This paper designs a hysteresis control circuit for a buck-type LED constant current driver chip. The chip adopts a high-side current detection scheme and uses a hysteresis current control method to perform hysteresis control on the drive current, thereby obtaining a constant average drive current. The design adopts a simple design concept to achieve constant current drive, does not require complex circuit analysis, can achieve precise current control, and has its own stability. The chip is developed using a 0.5μm 5V/18V/40V CDMOS process, with a power supply voltage range of 4.5V~28V and an operating temperature of -40℃~125℃. It can provide a constant 350mA drive current for the LED. By adjusting the external detection resistor, the constant LED drive current can be adjusted. The DIM signal is provided externally, and the brightness of the LED is adjusted by the duty cycle of the DIM. The Hspice simulation results show that the LED drive current is a hysteresis-changing triangle wave, and the constant current accuracy is less than 6.2%.
1 Introduction
At present, there are two driving modes for LEDs: constant voltage and constant current. Among them, constant current driving is the most commonly used mode. Constant current driving eliminates the current change caused by the change of forward voltage caused by factors such as temperature and process, and ensures constant LED brightness. Among the LED constant current driving control modes, the hysteresis current control mode has many advantages: simple structure, self-stability, not prone to unstable oscillation due to noise, etc., and is increasingly widely used. MAXIM16819 from MAXIM is an LED constant current driving chip.
This paper implements a simple hysteresis control module, which controls the on and off of the power switch tube by building a hysteresis comparison voltage inside the module and combining it with the PWM signal of the DIM control end to achieve constant current control of the LED.
2 Circuit Design and Principle Analysis
2.1 Hysteresis control principle
The application of the hysteresis control module is shown in Figure 1. The change of the LED drive current is reflected in the change of the voltage difference across the detection resistor RSENSE. In this design, the detection resistor is set to 0.5Ω. A smaller detection resistor is conducive to reducing power consumption and maintaining a higher conversion efficiency. The hysteresis current control module has two voltage thresholds built inside. The detection voltage Vcs is compared with the threshold voltage, and the comparison result is ANDed with the DIM dimming signal to control the on and off of the power switch tube.
Figure 1 Application diagram of hysteresis control module
Using PWM dimming, the full current is provided to the LED during the reduced current duty cycle. For example, to reduce the brightness by half, the full current is provided during the 50% duty cycle. Usually the frequency of the PWM dimming signal will exceed 100Hz to ensure that this pulse current is not noticeable to the human eye.
The internal circuit of the hysteresis control module is shown in Figure 2. When the DIM signal is at a high level, when Vcs is greater than the upper voltage threshold, the control circuit outputs a low level and turns off the power switch tube. The loop composed of LED, inductor L, freewheeling diode D and RSENSE allows the inductor to continue to provide current to the LED, and the inductor current gradually decreases, causing the detection voltage Vcs to decrease accordingly; when Vcs is less than the lower threshold voltage, the control circuit outputs a high level and turns on the power switch tube. At this time, D is cut off, forming a loop from the power supply through RSENSE, LED, L and the power switch tube to the ground. The power supply charges the inductor L, the inductor current rises, and the detection voltage Vcs rises accordingly. When Vcs is greater than the upper voltage threshold, the control circuit turns off the switch tube and repeats the action of the previous cycle, thus completing the hysteresis current control of the LED drive current, so that the drive current flowing through the LED, that is, the average value of the inductor current, is constant.
Figure 2 Internal modules of the hysteresis control module
2.2 Hysteresis comparison voltage generation circuit
The input voltage of 4.5V~28V is adjusted and converted into a constant voltage Vcc of 5V to power the subsequent circuit. As shown in Figure 3, the potential at point A is controlled by the operational amplifier and will be equal to the reference voltage 1.2V. Assuming that the output Vout is high, M2 is turned on, the current flowing through M1 is IM1=Vref/R2, and the voltage at point B is VBL=Vin-IM1 R1; when Vout is low, M2 is turned off, the current flowing through M1 becomes I′M1=Vref/(R2+R3), and the voltage at point B rises to VBH=Vin-I′M1 R1, so the voltage change at point B is ΔVB=VBH-VBL=Vref R1 R3/R2(R2+R3), which means that a hysteresis voltage is generated at point B when Vout changes from a high level to a low level. It can be seen that the hysteresis voltage has nothing to do with the input voltage, but is only determined by the reference voltage Vref and the size of the resistor. The size of the hysteresis voltage can be set by selecting the resistance value of each resistor.
[page]
Figure 3 Hysteresis comparison voltage generation circuit
2.3 Op amp circuit implementation
From the above analysis, it can be seen that the operational amplifier plays an important role. It must have a high gain to make the voltage at point A accurately follow the reference voltage, so as to accurately set the level at point B and the hysteresis voltage. In addition, since the change frequency of Vout is the same as the system switching frequency (the maximum switching frequency of the system is about 2MHz), the current flowing through M1 also switches quickly between IM1 and I′M1 at the same frequency, so the unit gain bandwidth of the operational amplifier must be greater than the maximum switching frequency of the system. The designed operational amplifier structure is shown in Figure 4. The folded input structure can obtain a larger common-mode input voltage range.
Figure 4 Op amp implementation circuit
From the frequency characteristic simulation diagram of the operational amplifier, it can be seen that the gain reaches 84.266dB, the phase margin is 108°, and the unit gain bandwidth is about 12MHz, which meets the circuit requirements.
Figure 5 Op amp frequency characteristic simulation
2.4 Average drive current setting
The op amp clamps the potential of point A to the bandgap voltage reference. The cascade current mirror composed of M7-M8, M6-M9 mirrors the bias current I1 to the branch where M8-M9-R5 is located, so the voltage Vn of one input terminal of the Compara2tor module remains constant, and the voltage Vp of the other input terminal will change with the detection voltage Vcs. When the comparator output Vout is high (the switch tube is turned on), the voltage at point B is VBL, which is the lower threshold detection voltage VCSMIN. When Vcs drops to this threshold, the symmetrical circuit structure composed of M6~M11 makes the current flowing through R5 and R6 equal, and Vn=Vp at this time. If Vcs Hysteresis current range: The above formula determines the ripple size of the driving current. 3 Simulation Results Analysis The circuit in this paper adopts 0.5μm 5V/18V/40V CDMOS process and is simulated by Hspice Z-2007.03. The simulation results are shown in Figure 6 under the combined effect of DIM signal with pulse width of 200μs and period of 300μs and Vin=12V (typical value). Figure 6 Circuit simulation when Vin = "12V" The LED driving current is simulated again when Vin=2.5V and Vin=28V respectively. The three simulation data results are shown in Table 1. Table 1 Driving current under three input voltage conditions When Vin=12V, the temperature characteristic of the LED driving current is simulated, and the three simulation waveform results are shown in Table 2. It can be seen that the temperature characteristic of the chip is good. Table 2 Vin = "Drive current at three ambient temperatures under 12V" Since the fixed delay τ of the system has an impact on the current ripple, the actual driving current peak is IMAX + τoff di/dt, and the current valley is IMIN-τON di/dt, τoff is the system delay from the driving current being greater than the set value to the power switch being turned off, τon is the system delay from the driving current being less than the set value to the power switch being turned on, and di/dt is the rate of change of the inductor current. If the inductance takes a larger value, it will have little effect on the average driving current, but it can reduce the current ripple. Otherwise, this is at the expense of increasing the volume of the external inductor. The circuit can achieve high efficiency. On the one hand, the power consumption in the detection resistor It will cause power dissipation of the power supply, but in this design RSENSE = 0.5Ω, then PRSENSE is quite small. On the other hand, the system efficiency is defined as the ratio of the power consumed by the LED to the power provided by the power supply, that is, η = PLED/PPOWER. Among them, PPOWER = Vin3 Ivin, PLED = VLED*. From the simulation, it can be seen that the average value of Ivin is much smaller than, so the efficiency of the system can be very high. 4 Conclusion This paper designs a hysteresis control circuit suitable for buck-type LED constant current driver chip. The high-side current detection scheme is adopted, and the hysteresis current control method is used to perform hysteresis control on the drive current, so as to obtain a constant average drive current. By adjusting the external detection resistor, the constant LED drive current can be adjusted. The chip adopts 015μm 5V/18V/40V CDMOS process, the power supply voltage range is 4.5V~28V, and it can provide a constant 350mA drive current for the LED. The temperature characteristic is -40℃~125℃, which can achieve a fairly high efficiency. When Vin changes from 4.5V to 28V, the average drive current changes by 22mA, and the maximum constant current accuracy is 6.2%.
Previous article:Research on a low voltage and high current DC-DC converter with low current ripple [Figure]
Next article:Technical Analysis of Several Linear Voltage Regulators
Recommended ReadingLatest update time:2024-11-22 16:32
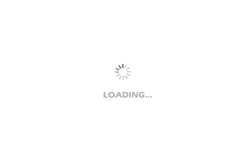
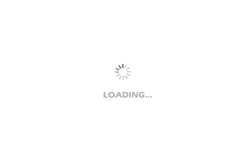
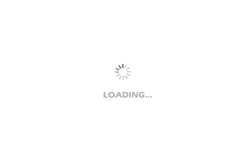
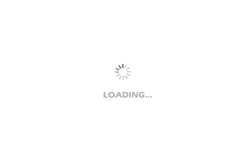
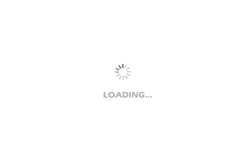
- Popular Resources
- Popular amplifiers
- RAQ #223: How to measure and determine soft-start timing without a soft-start equation?
- Vicor high-performance power modules enable the development of low-altitude avionics and EVTOL
- Bourns Launches Two Thick Film Resistor Series with High Power Dissipation Capabilities in Compact TO-220 and DPAK Package Designs
- Bourns Launches New High-Pulse Brake Resistor Series with Superior Energy Dissipation Capabilities
- Nexperia launches new 120 V/4 A half-bridge gate driver to further improve robustness and efficiency in industrial and automotive applications
- Vishay's New 150 V MOSFETs Offer Industry-Leading Power Loss Performance
- The first generation of SGT MOSFET series from Qiangmao: innovative trench technology, automotive-grade 60 VN channel, breakthrough in high-efficiency performance of automotive electronics
- DC/DC Power Supplies for Automotive Applications
- MathWorks and NXP Collaborate to Launch Model-Based Design Toolbox for Battery Management Systems
- Intel promotes AI with multi-dimensional efforts in technology, application, and ecology
- ChinaJoy Qualcomm Snapdragon Theme Pavilion takes you to experience the new changes in digital entertainment in the 5G era
- Infineon's latest generation IGBT technology platform enables precise control of speed and position
- Two test methods for LED lighting life
- Don't Let Lightning Induced Surges Scare You
- Application of brushless motor controller ML4425/4426
- Easy identification of LED power supply quality
- World's first integrated photovoltaic solar system completed in Israel
- Sliding window mean filter for avr microcontroller AD conversion
- What does call mean in the detailed explanation of ABB robot programming instructions?
- USB Type-C® and USB Power Delivery: Designed for extended power range and battery-powered systems
- RAQ #223: How to measure and determine soft-start timing without a soft-start equation?
- RAQ #223: How to measure and determine soft-start timing without a soft-start equation?
- GigaDevice's full range of automotive-grade SPI NOR Flash GD25/55 wins ISO 26262 ASIL D functional safety certification
- GigaDevice's full range of automotive-grade SPI NOR Flash GD25/55 wins ISO 26262 ASIL D functional safety certification
- New IsoVu™ Isolated Current Probes: Bringing a New Dimension to Current Measurements
- New IsoVu™ Isolated Current Probes: Bringing a New Dimension to Current Measurements
- Infineon Technologies Launches ModusToolbox™ Motor Kit to Simplify Motor Control Development
- Infineon Technologies Launches ModusToolbox™ Motor Kit to Simplify Motor Control Development
- STMicroelectronics IO-Link Actuator Board Brings Turnkey Reference Design to Industrial Monitoring and Equipment Manufacturers
- EEWORLD University Hall----Isolated power supply for PLC I/O modules
- ESP32 can't run the webserver example.
- C2000 series TMS320F28335 ADC considerations
- Project Development
- Car box disassembly
- Free application: Anxinke NB-IoT development board EC-01F-Kit (gift reviewer 300M annual card)
- Application Tips/ADC Application Elements in C8051F020
- Problems with lsm303agr measuring magnetic field
- CC2650 tinkering tutorial - the beginning of everything Hello world program!
- [Evaluation of domestic FPGA Gaoyun GW1N-4 series development board]——10. Confused about OSC jitter, rPLL jitter and deviation?