Since the emergence of external lighting, we divide lighting into three eras: the filament bulb era (incandescent lamp), the gas bulb era (fluorescent lamp), and the semiconductor light-emitting era (LED). Among them, the incandescent lamp with the longest history and the LED, the mainstream in the future, are the most important points for investigation. No matter how the era develops, the production process of the lighting industry is surprisingly similar, except that China is also at the downstream of the industry. The core technology is basically owned by countries and regions such as Europe, the United States, and Japan.
1. The principle of LED light emission is that when electrons pass through a layer of semiconductor material, they stimulate the semiconductor material to convert electrical energy into light energy. However, the light emission ability of a single layer of semiconductor is very weak, so many layers of single layer materials must be stacked up and pressed into a composite material similar to a thousand-layer cake, which is the "epitaxial wafer".
Therefore, the luminous efficiency of LEDs is determined by how many layers can be pressed into the same thickness. The thinner the single layer of material is, the more layers can be stacked, and the higher the luminous efficiency is. Currently, the thickness of each layer is generally only 2-20 microns, which also determines that epitaxial wafer production is the most difficult part of the entire LED production process.
2. Cutting - LED core: It is equivalent to extracting the filament from the tungsten wire material. The difference is that the epitaxial wafer is square after cutting.
Due to the special structure of the epitaxial wafer, it is very difficult to cut out the light-emitting core intactly. Not only does it require a vacuum environment, but it also requires a professional cutting machine. Currently, there are only two manufacturers in the world that produce such cutting machines.
3. Put the core into the LED chip: The chip is to the LED as the lamp holder is to the light bulb, which is the power supply part. The "chip" is a very important equipment to achieve the ideal effect of LED, because LED has very high requirements for current.
4. Encapsulate LED chips into luminous bodies: Encapsulate LED chips into luminous bodies, just like adding a lampshade to a filament lamp holder to make a light bulb. The shape of the lampshade can be different according to the needs, but the encapsulation technology determines the service life of the luminous body.
5. Lighting application: Just like using incandescent bulbs, different LED products can be assembled according to different functions and needs.
For LED lighting, the first three steps of epitaxial wafer, cutting and chip are upstream, the fourth step of packaging is midstream, and the fifth step of application is downstream. We need to use more energy to break through these problems.
Previous article:LED module usage precautions
Next article:New LED lighting cooling solution
Recommended ReadingLatest update time:2024-11-16 19:56
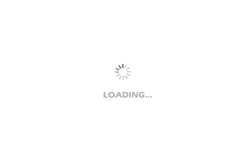
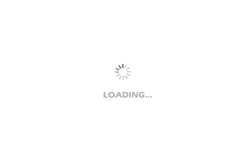
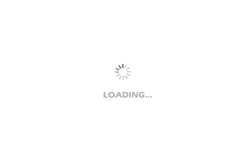
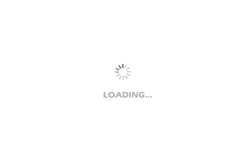
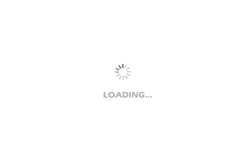
- Popular Resources
- Popular amplifiers
- MathWorks and NXP Collaborate to Launch Model-Based Design Toolbox for Battery Management Systems
- STMicroelectronics' advanced galvanically isolated gate driver STGAP3S provides flexible protection for IGBTs and SiC MOSFETs
- New diaphragm-free solid-state lithium battery technology is launched: the distance between the positive and negative electrodes is less than 0.000001 meters
- [“Source” Observe the Autumn Series] Application and testing of the next generation of semiconductor gallium oxide device photodetectors
- 采用自主设计封装,绝缘电阻显著提高!ROHM开发出更高电压xEV系统的SiC肖特基势垒二极管
- Will GaN replace SiC? PI's disruptive 1700V InnoMux2 is here to demonstrate
- From Isolation to the Third and a Half Generation: Understanding Naxinwei's Gate Driver IC in One Article
- The appeal of 48 V technology: importance, benefits and key factors in system-level applications
- Important breakthrough in recycling of used lithium-ion batteries
- Innolux's intelligent steer-by-wire solution makes cars smarter and safer
- 8051 MCU - Parity Check
- How to efficiently balance the sensitivity of tactile sensing interfaces
- What should I do if the servo motor shakes? What causes the servo motor to shake quickly?
- 【Brushless Motor】Analysis of three-phase BLDC motor and sharing of two popular development boards
- Midea Industrial Technology's subsidiaries Clou Electronics and Hekang New Energy jointly appeared at the Munich Battery Energy Storage Exhibition and Solar Energy Exhibition
- Guoxin Sichen | Application of ferroelectric memory PB85RS2MC in power battery management, with a capacity of 2M
- Analysis of common faults of frequency converter
- In a head-on competition with Qualcomm, what kind of cockpit products has Intel come up with?
- Dalian Rongke's all-vanadium liquid flow battery energy storage equipment industrialization project has entered the sprint stage before production
- Allegro MicroSystems Introduces Advanced Magnetic and Inductive Position Sensing Solutions at Electronica 2024
- Car key in the left hand, liveness detection radar in the right hand, UWB is imperative for cars!
- After a decade of rapid development, domestic CIS has entered the market
- Aegis Dagger Battery + Thor EM-i Super Hybrid, Geely New Energy has thrown out two "king bombs"
- A brief discussion on functional safety - fault, error, and failure
- In the smart car 2.0 cycle, these core industry chains are facing major opportunities!
- The United States and Japan are developing new batteries. CATL faces challenges? How should China's new energy battery industry respond?
- Murata launches high-precision 6-axis inertial sensor for automobiles
- Ford patents pre-charge alarm to help save costs and respond to emergencies
- New real-time microcontroller system from Texas Instruments enables smarter processing in automotive and industrial applications
- How does FPGA adjust the volume of the buzzer?
- [Repair] Repaired a data cable
- How long will the battle between community owners and communication base stations last?
- Please tell me the winding method and other parameters of the EE8 transformer that can increase 0.7V to 7V
- Conversion between CC2640R2F projects
- Pengfeng Technology RVBoards-Nezha (RISC-V SBC) Allwinner Development Board Introduction Part 3
- Cadence Certus Closure Solution is a new generation chip-level convergence solution. Welcome to learn more!
- What is the progress of domestic NPU chips?
- How is JTAG used for chip testing?
- Talk about downloading the DSP28335 register manual