The biggest advantages of the above-mentioned OLED TVs are fast picture response time, high contrast, low power consumption, ultra-thinness and wide viewing angle, etc. However, there is still a major obstacle to the mass production of large-size OLED displays required for TVs, namely the lack of technology that can be implemented to form a uniform film on a large-size substrate in order to effectively eliminate the brightness difference problem that has caused headaches in the past in the large-area organic electroluminescent (EL) panel manufacturing process.
The vacuum thermal evaporation (VTE) method currently used by most OLED products is to place a mask close to the substrate in a vacuum chamber to determine the type of material to be coated on the substrate. Since this method generates high temperatures during the evaporation process, the mask may be displaced, which can easily lead to uneven molding and low precision, resulting in uneven brightness.
Therefore, the industry began to look for alternative solutions, hoping to minimize the disadvantage of uneven brightness. Using a small inkjet print head to directly coat the OLED material on the panel is seen as an emerging solution. The method of manufacturing OLED products using inkjet technology generally sets multiple nozzles on the nozzle, but no matter how accurately the inkjet print head is manufactured, there will still be slight differences in the amount of ink in each nozzle. If it is not accurately adjusted, the thickness of the light-emitting layer will still be uneven during the film formation process, resulting in the occurrence of MURA (the phenomenon of uneven display brightness causing various traces). Even if the brightness unevenness has been reduced a lot, it can still be detected by the human eye, causing the panel to be classified as defective or inferior.
To improve the above phenomenon, the ink output and ink droplet placement must be more accurately controlled during the inkjet printing process. Epson proposed a solution to improve its micro-needle point piezoelectric inkjet technology originally used in general printers, accurately calculate the ink dosage and drop point distribution, and successfully improve the uniformity of OLED panel light emission.
Micro-needle piezoelectric inkjet improves MURA defects
Among the many factors that affect uniform light emission, the total amount of ink ejected each time is a very important variable. Since the thin film covered on the panel depends on the total amount of dissolved matter in the ink droplets and their degree of dispersion, and in order to achieve uniform film formation, the variation must be controlled within a range of less than 1%, so it is very important and complex to control the variation between each drop of ink. The way to measure this variation is to first apply different doses of ink dots on the substrate, wait for them to dry, and then measure the height and shape of each polymer dot to calculate the thickness difference. Figure 1 is an example of the difference in ink volume obtained using this method.
After obtaining the information of ink volume accuracy, the next problem to be faced is how to reduce the variation. By adjusting the input signal waveform of different print heads (Figure 2), the ink ejection volume of the print head can be controlled.
Figure 2 Waveform of the print head input signal
[page]
The industry has developed a smart dot control technology (VSDT) that can change the waveform of the nozzle voltage to allow the nozzle to eject three different sizes of ink dots, and then combine the different sizes of dots into a pixel. Usually, the amount of ink ejected by a nozzle at a time is about one billionth of a liter (pl), but if the pixel contains more ink before adjustment, the proportion of small dots must be increased, and vice versa, the proportion of large dots must be increased.
The above method can not only improve the printing accuracy (dose error less than 1%) and speed, but also eliminate the need for repeated measurement and adjustment operations. It can even achieve a frequency of only one correction every few months.
The test substrate mentioned above is a specially made test element group (TEG). This group uses inkjet technology in the five basic layers of the red, green and blue (RGB) three-color light-emitting layer (EML), hole transport layer (HTL) and intermediate layer (IL) that make up the light-emitting element (Figure 3), and then uses vacuum hot plating to process the electrode film forming part.
Figure 3 TEG structure diagram
[page]
The method to measure the results of ink volume control is to use an optical surface profiler to measure the system and pixel luminescence to compare the ink volume in the pixel space. Figures 4 and 5 compare the pixel luminescence and the amount of ink contained in the pixel without and with control, showing that the accuracy of the regulated system has been significantly improved in both aspects. The uneven brightness of the display panel has been reduced from an average of about 50% to only 4.7%, and the difference in film thickness after film formation has been reduced from the original 6% to less than 0.4%.
Figure 4: The amount of light emitted by each pixel
Figure 5: The amount of ink per pixel
Large OLED panels are unstoppable
[page]
由此可见,经过微针点压电技术及VSDT的修正,喷墨技术的误差标准已达可接受的范围。因此,产业界便以TEG为参考架构,实际製造出OLED面板。该面板以37吋的1,920×1,080(1080p)画素之规格生产,在经过切割后,成为便于生产的14吋OLED样本(图6)。关于该面板之详细规格,请参照表1。
Figure 6 14-inch OLED panel developed by Epson
Uneven brightness is a stumbling block for OLED TV commercialization
In summary, the inkjet process combined with micro-needle piezoelectric technology can successfully solve the problem of uniform film formation that has long troubled manufacturers, achieving extremely even coating and high production capacity, and is therefore regarded by the industry as a future star application of OLED display technology. In response, the industry is accelerating the development of low-molecular phosphorescent materials for printing purposes, hoping to extend the service life of the panel, and plans to apply this technology to the production of large panels in large quantities in two years, writing a new chapter in the OLED era.
Previous article:A brief analysis of the application and current status of P2P technology in Internet TV
Next article:faceVsion announces new HD webcam product
Recommended ReadingLatest update time:2024-11-16 22:01
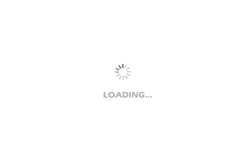
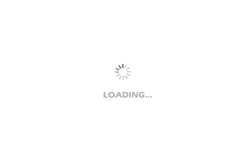
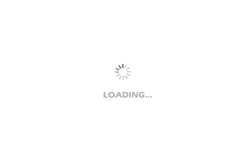
- Popular Resources
- Popular amplifiers
- Innovation is not limited to Meizhi, Welling will appear at the 2024 China Home Appliance Technology Conference
- Enjoy big-screen gaming anytime, anywhere: Making portable 4K UHD 240Hz gaming projector a reality
- AMD surpasses Intel: CPU shipments surge in Q3 this year
- Exynos is losing ground, Samsung plans to use Qualcomm chips in home appliances
- Intel and 50 partners unveiled a full range of 30 notebook and desktop AI PCs equipped with Intel Core Ultra (2nd Generation)
- Innovation leads the new trend of mobile refrigeration GMCC will present new products at 2024 CIAAR
- Lenovo and NVIDIA expand collaboration to jointly launch new liquid-cooled AI servers
- Ceiling fan solution based on XMC1302
- Gartner: Global AI PC shipments are expected to account for 43% of total PC shipments in 2025
- Innolux's intelligent steer-by-wire solution makes cars smarter and safer
- 8051 MCU - Parity Check
- How to efficiently balance the sensitivity of tactile sensing interfaces
- What should I do if the servo motor shakes? What causes the servo motor to shake quickly?
- 【Brushless Motor】Analysis of three-phase BLDC motor and sharing of two popular development boards
- Midea Industrial Technology's subsidiaries Clou Electronics and Hekang New Energy jointly appeared at the Munich Battery Energy Storage Exhibition and Solar Energy Exhibition
- Guoxin Sichen | Application of ferroelectric memory PB85RS2MC in power battery management, with a capacity of 2M
- Analysis of common faults of frequency converter
- In a head-on competition with Qualcomm, what kind of cockpit products has Intel come up with?
- Dalian Rongke's all-vanadium liquid flow battery energy storage equipment industrialization project has entered the sprint stage before production
- Allegro MicroSystems Introduces Advanced Magnetic and Inductive Position Sensing Solutions at Electronica 2024
- Car key in the left hand, liveness detection radar in the right hand, UWB is imperative for cars!
- After a decade of rapid development, domestic CIS has entered the market
- Aegis Dagger Battery + Thor EM-i Super Hybrid, Geely New Energy has thrown out two "king bombs"
- A brief discussion on functional safety - fault, error, and failure
- In the smart car 2.0 cycle, these core industry chains are facing major opportunities!
- The United States and Japan are developing new batteries. CATL faces challenges? How should China's new energy battery industry respond?
- Murata launches high-precision 6-axis inertial sensor for automobiles
- Ford patents pre-charge alarm to help save costs and respond to emergencies
- New real-time microcontroller system from Texas Instruments enables smarter processing in automotive and industrial applications
- 【NXP Rapid IoT Review】+⑦NXP Rapid IoT Review Summary
- Fluke and universities jointly build laboratories
- Can CAN bus load resistors be 0603 package chip resistors?
- Hardware Development Engineer 10-15K · 13 Salary Location: Tianjin
- Practical Circuit Diagrams and Schematic Diagrams of Frequency Converters
- MicroPython driver porting of LIS2MDL magnetic field sensor
- New application technologies in the Internet of Vehicles bring the required buffering to process the collection and transmission of information
- [MM32 eMiniBoard Review] Part 1: Unboxing
- IGBT DC voltage and current stabilizing power supply equipment solution requirements, seeking cooperation
- These tools can help you quickly understand ADI data converter products!