When the driver manipulates the steering wheel to steer, the torque sensor detects the steering direction of the steering wheel and the size of the torque, and transmits the voltage signal to the electronic control unit. The electronic control unit sends instructions to the motor controller based on the torque voltage signal, rotation direction and vehicle speed signal detected by the torque sensor, so that the motor outputs the steering assist torque of the corresponding size and direction, thereby generating auxiliary power. When the car is not turning, the electronic control unit does not send instructions to the motor controller, and the motor does not work.
Part I EPS Control Strategy
Control strategies are nothing more than three things:
What is input?
For the EPS control strategy, the input of its basic functions is mainly the steering wheel torque and steering wheel angle provided by the torque angle sensor inside the EPS system, and the vehicle speed signal obtained from the bus.
For some advanced EPS functions, it may be necessary to obtain vehicle dynamic parameters such as the side slip angle, yaw angular velocity, left and right front and rear wheel speeds from the CAN bus.
Driving assistance or autonomous driving also needs to obtain signals such as superimposed torque value, target steering wheel angle, target steering wheel speed, etc. from the CAN bus.
What is the output?
Based on the input, what kind of control logic is used to get the output?
Due to space limitations, only the control strategy of the basic functions of EPS is involved here. Please remember the following simplified formula: T_hand + T_motor = T_resistance
T_hand is the torque used by the driver to operate the steering wheel, which is measured by the torque angle sensor.
T_resistance is the torque generated by the resistance transmitted to the rack due to the friction between the tire and the ground. The working process of the steering system is the process of overcoming this resistance torque.
The EPS control strategy is actually the process of calculating T_motor based on various system input conditions. As for how T_motor is generated (in the field of motor control)
Careful viewers may ask, do we still need to use the vehicle speed as input? Where is the vehicle speed? Where is the vehicle speed?
There are some calibration parameters called CURVE or MAP in all the technical boxes. Those annoying parameters are basically related to vehicle speed.
Figure 1: Basic EPS control module
The first is the power-assist characteristic curve module. Since the invention of EPS, the main power-assist characteristic curve has gone through a process from straight line to segmented broken line to curve. The straight-line power-assist characteristic curve and the broken-line power-assist characteristic curve are relatively simple and easy to debug, but because the power-assist curve is not steerable everywhere, it is impossible to obtain a good steering feel to establish a gradient and a sense of the intermediate position.
The lead-lag correction module has many fancy names, such as stable compensator, adaptive compensator, etc. Its essence is a lead-lag correction link in the automatic control principle. Those who have learned the basic knowledge of the automatic control principle feedback system know that when the amplification factor of the forward channel of a control system is too large, it will inevitably lead to divergent instability of the system (Rouse stability criterion and Nyquist stability criterion).
The power assist characteristic curve is essentially an amplification factor K of the forward channel, but this K changes under different vehicle speeds and different hand torque conditions. When this K is relatively large, it will cause the EPS system to diverge. A typical situation is what we call "self-excited EPS". Without introducing the lead-lag correction module or the parameters of the lead-lag correction module are not adjusted properly, a slight excitation is given to the steering wheel, and the steering wheel may oscillate continuously at a certain position.
The introduction of the lag-lead module is designed to eliminate this phenomenon. There are two-order compensation, three-order compensation, and four-order compensation. The compensation algorithms above the fourth order are too complicated to adjust the parameters, so the author has not seen any company adopt them yet.
The design ideas are:
Try not to affect the amplitude-frequency and phase-frequency characteristics of the original system in the low-frequency band
Reduce system gain in the mid-range
Improve the phase-frequency characteristics of the system in the high frequency band to obtain a larger phase margin
The BODE diagram of a typical lead-lag correction module is as follows:
The high-frequency gain module performs high-pass filtering on the hand torque alone, and calculates a high-frequency gain torque based on the high-frequency part of the torque signal after a MAP. Because high-pass filtering will inevitably lead to phase advance, this part of the torque has a certain compensation effect on the motor inertia and the internal friction of the steering system.
The return control and damping control are a pair of good friends that complement each other. Without these two controls, the tires and suspension system can also provide a certain return force. But generally speaking:
At low speeds, the system resistance is too great, and the vehicle's self-centering force is not enough to overcome all resistance and return the steering wheel to the neutral position when the hands are released;
At high speeds, the vehicle's own restoring force is too great, and the head shake is likely to occur when the hands are released.
So this pair of good friends each has their own responsibilities. At low speeds, the return control works to provide an additional torque to help the steering wheel return to the middle position; at high speeds, the damping control works to provide a reverse torque to prevent the steering wheel from shaking. The ultimate goal is the same, to allow the steering wheel to return to the middle position accurately and smoothly at all speeds.
Part II EPS Architecture
The architecture that Depeng gave me did cause a lot of comments, so I will explain it here. The architecture of chassis electronics is generally the following mainstream architecture, a single dual-core with an external MCU.
EPS: missing, moving and locked are the three major D-level problems
In the field of wire control and unmanned driving, EPS itself is a set of more than two
We don't know if this is so exaggerated.
summary:
1) In the basic functional module of EPS, the power assist curve is the basis, the high-frequency correction is the key, and the return damping is the icing on the cake.
2) How will a single EPS or even 2-3 be handled in the future? It depends on the BOM cost and the purpose requirements. The entire design may have some variables. Can anyone explain it clearly?
Previous article:“Small and beautiful” smart electric car: How should the chassis be designed?
Next article:Electronic Power Steering System Architecture and Controller Selection Guide
Recommended ReadingLatest update time:2024-11-15 15:23
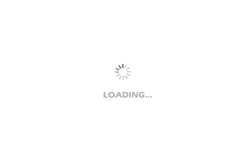
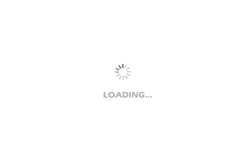
- Popular Resources
- Popular amplifiers
-
A review of learning-based camera and lidar simulation methods for autonomous driving systems
-
Automotive Electronics Technology (Edited by Han Jinyu and Zhang Yong)
-
Control strategies for advanced driver assistance systems and automated driving functions
-
Automotive Electrical and Electronics (Fifth Edition, James D. Halderman)
- A new chapter in Great Wall Motors R&D: solid-state battery technology leads the future
- Naxin Micro provides full-scenario GaN driver IC solutions
- Interpreting Huawei’s new solid-state battery patent, will it challenge CATL in 2030?
- Are pure electric/plug-in hybrid vehicles going crazy? A Chinese company has launched the world's first -40℃ dischargeable hybrid battery that is not afraid of cold
- How much do you know about intelligent driving domain control: low-end and mid-end models are accelerating their introduction, with integrated driving and parking solutions accounting for the majority
- Foresight Launches Six Advanced Stereo Sensor Suite to Revolutionize Industrial and Automotive 3D Perception
- OPTIMA launches new ORANGETOP QH6 lithium battery to adapt to extreme temperature conditions
- Allegro MicroSystems Introduces Advanced Magnetic and Inductive Position Sensing Solutions
- TDK launches second generation 6-axis IMU for automotive safety applications
- LED chemical incompatibility test to see which chemicals LEDs can be used with
- Application of ARM9 hardware coprocessor on WinCE embedded motherboard
- What are the key points for selecting rotor flowmeter?
- LM317 high power charger circuit
- A brief analysis of Embest's application and development of embedded medical devices
- Single-phase RC protection circuit
- stm32 PVD programmable voltage monitor
- Introduction and measurement of edge trigger and level trigger of 51 single chip microcomputer
- Improved design of Linux system software shell protection technology
- What to do if the ABB robot protection device stops
- Learn ARM development(14)
- Learn ARM development(15)
- Analysis of the application of several common contact parts in high-voltage connectors of new energy vehicles
- Wiring harness durability test and contact voltage drop test method
- From probes to power supplies, Tektronix is leading the way in comprehensive innovation in power electronics testing
- From probes to power supplies, Tektronix is leading the way in comprehensive innovation in power electronics testing
- Sn-doped CuO nanostructure-based ethanol gas sensor for real-time drunk driving detection in vehicles
- Design considerations for automotive battery wiring harness
- Do you know all the various motors commonly used in automotive electronics?
- What are the functions of the Internet of Vehicles? What are the uses and benefits of the Internet of Vehicles?
- [Environmental Expert's Smart Watch] Part 10: Status Light and Mode Switching
- Disassembly of 3.0 expansion dock, PD to HDMI conversion chip Bridgestone PS176HDMQFN48GTR2-B0 schematic diagram reference
- Stack Overflow Technology from Entry to Mastery
- Has anyone used HEW to compile?
- Three issues about LDO load regulation, linear regulation and voltage drop
- How to release the object is part of a locked union
- Lighting capacitor
- Design of Automatic AC Voltage Stabilizer
- LTC6915 is reverse grounded and forward connected to a bipolar signal. What is the final output?
- Is drinking yogurt a ritual now?