The single-electrode chip has very high requirements for die bonding in the packaging industry. For example, in the LED production process, the quality of die bonding affects the quality of the LED finished product. There are many factors that cause LED die bonding cracks. We only discuss the solutions to LED die bonding cracks from three aspects: materials, machines, and human factors.
1. The chip material itself is cracked
When the chip damage is greater than 1/5 of the width of a single side chip or the damage is at an oblique angle, the length of each single side is greater than 2/5 of the chip or the damage reaches the aluminum pad, such chips are unacceptable (this is one of the items in the chip inspection standard). The main reasons for the adverse phenomenon are:
1. Improper operation of chip manufacturers
2. The chip incoming material inspection was not carried out
3. Not selected during online operation
Solution:
1. Notify chip manufacturers to make improvements
2 Strengthen incoming material inspection and reject chips with too many damaged chips.
3. During the online Q inspection, the damaged chips should be picked out and replaced with good chips.
2. Improper use of LED die bonding machine
1. Improper machine suction parameters
The suction nozzle height and the height of the die bonding are directly controlled by the parameters in the machine computer. If the parameters are large, the suction height is small; if the parameters are small, the suction height is large. Whether the chip is damaged or not is directly affected by the suction height parameters of the machine. The main reasons for the bad phenomenon are: the machine parameters are large, the suction height is low, and the chip is subjected to excessive force, resulting in chip damage.
Solution:
Adjust the machine parameters, appropriately increase the height of the suction nozzle or the height of the bonding die. In the "SETUP" mode of the machine, in the "Bond head menu" in the first item "Pick Level" adjust the suction nozzle height, and then adjust the bonding die height in the second item "Bond Level".
2. The nozzle size does not match
Different sizes of chips require different nozzles for die bonding. If a large chip is used with a small nozzle, the chip cannot be sucked up and is prone to leakage; if a small chip is used with a large nozzle, the chip is easy to break. Therefore, choosing an appropriate nozzle is the premise for good chip bonding. The reason for the bad phenomenon is: the nozzle is too large and breaks the chip.
Solution: Choose the appropriate porcelain nozzle.
3. Cracks caused by improper human operation
A. Improper operation
Failure to follow the specified operation may result in chip damage. The main reasons for the adverse phenomenon are:
1. The materials were not held properly and fell to the ground.
2. Touch the chip when entering the oven
Solution: Hold the ingredients steady. Place the ingredients flat and gently into the oven without tilting or applying excessive force.
B. Heavy objects crushing
The chip is broken due to excessive external force. The main reasons for this phenomenon are:
1. The microscope fell onto the material, breaking the chip
2. Machine parts fall onto the material.
3. The iron plate presses the material
Solution:
1. Tighten the microscope screws
2. Check machine parts regularly to see if they are loose.
3. No objects such as iron plates can pass over the material.
Previous article:How to choose cooling equipment for LED display in summer?
Next article:Outdoor LED display screen - give a thumbs up to the communication effect
Recommended ReadingLatest update time:2024-11-22 20:25
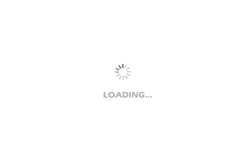
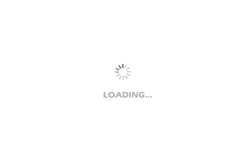
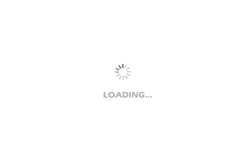
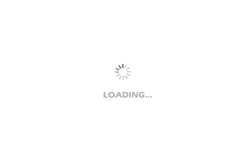
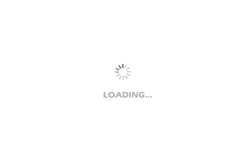
- Popular Resources
- Popular amplifiers
- RAQ #223: How to measure and determine soft-start timing without a soft-start equation?
- Vicor high-performance power modules enable the development of low-altitude avionics and EVTOL
- Bourns Launches Two Thick Film Resistor Series with High Power Dissipation Capabilities in Compact TO-220 and DPAK Package Designs
- Bourns Launches New High-Pulse Brake Resistor Series with Superior Energy Dissipation Capabilities
- Nexperia launches new 120 V/4 A half-bridge gate driver to further improve robustness and efficiency in industrial and automotive applications
- Vishay's New 150 V MOSFETs Offer Industry-Leading Power Loss Performance
- The first generation of SGT MOSFET series from Qiangmao: innovative trench technology, automotive-grade 60 VN channel, breakthrough in high-efficiency performance of automotive electronics
- DC/DC Power Supplies for Automotive Applications
- MathWorks and NXP Collaborate to Launch Model-Based Design Toolbox for Battery Management Systems
- Intel promotes AI with multi-dimensional efforts in technology, application, and ecology
- ChinaJoy Qualcomm Snapdragon Theme Pavilion takes you to experience the new changes in digital entertainment in the 5G era
- Infineon's latest generation IGBT technology platform enables precise control of speed and position
- Two test methods for LED lighting life
- Don't Let Lightning Induced Surges Scare You
- Application of brushless motor controller ML4425/4426
- Easy identification of LED power supply quality
- World's first integrated photovoltaic solar system completed in Israel
- Sliding window mean filter for avr microcontroller AD conversion
- What does call mean in the detailed explanation of ABB robot programming instructions?
- 2024 China Automotive Charging and Battery Swapping Ecosystem Conference held in Taiyuan
- State-owned enterprises team up to invest in solid-state battery giant
- The evolution of electronic and electrical architecture is accelerating
- The first! National Automotive Chip Quality Inspection Center established
- BYD releases self-developed automotive chip using 4nm process, with a running score of up to 1.15 million
- GEODNET launches GEO-PULSE, a car GPS navigation device
- Should Chinese car companies develop their own high-computing chips?
- Infineon and Siemens combine embedded automotive software platform with microcontrollers to provide the necessary functions for next-generation SDVs
- Continental launches invisible biometric sensor display to monitor passengers' vital signs
- Another technical solution for power-type plug-in hybrid: A brief discussion on Volvo T8 plug-in hybrid technology
- Electromagnetic radiation from power line communication systems indoors Electromagnetic radiation from power line communication systems indoors
- Last day! TI live broadcast with prizes | IoT display solutions using DLP micro-projection technology
- C6000DSP heap and stack
- EEWORLD University Hall ---- Training and explanation of black technology of smart amplifier
- SPI cannot receive data, please help
- Potential uses of UWB technology
- Circuit parameters of real op amp
- [Urgent recruitment in Shanghai] RFIC senior design engineer
- Hamburg Records
- About the problem that KEIL MDK can't simulate debugging ARM program