summary
This article introduces a 10W LED driver designed using TI's TPS92210 control chip. TPS92210 has a unique critical mode fixed peak current control function, and the design does not require feedback, making the entire design simple, with fewer components and low cost.
introduction
Recently, in the LED driver power supply market, non-isolated solutions have become a hot application due to their advantages such as smaller magnetic components, higher energy efficiency, fewer components, lower total bill of materials cost, and the ability to meet safety regulations with mechanical design. This article introduces a 10W LED driver power supply designed using TI's control chip TPS92210. Using the TPS92210's unique critical mode fixed peak current control function, the design does not require feedback, so the entire design is simple, with fewer components, low cost, and high efficiency.
1. Power supply solution introduction
This solution uses a critical Buck circuit controlled by TPS92210 and sets the TPS92210 to work at a fixed peak current to keep the inductor current peak value fixed. Because the circuit works in critical mode, the average value of the inductor current is equal to half of the peak current, thereby achieving the purpose of outputting a constant current.
At the same time, this solution does not require additional circuits, and the TPS92210 itself can implement output overcurrent, short circuit, open circuit and other protections. Therefore, the entire solution has fewer components and lower costs.
The input adopts a valley-fill circuit, which makes the PF value of the whole machine always above 0.7.
C8, L2, and C5 form a pi-type filter. The whole machine passed the conduction test.
Figure 1: 10W LED power solution
Figure 2: 10W LED power supply picture
1.1 TPS92210 critical mode setting
The TPS92210 needs to meet three conditions to start a new cycle:
1) The time since the last opening needs to be greater than the time controlled by the Ifb current.
2) The time since the last opening needs to be greater than the time limited by the chip's maximum frequency of 7.5us.
3) The Tze pin must have a zero point crossing from high to low.
Since the above three conditions need to be met, the design connects the FB pin to Vdd through a resistor to set a fixed DC bias, so that the turn-on of TPS92210 is completely determined by the voltage zero-crossing of the Tze pin, which ensures that the converter always works in the critical current mode.
1.2 Inductor Design
Calculate the inductance according to the input and output requirements. In this solution, the input is 176V~264Vac, the output is 40V, 0.25A. Since the input uses a valley-fill circuit, the input voltage range can be calculated as follows:
Based on the minimum and maximum input voltages calculated above, the minimum and maximum duty cycles can be calculated:
The average output current is 0.25A, and the current works in the critical current mode. The average current on the inductor is the output current. The peak current and effective current of the inductor can be calculated as follows:
Because the critical mode converter, the higher the input voltage, the higher the operating frequency. Considering the volume and efficiency, the maximum operating frequency is set to 100KHz.
Then the inductance can be calculated as follows:
So the inductance is about 700uH.
Based on the calculated inductance, it can be verified that the minimum switching frequency is:
Based on the calculated maximum duty cycle and minimum switching frequency, the maximum on-time can be obtained as:
Tonmax is less than the maximum on-time of 5us allowed by TPS92210, so there is no problem with the inductor design.
Select the core: Assuming Bmax=2500G, filling factor: k=0.4, current density: j=6A/mm^2, the AP value required for the core can be calculated as:
According to the AP value, RM5 is selected as the inductor core:
The Ae area of RM5 is as follows, and the number of turns required for the inductor can be calculated:
The inductor needs to have approximately 67 turns.
According to the previously calculated current RMS value and the set current density j, AWG30 is selected to wind the inductor.
Select 1 strand of AWG30 as the winding.
2. Test results
Based on the above analysis and design, a prototype was made and its performance was verified. The experimental results are as follows.
2.1 Efficiency Test
2.2 PF value
2.3 Current Accuracy
2.4 Startup
2.5 Output ripple
2.6 Short Circuit Protection
2.7 Open circuit protection
2.8 EMC Testing
3. Conclusion
This paper analyzes and designs a critical mode buck converter controlled by TPS92210. The feasibility and setting method of TPS92210 critical mode are analyzed. The calculation and design method of inductance are introduced in detail. Finally, a prototype is made to verify the correctness of the analysis and calculation. The feasibility of TPS92210 for non-isolated constant current LED driver power supply is guaranteed.
Previous article:What you need to know about motor drive design
Next article:Power ICs required for the latest FPGAs
Recommended ReadingLatest update time:2024-11-15 17:05
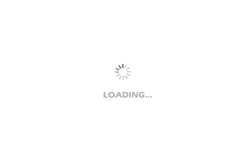
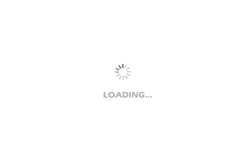
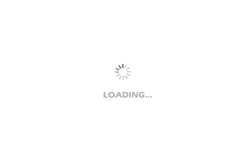
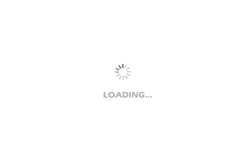
- Popular Resources
- Popular amplifiers
- MathWorks and NXP Collaborate to Launch Model-Based Design Toolbox for Battery Management Systems
- STMicroelectronics' advanced galvanically isolated gate driver STGAP3S provides flexible protection for IGBTs and SiC MOSFETs
- New diaphragm-free solid-state lithium battery technology is launched: the distance between the positive and negative electrodes is less than 0.000001 meters
- [“Source” Observe the Autumn Series] Application and testing of the next generation of semiconductor gallium oxide device photodetectors
- 采用自主设计封装,绝缘电阻显著提高!ROHM开发出更高电压xEV系统的SiC肖特基势垒二极管
- Will GaN replace SiC? PI's disruptive 1700V InnoMux2 is here to demonstrate
- From Isolation to the Third and a Half Generation: Understanding Naxinwei's Gate Driver IC in One Article
- The appeal of 48 V technology: importance, benefits and key factors in system-level applications
- Important breakthrough in recycling of used lithium-ion batteries
- LED chemical incompatibility test to see which chemicals LEDs can be used with
- Application of ARM9 hardware coprocessor on WinCE embedded motherboard
- What are the key points for selecting rotor flowmeter?
- LM317 high power charger circuit
- A brief analysis of Embest's application and development of embedded medical devices
- Single-phase RC protection circuit
- stm32 PVD programmable voltage monitor
- Introduction and measurement of edge trigger and level trigger of 51 single chip microcomputer
- Improved design of Linux system software shell protection technology
- What to do if the ABB robot protection device stops
- Huawei's Strategic Department Director Gai Gang: The cumulative installed base of open source Euler operating system exceeds 10 million sets
- Download from the Internet--ARM Getting Started Notes
- Learn ARM development(22)
- Learn ARM development(21)
- Learn ARM development(20)
- Learn ARM development(19)
- Learn ARM development(14)
- Learn ARM development(15)
- Analysis of the application of several common contact parts in high-voltage connectors of new energy vehicles
- Wiring harness durability test and contact voltage drop test method
- 76 Rules for China's Artificial Intelligence
- Application of high-performance line cards for synchronous networks
- Analysis of AC-coupled op amp circuits
- Let’s chat: Qinheng PD fast charging protocol chip online customization platform is launched, are you interested?
- ST NUCLEO-L452RE free trial is here
- Screen interface
- Using the encoder function of STM32, I am not very clear about the assignment of a data structure in the program. I would like to ask for your advice
- Qorvo Launches Industry-Leading Low Noise Figure LNA to Support 5G Base Station Deployment
- [Shijian's ADI Road Theme Tour] Second stop: Accumulate knowledge of instruments and meters, check in to win Kindle and other gifts
- How to check for broken wire errors when drawing AD schematics