RFID is a rapid identification technology that has developed rapidly in recent years. It obtains the stored information code through contactless identification of the tag carrier. The tag carrier is also commonly known as an electronic tag (TAG). Compared with traditional barcode technology, the electronic tag has the advantages of large data memory capacity, read and write, contactless identification, high temperature resistance, corrosion resistance and adaptability to harsh environments. It also has the ability to penetrate and can be read and written without obstacles. It can penetrate non-metallic or non-transparent materials such as paper, wood, plastic, etc., and the misreading rate is also low. Therefore, it is widely used in various industries.
This article introduces the use of RFID technology in the automotive manufacturing industry based on actual project experience to achieve tracking and management of body information in the paint shop.
2. Overall system structure
2.1 Structure of vehicle body tracking system
The paint shop of the second plant of Dongfeng Peugeot Citroen Automobile Co., Ltd. in Wuhan has reached the benchmark level of PSA's global lean model factory from production management to manufacturing process equipment and technology. The body tracking system inside the workshop adopts the current advanced RFID identification technology. The overall design structure of the system is shown in Figure 1. From the control perspective, it is roughly divided into three levels as shown in the figure: basic equipment layer, control layer, and central management layer; the ERP layer belongs to the enterprise management layer. The body data flow is shown by the arrows in the figure. Data is transmitted bidirectionally between each level, and the body information required for production management is permanently stored in the data server. During the production process, processes, robots, and conveying equipment can obtain the body information necessary to guide production from electronic tags.
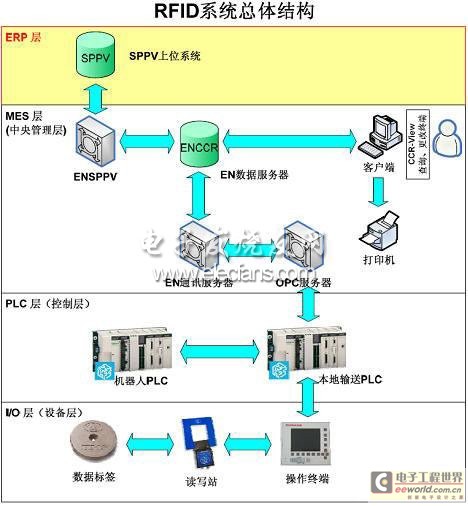
Figure 1 Overall structure of RFID system
2.2 Brief description of tasks of each component of the system
1) Central management: EN data server is the data processing management center of the whole system. It is responsible for information management and production process control, connected to the enterprise ERP system, and manages the production logistics guidance and information collection of the entire paint shop. The on-site client affiliated to the central control system can realize online query and modification of the actual body information in the workshop, such as color, model, etc., through the application system CCR-View operation platform.
2) Control layer: The local conveyor PLC mainly controls the operation of the conveyor chain and is responsible for uploading and issuing vehicle body information. After receiving the information sent by the central management, it is responsible for transmitting it to the lower-level read/write station. After receiving the information uploaded by the lower-level read/write station, it is responsible for transmitting it to the robot PLC, large-screen display board and process PLC. When the electrophoresis line control PLC receives different vehicle model information, it can call different voltage parameters; the painting robot PLC can select different spraying trajectories and paint pipelines according to the received vehicle model and color information, thereby realizing process control. This project uses Schneider Premium 57 series 5634M CPU and uses Ethernet connection to realize information transmission.
3) Basic equipment layer: mainly includes complete RFID (radio frequency identification system) and field operation terminal. RFID system includes electronic tags (Tags) and read/write stations. Electronic tags are used to store necessary vehicle logistics information. Read/write stations read and write data from tags. The communication protocol of read/write stations is based on TCP/IP and is directly connected to the control PLC through Ethernet. Field operation terminals are used to control read/write stations, provide a human-computer interaction interface, display relevant information stored in electronic tags, and realize local information entry, modification, query and other functions in emergency or information error situations.
3. System functions
3.1 Information transmission methods and characteristics before using RFID
Before using RFID technology, the storage of vehicle body information was mainly paper barcodes. The barcode method is to set up the client of the enterprise management SPPV system at the functional demand point, and query the database of the SPPV system by reading the barcode to obtain the required vehicle body information and guide production management. The advantage is convenience and flexibility, and the disadvantage is that it has great limitations in helping workshop production management. It can only provide information such as model and color, and cannot be integrated into the control of the workshop automation system. With the development of optoelectronic technology, for a period of time, many automobile companies also used a barcode extension technology-mechanical barcode (mechanical comb), which is to install a unique steel barcode on each sled, and use photoelectric sensors to scan and read and write to complete the transmission of different vehicle body information. Its characteristics are that the vehicle body information must be stored in the PLC, and a dedicated body data PLC is set to manage the data of all body bodies running inside the workshop. The BODY DATA PLC has a large amount of data exchange when the workshop is running, so the PLC performance requirements are high, large-capacity memory, and high requirements for the speed and reliability of network communication.
3.2 RFID Solution
After adopting the RFID system, an electronic tag is installed in the protective box at the bottom of each sled. The electronic tag stores a large amount of information such as barcode, vehicle model, color, vehicle definition code, etc., forming multiple small mobile databases that can be read and written through read-write stations throughout the production process. After multiple technical investigations and program demonstrations, the Wuhan Second Plant paint project selected the RFID identification system of EMS. The electronic tag uses the HMS150HT high temperature series product that can withstand up to 240°C. The mobile electronic tag stores a large amount of vehicle body and logistics guidance information (see Figure 2).
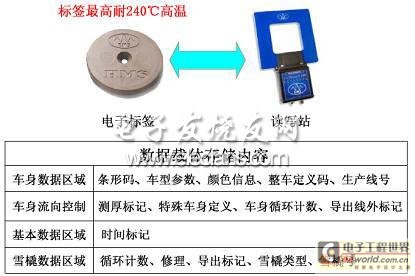
Figure 2 Mobile electronic tag
Therefore, when the local PLC and the data server communicate abnormally, the RFID system can still produce using the information stored in the electronic tag, and will not cause large-scale production to be terminated. The read/write head uses HF-CNTL-IND-02, and the communication protocol is based on TCP/IP, which has faster transmission speed and better stability. According to the needs of production and management functions, a total of 26 sets of read/write stations are set up at the entrances and exits of the paint shop, the bifurcation of workpiece logistics, and the entrances of important process steps (such as electrophoresis lines, UBS lines, spray booths, storage areas, etc.), so as to realize RFID tracking management and control of the entire production process from the car body entering the paint shop to the final assembly.
3.3 Main functions of the vehicle body tracking system
3.3.1 Production management guidance function
1) Car body data guides robots and humans to identify car models and spray colors.
2) Management of various types of body logistics: including body import, export, side thickness management, multiple cycle statistics, etc.
3) Vehicle management: including bottom and top paint sleds, UBS sling cleaning, export repair, etc.
4) Transmit vehicle body information to downstream workshop systems.
3.3.2 Information statistics report function
1) Real-time statistics of the number of work-in-progress in each process section and production line area,
2) Statistical reports on production information such as shift, day, and month,
3) Count the number of car bodies produced by time period, model and color
3.3.3 Real-time monitoring function of production line
1) Find the specific location of a vehicle, such as a storage area or repair room,
2) Check the status of the car body in the paint shop online or historically,
As an important submodule of the paint shop ENCCR system, various relevant production management personnel log in with independent usage permissions and can enter the RFID body tracking system from the central control room or the on-site client CCR-View platform to realize real-time query and printing of production information.
4. Software Design
4.1 Internal structure of the standard function block of the read/write station
In terms of software, the paint shop monitoring system of the second factory uses InTouch 9.0 of Wonderware as the upper computer configuration software. The read/write station uses the standard Ethernet protocol to connect and communicate with the operation terminal and PLC. The communication program between the PLC and the read/write station controller is the read/write station function block MFC_MAIN of the Premium PLC developed with Unity Pro. The MFC_MAIN function block covers all necessary program logic related to the read/write station. The program block structure is shown in Figure 3:
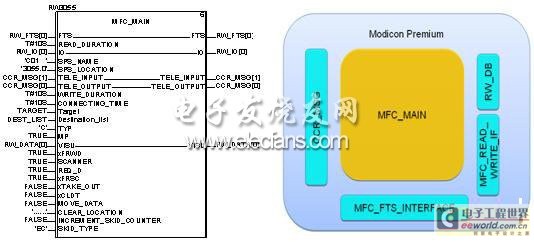
Figure 3 Program block structure
The internal structure of the main program block mainly includes the message CCR_MSG with the central monitoring system, the interface MFC_FTS_IF with the conveying system, the interface MFC_READ_WRITE_IF with the read-write system, and the data interface RW_DB with the operating terminal.
Previous article:Design of indoor positioning system based on RFID
Next article:Data recording system based on wireless communication technology
Recommended ReadingLatest update time:2024-11-16 15:59
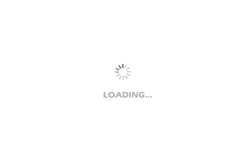
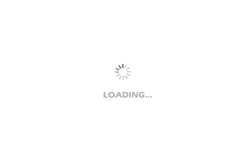
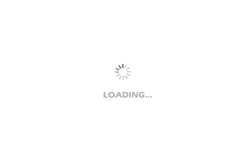
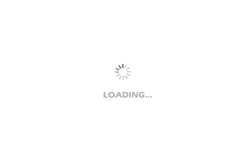
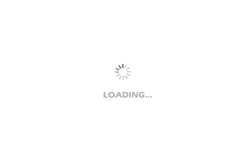
- Popular Resources
- Popular amplifiers
-
Radio Frequency Identification (RFID) System Technology and Application (Written by Ci Xinxin, Wang Subin, and Wang Shuo)
-
Introduction to Internet of Things Engineering 2nd Edition (Gongyi Wu)
-
Detailed explanation and engineering practice of unmanned monitoring technology (Xie Jianbin, Li Peiqin, Yan Wei, Liu Tong, Lin Chenglong, Hong Quanyi, Zhou Hongfei, Cui Yibing)
-
Introduction to Wireless Sensor Networks (Edited by Ma Sasa et al.)
- High signal-to-noise ratio MEMS microphone drives artificial intelligence interaction
- Advantages of using a differential-to-single-ended RF amplifier in a transmit signal chain design
- ON Semiconductor CEO Appears at Munich Electronica Show and Launches Treo Platform
- ON Semiconductor Launches Industry-Leading Analog and Mixed-Signal Platform
- Analog Devices ADAQ7767-1 μModule DAQ Solution for Rapid Development of Precision Data Acquisition Systems Now Available at Mouser
- Domestic high-precision, high-speed ADC chips are on the rise
- Microcontrollers that combine Hi-Fi, intelligence and USB multi-channel features – ushering in a new era of digital audio
- Using capacitive PGA, Naxin Micro launches high-precision multi-channel 24/16-bit Δ-Σ ADC
- Fully Differential Amplifier Provides High Voltage, Low Noise Signals for Precision Data Acquisition Signal Chain
- Innolux's intelligent steer-by-wire solution makes cars smarter and safer
- 8051 MCU - Parity Check
- How to efficiently balance the sensitivity of tactile sensing interfaces
- What should I do if the servo motor shakes? What causes the servo motor to shake quickly?
- 【Brushless Motor】Analysis of three-phase BLDC motor and sharing of two popular development boards
- Midea Industrial Technology's subsidiaries Clou Electronics and Hekang New Energy jointly appeared at the Munich Battery Energy Storage Exhibition and Solar Energy Exhibition
- Guoxin Sichen | Application of ferroelectric memory PB85RS2MC in power battery management, with a capacity of 2M
- Analysis of common faults of frequency converter
- In a head-on competition with Qualcomm, what kind of cockpit products has Intel come up with?
- Dalian Rongke's all-vanadium liquid flow battery energy storage equipment industrialization project has entered the sprint stage before production
- Allegro MicroSystems Introduces Advanced Magnetic and Inductive Position Sensing Solutions at Electronica 2024
- Car key in the left hand, liveness detection radar in the right hand, UWB is imperative for cars!
- After a decade of rapid development, domestic CIS has entered the market
- Aegis Dagger Battery + Thor EM-i Super Hybrid, Geely New Energy has thrown out two "king bombs"
- A brief discussion on functional safety - fault, error, and failure
- In the smart car 2.0 cycle, these core industry chains are facing major opportunities!
- The United States and Japan are developing new batteries. CATL faces challenges? How should China's new energy battery industry respond?
- Murata launches high-precision 6-axis inertial sensor for automobiles
- Ford patents pre-charge alarm to help save costs and respond to emergencies
- New real-time microcontroller system from Texas Instruments enables smarter processing in automotive and industrial applications
- 15 "Wanli" Raspberry Pi car - photoelectric encoder learning (forward and reverse judgment)
- A TOF "image" sensor that is worth playing with, VL53L5CX
- ARM immediate number explanation--the difference between LDR and MOV
- i.MX283 latest virtual machine system guide
- TI C5000 compiler error message list
- TI Award-winning Live Broadcast: Talking about "packaged antenna" smart millimeter wave sensors, even novices can handle industrial robots
- The voltage of the TPS73033 buck chip drops to 0.7V after the load is connected
- Wi-Fi 6 is here to provide network coverage for the entire home. Will you adopt it?
- Common APDU instruction error codes for CPU cards
- [GigaDevice GD32F310 Review] +ADC Data Collection