RFID ( Radio Frequency Identification) is a contactless automatic identification technology that began to emerge in the 1990s. It is a technology that uses radio frequency signals to achieve contactless information transmission through spatial coupling and achieves identification through the transmitted information.
Based on the actual production of the tobacco industry, this paper proposes a method of using RFID electronic tags in pallets for stacked transportation. By combining barcodes with RFID electronic tags, the problem of interaction and unification of logistics and information flow of stacked cigarettes is solved.
1. Radio Frequency Identification (RFID) System
An RFID system usually consists of three parts, as shown in Figure 1, namely, an RFID reader/writer, an RFID card, and an antenna. When the RFID reader/writer is working, it sends a radio frequency signal of a certain frequency through the antenna. When the RFID card enters the magnetic field, it generates an induced current and uses this energy to send out its own encoding and other information. The reader/writer reads the information and decodes it to obtain the data in the card. When writing data, the reader/writer transmits the write instruction information and the written data to the RFID card by emitting radio waves of a specific frequency, and the RFID card writes the data into the card according to the specified address.
Figure 1 RFID system composition
2. System Design and Implementation
1. System design
The system is designed with four parts: palletizing data generation, electronic tag writing, warehouse smoke information data adjustment, pallet factory scanning and municipal company arrival scanning.
First, the palletizing data is generated. In the palletizing process, the barcode information of each cigarette piece corresponding to each pallet is collected through a fixed scanner, and after the barcode data of these cigarette pieces are compressed, the compressed information is written into the electronic tag installed on the pallet through the electronic tag reading and writing device.
Secondly, the palletizing data is adjusted. In the storage link, the barcode data A of the cigarette pieces to be adjusted is collected by the barcode collection equipment, and the barcode data B of the cigarette pieces stored in the adjusted pallet is collected by the mobile electronic tag reading and writing equipment. Then the data of B is decompressed to form the pallet barcode data composition C. According to the adjustment function of A (increase, decrease, replacement), it is compared and adjusted with C to obtain the adjusted pallet data group D. D is compressed to obtain E, and then E is written into the electronic tag installed on the pallet through the mobile electronic tag reading and writing equipment.
Third, scan by stack before leaving the factory. When leaving the factory, use the RFID reader to read the barcode data of the cigarettes stored in the electronic tag on the stack pallet and decompress the data. Finally, realize the docking with the factory scanning system of "one dot, two scans" (that is, affix a barcode uniformly issued by the competent department to each cigarette produced, and scan it when leaving the warehouse and when entering the warehouse by the sales company).
Finally, the RFID code is scanned according to the arrival of the stack, and the barcode data of the cigarettes stored in the electronic tag on the stack pallet is read to decompress the data, and finally it is connected with the one-dozen-two-scan commercial arrival scanning system.
Management system implementation method #e#
2. Implementation of the management system
1 Application equipment
The management system is mainly applied to hardware equipment such as RFID tags, fixed reading and writing devices, handheld reading and writing devices, and RFID forklifts, as well as software such as RFID digital warehouse management system.
Among them, the RFID electronic tag XCTF-5013 is specially designed for the requirements of this project. It can be directly and conveniently installed in the pallet, effectively preventing the label from falling off and convenient for removal. The fixed reading and writing equipment is used in automatic stackers, conveyors, and elevators. The RFID reader will pass the pallet information read to the PLC for corresponding processing. The handheld reading and writing equipment is used for manual stacking, that is, first read the information, then read the barcode information on each cigarette one by one, pass this information to the system, and associate it in the database. The RFID forklift is used for pallet modification, and the pallet information is read by the RFID reader, and then the barcodes on the removed and supplemented cigarettes are scanned one by one with a wireless scanner, and all data are uploaded to the system to update the database.
In terms of software, the RFID digital warehouse management system includes the goods receiving management system, warehouse business management system, pallet in and out management system, interface service middleware, etc.
2 Application Process
Warehousing: When the goods enter the warehouse through the conveyor belt at the entrance, the cargo information of each pallet is written into the pallet through the reader at the entrance, and then the delivery location is calculated through the computer warehouse management system, and the inventory instructions are sent to the forklift vehicle system through the network system, and the goods are stored in the corresponding location as required.
Outbound delivery: After receiving the delivery instruction, the forklift goes to the designated cargo location to pick up the pallet cargo. Before picking up the cargo, the forklift reader/writer confirms the accuracy of the pallet cargo again. Then the pallet cargo is sent to the delivery port conveyor belt. The reader/writer on the delivery port conveyor belt reads the pallet label information to see if it is correct. If it is verified to be correct, the cargo is shipped.
3. Effect Analysis
When cigarettes enter the circulation field, at each station in the circulation field, the RFID system can automatically add relevant information using the reading and writing devices configured in each circulation link, without the need for manual intervention. After the cigarettes are transported to the storage center, the system automatically reads the RFID tag of each cigarette at the same time, and transmits it to the background storage and basic service platform, which will transmit the specific information of the arrival to the cigarettes for confirmation. The detailed information of each box of cigarettes is read by the RFID reader on the forklift and transmitted to the background to determine its storage method and location. The RFID reader on the conveyor belt reads the information of each cigarette and automatically sorts it according to the distribution list. After sorting, the various types of cigarettes are read by the RFID reader located on the packaging machine for final confirmation and then loaded for transportation. The cigarettes sent out are read at the warehouse door and then transmitted to the background logistics storage system and basic service platform.
Therefore, any RFID tag can clearly and accurately tell us the "identity", storage and transportation history, destination and other useful information of the cigarette. Once there is a problem with the product, RFID is a 100% solution to track the source of the cigarette, and can answer questions such as "where do the cigarettes come from, is the middleware processing link perfect", and give detailed and reliable answers. The logistics distribution and warehousing center receives the detailed list of cigarette transportation from the tobacco basic service platform, and arranges the storage plan in time according to the quantity, type and arrival time.
In short, RFID has great advantages and development space in supply chain management. It eliminates the mixing of finished cigarettes in cartons or on pallets, ensures that the correct products are delivered to the right place, realizes automatic sorting operations, eliminates manual operations, and can achieve full-line tracking of product information, making product supply and demand more reasonable and rapid.
Previous article:Application of RFID technology in muck truck management
Next article:Design of reader-writer for agricultural product production line based on RFID
Recommended ReadingLatest update time:2024-11-16 17:56
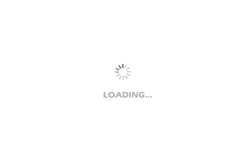
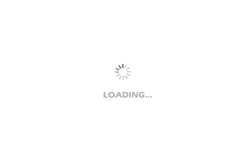
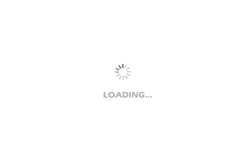
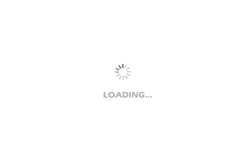
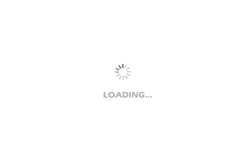
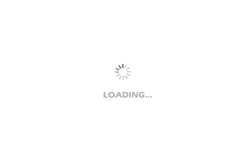
- Popular Resources
- Popular amplifiers
-
Radio Frequency Identification (RFID) System Technology and Application (Written by Ci Xinxin, Wang Subin, and Wang Shuo)
-
Introduction to Internet of Things Engineering 2nd Edition (Gongyi Wu)
-
Detailed explanation and engineering practice of unmanned monitoring technology (Xie Jianbin, Li Peiqin, Yan Wei, Liu Tong, Lin Chenglong, Hong Quanyi, Zhou Hongfei, Cui Yibing)
-
Introduction to Wireless Sensor Networks (Edited by Ma Sasa et al.)
- High signal-to-noise ratio MEMS microphone drives artificial intelligence interaction
- Advantages of using a differential-to-single-ended RF amplifier in a transmit signal chain design
- ON Semiconductor CEO Appears at Munich Electronica Show and Launches Treo Platform
- ON Semiconductor Launches Industry-Leading Analog and Mixed-Signal Platform
- Analog Devices ADAQ7767-1 μModule DAQ Solution for Rapid Development of Precision Data Acquisition Systems Now Available at Mouser
- Domestic high-precision, high-speed ADC chips are on the rise
- Microcontrollers that combine Hi-Fi, intelligence and USB multi-channel features – ushering in a new era of digital audio
- Using capacitive PGA, Naxin Micro launches high-precision multi-channel 24/16-bit Δ-Σ ADC
- Fully Differential Amplifier Provides High Voltage, Low Noise Signals for Precision Data Acquisition Signal Chain
- Innolux's intelligent steer-by-wire solution makes cars smarter and safer
- 8051 MCU - Parity Check
- How to efficiently balance the sensitivity of tactile sensing interfaces
- What should I do if the servo motor shakes? What causes the servo motor to shake quickly?
- 【Brushless Motor】Analysis of three-phase BLDC motor and sharing of two popular development boards
- Midea Industrial Technology's subsidiaries Clou Electronics and Hekang New Energy jointly appeared at the Munich Battery Energy Storage Exhibition and Solar Energy Exhibition
- Guoxin Sichen | Application of ferroelectric memory PB85RS2MC in power battery management, with a capacity of 2M
- Analysis of common faults of frequency converter
- In a head-on competition with Qualcomm, what kind of cockpit products has Intel come up with?
- Dalian Rongke's all-vanadium liquid flow battery energy storage equipment industrialization project has entered the sprint stage before production
- Allegro MicroSystems Introduces Advanced Magnetic and Inductive Position Sensing Solutions at Electronica 2024
- Car key in the left hand, liveness detection radar in the right hand, UWB is imperative for cars!
- After a decade of rapid development, domestic CIS has entered the market
- Aegis Dagger Battery + Thor EM-i Super Hybrid, Geely New Energy has thrown out two "king bombs"
- A brief discussion on functional safety - fault, error, and failure
- In the smart car 2.0 cycle, these core industry chains are facing major opportunities!
- The United States and Japan are developing new batteries. CATL faces challenges? How should China's new energy battery industry respond?
- Murata launches high-precision 6-axis inertial sensor for automobiles
- Ford patents pre-charge alarm to help save costs and respond to emergencies
- New real-time microcontroller system from Texas Instruments enables smarter processing in automotive and industrial applications
- Oscilloscope automobile turbocharger solenoid valve waveform and analysis
- Transformer voltage calculation
- Failure to send data in broadcast mode
- EEWORLD University - IGBT module technology, drive and application
- Mbed online compiler to be retired soon
- New China Mobile Onenet NB Development Board
- PicoPlanet – Development board with capacitive touch
- Looking for the distributor of Sonix SN8P2501DSG chip
- 【Qinheng CH582】2, Compilation environment + the first LED program
- AD 20.2.5.213