0 Introduction
The galvanometer scanning laser marking technology controls the deflection angle of two high-speed galvanometers to change the propagation direction of the laser, and focuses the laser on the workpiece surface through the F-Theata lens to mark the workpiece surface. Compared with traditional marking technology, it has a wide range of applications (suitable for processing surfaces of different materials and shapes), no mechanical deformation of the workpiece, no pollution, fast marking speed, good repeatability, high degree of automation, etc. It has a wide range of uses in many fields such as industry, national defense, and scientific research. High-speed and high-precision galvanometer marking has become the development direction of today's marking industry.
The traditional galvanometer marking control system is connected to the single-chip control board through the serial port and parallel port ISA bus of the PC. This method has a simple interface, convenient connection, and low development cost, but due to the low transmission speed, it can no longer meet the real-time requirements of modern CNC systems. This paper has made some new explorations in laser marking control technology: using the high-speed data transmission of PCI and the high-speed data processing capability of DSP, a "PC + PCI bus + DSP control board" method is proposed for the galvanometer marking control system, thereby achieving precise control of marking control, improving control efficiency, and ensuring system real-time performance. The DSP control board is the core of the entire system, which directly determines the scanning speed and scanning accuracy of the system. This paper will focus on the design of the control board.
1 DSP chip
The main chip of the DSP control board uses the high-speed data processing chip TMS320C6205 of the C6000 series of Texas Instruments. This chip is a high-performance fixed-point processor with a main frequency of up to 200MHz, which can execute 8 32-bit instructions per cycle and a processing speed of up to 1600MIPS; it adopts the high-performance VLIW structure TMS320C62xTM DSP core, has 8 independent functional units, 32 32-bit general registers; provides 64K bytes of internal program RAM and 64K bytes of internal data RAM; provides a 32-bit external memory seamless interface, including synchronous devices (such as SDRAM, SBSRAM, etc.), asynchronous devices (such as FLASH, SRAM, etc.) and addressable 52M bytes of external storage space; provides flexible PLL and clock generators, and can configure the multiplier value; provides a PCI bus interface that complies with the PCI 2.2 specification, directly realizing the bridging function between the chip and the PCI bus; provides two 32-bit timers; and provides a JTAG boundary scan interface for online debugging. The use of this chip can achieve high-speed data processing and ensure the real-time operation of the system. In addition, since it has a PCI bridge function and provides an interface with the PCI bus, it is economical and reliable.
2 Hardware Design
2.1 Structure diagram
As shown in Figure 1, the hardware structure block diagram of the system. The DSP control board is connected to the PC through the PCI bus to achieve high-speed communication. The DSP processing module is the main control module, and the TMS320C6205 chip with a main frequency of 200MHz is used as the main control chip. The DSP processing module makes full use of the fast computing power and high-precision timer of the C6000 series DSP to ensure that the galvanometer marking machine can mark at a uniform speed and high speed, which cannot be achieved by the PC. The peripheral circuit of the DSP includes a storage module, reset control, power control, clock system, JTAG port, digital-to-analog conversion module, CPLD logic control module and optoelectronic isolation module. The storage module includes a FLASH module and an SDRAM module. The FLASH is used to store the system startup code and software code, and the SDRAM is used to provide additional storage space required for software operation. The DSP control board outputs two analog quantities to control the movement of the two galvanometers, outputs a Q switch control signal to control the switching light of the laser, and inputs/outputs 16 optoelectronic isolation signals for function expansion.
2.2 Communication between PC and DSP
The PCI bus is a local bus that is not attached to a specific processor. Structurally, PCI is a first-level bus inserted between the CPU and the original system bus. A bridge circuit manages this layer and implements the interface between the upper and lower layers to coordinate data transmission. The manager provides signal buffering, enabling it to support 10 peripherals and maintain high performance at high clock frequencies. The PCI bus also supports bus mastering technology, allowing intelligent devices to obtain bus control when needed to speed up data transmission. Compared with the ISA bus, the PCI bus has the advantages of fast transmission speed and large transmission volume.
This system uses TMS320C6205, which has a PCI bus bridge function that complies with the PCI2.2 specification. Developers can avoid the hardware and software implementation of the PCI protocol, which brings convenience to system design, shortens the development cycle, and saves development costs. Developers only need to directly connect the bus signal on the PCI slot with the relevant PCI bus signal on the DSP chip. The DSP control board with "gold finger" can be directly inserted into the PCI card slot of the PC to realize communication between the PC and the DSP. PCI devices can access all internal RAM space, peripherals and external memory space.
The PCI bus width used by the DSP control board is 32 bits (3.3V), the bus frequency is 33MHz, and the transmission rate is 33×32/4MB/s = 132MB/s. This transmission rate provides a guarantee for the high-speed operation of the entire system.
2.3 CPLD Logic Control
The logic control of the entire high-speed system is realized by a high-speed CPLD chip. The MAX7128E chip of ALTERA is selected for implementation, with 2500 programmable logic gates, 128 macro cells, 8 logic array blocks, 100 user-definable I/O pins, and a pin-to-pin delay of 5ns. MAX7000 series devices can be programmed through a programmer or online. This design uses online programming (ISP). ISP allows quick and easy reprogramming during the design and development process, simplifies the production process, and allows the device to be assembled on the printed circuit board before programming.
In the system design, LED signal lights, FLASH, DA chip, 16-channel I/O optoelectronic isolation interface, analog switch, Q switch, PWM output, and software reset control all use the address of CE1 space. In order to prevent these devices from interfering with each other, the input address must be decoded. By judging the PA[2:6] and PA[16:21] input to the CPLD, we can know the address area that the DSP is accessing, and perform address decoding of the CE1 space, thereby generating corresponding control signals to achieve logic control and timing control.
The high addresses of the registers built on the CPLD are all the same, named dsp_reg_addr, and are composed of Pa16~21. If Pa16~21 is set to "111000", it means the address 0x0178xxxx.
The lower address is composed of Pa2~6, which addresses 10 registers. The address correspondence is shown in Table 1.
Table 1 Address allocation table
2.4 Digital-to-Analog Conversion Module
The digital-to-analog conversion module converts the digital signal processed by DSP into an analog signal to control the deflection of the two galvanometers. As the requirements for marking accuracy are getting higher and higher, the traditional 8-bit digital-to-analog converter can no longer meet the needs of users. Therefore, this system uses ADI's 16-bit high-precision digital-to-analog converter AD669 chip, as shown in Figure 2. AD669 has a 16-bit parallel input and a secondary data cache structure. In the design, the /L1 signal is directly grounded and set to be valid, and the first-level cache and the second-level cache are controlled by controlling the /CS and LDAC signals respectively. The voltage range of the control galvanometer signal is -10V~+10V. Taking the label with a size of 100mm×100mm as an example, the accuracy can reach 100mm/216=0.0015mm, and the corresponding minimum output voltage is 0.00031V.
Experiments have shown that when powered on, the output of the AD669 chip is an uncontrollable quantity, which will cause the galvanometer to deflect at the moment of power-on. If the deflection amplitude is too large, long-term use will cause the galvanometer to break. In order to protect the galvanometer, an analog switch circuit can be designed to control the output of the AD669 chip when powered on to 0V. The author places the analog switch at the reference voltage input terminal of the AD669 chip, and controls the analog switch through CPLD to control the presence or absence of the reference voltage, thereby ensuring that the galvanometer does not deflect when powered on.
3 PCB Design
The control board uses a high-speed DSP processing chip with a main frequency of 200MHz. In the high-speed signal system, there are EMC problems, which will affect the performance of the system. In order to design a stable control board with good anti-interference performance, the following measures were taken
1. Reasonable arrangement of board layers
The control board is a six-layer board, and the board layer design is (from top to bottom) signal layer-ground layer-power layer-signal layer-ground layer-signal layer. This board layer structure arrangement makes each signal layer and power layer close to a ground layer, providing a shorter return path for the signal.
2. Processing of clock signal lines
Half of the PCI clock signal is boosted by reflected waves, so the clock signal CLK routing length is approximately 2500 mil, and it is achieved by serpentine routing (this point is clearly stipulated in the routing requirements of the PCI2.2 specification). For DSP chips, the crystal oscillator circuit should be as close to the DSP chip as possible, and the clock signal should be as short as possible.
3. Processing of SDRAM related signal lines
The operating frequency of SDRAM is 100MHz. At high frequencies, the signal transmission time is directly related to the length of the signal routing, and this problem cannot be ignored. Therefore, the data line and address line of SDRAM should be routed with equal length to ensure the quality of signal transmission. In addition, crosstalk and ringing problems are also very likely to occur at high frequencies. For the control signals and data and address bus signals of the SDRAM and DSP interface, matching resistors are connected in series at the source end to improve the signal transmission quality and ensure that SDRAM can work normally at high frequencies.
4. Isolation of digital and analog circuits
The control board has digital circuits and analog circuits. When laying out, the isolation of digital and analog circuits must be considered. Try to separate the digital circuits and analog circuits to avoid digital signal routing across the analog circuit area to prevent mutual interference between the two circuits. In addition, the digital circuit and analog circuit share a common ground through a 0 ohm resistor.
5. Use of capacitors
Place a 1.01uF decoupling capacitor next to the power pin of each digital chip.
4 Conclusion
This system combines the high-speed PCI bus with the C6000 high-speed DSP processor, equipped with a high-precision digital-to-analog conversion module, to achieve a high-speed and high-precision control system, and successfully applied it to the galvanometer laser marking system. The system makes full use of the high-speed processing capability of the DSP and the internal high-precision timer, sharing the real-time tasks of the PC, thereby achieving the complementary advantages of the PC and the DSP control board, achieving real-time marking, and ensuring the uniformity of the marking quality. This article also gives the points to note for the DSP control board in the PCB design stage. The board has been put into use in actual production and has good stability and anti-interference.
Previous article:Interface Technology between Image Processor 6538 and 8031
Next article:Design of communication system baseband verification platform based on FPGA
Recommended ReadingLatest update time:2024-11-16 17:27
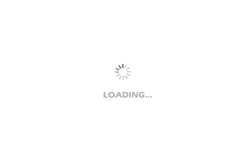
- Popular Resources
- Popular amplifiers
- Huawei's Strategic Department Director Gai Gang: The cumulative installed base of open source Euler operating system exceeds 10 million sets
- Analysis of the application of several common contact parts in high-voltage connectors of new energy vehicles
- Wiring harness durability test and contact voltage drop test method
- Sn-doped CuO nanostructure-based ethanol gas sensor for real-time drunk driving detection in vehicles
- Design considerations for automotive battery wiring harness
- Do you know all the various motors commonly used in automotive electronics?
- What are the functions of the Internet of Vehicles? What are the uses and benefits of the Internet of Vehicles?
- Power Inverter - A critical safety system for electric vehicles
- Analysis of the information security mechanism of AUTOSAR, the automotive embedded software framework
Professor at Beihang University, dedicated to promoting microcontrollers and embedded systems for over 20 years.
- Innolux's intelligent steer-by-wire solution makes cars smarter and safer
- 8051 MCU - Parity Check
- How to efficiently balance the sensitivity of tactile sensing interfaces
- What should I do if the servo motor shakes? What causes the servo motor to shake quickly?
- 【Brushless Motor】Analysis of three-phase BLDC motor and sharing of two popular development boards
- Midea Industrial Technology's subsidiaries Clou Electronics and Hekang New Energy jointly appeared at the Munich Battery Energy Storage Exhibition and Solar Energy Exhibition
- Guoxin Sichen | Application of ferroelectric memory PB85RS2MC in power battery management, with a capacity of 2M
- Analysis of common faults of frequency converter
- In a head-on competition with Qualcomm, what kind of cockpit products has Intel come up with?
- Dalian Rongke's all-vanadium liquid flow battery energy storage equipment industrialization project has entered the sprint stage before production
- Allegro MicroSystems Introduces Advanced Magnetic and Inductive Position Sensing Solutions at Electronica 2024
- Car key in the left hand, liveness detection radar in the right hand, UWB is imperative for cars!
- After a decade of rapid development, domestic CIS has entered the market
- Aegis Dagger Battery + Thor EM-i Super Hybrid, Geely New Energy has thrown out two "king bombs"
- A brief discussion on functional safety - fault, error, and failure
- In the smart car 2.0 cycle, these core industry chains are facing major opportunities!
- The United States and Japan are developing new batteries. CATL faces challenges? How should China's new energy battery industry respond?
- Murata launches high-precision 6-axis inertial sensor for automobiles
- Ford patents pre-charge alarm to help save costs and respond to emergencies
- New real-time microcontroller system from Texas Instruments enables smarter processing in automotive and industrial applications
- FAQ_ How to implement RX-TX switching control
- Thank you for being there + bow deeply
- How to view the complex technical documentation of TI DSP
- Please help analyze this circuit.
- kicad-eda_6-layer-pcb_A64-OlinuXino_Rev_D
- The wheel speed pulse signal of the car is too narrow, and the sampling frequency of the equipment is too low to collect it. Is there any way to extend the pulse width?
- Battery Test Equipment --- Signal Chain
- iTOP-4418 development board TF card burning-boot uboot
- LSM6DSL cannot generate interrupts, WAKE_UP_SRC is always 0; changing CTRL1_XL doubles the Z-axis reading
- MSP432 learning experience: system tick timer