1 Introduction
With the development of industry and science and technology, users have higher and higher requirements for power quality. All raw power, including city power, may not meet the requirements of users and must be processed before use. Inverter technology plays an important role in this process. Traditional inverter technology is mostly analog control or a combination of analog and digital control systems. Its disadvantages are
1) The control circuit has many components, large size and complex structure;
2) Lack of flexibility: once the hardware circuit is designed, the control strategy cannot be changed;
3) Debugging is troublesome. Due to differences in component characteristics, the power supply consistency is poor, and the operating point drift of analog devices will cause the drift of system parameters, which brings inconvenience to debugging.
Therefore, traditional inverters are no longer suitable for new requirements in many situations.
With the advent of high-speed and low-cost digital signal processors (DSPs), digital power supplies (DPSs) have emerged. Its advantages include:
1) Digitalization makes it easier to process and control digital chips, avoid distortion and distortion of analog signal transmission, and reduce interference from stray signals;
2) Facilitate system debugging;
3) If network communication and power supply software debugging technology are combined, remote sensing, remote measurement and remote adjustment can be achieved.
All these make digital control of inverter power supply a future development trend.
This paper adopts the TMS320LF2407 DSP designed by TI for motor and power electronics as the controller, and introduces the hardware and software design of the digital cycloconverter.
2 Structural features of TMS320LF2407
TMS320LF2407 has the structural features necessary for high-speed signal processing and digital control functions. Combining its optimized peripheral units with a high-performance DSP core, it can provide high-speed and full-speed advanced control technology for various types of motors. Its main features are
1) The system runs at a main frequency of 30MHz, which shortens the instruction cycle to 33ns. Most instructions can be completed within a single cycle, improving the real-time capability of the controller.
2) Two event manager modules EVA and EVB, each including two 16-bit general-purpose timers; eight 16-bit pulse width modulation (PWM) channels. They can realize three-phase inverter control; symmetrical and asymmetrical waveforms of PWM; fast PWM channel shutdown when the external pin PDPINTx appears low level; programmable PWM dead zone control to prevent the upper and lower bridge arms from inputting trigger pulses at the same time; 16-channel A/D converter and other functions. The event management module is suitable for controlling AC induction motors, brushless DC motors, switched reluctance motors, stepper motors, multi-stage motors and inverters.
3) The minimum conversion time of the 10-bit A/D converter is 500ns, and two event managers can be selected to trigger two 8-channel input A/D converters or one 16-channel input A/D converter.
4) Up to 40 general-purpose input/output pins (GPIO) that can be individually programmed or multiplexed.
3 System Structure
The system consists of two parts: the main circuit and the control circuit, as shown in Figure 1. The main circuit uses a phase-shifted zero voltage, zero current (PS-ZVZCS) full-bridge converter and a phase-controlled cyclic converter PCCYC (Phase Control LED Cycle Converter). Compared with other converters, the phase-controlled cyclic converter can always work in the first and third quadrants. Combined with the phase-shifting technology, it can greatly improve the working efficiency of the high-frequency transformer. At the same time, a high-frequency loop is used for inversion, so there is no need to use an industrial frequency transformer, which reduces the volume. The full-bridge converter uses a saturable inductor Lr and a DC blocking capacitor Cr to block the circulating current, which can achieve ZVS of the leading bridge arm and ZCS of the lagging bridge arm in a wide load range, reducing the switch stress, reducing the loss and improving the working efficiency. The selection of Lr and Cr can refer to the reference [4]. The control part uses a fast and efficient DSP as the core controller, and drives the power switch tube in the main circuit through optocoupler isolation and a special driver chip EXB841 with IGBT self-protection. Cooperating with sampling circuit and protection circuit, it can realize real-time control of output, and has fast dynamic response speed and good output characteristics.
Figure 1 System structure diagram
4 Working Principle
Q1~Q4 form a full bridge, Q5 and Q6 form a cycloconverter. The driving waveform of the switch tube is shown in Figure 2.
Figure 2 Switch tube drive waveform
The whole working process can be divided into 4 stages, which are described below.
In the first stage, Q1 and Q4 are turned on
When Q1 and Q4 (with phase difference) are turned on and Q5 is turned on in advance, the energy on the DC side can be transmitted to the output end. At this time, the resonant inductor stores energy and Q5 is soft-turned on, reducing the switching loss. This is shown as ug5 in Figure 2.
Second stage resonance
Due to the resonance of the circuit's DC blocking capacitor and the resonant inductor (including the leakage inductance in the transformer), the energy stored in the inductor in the first stage is released. When the resonant current reaches zero, Q1 is turned off. In this stage, Q2 and Q4 are turned on, and Q5 is turned off after a delay, as shown in ug5 in Figure 2.
In the third stage, Q2 and Q3 are turned on
In this stage, Q6 is turned on in advance before Q2 and Q3 are turned on. When Q2 and Q3 (there is a dead zone between Q1 and Q2) are turned on, the energy on the DC side can be transferred to the output end, and Q6 is soft-turned on at this time, as shown in ug6 in Figure 2.
The fourth stage of resonance
The working principle is similar to that of the second stage. At this time, the current direction is opposite to that of the second stage. When the energy on the inductor is released, Q6 is turned off. At this time, one cycle ends and the next cycle begins.
As can be seen from Figure 1, no matter what the polarity of the transformer secondary voltage is, if Q5 is turned on and Q6 is turned off, the output terminal OUT1 is positive and OUT2 is negative; if Q6 is turned on and Q5 is turned off, OUT2 is positive and OUT1 is negative. Therefore, by controlling the turn-on sequence of Q5 and Q6, the polarity of the output terminal can be controlled, and a variety of waveforms can be obtained, such as AC, pulse and other waveforms. If you want to output the positive half cycle of the sine wave, PULS1 controls Q1, Q4, PULS2 controls Q2, Q3, and at the same time let Q5 and Q6 turn on accordingly in advance, then the positive half cycle of the sine wave can be output, as shown in Figure 3.
(a) Driving waveform
(b) Output waveform
Figure 3: Positive half cycle of output sine wave
To output the negative half cycle of the sine wave, it is only necessary to exchange the conduction sequence of Q5 and Q6, as shown in Figure 4.
(a)
(b)
Figure 4 Negative half cycle of output sine wave
5 Software Implementation
The processing speed of TMS320LF2407 is 30MIPS, and almost all instructions can be completed within a single cycle of 50ns. With its powerful instruction operation function, it is easy to implement various control algorithms and high-speed real-time sampling, which can improve the working efficiency of the system. In order to improve the dynamic quality of the system and reduce the static error of the system, a closed loop is used to realize the control of each power conversion link. 5.1 PWM wave output This paper adopts the regular sampling method with triangle wave as carrier to obtain rectangular waves of equal height and unequal width, i.e. pulses. The midpoint of each pulse corresponds to the midpoint of the corresponding triangle wave. At the negative peak moment tD of the triangle wave, the sinusoidal modulated wave is sampled to obtain point D. A horizontal straight line is drawn through point D and intersects the triangle wave at points A and B, respectively, as shown in Figure 5. Then we have δ = Tc (1 + sinωrtD) / 2
Figure 5 Regular sampling method for sampling triangular wave carrier According to this relationship, if there are N rectangular waves in one cycle, the duty cycle of the i-th rectangular wave is Dr=0.5+0.5sin(i*2π/N) By using the period and duty cycle to set the corresponding registers of the PWM circuit in TMS320LF2407, the required PWM pulse waveform can be obtained on PWMx (x=1, 2, 3, 4, 7, 8). These PWM pulses can be used to control the corresponding 6 switch tubes to output a sine waveform. It should be noted that the quality of the output sine wave is related to the discrete number of sine waves used for control. If the discrete number is larger, the output sine wave will be smoother, but the DSP calculation amount will be increased. On the contrary, the output will be worse. Therefore, for specific applications, it is necessary to select appropriate discrete values. Timers T1 and T3 are set to underflow and cycle matching interrupt modes, used as PWM output time bases, and work in continuous increase/decrease counting mode. 5.2 Real-time Sampling The 16-channel ADC conversion circuit integrated in TMS320LF2407 is used to realize voltage and current sampling (the minimum conversion time for each channel is 500ns). The sampling signal is converted into the 0-3.3V level required by the ADC of LF2407 through the sampling module MAX122. In one power frequency cycle, the sampling will be performed 200 times (the switching frequency is 20kHz). Once there is an impact load, the output current or voltage will be too high, so that the DSP can capture this mutation in time. The DSP will call the corresponding subroutine to handle overvoltage or overcurrent conditions to protect the normal operation of the entire circuit. Timer T2 is set to underflow and periodic interrupt mode, used as the control time base for ADC sampling, and works in continuous increase/decrease counting mode. 6 Experimental Results According to the above principles, an experimental system was preliminarily designed and achieved relatively good results. Its main technical parameters are listed in Table 1. Table 1 Main technical parameters
FIG6 shows the voltage on the DC blocking capacitor in the full-bridge circuit, and FIG7 shows the transformer primary side neutral point voltage and transformer primary side current waveforms.
Time: 5μs/div, Voltage: 2V/div, Figure 6 DC blocking capacitor voltage
Time: 5μs/div, Voltage: 150V/div, Current: 5A/div Figure 7 Primary side neutral point voltage and primary side current It can be seen that the switch tube in the full-bridge circuit achieves soft turn-on and soft turn-off under the resonance of the DC blocking capacitor and the saturated inductor. Figure 8 shows the output voltage waveform.
Figure 8 Output voltage waveform 7 Conclusion This paper introduces the circuit topology of phase-controlled cycloconverter based on DSP digital control, analyzes its working principle, and proposes the process of generating control signals. The experimental results prove the correctness of digital implementation and achieve good results. It is certain that the high-frequency chain cycloconverter implemented by digitalization has stronger advantages than the traditional inverter based on analog or analog and digital combination. Digitalization makes the system highly programmable, and it has advantages that traditional inverters cannot match in debugging, product updates or upgrades. |
5.1 PWM wave output
This paper adopts the regular sampling method with triangle wave as carrier to obtain rectangular waves of equal height and unequal width, i.e. pulses. The midpoint of each pulse corresponds to the midpoint of the corresponding triangle wave. At the negative peak moment tD of the triangle wave, the sinusoidal modulated wave is sampled to obtain point D. A horizontal straight line is drawn through point D and intersects the triangle wave at points A and B, respectively, as shown in Figure 5. Then we have
δ = Tc (1 + sinωrtD) / 2
Figure 5 Regular sampling method for sampling triangular wave carrier
According to this relationship, if there are N rectangular waves in one cycle, the duty cycle of the i-th rectangular wave is
Dr=0.5+0.5sin(i*2π/N)
By using the period and duty cycle to set the corresponding registers of the PWM circuit in TMS320LF2407, the required PWM pulse waveform can be obtained on PWMx (x=1, 2, 3, 4, 7, 8). These PWM pulses can be used to control the corresponding 6 switch tubes to output a sine waveform. It should be noted that the quality of the output sine wave is related to the discrete number of sine waves used for control. If the discrete number is larger, the output sine wave will be smoother, but the DSP calculation amount will be increased. On the contrary, the output will be worse. Therefore, for specific applications, it is necessary to select appropriate discrete values. Timers T1 and T3 are set to underflow and cycle matching interrupt modes, used as PWM output time bases, and work in continuous increase/decrease counting mode.
5.2 Real-time Sampling
The 16-channel ADC conversion circuit integrated in TMS320LF2407 is used to realize voltage and current sampling (the minimum conversion time for each channel is 500ns). The sampling signal is converted into the 0-3.3V level required by the ADC of LF2407 through the sampling module MAX122. In one power frequency cycle, the sampling will be performed 200 times (the switching frequency is 20kHz). Once there is an impact load, the output current or voltage will be too high, so that the DSP can capture this mutation in time. The DSP will call the corresponding subroutine to handle overvoltage or overcurrent conditions to protect the normal operation of the entire circuit. Timer T2 is set to underflow and periodic interrupt mode, used as the control time base for ADC sampling, and works in continuous increase/decrease counting mode.
6 Experimental Results
According to the above principles, an experimental system was preliminarily designed and achieved relatively good results. Its main technical parameters are listed in Table 1.
Table 1 Main technical parameters
FIG6 shows the voltage on the DC blocking capacitor in the full-bridge circuit, and FIG7 shows the transformer primary side neutral point voltage and transformer primary side current waveforms.
Time: 5μs/div, Voltage: 2V/div,
Figure 6 DC blocking capacitor voltage
Time: 5μs/div, Voltage: 150V/div, Current: 5A/div
Figure 7 Primary side neutral point voltage and primary side current
It can be seen that the switch tube in the full-bridge circuit achieves soft turn-on and soft turn-off under the resonance of the DC blocking capacitor and the saturated inductor. Figure 8 shows the output voltage waveform.
Figure 8 Output voltage waveform
7 Conclusion
This paper introduces the circuit topology of phase-controlled cycloconverter based on DSP digital control, analyzes its working principle, and proposes the process of generating control signals. The experimental results prove the correctness of digital implementation and achieve good results. It is certain that the high-frequency chain cycloconverter implemented by digitalization has stronger advantages than the traditional inverter based on analog or analog and digital combination. Digitalization makes the system highly programmable, and it has advantages that traditional inverters cannot match in debugging, product updates or upgrades.
Previous article:Design of a simple pure hardware grid-connected inverter
Next article:Grid-connected inverter anti-islanding test detection device
Recommended ReadingLatest update time:2024-11-16 16:55
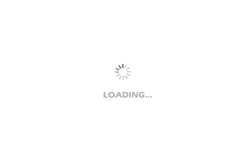
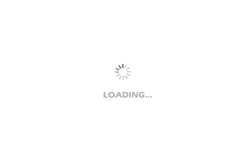
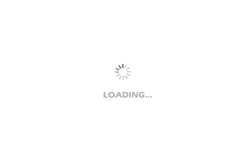
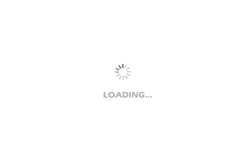
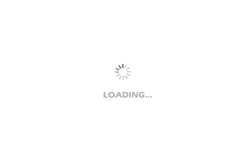
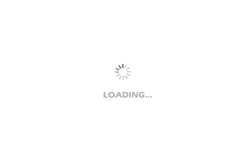
- Popular Resources
- Popular amplifiers
- MathWorks and NXP Collaborate to Launch Model-Based Design Toolbox for Battery Management Systems
- STMicroelectronics' advanced galvanically isolated gate driver STGAP3S provides flexible protection for IGBTs and SiC MOSFETs
- New diaphragm-free solid-state lithium battery technology is launched: the distance between the positive and negative electrodes is less than 0.000001 meters
- [“Source” Observe the Autumn Series] Application and testing of the next generation of semiconductor gallium oxide device photodetectors
- 采用自主设计封装,绝缘电阻显著提高!ROHM开发出更高电压xEV系统的SiC肖特基势垒二极管
- Will GaN replace SiC? PI's disruptive 1700V InnoMux2 is here to demonstrate
- From Isolation to the Third and a Half Generation: Understanding Naxinwei's Gate Driver IC in One Article
- The appeal of 48 V technology: importance, benefits and key factors in system-level applications
- Important breakthrough in recycling of used lithium-ion batteries
- Innolux's intelligent steer-by-wire solution makes cars smarter and safer
- 8051 MCU - Parity Check
- How to efficiently balance the sensitivity of tactile sensing interfaces
- What should I do if the servo motor shakes? What causes the servo motor to shake quickly?
- 【Brushless Motor】Analysis of three-phase BLDC motor and sharing of two popular development boards
- Midea Industrial Technology's subsidiaries Clou Electronics and Hekang New Energy jointly appeared at the Munich Battery Energy Storage Exhibition and Solar Energy Exhibition
- Guoxin Sichen | Application of ferroelectric memory PB85RS2MC in power battery management, with a capacity of 2M
- Analysis of common faults of frequency converter
- In a head-on competition with Qualcomm, what kind of cockpit products has Intel come up with?
- Dalian Rongke's all-vanadium liquid flow battery energy storage equipment industrialization project has entered the sprint stage before production
- Allegro MicroSystems Introduces Advanced Magnetic and Inductive Position Sensing Solutions at Electronica 2024
- Car key in the left hand, liveness detection radar in the right hand, UWB is imperative for cars!
- After a decade of rapid development, domestic CIS has entered the market
- Aegis Dagger Battery + Thor EM-i Super Hybrid, Geely New Energy has thrown out two "king bombs"
- A brief discussion on functional safety - fault, error, and failure
- In the smart car 2.0 cycle, these core industry chains are facing major opportunities!
- The United States and Japan are developing new batteries. CATL faces challenges? How should China's new energy battery industry respond?
- Murata launches high-precision 6-axis inertial sensor for automobiles
- Ford patents pre-charge alarm to help save costs and respond to emergencies
- New real-time microcontroller system from Texas Instruments enables smarter processing in automotive and industrial applications
- RP2040 components purchased from element14 event
- Flushing steps (smart toilet development record)
- How to speed up MobaXterm pasting
- Award-winning live broadcast | The new Infineon MOSFET based on Source-down technology effectively improves power density, which is visible to the naked eye
- Bike modification series: Modification buttons
- Hot Questions and Answers: What else can you do besides IT?
- Control design of intelligent car based on MSP430 single chip microcomputer
- About RX62T PWM output problem
- [GD32F310 Review] ADC Configuration and Use
- How to display animation?