Multi-axis inertial sensors have become increasingly popular in the medical application market. Inertial MEMS components that integrate multi-axis sensing functions have excellent performance in terms of size, power consumption, accuracy and reliability, and can meet the stringent requirements of medical applications. Precision medical instruments such as surgical navigation tools have begun to be introduced in large quantities.
Navigation is associated with cars, trucks, planes, ships and people. However, it is also beginning to play an important role in the field of medical technology, where precision surgical instruments and robots require navigation. The design requirements of surgical navigation tools have broad commonality with traditional vehicle navigation, but the former also presents some unique challenges, such as indoor use, lack of access to global satellite positioning system (GPS) support, and the need for higher performance.
This article will examine the unique challenges of medical navigation applications and explore possible solutions from sensor mechanisms to system characteristics, and introduce methods to enhance sensing performance, such as using Kalman filtering.
Multi-axis MEMS sensors transform medical information
Microelectromechanical systems (MEMS) are a mature technology that most people encounter every day, making cars safer, enhancing the usability of cell phones, and improving the performance of tools and sports equipment, thereby improving the level of medical care for patients.
MEMS components used for linear motion sensing are typically based on a micromachined polysilicon surface structure formed on a silicon wafer and suspended from the surface of the wafer by polysilicon springs, providing resistance to acceleration forces. Under acceleration, the deflection of the MEMS axis is measured by a differential capacitor consisting of an independent fixed plate and a plate connected to the moving mass. In this way, the motion unbalances the differential capacitor, resulting in the magnitude of the sensor output being proportional to the acceleration.
For example, when a car suddenly decelerates due to a collision, the MEMS axis in the airbag sensor will produce the same movement, causing the capacitor to unbalance and eventually generate a signal to trigger the airbag to deploy. This basic accelerometer structure can be adjusted according to different application performance parameters and with the addition of data processing functions, it can accurately indicate tilt, speed and even position. Another technically related structure is the gyroscope, which can detect the rotation rate and output it in degrees per second.
The ability to accurately detect and measure motion through a tiny component that consumes very little power is valuable in almost any application involving motion. Table 1 lists the basic medical applications by type of motion.
While simple motion sensing is valuable, such as linear motion in one axis, most applications involve multiple types of motion in multiple axes. Capturing this multi-dimensional motion not only brings new benefits, but also maintains accuracy in situations where off-axis disturbances may affect single-axis motion measurements.
To accurately measure the motion experienced by an object, multiple types of sensors (such as linear and rotation) must be combined. For example, accelerometers are sensitive to the Earth's gravity and can be used to determine the angle of inclination. In other words, when a MEMS accelerometer is rotated (±90 degrees) in a ±1g gravity field, it can convert the motion into an angular representation.
However, accelerometers cannot distinguish between static acceleration (gravity) and dynamic acceleration. Therefore, accelerometers are combined with gyroscopes to use the additional data processing capabilities of the combined components to distinguish between linear acceleration and tilt (i.e., when the gyroscope output shows a rotation that coincides with the apparent tilt recorded by the accelerometer). As the system's dynamics (number of axes of motion and degrees of freedom of movement) increase, the sensor fusion process becomes more complex.
It is also important to understand the impact of the environment on sensor accuracy. An obvious factor is temperature, which can be calibrated. In fact, high-precision sensors can be recalibrated and dynamically compensate themselves. Another less obvious consideration is the potential for vibration. Even very slight vibrations can shift the accuracy of the rotation rate sensor. This effect is called linear acceleration effect and vibration correction, and its impact can be severe, depending on the quality of the gyroscope. In this case, sensor fusion can also improve performance, that is, using the accelerometer to detect linear acceleration and then using this information and calibration information about the gyroscope's linear acceleration sensitivity to correct for it.
Inertial sensors help medical navigation to emerge
Many applications require multi-degree-of-freedom motion sensing, such as a six-axis inertial sensor that can simultaneously detect linear acceleration and rotational motion (also known as roll, pitch, and yaw) in the x, y, and z axes.
Inertial sensors are widely used in industry as an auxiliary navigation element. Usually, inertial sensors are used together with other navigation devices such as GPS. When the GPS connection is unreliable, inertial navigation can be enhanced by dead reckoning technology.
For all but the simplest navigation, most solutions rely on multiple types of sensors to provide the required accuracy and performance under all conditions. GPS, optical, and magnetic sensing technologies are well known and available in a wide variety of products, however, each has its own limitations and even when used together, they cannot fully compensate for each other’s inaccuracies. MEMS inertial sensors have the potential to fully compensate for sensor inaccuracies because they do not have the aforementioned interferences and do not require external infrastructure: no satellites, magnetic fields, or cameras, just inertia. Table 2 lists the main navigation sensor technologies and their pros and cons.
Just as vehicle navigation devices experience GPS blockage, optical navigation technology used in medical systems also encounters line-of-sight blockage. Inertial sensors can perform dead reckoning when optical blockage occurs, thereby enhancing system reliability through redundant detection.
One medical application that fits the principles listed in Table 2 is the use of inertial sensors in the operating room to more precisely align an artificial knee or hip joint to the patient's unique bone structure. The goal in this case is to align the implant to less than 1 degree relative to the patient's natural axis. More than 95% of total knee replacement (TKA) surgeries use mechanical alignment methods, which typically produce errors of 3 degrees or more.
Computer-assisted methods using optical alignment have begun to replace some mechanical procedures, but adoption has been slow, perhaps because of the high cost of the equipment. Whether using mechanical or optical alignment, misalignment (defined as a 3-degree error or more) occurs in about 30% of these surgeries, causing discomfort to the patient and often requiring additional surgery. Possible benefits of reducing misalignment include shorter surgical times, greater patient comfort, and longer-lasting joint replacements.
Inertial sensors in the form of a full multi-axis inertial measurement unit (IMU) have been shown to significantly improve the accuracy of TKA surgery. The MEMS-based inertial sensing unit contains all the required sensing functions, including three linear sensors and three rotational sensors, which can replace mechanical and optical-based alignment technologies. The component uses multiple types of sensors and embedded processing to dynamically correct sensor drift, such as linear acceleration offset of gyroscopes, temperature drift of linear and rotational sensing, etc. This relatively complex precision sensor package can be easily connected through a standard four-wire serial peripheral interface (SPI).
MEMS inertial sensors are highly reliable (as evidenced by their 20-year history in the automotive industry) and their successful use in mobile phones and video games make them very attractive. However, performance requirements vary greatly from application to application, and components suitable for gaming will not solve the high-performance navigation problem described in this article. For navigation, the important MEMS performance indicators are bias drift, vibration effects, sensitivity, and noise. The performance level required for precision industrial and medical navigation is typically an order of magnitude higher than the performance level of MEMS sensors used in consumer electronic devices. Table 3 lists general system considerations that can help in selecting sensors.
Most systems incorporate some form of Kalman filter to effectively combine multiple sensor types. The Kalman filter takes into account the system dynamics model, the relative accuracy of the sensors, and other application-specific control inputs to effectively determine the most realistic motion scenario. High-precision inertial sensors (low noise, low drift, stable over temperature/time/vibration/power supply variations) reduce the complexity of the Kalman filter, the number of redundant sensors required, and the number of constraints on the allowable system operating scenarios.
Medical applications are complex and MEMS technology continues to evolve
While sensors have enabled a wide variety of medical applications, from relatively simple motion capture to complex motion analysis, the high performance requirements of medical sensors present complex and computationally intensive design challenges. Fortunately, many of the principles required to solve these next-generation medical challenges are based on methods proven in industrial navigation applications, including sensor fusion and processing techniques. In the field of medical navigation, the complexity of motion and the requirements for accuracy and reliability will drive the development of multiple processors, additional sensor post-processing, complex algorithms, and complex testing and compensation schemes.
While consumer applications strongly pursue small size, low power consumption, multi-axis inertial sensors, some developers also value high-precision, low power consumption, high-performance sensors that can be stable and reliable under various environmental conditions. Compared with existing measurement and detection technologies, these inertial MEMS components have advantages in accuracy, size, power consumption, redundancy and accessible performance.
Previous article:Design of smart grid power meter lock management system
Next article:MAX8873, MAX8874 Low-Dropout, 120mA Linear Regulators Data Sheet
Recommended ReadingLatest update time:2024-11-16 14:47
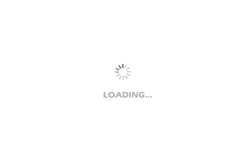
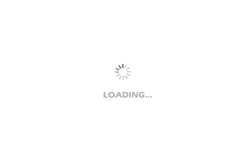
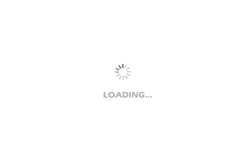
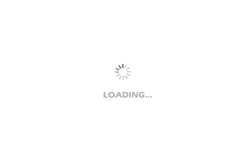
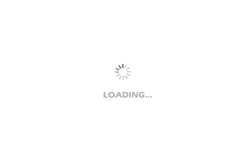
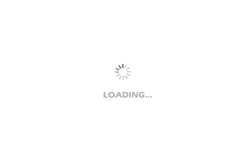
- Popular Resources
- Popular amplifiers
-
Analysis and Implementation of MAC Protocol for Wireless Sensor Networks (by Yang Zhijun, Xie Xianjie, and Ding Hongwei)
-
Introduction to Internet of Things Engineering 2nd Edition (Gongyi Wu)
-
西门子S7-12001500 PLC SCL语言编程从入门到精通 (北岛李工)
-
Modern Motor Control Technology (Wang Chengyuan, Xia Jiakuan, Sun Yibiao)
- High signal-to-noise ratio MEMS microphone drives artificial intelligence interaction
- Advantages of using a differential-to-single-ended RF amplifier in a transmit signal chain design
- ON Semiconductor CEO Appears at Munich Electronica Show and Launches Treo Platform
- ON Semiconductor Launches Industry-Leading Analog and Mixed-Signal Platform
- Analog Devices ADAQ7767-1 μModule DAQ Solution for Rapid Development of Precision Data Acquisition Systems Now Available at Mouser
- Domestic high-precision, high-speed ADC chips are on the rise
- Microcontrollers that combine Hi-Fi, intelligence and USB multi-channel features – ushering in a new era of digital audio
- Using capacitive PGA, Naxin Micro launches high-precision multi-channel 24/16-bit Δ-Σ ADC
- Fully Differential Amplifier Provides High Voltage, Low Noise Signals for Precision Data Acquisition Signal Chain
- Innolux's intelligent steer-by-wire solution makes cars smarter and safer
- 8051 MCU - Parity Check
- How to efficiently balance the sensitivity of tactile sensing interfaces
- What should I do if the servo motor shakes? What causes the servo motor to shake quickly?
- 【Brushless Motor】Analysis of three-phase BLDC motor and sharing of two popular development boards
- Midea Industrial Technology's subsidiaries Clou Electronics and Hekang New Energy jointly appeared at the Munich Battery Energy Storage Exhibition and Solar Energy Exhibition
- Guoxin Sichen | Application of ferroelectric memory PB85RS2MC in power battery management, with a capacity of 2M
- Analysis of common faults of frequency converter
- In a head-on competition with Qualcomm, what kind of cockpit products has Intel come up with?
- Dalian Rongke's all-vanadium liquid flow battery energy storage equipment industrialization project has entered the sprint stage before production
- Allegro MicroSystems Introduces Advanced Magnetic and Inductive Position Sensing Solutions at Electronica 2024
- Car key in the left hand, liveness detection radar in the right hand, UWB is imperative for cars!
- After a decade of rapid development, domestic CIS has entered the market
- Aegis Dagger Battery + Thor EM-i Super Hybrid, Geely New Energy has thrown out two "king bombs"
- A brief discussion on functional safety - fault, error, and failure
- In the smart car 2.0 cycle, these core industry chains are facing major opportunities!
- The United States and Japan are developing new batteries. CATL faces challenges? How should China's new energy battery industry respond?
- Murata launches high-precision 6-axis inertial sensor for automobiles
- Ford patents pre-charge alarm to help save costs and respond to emergencies
- New real-time microcontroller system from Texas Instruments enables smarter processing in automotive and industrial applications
- TouchGFX design by ddllxxrr
- As the party A, it's a bit painful...
- Internal structure of ESP8266 chip
- EEWORLD University ---- Tektronix uses mixed signal oscilloscope to explore the secrets of the bus
- Why choose 120Ω? The terminal resistance value recommended by the CAN standard
- Is there any sensor expert?
- About New Energy Vehicle Mode 2 IC-CPD Charging Gun Type A Leakage Current Sensor
- Help! What brand are the 2 UV sensors in the picture?
- Please tell me the pin definition of EPM7128S 100 pin. . . .
- BQ25120 Battery Management IC Problem Solving Sharing