In technology fields such as medical equipment, automotive instrumentation, and industrial control, when equipment design involves strain gauges, sensor interfaces, and current monitoring, precision analog front-end amplifiers are often required to extract and amplify very weak real signals and suppress unwanted signals such as common-mode voltage and noise. Initially, designers will focus on ensuring that precision parameters such as device-level noise, offset, gain, and temperature stability meet application requirements.
Designers can then select front-end analog components that meet the total error budget requirements based on the above characteristics. However, there is an often overlooked problem in such applications, which is high-frequency interference caused by external signals, which is commonly known as "electromagnetic interference (EMI)". EMI can occur in many ways, mainly affected by the final application. For example, an instrumentation amplifier may be used in a control board that interfaces with a DC motor. The current loop of the motor, which includes power leads, brushes, commutator, and coils, usually acts like an antenna and can emit high-frequency signals, which may interfere with the small voltage at the input of the instrumentation amplifier.
Another example is current sensing in automotive solenoid control. The solenoid is powered from the vehicle battery through long wires that act like antennas. A series shunt resistor is connected in the wire path, and the voltage across the resistor is measured by a current sense amplifier. High-frequency common-mode signals may exist in the line, and the input of the amplifier is susceptible to such external signals. Once affected by external high-frequency interference, the accuracy of the analog device may be degraded, and it may even be impossible to control the solenoid circuit. This state manifests in the amplifier as the amplifier output accuracy exceeds the error budget and data sheet tolerance, and in some cases may even reach the limit, causing the control loop to shut down.
How does EMI cause large DC deviations? It may be one of the following situations: Many instrumentation amplifiers are designed to have excellent common-mode rejection performance in the frequency range up to tens of kilohertz. However, when an unshielded amplifier is exposed to tens or hundreds of "megahertz" of RF radiation, problems may occur. At this time, the input stage of the amplifier may experience asymmetrical rectification, resulting in a DC offset that can be very significant after further amplification, and combined with the amplifier's gain, it may even reach the upper limit of its output or some external circuits.
Examples of How High-Frequency Signals Affect Analog Devices
This example will detail a typical high-side current sensing application. Figure 1 shows a common configuration used to monitor solenoid valves or other inductive loads in an automotive environment.
Figure 1. High-side current monitoring.
The effects of high-frequency interference were investigated using two current-sense amplifier configurations of similar design. The two devices are identical in functionality and pinout; however, one has an internal EMI filter circuit while the other does not.
Figure 2. Current sensor output (no internal EMI filter, forward power = 12 dBm, 100 mV/div, DC output peak at 3 MHz)
Figure 2 shows how the dc output of the current sensor deviates from its ideal value when the input varies over a wide frequency range. It can be seen that the deviation is most significant (>0.1 V) in the frequency range of 1 MHz to 20 MHz, and the dc error reaches a maximum value (1 V) at 3 MHz, which is a large percentage of the amplifier's output voltage range of 0 V to 5 V.
Figure 3 shows the test results of the same experiment and configuration using an alternative pin-compatible current sensor with the same circuit architecture and similar DC specifications as the previous example, but with input EMI filtering built in. Note that the voltage range is increased by a factor of 20.
Figure 3. Current sensor output (internal EMI filter, forward power = 12 dBm, 5 mV/div, DC output peaks at >100 MHz)
In this case, the error is only about 3 mV at 40 MHz, and the peak error (at >100 MHz) is less than 30 mV, a 35x improvement. This clearly shows that built-in EMI filtering helps significantly protect the current sensor from high-frequency signals present at the input. In a real-world application, even if the severity of the EMI is unknown, the control loop will actually stay within its tolerance if the current sensor with built-in EMI filtering is used.
Both devices were tested under exactly the same conditions. The only difference is that the AD8208 (see Appendix) has internal low-pass RF input filters on both the input and supply pins. Adding such a component to the chip may seem trivial, but since the application is typically PWM controlled, the current sense amplifier must be able to withstand continuous switching common-mode voltages of up to 45 V. Therefore, the input filters must be closely matched to maintain accurate high gain and common-mode rejection.
Why and how to ensure EMI compliance when designing and testing
Automotive applications are particularly sensitive to EMI events, which are unavoidable in a noisy electrical environment consisting of a central battery, bundled wiring harnesses, various inductive loads, antennas, and external interference associated with the vehicle. Since multiple critical function controls such as airbag deployment, cruise control, braking, and suspension involve electronic devices, EMI compatibility must be guaranteed and false alarms or false triggers due to external interference are not allowed. In the past, EMI compatibility testing was the last test in automotive applications. If something went wrong, designers had to find a solution in a hurry, which often involved changing the board layout, adding additional filters, or even replacing components.
This uncertainty greatly increases design costs and causes a lot of headaches for engineers. The automotive industry has been taking concrete steps to improve EMI compatibility. Because devices must meet EMI standards, automotive OEMs now require semiconductor manufacturers (such as Analog Devices) to perform EMI testing at the device level before considering using their devices. This process is now commonplace, and all IC manufacturers use standard specifications to test the EMI compatibility of their devices.
To learn about standard EMI test requirements for various types of integrated circuits, please purchase documents from the International Electrotechnical Commission (IEC). Documents such as IEC 62132 and IEC 61967 provide information about EMI and EMC, which describe in great detail how to test specific integrated circuits using industry-recognized standards. The various tests mentioned above are performed according to these guidelines.
Specifically, these tests are done using “direct power injection,” a method that couples RF signals to specific device pins through capacitors. Depending on the type of IC being tested, each input of the device is tested for different RF signal power levels and frequency ranges. Figure 4 shows a schematic diagram of how direct power injection testing is performed on specific pins.
Figure 4. Direct power injection
These standards contain a great deal of necessary information on circuit configuration, layout methods, and monitoring techniques to help properly understand the success or failure of device testing. A more complete schematic of the IEC standard is shown in Figure 5.
Figure 5. EMI tolerance test schematic
Summarize
EMI compatibility of integrated circuits is critical to the success of electronic designs. This article shows how two very similar amplifiers can perform dc measurements in an RF environment with or without an internal EMI filter. EMI is a very important aspect in automotive applications when considering safety and reliability. Today, IC manufacturers such as Analog Devices are increasingly considering EMI tolerance when designing and testing devices for critical applications. IEC standards provide useful guidelines in great detail. For the automotive market, current sensing devices such as the AD8207 , AD8208 , and AD8209 have passed EMI testing. Newer devices such as the AD8280 lithium-ion battery safety monitor and the AD8556 digitally programmable sensor signal amplifier have been specifically designed and tested to meet EMI requirements.
appendix
More details on the AD8208: The AD8203 (Figure A) is a single-supply difference amplifier ideal for amplifying and low-pass filtering small differential voltages in the presence of large common-mode voltages. The input common-mode voltage range is -2 V to +45 V when operating from a single +5 V supply. The amplifier offers enhanced input overvoltage and ESD protection, as well as built-in EMI filtering.
Figure A. AD8208 difference amplifier
The AD8208 has excellent ac and dc performance and is qualified for automotive applications that require stable and reliable precision devices to improve system control. Typical offset and gain drift are less than 5 µV/°C and 10 ppm/°C, respectively. The device is available in SOIC and MSOP packages and has a minimum common-mode rejection ratio (CMR) of 80 dB from DC to 10 kHz.
An externally available 100kΩ resistor is available for low-pass filtering and to establish gains other than 20.
Previous article:EMC solution in remote control design
Next article:Switch and Multiplexer Design Considerations for Harsh Operating Environments
Recommended ReadingLatest update time:2024-11-23 08:24
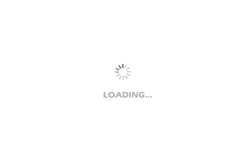
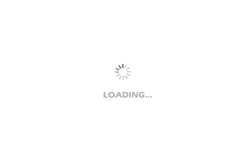
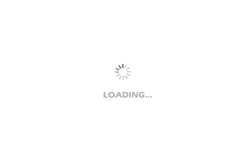
- Popular Resources
- Popular amplifiers
-
Study on the Behavioral Model of Silicon Carbide MOSFET Power Module and EMI Prediction of Low-Voltage Auxiliary Power Supply
-
Cable radiated EMI modeling considering mutual coupling effects_Junpeng Ji
-
Design of broadband hybrid active EMI filter for switching power supply_Liao Yuehong
-
Switching power supply conducted EMI simulation and filter circuit design_Jiang Yunfu
- USB Type-C® and USB Power Delivery: Designed for extended power range and battery-powered systems
- ROHM develops the second generation of MUS-IC™ series audio DAC chips suitable for high-resolution audio playback
- ADALM2000 Experiment: Transformer-Coupled Amplifier
- High signal-to-noise ratio MEMS microphone drives artificial intelligence interaction
- Advantages of using a differential-to-single-ended RF amplifier in a transmit signal chain design
- ON Semiconductor CEO Appears at Munich Electronica Show and Launches Treo Platform
- ON Semiconductor Launches Industry-Leading Analog and Mixed-Signal Platform
- Analog Devices ADAQ7767-1 μModule DAQ Solution for Rapid Development of Precision Data Acquisition Systems Now Available at Mouser
- Domestic high-precision, high-speed ADC chips are on the rise
- Intel promotes AI with multi-dimensional efforts in technology, application, and ecology
- ChinaJoy Qualcomm Snapdragon Theme Pavilion takes you to experience the new changes in digital entertainment in the 5G era
- Infineon's latest generation IGBT technology platform enables precise control of speed and position
- Two test methods for LED lighting life
- Don't Let Lightning Induced Surges Scare You
- Application of brushless motor controller ML4425/4426
- Easy identification of LED power supply quality
- World's first integrated photovoltaic solar system completed in Israel
- Sliding window mean filter for avr microcontroller AD conversion
- What does call mean in the detailed explanation of ABB robot programming instructions?
- STMicroelectronics discloses its 2027-2028 financial model and path to achieve its 2030 goals
- 2024 China Automotive Charging and Battery Swapping Ecosystem Conference held in Taiyuan
- State-owned enterprises team up to invest in solid-state battery giant
- The evolution of electronic and electrical architecture is accelerating
- The first! National Automotive Chip Quality Inspection Center established
- BYD releases self-developed automotive chip using 4nm process, with a running score of up to 1.15 million
- GEODNET launches GEO-PULSE, a car GPS navigation device
- Should Chinese car companies develop their own high-computing chips?
- Infineon and Siemens combine embedded automotive software platform with microcontrollers to provide the necessary functions for next-generation SDVs
- Continental launches invisible biometric sensor display to monitor passengers' vital signs
- PYPL October 2022 Rankings
- Looking for a voltage detection circuit or chip, 3v to 12v
- Weekly review information broadcast ~ Watch it all at once!
- XA9500XL: High-performance 3.3V CPLD automotive electronics XA series
- Creative poker clock based on ESP32
- "Wanli" Raspberry Pi car launched
- Tencent security engineer curiously checked hotel WiFi vulnerabilities and was arrested by Singapore Security Bureau
- CSL library for GPIO of C6000 series DSP
- Some comments for the forum
- How can dust people reply to receive confirmation information? . .