Definition and classification
With the in-depth development of power electronics technology, the electronic control system has changed from a low-power and low-voltage auxiliary electrical device for traditional automobiles to an energy-saving, environmentally friendly, high-efficiency and low-noise electrical transmission electrical device for new energy vehicles.
Definition of New Energy Vehicle Electronic Control System
The electric control system of new energy vehicles is a device that controls the vehicle's drive motor. In new energy vehicles, due to the application of power electronics technology, its electrical system has undergone tremendous changes, from low-power and low-voltage auxiliary electrical devices of traditional vehicles to energy-saving, environmentally friendly, high-efficiency and low-noise electrical transmission electrical devices of new energy vehicles. It has become a substitute for traditional automobile engines and gearboxes, and directly determines the main performance indicators of pure electric vehicles such as climbing, acceleration and maximum speed.
Classification of electronic control systems for new energy vehicles
The electronic control system of new energy vehicles can be divided into the main controller and the auxiliary controller:
(1) Main controller: controls the vehicle's drive motor, that is, by receiving control information transmitted by the vehicle controller and control mechanisms such as the brake pedal, accelerator pedal, and shift mechanism, it controls the motor torque, speed, and direction of the drive motor, and can also control the voltage and current output of the power battery accordingly;
(2) Auxiliary controller: controls the vehicle's power steering pump motor, air conditioning motor, and BSG (an all-in-one machine that uses belt drive to combine starting and power generation) motor.
At the same time, the design and calibration of the electric control system of new energy vehicles are highly related to the motor system. Based on the different matching motors, the electric control system needs to develop different technical platforms:
(1) Early DC motors were generally controlled by pulse width modulation (PWM) chopping control, which was a relatively simple control technology and had limited applications;
(2) With the widespread application of AC asynchronous motors and permanent magnet synchronous motors, the complexity of electronic control systems has increased rapidly, and vector control technology and direct torque control technology have become the mainstream technologies of electronic control products. In addition, the popularization of pure electric passenger vehicles will gradually increase the demand for the integration of drive motors and electronic control systems.
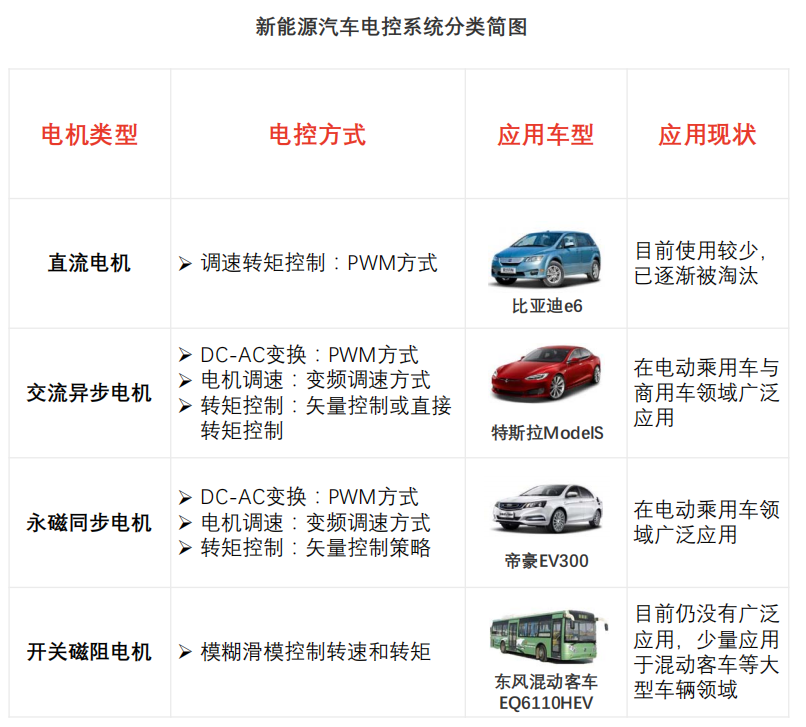
System composition and core technology
As the power conversion unit connecting the battery and the drive motor in new energy vehicles, the electronic control system is the core of motor drive and control.
Electronic control system composition
The electric control system of new energy vehicles is mainly composed of inverters, drivers, power modules, controllers, protection modules, cooling system signal detection modules and other components. Among them, the inverter, driver and controller are the core components of the electric control system:
(1) Inverter: controls the current of the drive motor and is mainly composed of IGBT (insulated gate bipolar transistor) power modules;
(2) Startup module: converts the microcontroller's control signal to the motor into a drive signal for the power inverter, and isolates the power signal from the control signal;
(3) Controller: mainly includes microprocessor and its minimum system, which is the monitoring circuit of motor current, voltage and other status, protection circuit and communication circuit for data exchange with external control units such as controller and battery management system. Control software implements corresponding control algorithms according to the characteristics of different types of motors.
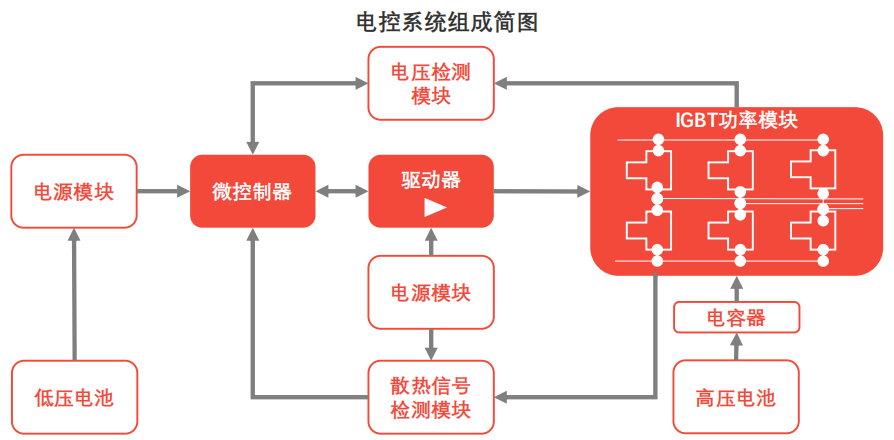
Application of electronic control system in new energy vehicles In new energy vehicles, batteries are the basic energy and power source, the drive motor converts this on-board energy into driving power, and the electronic control system controls the operation and power output of the entire vehicle. During the driving process of the vehicle, the inverter receives the DC power transmitted by the battery and inverts it into three-phase AC power to provide power to the vehicle drive motor, and the controller receives the drive motor speed, torque and other signals and feeds them back to the instrument. When there is an acceleration or braking behavior instruction, the controller controls the frequency of the inverter to increase or decrease, thereby achieving the purpose of acceleration or deceleration.
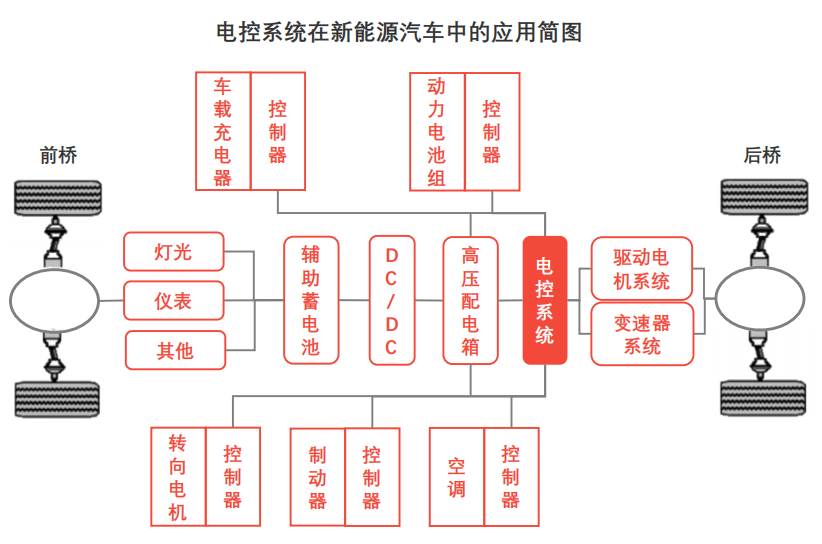
New energy vehicle electronic control systems must have high control accuracy, high dynamic response rate, and provide sufficient safety and reliability
Analysis of core technologies of electronic control system
The electronic control system of new energy vehicles needs to adapt to frequent start-stop and acceleration and deceleration, high torque at low speed and high torque at high speed, and has a large speed range. The electronic control system of hybrid vehicles also needs to handle special functions such as drive motor starting, power generation, and brake energy feedback. Therefore, the electronic control system of new energy vehicles needs to have high control accuracy, high dynamic response rate, and provide high safety and reliability, and its technology and manufacturing level directly affect the performance of the vehicle.
As a key technology of the electronic control system of new energy vehicles, IGBT power module must not only meet the vehicle's power performance indicators, but also have appropriate power electronic circuit design and selection, a fully functional control circuit architecture, reliable electromagnetic compatibility and heat dissipation capabilities, etc., to ensure the long-term stable operation of the electronic control system.
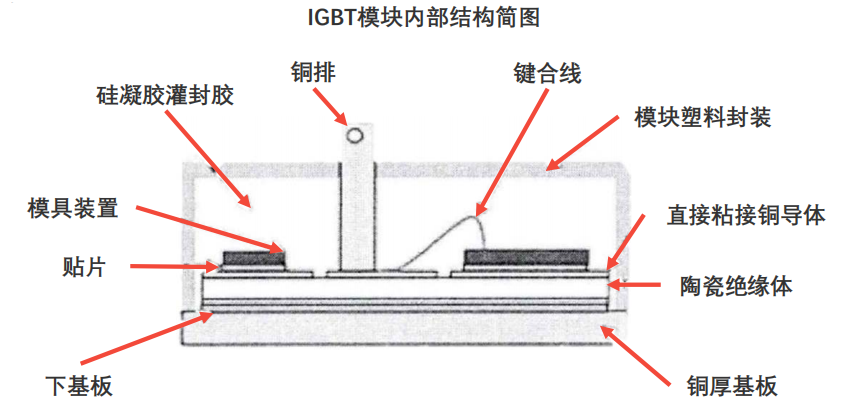
Demand for IGBT power modules in new energy vehicle electronic control systems
Compared with traditional internal combustion engine vehicles, new energy vehicles have more complex operating conditions, resulting in a harsh internal environment of their electronic control systems and extremely high internal temperature rises. Therefore, the operating temperature range of automotive-grade IGBT power modules must reach -40-125°C. As the main power conversion component of the electronic control system, the IGBT power module is in high-load operation for a long time, and its internal chip temperature can reach 50-80°C. At present, in the automotive industry, IGBT power modules need to pass a series of tests and design verifications such as thermal cycles, thermal shocks, and power cycles to ensure the reliability and heat dissipation of the modules.
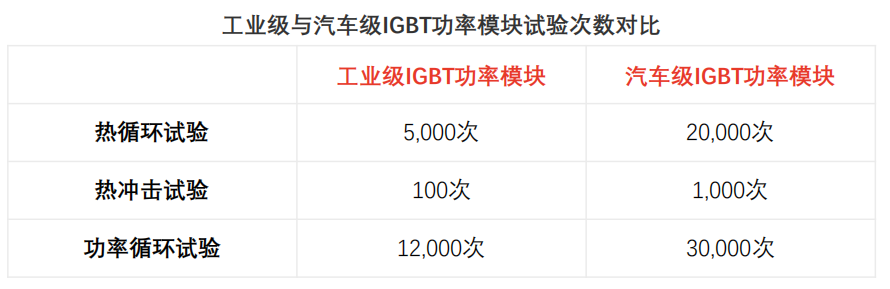
Analysis of IGBT power module packaging technology
At present, the packaging technology of IGBT power modules is mainly divided into single-tube and double-tube forms:
(1) Single-tube form: 62mm classic package, mainly used for industrial inverters. The single-tube form uses small-capacity IGBTs in series and parallel to achieve large-capacity application requirements. A single inverter requires a combination of 6 modules;
(2) Dual-tube form: Mainly used in photovoltaic power generation inverters and electric vehicle inverters, it can effectively reduce the size of the electronic control system, and has strong versatility and low overall cost.
development path
With the in-depth development of automatic control theory, power electronics technology, and computer control technology, the electronic control system devices are developing rapidly, and the expansion of the new energy vehicle market has driven the rise of the automotive electronic control system industry.
Infancy (1930-1947): The first appearance of automotive electronic technology was the vacuum tube radio installed in passenger cars in the early 1930s. However, due to the disadvantages of vacuum tube radios such as poor shock resistance, large size, and high power consumption, they became the main obstacle to their promotion and application in automobiles;
Exploration period (1948-1966): The invention of the transistor in 1948 and the emergence of the first integrated circuit in 1958 ushered in a new era of automotive electronic technology. Since the 1960s, semiconductor components have been used in passenger cars, and silicon diodes have been used as power transistors to replace the original voltage regulators and other electromagnetic contactors, which has greatly improved the performance and reliability of the car;
Development period (1967-1979): In 1967, integrated circuit components were first used in automobiles, combining electronic technology with automobile engine electrical systems to develop automobile generator integrated circuit voltage regulators, integrated circuit igniters and other automotive electronic products. In the same year, Chrysler Corporation of the United States equipped its cars with electronically controlled ignition devices, while Bosch of Germany developed electronically controlled fuel injection devices, marking the initial development of automobile electronic control systems as auxiliary electrical devices for traditional internal combustion engine vehicles;
Rapid development period (1980-1999): Since the mid-to-late 1980s, thyristor rectifiers have gradually replaced mercury rectifiers in DC motors, making a huge leap in DC electric drive technology. At the same time, control circuits have also achieved high integration, miniaturization, high reliability and low cost, which has greatly improved the performance indicators of DC motor speed control systems, expanded the scope of application, and rapidly developed DC motor speed control technology;
Mature stage (2000 to present): After entering the 21st century, with the development of computer and microelectronics technology and the continuous emergence of new power electronic power devices, the control strategy of electric motors has undergone tremendous changes, and the frequency conversion technology and pulse width modulation technology have become more mature. In addition, the breakthrough of permanent magnet material technology and the combination of microelectronics technology have produced permanent magnet synchronous motors, which have been widely used in the automotive field with their performance advantages, driving the electronic control system to gradually extend advanced control algorithms with microprocessors and sensors, and fully controlled power devices MOSFET and IGBT have gradually become mainstream.
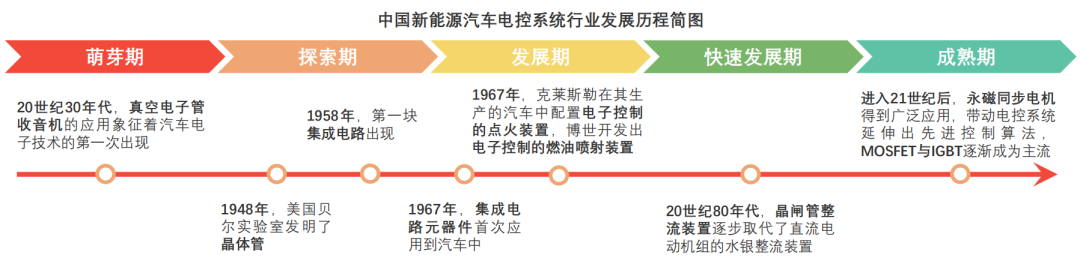
Industrial Chain
The various links in the new energy vehicle electronic control system industry chain are closely connected, but the industry is squeezed by upstream and downstream, and the competition within the industry is fierce.
The industrial chain of China's new energy vehicle electronic control system industry is composed of upstream electronic component suppliers, midstream new energy vehicle electronic control system integrators and downstream new energy vehicle OEMs.
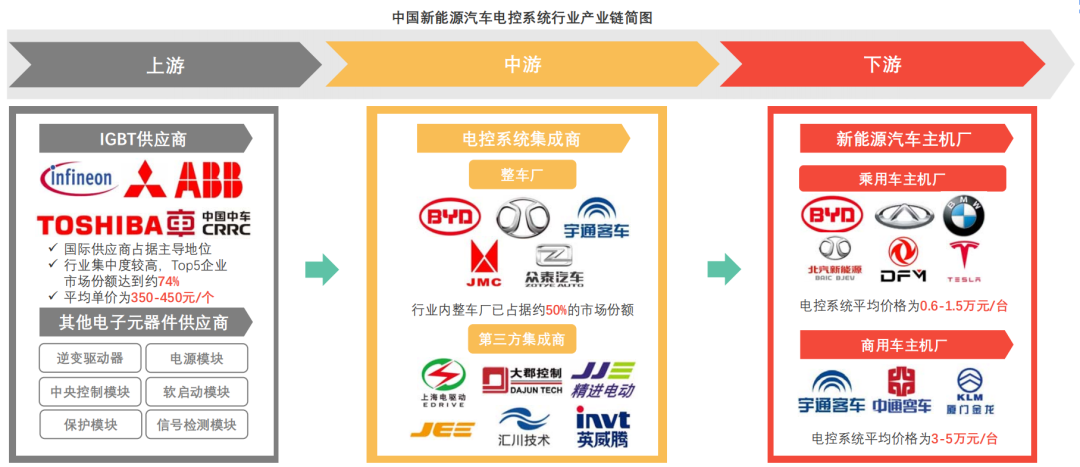
Upstream analysis of the industry chain
China's IGBT industry started late, and most companies still do not have independent production capabilities. The market is still dominated by international suppliers.
Analysis of upstream IGBT suppliers
IGBT is a composite fully controlled voltage-driven power semiconductor device composed of BJT (bipolar junction transistor) and MOS (insulated gate field effect transistor), with excellent performances such as high frequency, high voltage and high current. In the past five years, with the rapid development of China's economy, IGBT has been widely used in key areas such as daily consumption, industrial manufacturing, power transmission and distribution, transportation, aerospace, etc.
In new energy vehicles, IGBT is used in inverters, accounting for 40-50% of the total cost of the entire new energy vehicle electronic control system. At present, the Chinese IGBT market is still dominated by international suppliers such as Infineon, ABB, Mitsubishi, Toshiba, and Fuji. At the same time, the IGBT industry has a high market concentration, with the world's top 5 suppliers accounting for 74% of the total market share.
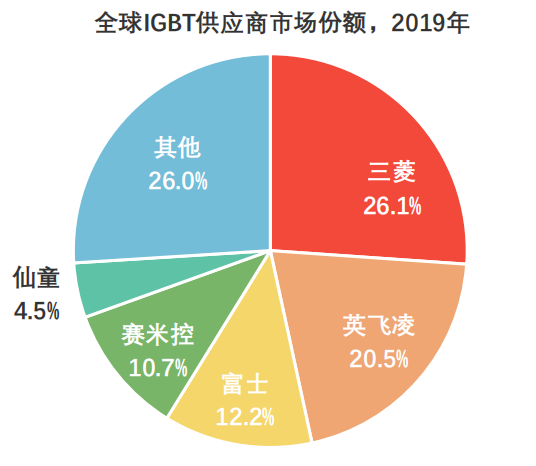
Analysis of the current status of China's IGBT industry
The development of technology and industrialization of China's IGBT industry is relatively late, and the industry's technical threshold is high and the capital investment is large, resulting in about 90% of IGBT products in the Chinese market currently relying on imports. There are a small number of companies engaged in the assembly of small and medium-power IGBT products in China, but they have not yet formed a scale. In terms of high-power IGBT module packaging technology, only a few companies have mastered it. In terms of IGBT chip technology and later system applications, China's only local company, CRRC, has fully mastered IGBT chip technology research and development, module packaging testing and system applications.
Driven by China's national policies and driven by the market, China's IGBT industry has developed rapidly and has gradually formed a complete IGBT industry chain of IDM model and foundry model, further promoting the localization process of IGBT.
(1) In terms of IGBT chip technology: China's leading IGBT suppliers, represented by CRRC, have built the world's second and China's first 8-inch IGBT chip professional production line, with an annual output of 120,000 pieces and supporting automated packaging and testing capabilities to produce 1 million IGBT modules per year. The chip and module voltage range is fully covered from 650-6,500V, and the first batch of 8-inch 1,700V IGBT chips have been successfully rolled off the production line. The 8-inch 3,300V chips have been trial-produced and tested.
(2) In terms of IGBT module technology: The chips used to package IGBT modules are still provided by international suppliers such as Infineon and ABB.
As the core electronic component of the electric control system of new energy vehicles, the cost of IGBT directly determines the room for reducing the total cost of the electric control system. However, as the development of domestic IGBT products in China is not yet mature, midstream electric control system integrators need to purchase IGBT products from overseas, and their bargaining power is relatively low.
Analysis of midstream of the industry chain
IGBT, a key component of China's new energy vehicle electronic control system, is still dependent on imports, and upstream suppliers have a high market concentration, resulting in high component procurement costs for electronic control system integrators.
Analysis of China's new energy vehicle electronic control system industry
The development of new energy vehicle electronic control systems includes software and hardware design and integration. The core software is usually developed by downstream vehicle manufacturers, while the hardware and underlying driver software can be provided by automotive parts suppliers. At present, the industry competitors are mainly composed of vehicle manufacturers such as BYD and BAIC New Energy and third-party professional new energy vehicle electronic control system integrators such as Huichuan Technology and Shanghai Electric Drive. At the same time, vehicle manufacturers represented by BYD can not only realize the self-production and self-use of electronic control systems, but also meet the equipment needs of other vehicle manufacturers, and have occupied about 45% of the industry's market share.
Analysis on the production model of new energy vehicle electronic control system integrators
New energy vehicle electronic control system integrators in the industry mostly adopt a production plan that combines order-based production with stock-based production, and a production model that combines independent production with outsourced processing.
(1) Production according to orders and production according to stock: New energy vehicle electronic control system integrators give priority to the production of ordered products to ensure the timeliness of supply and the effective use of operating resources. When order demand is met and there is surplus production capacity, they will arrange stocking according to the characteristics of the off-season and peak-season sales of various products to maintain a reasonable inventory, thereby solving the problem of insufficient production capacity when orders are concentrated;
(2) Self-production and outsourcing: New energy vehicle electronic control system products are composed of many electronic components and accessories. Electronic control system integrators are mainly responsible for the core links in the production process, such as drawing design, circuit board protection, software burning, assembly, testing and inspection. As for electronic processing links such as patch and plug-in, electronic control system integrators usually complete them through outsourcing, and do so in the form of signing outsourcing processing contracts and paying processing fees.
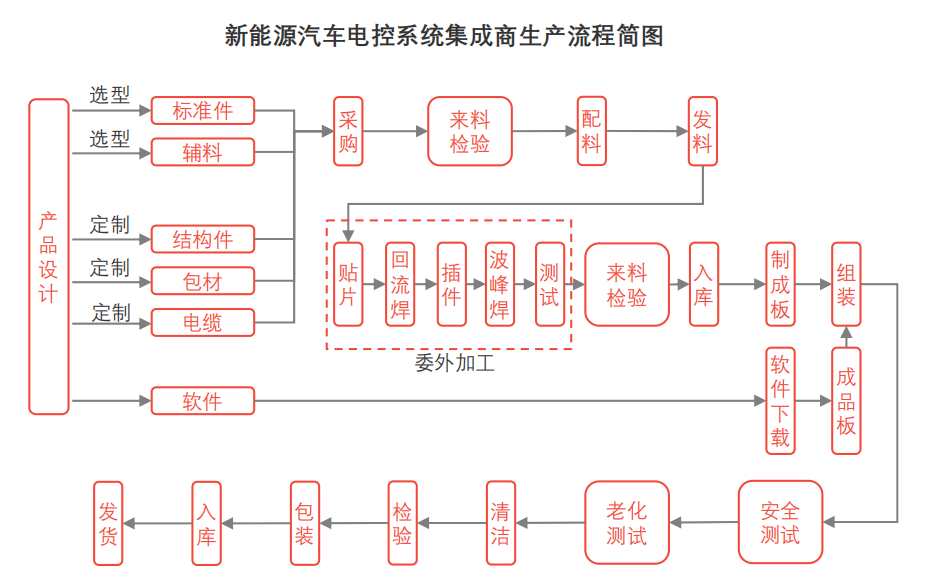
Analysis on purchasing situation of new energy vehicle electronic control system integrators
The raw materials of new energy vehicle electronic control system products mainly include electronic components such as IGBT modules, DSP chips, electrolytic capacitors, rectifier bridges, and various accessories such as metal materials and plastics, and the market supply is relatively sufficient. Among them, the average unit price of the core component IGBT module is relatively high, reaching about 350-450 yuan/piece, and the market concentration of upstream suppliers is relatively high, mainly relying on imports, which is the main procurement cost expenditure of new energy vehicle electronic control system integrators.
Analysis of downstream industry chain
Downstream new energy passenger vehicle OEMs have begun to independently develop and produce supporting electronic control system products, but new energy commercial vehicle OEMs and small and medium-sized new energy vehicle OEMs have a large demand for third-party electronic control system products.
Overview of the downstream of the new energy vehicle electronic control system industry
The downstream of the new energy vehicle electronic control system industry mainly involves new energy passenger vehicle OEMs such as BYD and BAIC New Energy, and commercial vehicle OEMs such as Yutong Bus and Zhongtong Bus. Affected by multiple factors such as the high macroeconomic pressure, the price reduction effect of the National Five fuel vehicles, and the decline of relevant subsidy support policies, according to data from the China Association of Automobile Manufacturers, China's new energy vehicle production suffered a decline in 2019, with annual production of 1.242 million vehicles, a year-on-year decrease of 2.3%, but the production of new energy passenger vehicles still maintained a steady growth. Among them, BYD has further expanded its leading advantage in the new energy market with its comprehensive product layout and advantages in battery, motor and electronic control technologies.
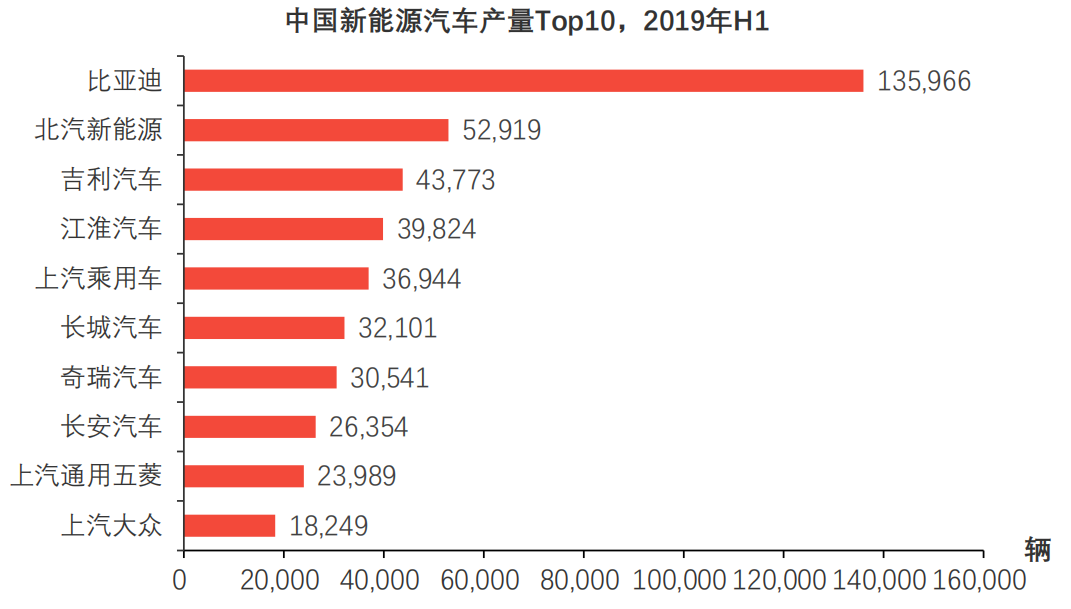
Analysis of the requirements of passenger car OEMs and commercial vehicle OEMs for electronic control systems
(1) In the field of new energy passenger vehicle OEMs: Vehicle manufacturers represented by BYD and BAIC New Energy have strong comprehensive strength and have begun to independently develop and produce electronic control system products for their new energy vehicle models, with an average price of RMB 6,000 to RMB 15,000 per unit;
(2) In the field of new energy commercial vehicle OEMs: Vehicle manufacturers lack experience in the research and development of electronic control systems and mostly choose to purchase new energy vehicle electronic control system products from third parties. Only a few large-scale vehicle manufacturers, represented by Yutong Bus, choose to independently develop and produce supporting electronic control system products, with an average price of 30,000 to 50,000 yuan per unit.
From the perspective of vehicle model distribution, pure electric vehicles are gradually becoming the mainstream. According to data from the China Association of Automobile Manufacturers, China produced 1.02 million pure electric vehicles in 2019, a year-on-year increase of 3.4%, and the market share reached 80.7%.
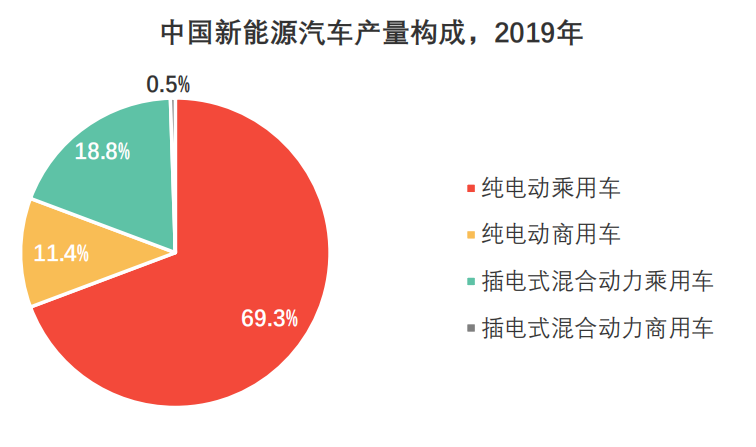
Market size
At this stage, the Chinese government is gradually transforming its policy encouragement for new energy vehicles into market guidance, which will effectively boost the output and market share of new energy vehicles and create development opportunities for China's new energy vehicle electronic control system industry.
China's new energy vehicle electronic control system industry has developed rapidly along with the rise of new energy vehicles. Its industry market size (measured by sales revenue) has increased from RMB 5.68 billion in 2015 to RMB 15.43 billion in 2019, with an average annual compound growth rate of 28.4%. Since 2018, due to the decline in subsidies for new energy vehicles and the cooling of the capital market, the growth rate of China's new energy vehicle electronic control system industry has slowed down. However, the implementation of the "double points system" will realize the financial support of the government subsidy policy for the new energy vehicle industry, and transform policy encouragement into market guidance, effectively establish a long-term management mechanism for new energy vehicles, and will drive the increase in China's medium- and long-term new energy vehicle production. At the same time, the Chinese government actively promotes the localization process of core components of new energy vehicle electronic control systems such as IGBT, and continuously improves the layout of the industrial chain of the electronic control system industry, creating development opportunities for China's new energy vehicle electronic control system industry. It is expected that the market size of China's new energy vehicle electronic control system industry will continue to grow in the next five years, and is expected to exceed RMB 21.91 billion by 2024, with an average annual compound growth rate of 7.3%.
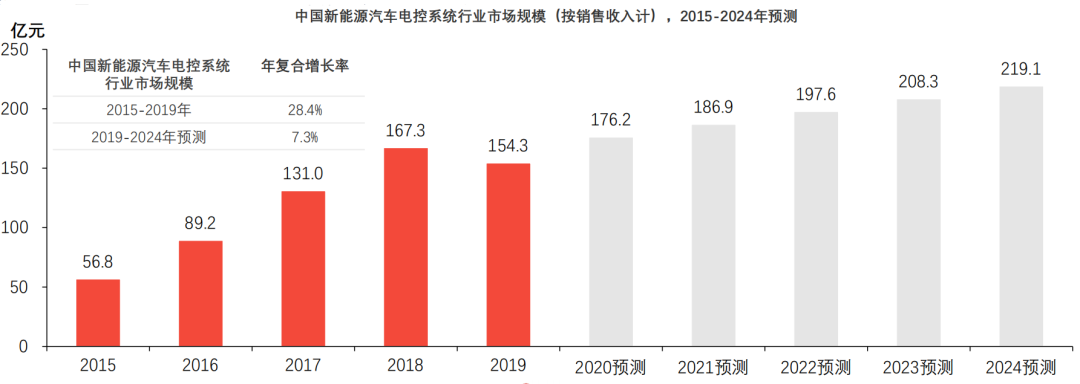
Driving factors of China's new energy vehicle electronic control system industry
Rapid development of charging infrastructure
The rapid development of charging infrastructure has greatly improved the convenience of car owners, which will promote the increase in sales of pure electric vehicles and drive the rapid growth of market demand for new energy vehicle electronic control system products.
Charging infrastructure continues to improve
With the rapid development of the new energy vehicle market, the construction of charging infrastructure has become the focus of new energy vehicles to further replace traditional internal combustion engine vehicles and expand market share. According to the operation status of electric vehicle charging infrastructure released by the China Electric Charging Infrastructure Promotion Alliance, as of December 2019, the number of public charging infrastructure in China reached 516,000 units, an increase of 18.1% year-on-year, and showed a stable growth trend.
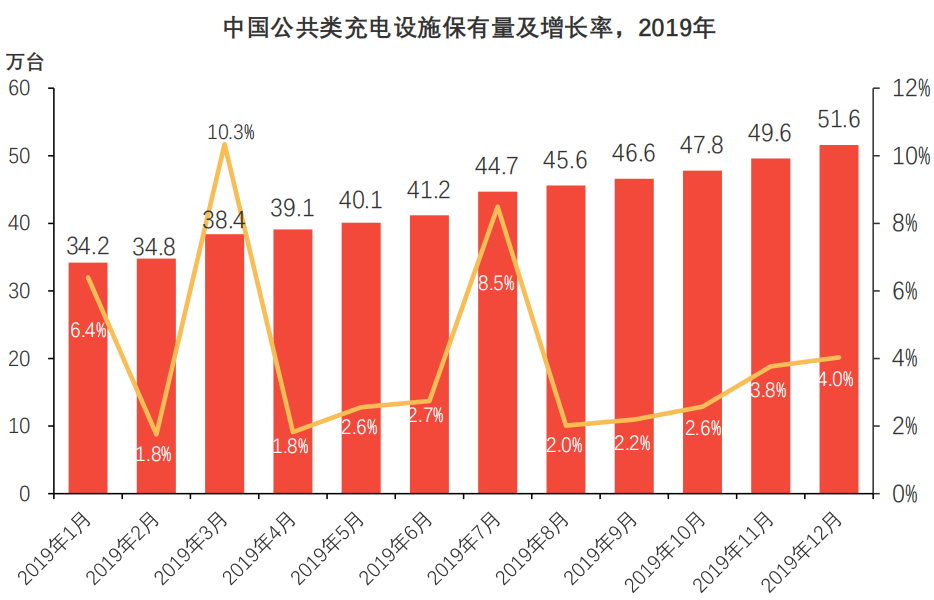
In addition, as of December 2019, the number of charging infrastructure in China has reached 1.219 million, a year-on-year increase of 50.8%, and the cumulative sales of new energy vehicles have reached 4.2 million, with a car-to-pile ratio of 3.4:1, and the power of charging piles has been greatly improved, reaching more than 120 kilowatts. At the same time, the development of charging infrastructure in provinces and cities such as Guangdong, Jiangsu, Beijing, and Shanghai in China has been relatively complete, and the construction of charging infrastructure in the top 10 regions accounts for 73.9%.
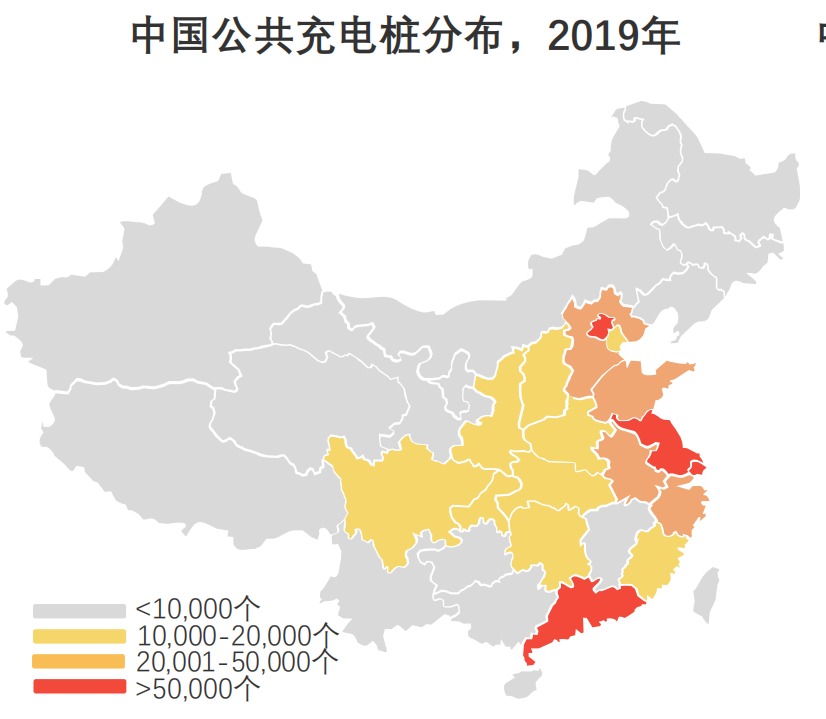
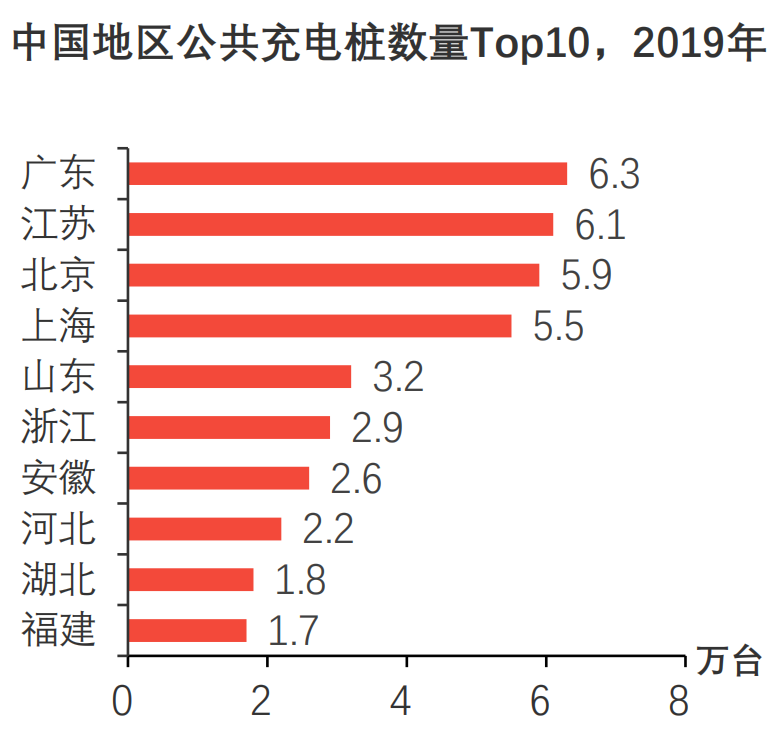
中国充电基础设施建设的不断完善将显著提升新能源汽车的便捷性与实用性,从而吸引大批潜在消费者进行换购,促进新能源汽车销量的提高,带动车辆配套电控产品市场需求量的增加,为中国新能源汽车电控系统行业创造广阔发展空间。
The rise of new car-making forces
With the improvement of the electrification level of the automobile industry, emerging car manufacturers with strong Internet backgrounds have begun to enter the market, injecting a large amount of customer resources into China's new energy vehicle electronic control system integrators.
New car-making forces are emerging rapidly
At present, China's automobile industry is accelerating its transformation. With the increasing level of automobile electrification, the proportion of electronic hardware and supporting software in automobiles has gradually increased. The automobile industry has entered a stage of rapid transformation. Emerging technology companies represented by Internet and information technology companies and technology companies have joined the traditional automobile industry, and new car-making forces have been born. Since the emergence of new car-making forces in 2014, after nearly five years of development, they have gradually broken through the bottleneck of manufacturing and production technology. New car-making forces represented by Weilai, Weimar and Xiaopeng have successfully completed delivery in 2018, and the models of new car-making forces have initially possessed market competitiveness through the upgrade of hardware equipment and the optimization of intelligent systems.
New car-making forces represented by Weilai and Xiaopeng have a strong Internet background, but their experience and relevant reserves in vehicle manufacturing and parts production are relatively weak, so they often choose to purchase supporting electronic control system products or outsource powertrain solutions. At this stage, in the field of new energy passenger vehicles, a large number of new car-making forces have entered the market, and there is a strong demand for third-party new energy vehicle electronic control system integrators, which has promoted them to transform from simple electronic control system product suppliers to powertrain solution providers for new energy vehicle manufacturers, creating a new growth point for professional third-party electronic control system integrators in China's new energy vehicle electronic control system industry, and promoting China's new energy vehicle industry to gradually become a mainstream trend through the supply of electronic control systems by third parties.
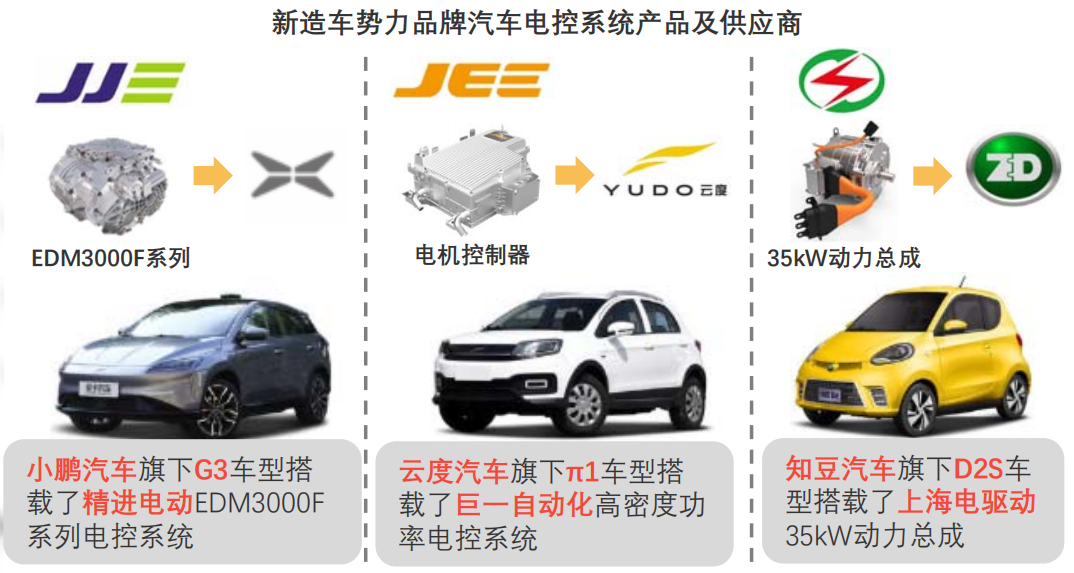
Risk Analysis of China's New Energy Vehicle Electronic Control System Industry
China's new energy vehicle electronic control system industry is highly correlated with upstream and downstream areas of the industrial chain. The development of the industry is greatly affected by macro factors such as new energy vehicle policies and overall economic conditions.
(1) Risk of changes in industry policies
The downstream new energy vehicle industry in China's new energy vehicle electronic control system industry is greatly affected by government policies. In the past five years, the Chinese government's subsidies for new energy vehicles have continued to decline, which has led to a pre-cooling of new energy vehicle manufacturers in the capital market and a decline in new energy vehicle production for the first time. According to data from the China Association of Automobile Manufacturers, China's new energy vehicle production in 2019 was 1.242 million vehicles, a year-on-year decrease of 2.3% from 2018. If the new energy vehicle industry policy is adjusted again in the future, it will directly affect the reduction in the market demand for new energy vehicle electronic control system products, thereby leading to a decline in the revenue growth rate and profit scale of electronic control system integrators.
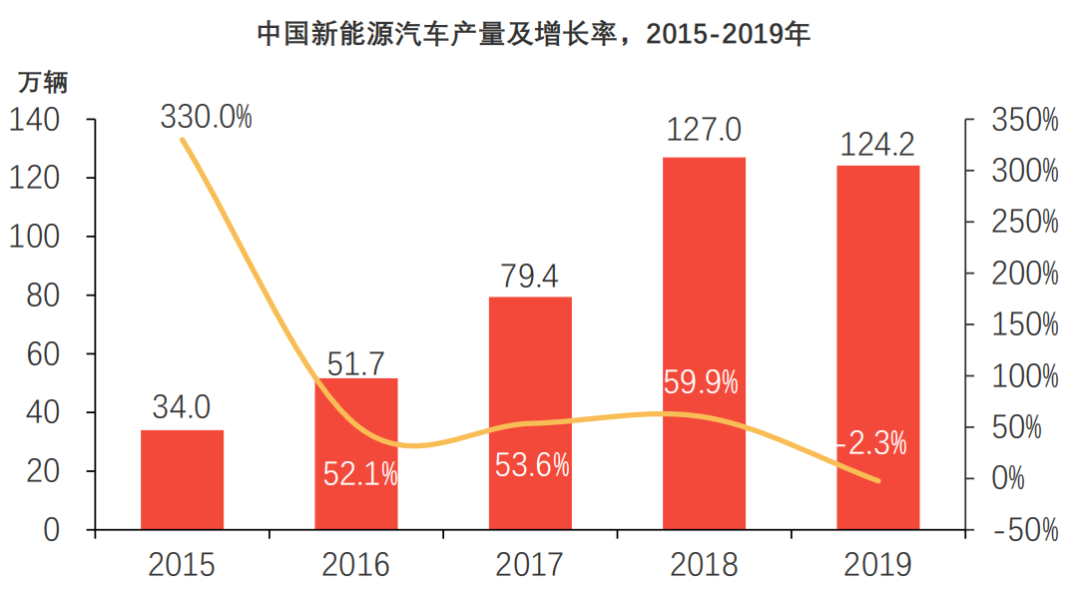
(2) Risk of raw material price fluctuations
The raw material procurement costs of China's new energy vehicle electric control system integrators account for a large proportion of their main business costs, reaching about 90%. Therefore, raw material price fluctuations have a great impact on the gross profit margin of electric control system integrators. At the same time, the IGBT modules, the core raw materials of the electric control system, are still controlled by a few international suppliers, and the supplier market concentration is relatively high. If there is a shortage of IGBT modules or price increases, it will have an adverse impact on the gross profit margin of electric control system integrators, leading to a decline in profitability.
(3) Risk of reduced dependence on downstream customers
At present, new energy passenger vehicle OEMs represented by BYD and BAIC New Energy have begun to independently develop and produce electronic control system products for their models by leveraging their advantages in funds and R&D strength, with a relatively low proportion of external purchases. If such new energy passenger vehicle OEMs continue to expand their production capacity to provide supporting electronic control system products for new energy bus OEMs or low-speed electric vehicle OEMs and other companies, it will greatly squeeze the market share of third-party integrators in China's new energy vehicle electronic control system industry, and lead to the loss of their customer resources and a decline in market demand.
(4) Risk of intensified market competition
With the acceleration of the R&D process of China's new energy vehicle electronic control system integrators, the launch of mature products and the penetration of foreign-funded enterprises in the Chinese market, the market competition in China's new energy vehicle electronic control system industry will become more and more fierce in the future. If China's new energy vehicle electronic control system integrators cannot continue to carry out technological innovation and launch products that meet market demand in the market competition, it will greatly limit the expansion of its customer resources and cause the loss of existing customer resources, thereby leading to a decline in its revenue and market share.
Relevant policies and regulations on China's new energy vehicle electronic control system industry
New energy vehicles conform to the development trend of energy conservation and environmental protection. With the support of Chinese government policies, they have been rapidly applied and their market share has been continuously improved, which in turn has driven the rapid development of the supporting electronic control system industry.
In the past five years, the Chinese government has issued a series of favorable policies to support the development of the new energy vehicle electronic control system industry, mainly in the following two aspects:
(1) Promote the healthy and orderly growth of China's new energy vehicle electronic control system industry. The promulgation of the "Made in China 2025" policy has determined the future development direction of China's new energy electronic control system industry, and promoted the optimization and upgrading of electronic control system products to high power density, high integration, high voltage and other performance indicators;
(2) Support the development of the new energy vehicle industry and expand the market demand for the new energy vehicle electronic control system industry. The release of China's new dual-credit policy, the "Three-Year Action Plan to Win the Blue Sky Defense War" and the "Notice on Further Improving the Financial Subsidy Policy for the Promotion and Application of New Energy Vehicles" have clarified the subsidy plan and development goals for China's new energy vehicle sector in the future, effectively promoting the large-scale application of China's new energy vehicles in public transportation, logistics and distribution, thereby driving the rapid increase in the market demand for electronic control products.
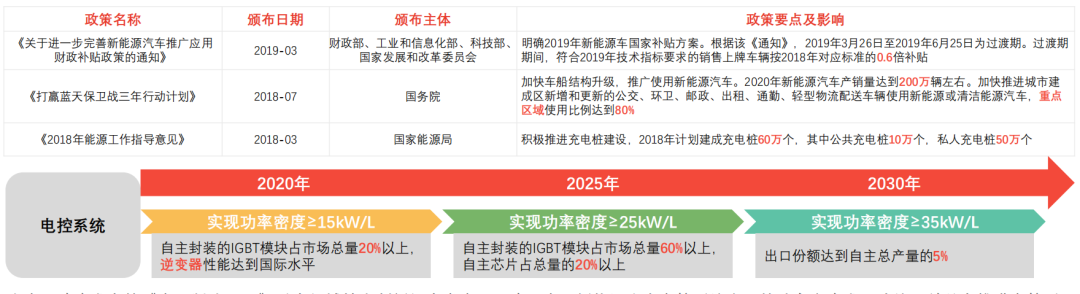
In the "Made in China 2025" key areas of technological innovation green paper released by the Chinese government, the power density development route of China's new energy vehicle electronic control system products is clarified, and efforts are made to promote the import substitution process of IGBT modules, the core components of electronic control system products, to help break through the bottleneck of raw material supply in China's new energy vehicle electronic control system industry, which will effectively reduce the procurement costs of electronic control system integrators and create broad profit space for them.
Development trend of China's new energy vehicle electronic control system industry
Integrated Development
With the rapid development of China's new energy vehicle industry, the market has put forward higher requirements for the control efficiency and technology of electronic control systems. The integration of electronic control systems has become an important development trend.
Integrated electronic control system
With the continuous development of the new energy vehicle industry, the system integration trend between the core components of new energy pure electric vehicles has become more and more obvious, and the integration of electronic control systems has gradually become an important technical development trend. At present, all-in-one electronic control system products such as drive motor controllers and steering power pump motor controllers, air pump motor controllers, on-board DC/DC controllers, on-board chargers, and high-voltage power distribution integrated products such as electric air conditioners, electric defrost, and electric heating have begun to be put into use in electric passenger cars and commercial vehicles.
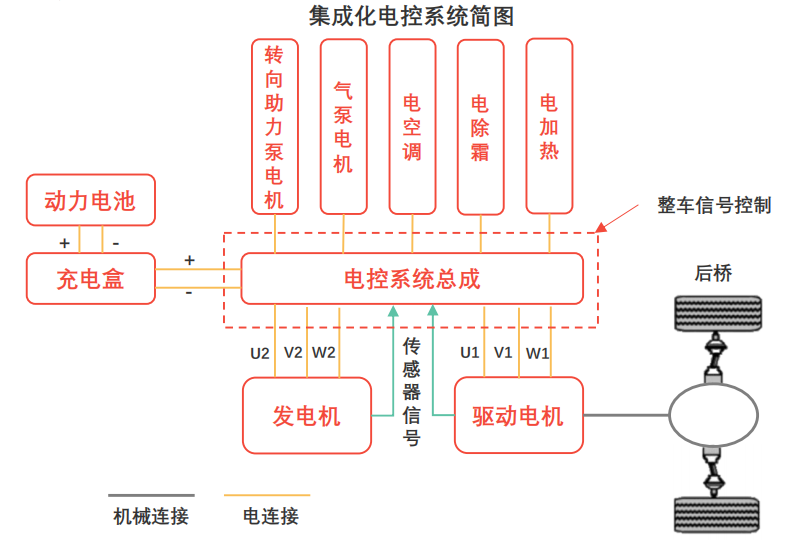
Analysis of the advantages of integrated electronic control system
The integration of multiple components reduces the number of connectors and wiring, and the electronic control system structure becomes more compact, which greatly reduces the weight and volume, thus having great advantages in the application link:
(1) The product has a compact structure and small size, which is conducive to space layout;
(2) The product is light in weight and has low driving energy consumption;
(3) The center of gravity is lowered, which is beneficial to the control of the vehicle;
(4) High-speed transmission, bringing higher torque capacity to new energy vehicles;
(5) The scalable modular design greatly shortens the product development cycle and effectively reduces development costs.
Current status of enterprise integration development in the industry
Electronic control system integrators represented by INVT, GTAKE and Huichuan Technology have begun to move towards integration and have successfully developed two-in-one and all-in-one electronic control system products for automobile companies.
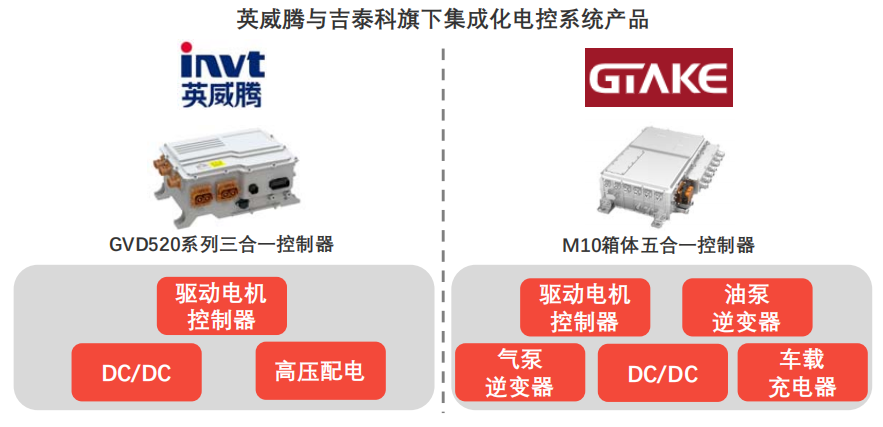
Optimizing the efficiency of electronic control systems
Improving the efficiency of the electronic control system can effectively improve the economy of the vehicle and reduce the weight of the vehicle, thereby increasing the range of new energy pure electric vehicles.
Improving battery life has become an important development direction in the field of new energy vehicles
As the core of the electric drive assembly of new energy electric vehicles, the electronic control system has an important impact on the power and economy of the entire vehicle. In the past five years, China's new energy vehicle electronic control system industry has developed rapidly in key technical fields, and the product series can basically meet the power demand below 200kw. However, China still does not have the manufacturing capability of fully independent development in the field of IGBT modules, a key component of the electronic control system, resulting in the power density of China's new energy vehicle electronic control system products being 12-18kW/L, which is still far behind the 20-35kW/L of international leading products. At present, the average cruising range of mainstream electric passenger cars in China's new energy vehicle market is about 300km, which is shorter than that of traditional internal combustion engine vehicles. Therefore, improving the efficiency of new energy vehicle electronic control systems has become a research and development focus.
Analysis of key technologies for optimizing the efficiency of electronic control systems
New energy vehicle electronic control system efficiency optimization technologies include carrier frequency dynamic adjustment technology, overmodulation technology and double-sided heat dissipation technology:
Dynamic carrier frequency adjustment technology
The main loss source of the electric control system is the inverter part, and 70% of the inverter loss comes from the switch.
The carrier frequency dynamic adjustment technology can reduce the number of switching times by 30%, effectively improve the efficiency of the electronic control system, and reduce the loss of the electronic control system. When the vehicle motor is running at a low speed, the efficiency of the electronic control system can be increased by about 2%, thereby increasing the vehicle's cruising range.
Overmodulation Technology
The loss sources of the electronic control system also include conduction loss
The conduction loss is greatly affected by the output current. When the output current decreases, the corresponding output voltage needs to be increased accordingly.
By adding overmodulation, the output power and torque in the weak magnetic field area can be effectively improved, the output voltage can be increased by 4%, the peak power can be increased accordingly, and the dynamic performance of the whole vehicle at high speed can be improved.
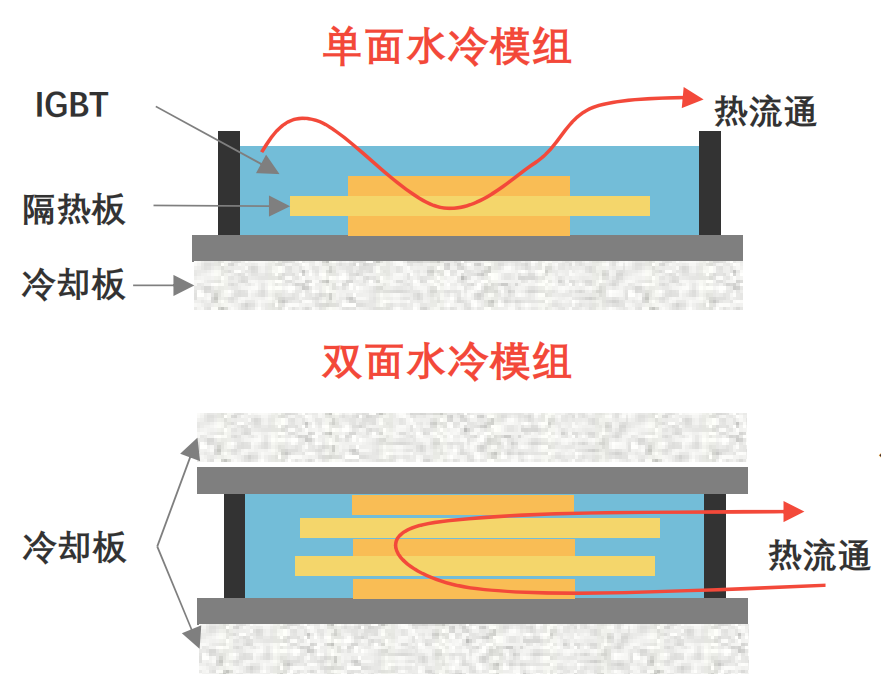
Double-sided cooling technology
Compared with the single-sided water-cooling module, the thermal resistance of the double-sided heat dissipation module can be reduced by 32%, and the water pressure drop is reduced to 35% of the single-sided water-cooling module, effectively improving the heat dissipation efficiency of the electronic control module.
The double-sided water cooling module design can increase the power density of the electronic control system by 88% and the output power by about 30%.
Competition landscape of China's new energy vehicle electronic control system industry
As the new energy vehicle electronic control system industry was launched simultaneously with the Chinese electric vehicle market, the industry-related standard system has not yet taken shape, vehicle manufacturers and third-party suppliers each occupy an advantageous position, and the market competition pattern is not yet clear.
Analysis of the competitive landscape of China's new energy vehicle electronic control system industry
At present, China's pure electric vehicle market is in its initial development stage, and the market scale has not yet started on a large scale. China's local vehicle manufacturers are also in the process of formulating and improving their research and development, procurement, production and sales plans for pure electric vehicles. Therefore, the supporting new energy vehicle electronic control system industry has not yet formed a clear and stable market competition pattern.
At present, China's new energy vehicle electronic control system industry market is mainly occupied by Chinese local brands. Due to their higher prices and other reasons, foreign products have a relatively small market share in the market cultivation and initial development stages.
Previous article:How to redefine the cockpit under the transformation of intelligent automobiles?
Next article:How to Design HVAC Systems for Hybrid/Electric Vehicles
- Popular Resources
- Popular amplifiers
- A new chapter in Great Wall Motors R&D: solid-state battery technology leads the future
- Naxin Micro provides full-scenario GaN driver IC solutions
- Interpreting Huawei’s new solid-state battery patent, will it challenge CATL in 2030?
- Are pure electric/plug-in hybrid vehicles going crazy? A Chinese company has launched the world's first -40℃ dischargeable hybrid battery that is not afraid of cold
- How much do you know about intelligent driving domain control: low-end and mid-end models are accelerating their introduction, with integrated driving and parking solutions accounting for the majority
- Foresight Launches Six Advanced Stereo Sensor Suite to Revolutionize Industrial and Automotive 3D Perception
- OPTIMA launches new ORANGETOP QH6 lithium battery to adapt to extreme temperature conditions
- Allegro MicroSystems Introduces Advanced Magnetic and Inductive Position Sensing Solutions
- TDK launches second generation 6-axis IMU for automotive safety applications
- LED chemical incompatibility test to see which chemicals LEDs can be used with
- Application of ARM9 hardware coprocessor on WinCE embedded motherboard
- What are the key points for selecting rotor flowmeter?
- LM317 high power charger circuit
- A brief analysis of Embest's application and development of embedded medical devices
- Single-phase RC protection circuit
- stm32 PVD programmable voltage monitor
- Introduction and measurement of edge trigger and level trigger of 51 single chip microcomputer
- Improved design of Linux system software shell protection technology
- What to do if the ABB robot protection device stops
- Huawei's Strategic Department Director Gai Gang: The cumulative installed base of open source Euler operating system exceeds 10 million sets
- Download from the Internet--ARM Getting Started Notes
- Learn ARM development(22)
- Learn ARM development(21)
- Learn ARM development(20)
- Learn ARM development(19)
- Learn ARM development(14)
- Learn ARM development(15)
- Analysis of the application of several common contact parts in high-voltage connectors of new energy vehicles
- Wiring harness durability test and contact voltage drop test method
- 【RPi PICO】Breathing light
- Why does the resolution decrease when the gain is increased?
- Evaluation of the domestic FPGA Gaoyun GW1N-4 series development board - Software Part 2
- A busbar power supply plant power rapid protection anti-sway cabinet
- How to put C2000 into low power mode
- GD32F350 is easy to use
- Industrial and Automation Solutions Collection
- Award-winning live broadcast | Use ModusToolbox to build a system to flexibly meet IoT design challenges
- Verilog009
- 5G is a revolutionary advancement in mobile communications