Measurement compatibility
It is very important to ensure the compatibility between the pressure sensor and its actual application. Before making a pressure sensor selection, the following aspects should be considered: (1) material (2) chemical substance (3) concentration (4) temperature (5) exposure time (6) exposure form (7) failure criteria and (8) general information, such as application environment, device protection and other equipment components in the area.
In all cases, the user is ultimately responsible for ensuring the compatibility of the sensor with the measured medium.
Errors that affect pressure sensor performance
When calculating the total error of a pressure sensor, the following defined errors should be used. To determine the extent of the specific error of the pressure sensor you have selected, refer to the specifications for that sensor in this catalog.
Note: Some nominal specifications can be reduced or eliminated in specific user applications. For example, if a pressure sensor is used within half of its specified temperature range, the temperature error can be reduced by half. If automatic zeroing techniques are used, zero offset and zero drift errors can be eliminated.
Zero offset is the sensor output when the same pressure is applied to both sides of the diaphragm.
Range It is the algebraic difference between the output endpoints. Usually the two endpoints are zero and full scale.
Zero point temperature drift It is the zero point change caused by temperature change. Zero point drift is not a predictable error because each device can drift up or down, and temperature change will cause the entire output curve to shift up or down along the voltage axis. (Figure 1).
Figure 1 Zero offset error
Sensitivity temperature drift is the change in sensitivity caused by temperature changes, which will cause the slope of the sensor output curve to change (Figure 2).
Figure 2 Sensitivity offset error
Linearity error is the deviation of the sensor output curve from a calibrated straight line over the desired pressure range. One method of calculating linearity error is the least squares method, which mathematically provides the best fit straight line (B. FSL) for the data points (Figure 3).
Figure 3 Best fit straight line linearity
Another method is terminal base point linearity (TBL) or endpoint linearity. TBL is determined by drawing a straight line (L1) between the two end data points on the output curve. Then a perpendicular line is drawn from line L1 to the output curve, and the intersecting data points are selected to achieve the maximum length of the perpendicular line. The length of the perpendicular line represents the terminal base point linearity error (Figure 4).
Figure 4 End point linearity
Repeatability error is the deviation in the output reading for any given input pressure when all other conditions remain constant (Figure 5).
Figure 5
Hysteresis error Usually expressed as a combination of mechanical hysteresis and temperature hysteresis. (Figure 6).
Figure 6
Mechanical hysteresis : refers to the error of the output at a given input pressure (in different processes of rising and falling).
Temperature hysteresis is the deviation in output at a given input pressure before and after a temperature cycle.
Ratio Variation Ratio variation refers to the ratio of the sensor output to the supply voltage when other conditions remain constant. Ratio variation error is the change in this ratio, usually expressed as a percentage of the range.
Calculation accuracy or total error
When selecting a pressure sensor, the total error effect is important. The following method takes into account the individual errors as well as the interchangeability errors between components.
Two methods for calculating the total error are:
Root mean square sum of squares (RSS) and maximum and worst case errors. In practice, the RSS method gives the most accurate and realistic values, while in the case of the worst case error method, the probability that all errors of a pressure sensor are in the maximum case is very small.
example:
An application requires 0-15psig, 5°C to 50°C temperature range and 7VDC power supply, 142PCI5G
Step 1: Determine different error rates
parameter
Zero offset
Range error
Linearity
Zero/full scale drift synthesis
Error (calculating maximum and minimum application temperatures, use the larger of the two numbers) = 0.5%
Repeatability & hysteresis: 0.3%
1-year stability: 1.0%
Ratio error: 1.0%
Step 2 Calculate the total error
RSS method: Take the square root of the sum of the squares of the above determinations and errors
RSS maximum error maximum range.
Worst case error = 2.3%.
The worst case error is the sum of all maximum errors = 1.0+1.0+0.75+0.7+0.3+1.0+1.0.
Worst case error = 5.57% absolute maximum range.
Previous article:Design of a power supply protection device with configurable load threshold
Next article:Comprehensive management of multimedia processor power
Recommended ReadingLatest update time:2024-11-16 15:53
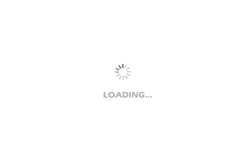
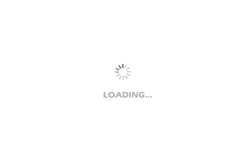
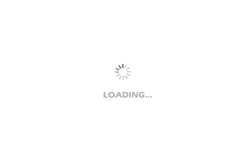
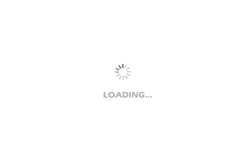
- Popular Resources
- Popular amplifiers
-
Analysis and Implementation of MAC Protocol for Wireless Sensor Networks (by Yang Zhijun, Xie Xianjie, and Ding Hongwei)
-
Introduction to Internet of Things Engineering 2nd Edition (Gongyi Wu)
-
西门子S7-12001500 PLC SCL语言编程从入门到精通 (北岛李工)
-
Modern Motor Control Technology (Wang Chengyuan, Xia Jiakuan, Sun Yibiao)
- MathWorks and NXP Collaborate to Launch Model-Based Design Toolbox for Battery Management Systems
- STMicroelectronics' advanced galvanically isolated gate driver STGAP3S provides flexible protection for IGBTs and SiC MOSFETs
- New diaphragm-free solid-state lithium battery technology is launched: the distance between the positive and negative electrodes is less than 0.000001 meters
- [“Source” Observe the Autumn Series] Application and testing of the next generation of semiconductor gallium oxide device photodetectors
- 采用自主设计封装,绝缘电阻显著提高!ROHM开发出更高电压xEV系统的SiC肖特基势垒二极管
- Will GaN replace SiC? PI's disruptive 1700V InnoMux2 is here to demonstrate
- From Isolation to the Third and a Half Generation: Understanding Naxinwei's Gate Driver IC in One Article
- The appeal of 48 V technology: importance, benefits and key factors in system-level applications
- Important breakthrough in recycling of used lithium-ion batteries
- Innolux's intelligent steer-by-wire solution makes cars smarter and safer
- 8051 MCU - Parity Check
- How to efficiently balance the sensitivity of tactile sensing interfaces
- What should I do if the servo motor shakes? What causes the servo motor to shake quickly?
- 【Brushless Motor】Analysis of three-phase BLDC motor and sharing of two popular development boards
- Midea Industrial Technology's subsidiaries Clou Electronics and Hekang New Energy jointly appeared at the Munich Battery Energy Storage Exhibition and Solar Energy Exhibition
- Guoxin Sichen | Application of ferroelectric memory PB85RS2MC in power battery management, with a capacity of 2M
- Analysis of common faults of frequency converter
- In a head-on competition with Qualcomm, what kind of cockpit products has Intel come up with?
- Dalian Rongke's all-vanadium liquid flow battery energy storage equipment industrialization project has entered the sprint stage before production
- Allegro MicroSystems Introduces Advanced Magnetic and Inductive Position Sensing Solutions at Electronica 2024
- Car key in the left hand, liveness detection radar in the right hand, UWB is imperative for cars!
- After a decade of rapid development, domestic CIS has entered the market
- Aegis Dagger Battery + Thor EM-i Super Hybrid, Geely New Energy has thrown out two "king bombs"
- A brief discussion on functional safety - fault, error, and failure
- In the smart car 2.0 cycle, these core industry chains are facing major opportunities!
- The United States and Japan are developing new batteries. CATL faces challenges? How should China's new energy battery industry respond?
- Murata launches high-precision 6-axis inertial sensor for automobiles
- Ford patents pre-charge alarm to help save costs and respond to emergencies
- New real-time microcontroller system from Texas Instruments enables smarter processing in automotive and industrial applications
- Interface corresponding to SNVS_TAMPER3 signal
- Looking for a good and available domestic accelerometer
- nRF52832-QFAA Hardware Reference Design
- How to design the MCU+8266 program structure
- 【RPi PICO】Snapshot of the RP2040 chip
- Why does TIM1_CH3N not output PWM after configuring PWM in STM32F103C8T6?
- Please advise on the PinMux code
- Can you recommend a chip that can boost 3.3V to 5V?
- How to quickly gain points?
- [National Technology N32G457 Review] RT_Thread solves the problem that SPI NSS cannot be pulled low