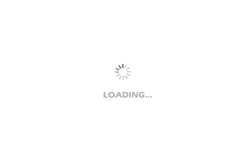
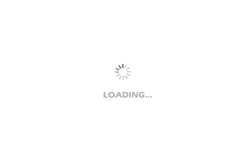
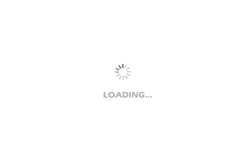
- Popular Resources
- Popular amplifiers
-
Microgrid Stability Analysis and Control Microgrid Modeling Stability Analysis and Control to Improve Power Distribution and Power Flow Control (
-
Modern Electronic Technology Training Course (Edited by Yao Youfeng)
-
New Energy Vehicle Control System Inspection and Maintenance (Edited by Bao Pili)
-
Intelligent Control Technology of Permanent Magnet Synchronous Motor (Written by Wang Jun)
- MathWorks and NXP Collaborate to Launch Model-Based Design Toolbox for Battery Management Systems
- STMicroelectronics' advanced galvanically isolated gate driver STGAP3S provides flexible protection for IGBTs and SiC MOSFETs
- New diaphragm-free solid-state lithium battery technology is launched: the distance between the positive and negative electrodes is less than 0.000001 meters
- [“Source” Observe the Autumn Series] Application and testing of the next generation of semiconductor gallium oxide device photodetectors
- 采用自主设计封装,绝缘电阻显著提高!ROHM开发出更高电压xEV系统的SiC肖特基势垒二极管
- Will GaN replace SiC? PI's disruptive 1700V InnoMux2 is here to demonstrate
- From Isolation to the Third and a Half Generation: Understanding Naxinwei's Gate Driver IC in One Article
- The appeal of 48 V technology: importance, benefits and key factors in system-level applications
- Important breakthrough in recycling of used lithium-ion batteries
- Innolux's intelligent steer-by-wire solution makes cars smarter and safer
- 8051 MCU - Parity Check
- How to efficiently balance the sensitivity of tactile sensing interfaces
- What should I do if the servo motor shakes? What causes the servo motor to shake quickly?
- 【Brushless Motor】Analysis of three-phase BLDC motor and sharing of two popular development boards
- Midea Industrial Technology's subsidiaries Clou Electronics and Hekang New Energy jointly appeared at the Munich Battery Energy Storage Exhibition and Solar Energy Exhibition
- Guoxin Sichen | Application of ferroelectric memory PB85RS2MC in power battery management, with a capacity of 2M
- Analysis of common faults of frequency converter
- In a head-on competition with Qualcomm, what kind of cockpit products has Intel come up with?
- Dalian Rongke's all-vanadium liquid flow battery energy storage equipment industrialization project has entered the sprint stage before production
- Allegro MicroSystems Introduces Advanced Magnetic and Inductive Position Sensing Solutions at Electronica 2024
- Car key in the left hand, liveness detection radar in the right hand, UWB is imperative for cars!
- After a decade of rapid development, domestic CIS has entered the market
- Aegis Dagger Battery + Thor EM-i Super Hybrid, Geely New Energy has thrown out two "king bombs"
- A brief discussion on functional safety - fault, error, and failure
- In the smart car 2.0 cycle, these core industry chains are facing major opportunities!
- The United States and Japan are developing new batteries. CATL faces challenges? How should China's new energy battery industry respond?
- Murata launches high-precision 6-axis inertial sensor for automobiles
- Ford patents pre-charge alarm to help save costs and respond to emergencies
- New real-time microcontroller system from Texas Instruments enables smarter processing in automotive and industrial applications
- TCP/IP Detailed Explanation (Layer 7/Layer 4 Protocol)
- FPGA Selection Strategy.pdf
- Medical device requirements for chip temperature
- Send Chip Coins: #What to do when you encounter problems with Guoxin#, technical support is rubbed on the ground?
- 【RPi PICO】MicroPython firmware with encryption support
- I want to use a 3.3v microcontroller to share power to control a relay, but the microcontroller stops working after grounding.
- Welfare is coming! The recommended chip list for the TI Cup is freshly released!
- Based on RT-Thread open source works show - rice field environmental information monitoring system
- A brief introduction and configuration of 28335 external interrupt
- Analyze the relationship between J-link hardware, firmware, and drivers