The DC power supply system is mainly responsible for supplying power to control equipment, protection equipment, etc. in the process of power production. Insulation degradation and DC bus grounding are common faults in DC power supply systems. Once a DC power supply fails, it will affect the normal operation of the control equipment and protection equipment. In severe cases, it may even lead to incorrect control of the control equipment and refusal of protection of the protection equipment, thus causing production accidents. Therefore, the insulation performance detection and grounding detection of the DC power supply system are issues worthy of attention. Common DC grounding detection systems mostly use the balanced bridge principle to detect the insulation resistance of the bus, the dual-frequency detection principle to detect the insulation resistance of the branch, and find the grounding branch. However, the balanced bridge principle cannot detect the resistance value when the insulation resistance of the positive and negative bus decreases in proportion, and the dual-frequency detection principle requires the injection of AC signals into the system, which will increase the ripple of the DC power supply system. The DC grounding detection system introduced in this article uses the "balanced-unbalanced method" to detect the bus voltage and uses a leakage current sensor to detect the branch insulation resistance, which effectively overcomes the defects of the above methods.
The DC grounding detection system is mainly used to measure the insulation resistance of the DC system to the ground and detect bus grounding faults. The specific detection contents include: measuring the voltage between the positive and negative busbars and the ground, the voltage difference between the positive and negative busbars, the insulation resistance between the positive and negative busbars and the ground, and the insulation resistance between each branch and the ground. When a ground fault occurs, determine the positive and negative polarity of the ground busbar and find the specific grounding branch.
1 DC grounding detection principle
1.1 Working principle of DC grounding detection system
Due to the long-term operation of the DC power supply system in a harsh environment, the lines, connectors, wiring terminals, knife switches, etc. will age, resulting in reduced insulation performance of the positive and negative busbars, reduced insulation resistance to the ground, and leakage current. The generation of leakage current will cause the current flowing into and out of the power load to be inconsistent (part of the current flows into the ground through the insulation resistance). The non-contact DC leakage current sensor can sense the DC current difference flowing into and out of the sensor into a DC voltage. In this way, a non-contact DC leakage current sensor is installed on the input and output lines of each power load, and the leakage current of each power load or line can be detected. The DC grounding detection system calculates the magnitude of the leakage current based on the induced voltage of the leakage current sensor. Then, the positive and negative bus voltages to ground are detected using the “balanced-unbalanced method”, and the insulation resistance of each branch is calculated based on the bus voltage and leakage current.
1.2 Principle of insulation resistance detection by balanced-unbalanced method
The balanced-unbalanced detection method connects different balanced and unbalanced resistance networks to the tested line in sequence by controlling the on and off of the switch, and measures the voltage Un of the detection point A at the same time. According to the connected network structure and the measured Un voltage value, the bus voltage and bus insulation resistance can be calculated. This method can effectively overcome the defect that the bridge balance principle detection method cannot detect the proportional decrease of the positive and negative bus insulation resistance, and also avoids the influence of the dual-frequency detection method on the power supply ripple of the DC power supply system. The detection process of the balanced-unbalanced detection method is shown in Figure 2.
As shown in Figure 2, U+ and U- are the bus supply voltages of the measured line. The voltage difference Ux+y between the two buses is 440 V during normal operation and varies with the internal resistance of the battery. Rx and Ry are the positive bus insulation resistance and negative bus insulation resistance of the measured line, respectively. The positive and negative bus insulation resistances reflect the overall insulation performance of the 64 positive and negative branches, which is equivalent to the parallel connection of the positive and negative insulation resistances of each branch. Under normal circumstances, the insulation resistance of the two buses is >20 kΩ. Ux and Uy are the positive and negative bus voltages to the ground. The magnitude varies with the insulation resistance of the positive and negative buses, but the voltage difference between the two buses is constant at Ux+y. In order to detect the positive and negative bus voltages Ux, Uy, Rx, and Ry, the system uses the "balance-unbalance detection method" to detect the bus voltage and bus insulation resistance. The calculation formula is shown in formula (1).
When K1, K2 are connected, K3, K4, K5 are disconnected, (connected to a balanced bridge)
When K1, K2, K3, K5 are connected, K4 is disconnected, (connected to an unbalanced bridge)
When K1, K2, K4, K5 are connected, K3 is disconnected, (connected to an unbalanced bridge)
Solving equations (1) to (3) together, we can get
According to Ohm's law and the principle of voltage division, we can get
2 System hardware design
The DC grounding detection system uses the low-power processor
MSP430F149
as the hardware core, and the peripheral circuit can be divided into a data acquisition module, a human-computer interaction module, and a processor module. The data acquisition module is responsible for detecting the leakage current, bus voltage, and bus insulation resistance of the 64 branches; the human-computer interaction module is responsible for LCD display and keyboard input; the processor module is responsible for coordinating the data processing, data storage, human-computer interaction, etc. of the entire system. The specific hardware structure block diagram is shown in Figure 3.
Positive and negative bus voltage detection. After the positive bus, negative bus and ground wire pass through the "balanced-unbalanced" detection bridge, the voltage at detection point A is divided by the potentiometer to obtain a low-voltage DC signal that is easy to collect. The voltage of the positive and negative bus relative to the ground exceeds the safe voltage of the human body. In order to reduce the connection between the processor and the detection bridge, the system uses a voltage-frequency converter to collect the divided signal. Due to the use of a voltage-frequency converter, only one signal line and one optocoupler device are required to detect the bus voltage, which improves the reliability and stability of the system and simplifies the system design. The low-voltage DC signal after voltage division is converted by the voltage/frequency converter AD7740 into a square wave signal whose frequency is linearly related to the input voltage. The square wave signal is sent to the processor after optocoupler isolation to prevent the high voltage of the bus from causing harm to the operator. The processor measures the frequency of the square wave signal and converts it into the voltage corresponding to the detection point A. Finally, the bus voltage and bus insulation resistance are calculated based on the voltage at point A measured three times and the network structure.
64-way branch leakage current detection. The DC induced voltage sent by the non-contact leakage current sensor is selected by 8 8-to-1 analog switches (CD4097) to form 8 DC voltage signals. In order to reduce the impact of the input impedance of the ADC chip on the measurement accuracy, the voltage signal is sent to the 8 analog signal input terminals of the A/D converter
TLC254
3 after being sent to the buffer by a high input impedance op amp. The A-DC chip automatically switches channels internally, cyclically collects analog signals from 8 input terminals, and the collected data is sent to the processor
MSP430F149
through the SPI serial communication bus
.
The human-computer interaction module is divided into LCD display and matrix keyboard. The LCD is also a serial SPI interface, sharing an SPI interface with the ADC chip, and distinguished by the I/O port chip selection. The LCD is mainly used to cyclically display the current positive and negative bus voltages, positive and negative bus insulation resistances, current time, and branch numbers with abnormal insulation resistance. The keyboard uses 4 I/O interfaces to scan the 2×2 matrix keyboard to input the upper and lower limits of the insulation resistance alarm. The upper and lower limits of the bus voltage alarm, select the stored data to be viewed.
The processor module is divided into data storage, real-time calendar clock, system reset, system power supply, JTAG debugging interface, etc. When the bus voltage or insulation resistance of the system is abnormal, the instrument will automatically record the current bus voltage, bus insulation resistance, abnormal branch number and the current fault date, and store them in EEPROM for future query. The real-time calendar clock chip is used to provide a time record source for the occurrence of abnormal faults and can be used for daily display.
3 System software design
This system uses the MSP430F149 processor as the system control center. The advantage of the large data storage of the single-chip microcomputer is used in the software design to facilitate the storage and processing of the data collected by the 64-channel leakage current sensor, bus voltage and bus insulation resistance data. The first thing to complete in the main program is the initialization of each module, mainly including LCD initialization, analog switch initialization, and analog-to-digital converter initialization. In order to ensure the reliability of the system, the system will first perform a self-test after power-on. After ensuring that the hardware circuits of each part of the system are normal, it will automatically enter the DC grounding detection state, otherwise the self-test failure message will be displayed to prompt the operator.
The entire program is written in C language. In the program design, the structured programming method is adopted to make each module program relatively independent, which is convenient for the maintenance, transplantation and upgrading of the program code. At the same time, such a separate program design reduces the difficulty of code debugging and shortens the debugging cycle. The data closely related to the ground fault information (such as bus voltage, bus insulation resistance, branch insulation resistance, grounding branch number, etc.) is placed in a structure to facilitate power-off storage and playback display. The main program flow chart of the system is shown in Figure 4.
4 Experimental data analysis
In order to achieve good test results, A/D acquisition must achieve a certain test accuracy. Figure 5 shows the measured data and test error analysis curve of A/D acquisition. It can be seen from the figure that the error of A/D acquisition is about 20 mV, which is within the normal range because the system uses 8-bit A/D and 5 V reference voltage. This sampling accuracy meets the overall design requirements.
In the experimental environment, a 110 V regulated DC power supply is used to simulate direct battery power supply. It can be seen that U1=110 V. A group of resistors are respectively connected between the positive and negative busbars and the ground wire to simulate the insulation resistance of the positive and negative busbars. Groups 1 to 4 simulate the situation where both the positive and negative busbars are grounded, group 5 simulates the situation where there is no busbar grounding, groups 6 and 7 simulate the situation where the negative busbar is grounded, and groups 8 and 9 simulate the situation where the positive busbar is grounded. The test results are shown in Table 1.
From groups 1 to 5, it can be seen that when the insulation resistance is large, the relative error of the test increases slightly. This is because the input impedance of the sampling A/D is small, so when the test resistance is large, the error is relatively large. In addition, when the insulation resistance of the negative bus is <30 kΩ and the insulation resistance of the negative bus is normal, the measurement effect of the former is worse. Because the actual measured voltages U2 and U3 are both small at this time, the relative error of A/D sampling is larger, so the error of the resistance is also larger. However, it is much better than the balanced bridge method that cannot detect the two-point grounding situation, and can detect the grounding positively. In the insulation detection environment, as long as the insulation resistance is >20 kΩ, it is considered that the insulation is good. Therefore, for the application environment of insulation detection, this system can accurately test the insulation resistance of each line, which fully meets the needs of the application environment.
5 Conclusion
The DC grounding detection system and insulation resistance detection technology introduced in this article can obtain relatively accurate test results regardless of the form of insulation resistance, which well solves the problems existing in the traditional balanced bridge detection method and dual-frequency detection method. This solution can be applied not only to DC system insulation monitoring in power plants and substations, but also to DC system insulation monitoring and grounding detection in railway and telecommunication departments.
Previous article:Short-circuit treatment of ideal DC voltage source in AC path
Next article:Design and implementation of shortwave broadband low voltage power amplifier
Recommended ReadingLatest update time:2024-11-16 19:59
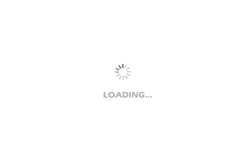
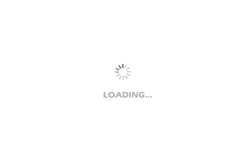
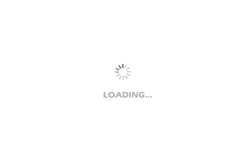
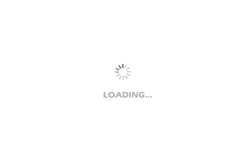
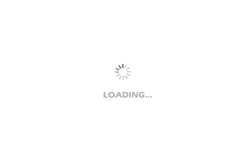
- MathWorks and NXP Collaborate to Launch Model-Based Design Toolbox for Battery Management Systems
- STMicroelectronics' advanced galvanically isolated gate driver STGAP3S provides flexible protection for IGBTs and SiC MOSFETs
- New diaphragm-free solid-state lithium battery technology is launched: the distance between the positive and negative electrodes is less than 0.000001 meters
- [“Source” Observe the Autumn Series] Application and testing of the next generation of semiconductor gallium oxide device photodetectors
- 采用自主设计封装,绝缘电阻显著提高!ROHM开发出更高电压xEV系统的SiC肖特基势垒二极管
- Will GaN replace SiC? PI's disruptive 1700V InnoMux2 is here to demonstrate
- From Isolation to the Third and a Half Generation: Understanding Naxinwei's Gate Driver IC in One Article
- The appeal of 48 V technology: importance, benefits and key factors in system-level applications
- Important breakthrough in recycling of used lithium-ion batteries
- Innolux's intelligent steer-by-wire solution makes cars smarter and safer
- 8051 MCU - Parity Check
- How to efficiently balance the sensitivity of tactile sensing interfaces
- What should I do if the servo motor shakes? What causes the servo motor to shake quickly?
- 【Brushless Motor】Analysis of three-phase BLDC motor and sharing of two popular development boards
- Midea Industrial Technology's subsidiaries Clou Electronics and Hekang New Energy jointly appeared at the Munich Battery Energy Storage Exhibition and Solar Energy Exhibition
- Guoxin Sichen | Application of ferroelectric memory PB85RS2MC in power battery management, with a capacity of 2M
- Analysis of common faults of frequency converter
- In a head-on competition with Qualcomm, what kind of cockpit products has Intel come up with?
- Dalian Rongke's all-vanadium liquid flow battery energy storage equipment industrialization project has entered the sprint stage before production
- Allegro MicroSystems Introduces Advanced Magnetic and Inductive Position Sensing Solutions at Electronica 2024
- Car key in the left hand, liveness detection radar in the right hand, UWB is imperative for cars!
- After a decade of rapid development, domestic CIS has entered the market
- Aegis Dagger Battery + Thor EM-i Super Hybrid, Geely New Energy has thrown out two "king bombs"
- A brief discussion on functional safety - fault, error, and failure
- In the smart car 2.0 cycle, these core industry chains are facing major opportunities!
- The United States and Japan are developing new batteries. CATL faces challenges? How should China's new energy battery industry respond?
- Murata launches high-precision 6-axis inertial sensor for automobiles
- Ford patents pre-charge alarm to help save costs and respond to emergencies
- New real-time microcontroller system from Texas Instruments enables smarter processing in automotive and industrial applications
- RISC-V MCU Application Development Series Tutorial CH32V103
- Communication between Yitong Chuanglian MODBUS to PROFIBUS gateway and Honeywell DCS system
- Let's take a look
- 【TI Wireless】Micro Dual-Mode Wireless Receiver
- PWM and PFM
- Let’s talk about whether Huawei can survive in the end.
- Can the network cable be directly soldered to the PCB without a crystal plug or can the network cable be plugged into the circuit board with terminals?
- [Revenge RVB2601 creative application development] helloworld_beginner's guide to debugging methods and processes
- What changes will occur if RFID technology is applied to clothing production?
- EEWORLD University Hall----30 Case Studies of MATLAB Intelligent Algorithms