DDC is developed from PLC and is designed by manufacturers specifically for niche markets. Its biggest advantage over PLC is that it has a fixed control program.
Note : DDC (Direct Digital Control) is usually called DDC controller. The composition of DDC system usually includes central control equipment (centralized control computer, color monitor, keyboard, printer, uninterruptible power supply, communication interface, etc.), on-site DDC controller, communication network, and corresponding sensors, actuators, control valves and other components.
Regarding PLC and DDC, which one has more advantages in building automation systems? Make the following comparison:
1. Application areas
DDC is developed from PLC, which is specially used in industrial automation. Almost all industrial production line control systems, thermal power plant control systems, and steel plant control systems in China use PLC systems. Currently, a considerable number of building control systems also use PLC. Building automation DDC is developed from PLC by manufacturers based on the characteristics of building automation. The difference between it and PLC is that it only solidifies some programs inside, but it also lacks the flexibility of PLC and the ability to cope with complex electromagnetic interference environments.
2. Structural differences
After years of development, today's PLC is actually the same as DDC in terms of networking. It also supports multiple protocols, has a layered structure, and can achieve point-to-point communication. PLCs distributed at various sites on site do not need to be managed through a host computer for communication.
3. Software Features
The host computer software of the DDC system is mostly dedicated software, which actually shows its incompatibility from another aspect. The software of each manufacturer is different, and many of them are in English, which is the beginning of a nightmare for technicians. The host computer software of the PLC system can be either dedicated software or general configuration software. At present, the general configuration software in China is purely in Chinese, and the configuration is flexible and convenient. General configuration software can handle complex industrial control systems, let alone district building control. Besides, whether it is the debugging of the PLC system or the DDC system, professional debugging personnel complete the configuration, and then train the owner to operate and manage. It is actually the same for the owner. On the other hand, general configuration software can realize all the functions of professional software, and can also realize many functions that professional software cannot realize (such as high simulation interface, human voice alarm, user customization function, etc.).
4. Professionalism
Many building control projects now use PLC systems. Facts have proven that the above-mentioned DDC functions can also be completed by PLC systems. Experienced PLC building control implementers have also accumulated all control process programs, energy management and energy-saving programs. At the same time, because they have source programs for all process programs, they can quickly make customized functions for different projects. Since there are also ready-made process programs, on-site debugging work is also very short, and it will also be smoother than DDC debugging, because the DDC built-in program only has interface functions and is in a fixed format. If there are special needs, you have to contact the manufacturer's engineers thousands of miles away, and it is not certain whether they can be solved.
5. Scalability
Everyone knows that the PLC system is a universal and open system. At present, most PLC systems and most DDC system operator stations use TCP/IP protocol, and can be connected as long as there is a network. However, the current DDC system software charges expensive fees based on the number of users, which makes most completed building control systems want to have sub-control operation stations but dare not think about it! PLC system just has this advantage.
6. Security
In fact, just imagine this problem: a thermal power plant is generating electricity, and suddenly a PLC module breaks down. If the entire system needs to be shut down to replace it as mentioned above, what will be the consequences? The boiler may explode! Haha! It is much more serious than the consequences of building control! Now many PLC system modules are hot-swappable and hot-standby redundant (these functions seem to have been learned from PLC in recent years). PLC is developed for industrial environments. In complex industrial control environments, module failures or system shutdowns may cause major accidents or casualties. The reliability requirements are much higher than those of DDC! I don’t know how the above statement came about. The PLC control core can operate reliably and trouble-free for a long time in harsh environments, and is easy to wire, easy to maintain, has good isolation, strong corrosion resistance, can adapt to a wide temperature range, and has a mean time between failures (MTBF) of more than 15 years.
7. Debugging complexity
The most commonly used language in PLC programming now is ladder diagram, which is visual and WYSIWYG. It does not require a high level of English and can be learned by ordinary electricians.
The current PLC system is the same as the DDC system. You can sit in a comfortable machine room and debug the whole system with a laptop and an Internet cable. As for the accuracy problem, you can tell from the product technical parameters! I just want to say: Is the accuracy requirement of industrial control lower than that of building control? I think no one would think so! Haha! The control system on the modern industrial production line has tens of thousands of points (basically PLC is used, but none of them use DDC), and it requires millisecond-level network connection. Can DDC do it?
Overview
In fact, DDC is developed from PLC, and is designed by manufacturers specifically for the niche market. Its biggest advantage over PLC is that it has a fixed control program, and its other performance aspects are inferior to PLC. Since DDC only targets the professional niche market of building control, the national market capacity is not large, which is the fundamental reason why DDC has poor performance and a higher price.
The manufacturer's initial starting point for the fixed control program in DDC is that most of the contractors of the building control system are weak current system integrators, who have relatively little contact with automatic control technology, so the manufacturer must make an easy product for them to debug. However, this also makes it lose flexibility.
If you encounter an experienced automatic control engineer, the fixed program in the product will become a burden to his ability to perform. After the building control system is completed and delivered to the user, the user's maintenance engineer is more exposed to PLC in society. The most commonly used PLC programming language is ladder diagram language, which is visual and WYSIWYG. It does not require English proficiency and can be learned by ordinary electricians, so its maintenance technology and cost are lower.
Previous article:16-bit, high-precision 4-20mA input isolated analog front end (AFE)
Next article:Introduction to the basic operation and functions of programmable logic controller (PLC)
Recommended ReadingLatest update time:2024-11-16 19:34
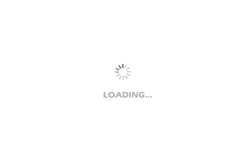
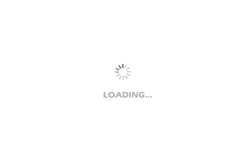
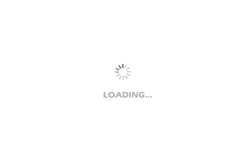
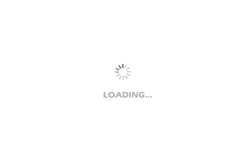
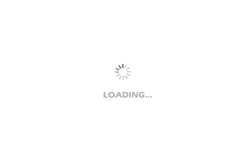
- Popular Resources
- Popular amplifiers
- High signal-to-noise ratio MEMS microphone drives artificial intelligence interaction
- Advantages of using a differential-to-single-ended RF amplifier in a transmit signal chain design
- ON Semiconductor CEO Appears at Munich Electronica Show and Launches Treo Platform
- ON Semiconductor Launches Industry-Leading Analog and Mixed-Signal Platform
- Analog Devices ADAQ7767-1 μModule DAQ Solution for Rapid Development of Precision Data Acquisition Systems Now Available at Mouser
- Domestic high-precision, high-speed ADC chips are on the rise
- Microcontrollers that combine Hi-Fi, intelligence and USB multi-channel features – ushering in a new era of digital audio
- Using capacitive PGA, Naxin Micro launches high-precision multi-channel 24/16-bit Δ-Σ ADC
- Fully Differential Amplifier Provides High Voltage, Low Noise Signals for Precision Data Acquisition Signal Chain
- Innolux's intelligent steer-by-wire solution makes cars smarter and safer
- 8051 MCU - Parity Check
- How to efficiently balance the sensitivity of tactile sensing interfaces
- What should I do if the servo motor shakes? What causes the servo motor to shake quickly?
- 【Brushless Motor】Analysis of three-phase BLDC motor and sharing of two popular development boards
- Midea Industrial Technology's subsidiaries Clou Electronics and Hekang New Energy jointly appeared at the Munich Battery Energy Storage Exhibition and Solar Energy Exhibition
- Guoxin Sichen | Application of ferroelectric memory PB85RS2MC in power battery management, with a capacity of 2M
- Analysis of common faults of frequency converter
- In a head-on competition with Qualcomm, what kind of cockpit products has Intel come up with?
- Dalian Rongke's all-vanadium liquid flow battery energy storage equipment industrialization project has entered the sprint stage before production
- Allegro MicroSystems Introduces Advanced Magnetic and Inductive Position Sensing Solutions at Electronica 2024
- Car key in the left hand, liveness detection radar in the right hand, UWB is imperative for cars!
- After a decade of rapid development, domestic CIS has entered the market
- Aegis Dagger Battery + Thor EM-i Super Hybrid, Geely New Energy has thrown out two "king bombs"
- A brief discussion on functional safety - fault, error, and failure
- In the smart car 2.0 cycle, these core industry chains are facing major opportunities!
- The United States and Japan are developing new batteries. CATL faces challenges? How should China's new energy battery industry respond?
- Murata launches high-precision 6-axis inertial sensor for automobiles
- Ford patents pre-charge alarm to help save costs and respond to emergencies
- New real-time microcontroller system from Texas Instruments enables smarter processing in automotive and industrial applications
- Counting TI's star products in T-BOX: Automotive Ethernet | Section 1 DP83TC811S-Q1: Automotive Ethernet makes your T-BOX...
- How to design an accurate and thermally efficient wearable body temperature detection system?
- Is it true that the greater the memory depth of an oscilloscope, the better?
- Brief Introduction of Non-Magnetic Coil Solution for National Technology Intelligent Water Meter
- Adjusting the fire power of the induction cooker with a magnetic switch
- Are there any 6-channel analog switches that you would recommend?
- How is the current transformer used?
- Sensor Basics and Common Terms
- "Power supply obstacle" + voltage stress
- About LM2611