Overview
This reference design uses the MAX16823 3-channel linear LED driver and an external BJT to implement a 3S3P RCL driver circuit. Figures 1 and 2 show the PCB and heat sink installed; Figure 3 shows the reference design board layout; and Figure 4 shows the reference design schematic.
The following is a detailed discussion of the reference design, providing analysis of the main functional circuits, design specifications, and test data.
Figure 1. PCB and heat sink installed
Figure 2. Side view with heat sink installed
Figure 3. LED driver wiring
Figure 4.
LED driver
schematic
Design Analysis
The reference design consists of four circuits: input protection circuit and input selector, 10% duty cycle generator, load dump and double battery detection, and LED drive circuit.
Input protection
Input protection is mainly provided by metal oxide varistors MOV1 and MOV2. In the design, we used Littelfuse's V18MLA1210H (EPCOS also provides high-quality MOV devices). MOVs with different joule ratings are selected according to the specific application environment.
Input Selector
After the input voltage is established, the input selector switches power to the taillight node unless a valid power source is applied to the brake/turn input. Once the power source is supplied to the brake/turn input, the input selector automatically blocks the taillight input current. This architecture will provide 600mA current to the brake/turn input, indicating RCL function. When the LED driver fails or the LED itself fails, the MAX16823 will completely shut down all LEDs, and less than 5mA of current will flow out of the brake/turn signal. The output stage circuit of the lamp can successfully detect this low current and issue an alarm signal as required by the design.
D5 and R16 form a detection circuit. This detection circuit turns on Q4 when the taillight input node voltage is 9V or higher and the brake/turn input node is grounded or high impedance. The input voltage is loaded to VIN through diode D3 to provide the main power supply for the LED driver. When the brake/turn input voltage reaches within 2V of the taillight voltage, Q4 is turned off and VIN is powered through diode D4. R17 provides a 2.1kΩ resistor to ground to ensure maximum impedance at this node. R17 has a power of 270mW under dual battery conditions (24V), so a 0.5W resistor must be selected. The main limitation of this circuit is that when the brake/turn input voltage and taillight are operating simultaneously, it is assumed that the difference between the brake/turn input voltage and the taillight input voltage is within 2V.
10% Duty Cycle Generator
The 10% duty cycle generator generates a square wave signal with a duty cycle of 10%, which is sent to the MAX16823 LED driver to adjust the LED brightness. The dimming circuit will work effectively as long as the taillight input provides a valid voltage. R10 and D2 provide a 5.1V regulated source for powering U3 (ICM7555ISA). Under dual battery conditions, R10 must be selected as a 0.25W resistor because the power consumption may reach 44mW. Timer U3 is configured as an astable oscillator. The on-time is determined by the time C6 is charged through D1 and R11 (t ON = 0.693 × R11 × C6 = 0.418ms [typical]); the off-time is determined by the time C6 is discharged through R12 (t OFF = 0.693 × R12 × C6 = 3.8ms [typical]). The sum of the on-time and the off-time constitutes a square wave signal with a period of approximately 237 Hz and a duty cycle of 9.9%. FIG5 shows the duty cycle.
Resistor R13 provides current limiting protection to reduce EMI radiation that may be generated by this switch node. R13 should be physically located as close to U3 as possible to reduce EMI. A 10% duty cycle square wave signal is coupled to U1 through D7 and R14. D7 provides a logical OR circuit that allows the 10% duty cycle pulse to pass as long as there is no valid power to the brake/turn signal. This configuration provides low LED brightness when there is a supply voltage applied to the tail light input. When a valid voltage is applied to the brake/turn signal input, D7 provides voltage to the DIM1, DIM2, and DIM3 inputs to achieve 100% LED brightness (high LED brightness). Because the LEDGOOD signal cannot exceed 6V, resistor R14 limits the current to less than 2mA, and D9 and D2 provide voltage clamps to prevent excessive node voltages. Resistor R15 is a pull-down resistor when there is no voltage applied to the anode of D7. With a 400kΩ resistor, R15 will keep the DIM node voltage below 0.6V, sinking 1.5µA—much less than the 0.1µA sourced by the DIM input.
Figure 5. Oscillator output.
[page]
Load Dump and Double Battery Detection
The load dump and double battery detection circuits determine if the OR logic input voltage exceeds 21V. An input voltage exceeding 21V means a load dump (400ms) or double battery condition (unlimited time) has occurred, which will cause excessive power dissipation in the three LED driver transistors. Therefore, the detection circuit pulls the DIMx input low, turning off the output driver. In addition, the detection circuit pulls the LGC capacitor (C2) low to avoid possible false detection. Since the DIMx and LGC pin voltages are controlled within 10V, the voltage ratings of Q5 and D6 are not critical. The detection voltage is the sum of the breakdown voltage of D8 and the voltage of R18 to ground, which is approximately 22V. With a resistance of 20kΩ, R9 will generate a bypass leakage current of 20µA before Q5 turns on.
LED Driver for 3S3P RCL
The core IC of the reference design is the MAX16823ATE LED driver, with an input voltage of up to 45V at the IN pin. The IC provides current from the OUTx pin to drive the LED. Using a current-sense resistor to sense the current, the MAX16823 adjusts the output current of the OUTx pin to keep the voltage of the CS pin at 203mV as needed. Because each output channel of the IC itself can only provide 70mA output, we add external drivers to each string of LEDs to provide 200mA drive current for each string of LEDs and help solve the heat dissipation problem. Transistors Q1, Q2, and Q3 (ZXT690BKTC) provide the required current gain. These transistors are available in TO-262 packages to provide good heat dissipation for the die.
Q1, Q2, and Q3 are 45V, 2A transistors with a saturation voltage drop V CE(Sat) of less than 200mV when the I C /I B gain is 200 times . Because the voltage difference between the minimum input voltage (9V) and the maximum on-voltage of the LED string (3 × 2.65V = 7.95V) is only 1.05V, the V CE(Sat) rating is very important, and sufficient design margin must be left to meet the voltage drop of Q4 and D3, as well as the V CE(Sat) requirements of Q1, Q2, and Q3 . Please refer to the data sheet for details.
The resistor divider network R1/R2, R3/R4, and R5/R6 ensures that the output current of each OUTx is not less than 5mA, thus ensuring stable operation of the IC. In the design step, the minimum and maximum values of the transistor base current are analyzed. These currents flow through resistors R1, R3, and R5. The sum of the resistor voltage drop, the transistor's V BE , and the current-sense resistor voltage drop is the voltage across R2, R4, and R6. These resistors are selected so that the sum of the current flowing through the resistor and the transistor base current is not less than 5mA. On the other hand, the output current of OUTx must be less than 70mA (rated current). Please refer to the data sheet for details.
Heat dissipation considerations
The power dissipated by the pass transistor in this design reaches 6W. In order to reduce the temperature rise of the transistor, the transistor pad is connected to the bottom layer of the PCB through multiple vias, and the heat is transferred to the aluminum heat sink through an electrically insulating (but thermally conductive) adhesive pad. The heat sink itself rises by 31°C when dissipating 6W of power. Although Zetex's transistors do not provide the thermal resistance from junction to case, the thermal resistance of the TO-262 package provided by other transistor suppliers can be referenced, which is about 3.4°C/W. This thermal resistance means that the temperature inside each transistor will be 5.4°C higher than the case. In short, under the worst operating conditions, the junction temperature is 35°C to 40°C higher than the ambient temperature. The actual temperature measured in this reference design is about 30°C higher.
Transient response
Figures 6
and
7
show the transient response of the transistor when the taillight is powered. During the test, the oscillator outputs a pulse signal with a 10% duty cycle to pulse-width modulate the MAX16823 to drive the external transistor on/off; the undershoot in Figure 6 lasts for 3µs, and the overshoot in Figure 7 lasts for 100µs, which does not cause any problems.
Figure 6. Q1 collector waveform when the transistor is on (V
IN
= 12.5V)
Figure 7. Q1 collector waveform when the transistor is off (V
IN
= 12.5V)
Previous article:Freescale Body Control Module (BCM) Solutions
Next article:A car door lock hardware and software design based on fingerprint recognition technology
Recommended ReadingLatest update time:2024-11-16 20:27
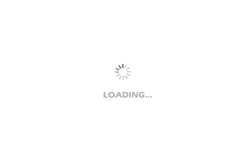
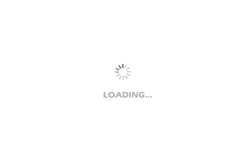
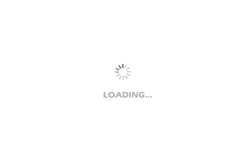
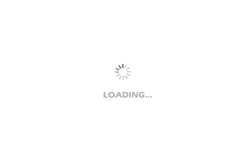
- Popular Resources
- Popular amplifiers
-
MCU C language programming and Proteus simulation technology (Xu Aijun)
-
100 Examples of Microcontroller C Language Applications (with CD-ROM, 3rd Edition) (Wang Huiliang, Wang Dongfeng, Dong Guanqiang)
-
Research on three-phase all-solid-state high-efficiency LED tunnel lighting system based on chip drive_Li Jian
-
Follow me Season 2 Episode 1 All Code + Library
- Car key in the left hand, liveness detection radar in the right hand, UWB is imperative for cars!
- After a decade of rapid development, domestic CIS has entered the market
- Aegis Dagger Battery + Thor EM-i Super Hybrid, Geely New Energy has thrown out two "king bombs"
- A brief discussion on functional safety - fault, error, and failure
- In the smart car 2.0 cycle, these core industry chains are facing major opportunities!
- The United States and Japan are developing new batteries. CATL faces challenges? How should China's new energy battery industry respond?
- Murata launches high-precision 6-axis inertial sensor for automobiles
- Ford patents pre-charge alarm to help save costs and respond to emergencies
- New real-time microcontroller system from Texas Instruments enables smarter processing in automotive and industrial applications
- Innolux's intelligent steer-by-wire solution makes cars smarter and safer
- 8051 MCU - Parity Check
- How to efficiently balance the sensitivity of tactile sensing interfaces
- What should I do if the servo motor shakes? What causes the servo motor to shake quickly?
- 【Brushless Motor】Analysis of three-phase BLDC motor and sharing of two popular development boards
- Midea Industrial Technology's subsidiaries Clou Electronics and Hekang New Energy jointly appeared at the Munich Battery Energy Storage Exhibition and Solar Energy Exhibition
- Guoxin Sichen | Application of ferroelectric memory PB85RS2MC in power battery management, with a capacity of 2M
- Analysis of common faults of frequency converter
- In a head-on competition with Qualcomm, what kind of cockpit products has Intel come up with?
- Dalian Rongke's all-vanadium liquid flow battery energy storage equipment industrialization project has entered the sprint stage before production
- Allegro MicroSystems Introduces Advanced Magnetic and Inductive Position Sensing Solutions at Electronica 2024
- Car key in the left hand, liveness detection radar in the right hand, UWB is imperative for cars!
- After a decade of rapid development, domestic CIS has entered the market
- Aegis Dagger Battery + Thor EM-i Super Hybrid, Geely New Energy has thrown out two "king bombs"
- A brief discussion on functional safety - fault, error, and failure
- In the smart car 2.0 cycle, these core industry chains are facing major opportunities!
- The United States and Japan are developing new batteries. CATL faces challenges? How should China's new energy battery industry respond?
- Murata launches high-precision 6-axis inertial sensor for automobiles
- Ford patents pre-charge alarm to help save costs and respond to emergencies
- New real-time microcontroller system from Texas Instruments enables smarter processing in automotive and industrial applications
- TI Engineer's Annual Review: Processors (Hot Products: MSP430, C2000, C6000 Multicore, etc.) Selected Q&A
- How to choose an analog-to-digital converter?
- [Project source code] FPGA-based asynchronous FIFO show-ahead mode
- [Construction Monitoring and Security System] XIV. Realization of the core functions of the project
- Is the Linux interrupt handling process global or local interrupts?
- Commonly used surge suppression devices
- Or is it a buck-boost problem? Please ask the teachers
- RSL10-002GEVB power management node design
- How to measure current ranging from 1uA to 1.5A
- Analysis and application of four common constant current source circuits