How to use an oscilloscope
1 Oscilloscope Use
This section introduces how to use an oscilloscope. There are many types and models of oscilloscopes with different functions. The 20MHz or 40MHz dual-trace oscilloscopes are more commonly used in digital circuit experiments. The usage of these oscilloscopes is similar. This section does not target a specific model of oscilloscope, but only conceptually introduces the common functions of oscilloscopes in digital circuit experiments.
1.1 Fluorescent screen
The fluorescent screen is the display part of the oscilloscope. There are multiple scale lines in the horizontal and vertical directions on the screen, indicating the relationship between the voltage and time of the signal waveform. The horizontal direction indicates time, and the vertical direction indicates voltage. The horizontal direction is divided into 10 grids, the vertical direction is divided into 8 grids, and each grid is divided into 5 parts. The vertical direction is marked with 0%, 10%, 90%, 100% and other signs, and the horizontal direction is marked with 10%, 90% signs, which are used to measure parameters such as DC level, AC signal amplitude, and delay time. The voltage value and time value can be obtained by multiplying the number of grids occupied by the measured signal on the screen by the appropriate proportional constant (V/DIV, TIME/DIV).
1.2 Oscilloscope tube and power supply system
1. Power (Power)
Oscilloscope main power switch. When this switch is pressed, the power indicator light is on, indicating that the power is on.
2. Brightness (Intensity)
Rotating this knob can change the brightness of the light spot and the scan line. It can be smaller when observing low-frequency signals and larger when observing high-frequency signals.
Generally, it should not be too bright to protect the fluorescent screen.
3. Focus (Focus)
The focus knob adjusts the size of the electron beam cross-section to focus the scan line to the clearest state.
4. Scale brightness (Illuminance)
This knob adjusts the brightness of the illuminance behind the fluorescent screen. Under normal indoor light, the illuminance is better. In an environment with insufficient indoor light, the illuminance can be appropriately brightened.
1.3 Vertical deflection factor and horizontal deflection factor
1. Vertical deflection factor selection (VOLTS/DIV) and fine adjustment
The distance that the light spot deflects on the screen under the action of a unit input signal is called the offset sensitivity. This definition applies to both the X-axis and the Y-axis. The reciprocal of the sensitivity is called the deflection factor. The unit of vertical sensitivity is cm/V, cm/mV or DIV/mV, DIV/V, and the unit of vertical deflection factor is V/cm, mV/cm or V/DIV, mV/DIV. In fact, due to customary usage and the convenience of measuring voltage readings, the deflection factor is sometimes regarded as sensitivity.
Each channel in the tracer oscilloscope has a vertical deflection factor selection band switch. Generally, it is divided into 10 levels from 5mV/DIV to 5V/DIV in the form of 1, 2, 5. The value indicated by the band switch represents the voltage value of one grid in the vertical direction on the fluorescent screen. For example, when the band switch is set to 1V/DIV, if the signal light spot on the screen moves one grid, it means that the input signal voltage changes by 1V.
There is often a small knob on each band switch to fine-tune the vertical deflection factor of each level. Turn it clockwise to the bottom, which is in the "calibration" position. At this time, the vertical deflection factor value is consistent with the value indicated by the band switch. Rotate this knob counterclockwise to fine-tune the vertical deflection factor. After the vertical deflection factor is fine-tuned, it will cause inconsistency with the indicated value of the band switch, which should be paid attention to. Many oscilloscopes have a vertical expansion function. When the fine-tuning knob is pulled out, the vertical sensitivity is expanded several times (the deflection factor is reduced several times). For example, if the deflection factor indicated by the band switch is 1V/DIV, when the ×5 expansion state is adopted, the vertical deflection factor is 0.2V/DIV.
When doing digital circuit experiments, the ratio of the vertical movement distance of the measured signal on the screen to the vertical movement distance of the +5V signal is often used to judge the voltage value of the measured signal.
2. Time base selection (TIME/DIV) and fine-tuning
The use of time base selection and fine-tuning is similar to that of vertical deflection factor selection and fine-tuning. Time base selection is also realized through a band switch, and the time base is divided into several gears according to 1, 2, and 5. The indicated value of the band switch represents the time value of the light spot moving one grid in the horizontal direction. For example, in the 1μS/DIV gear, the light spot moving one grid on the screen represents the time value of 1μS.
The "fine adjustment" knob is used for time base calibration and fine adjustment. When it is turned clockwise to the calibration position, the time base value displayed on the screen is consistent with the nominal value shown on the band switch. Turn the knob counterclockwise to fine-tune the time base. When the knob is pulled out, it is in the scanning expansion state. Usually it is ×10 expansion, that is, the horizontal sensitivity is expanded by 10 times and the time base is reduced to 1/10. For example, in the 2μS/DIV gear, the time value represented by one horizontal grid on the fluorescent screen in the scanning expansion state is equal to 2μS×(1/10)=0.2μS.
There are 10MHz, 1MHz, 500kHz, and 100kHz clock signals on the TDS laboratory bench, which are generated by a quartz crystal oscillator and a frequency divider. They are very accurate and can be used to calibrate the time base of the oscilloscope.
The standard signal source CAL of the oscilloscope is specially used to calibrate the time base and vertical deflection factor of the oscilloscope. For example, the standard signal source of the COS5041 oscilloscope provides a square wave signal with VP-P=2V, f=1kHz.
The Position knob on the front panel of the oscilloscope adjusts the position of the signal waveform on the screen. Rotate the horizontal position knob (marked with a horizontal double-sided arrow) to move the signal waveform left and right, and rotate the vertical position knob (marked with a vertical double-sided arrow) to move the signal waveform up and down.
1.4 Input channel and input coupling selection
1. Input channel selection
There are at least three input channel selection modes: channel 1 (CH1), channel 2 (CH2), and dual channel (DUAL). When channel 1 is selected, the oscilloscope only displays the signal of channel 1. When channel 2 is selected, the oscilloscope only displays the signal of channel 2. When dual channel is selected, the oscilloscope displays the channel 1 signal and the channel 2 signal at the same time. When testing the signal, first connect the ground of the oscilloscope to the ground of the circuit under test. According to the selection of the input channel, plug the oscilloscope probe into the corresponding channel socket, connect the ground on the oscilloscope probe to the ground of the circuit under test, and the oscilloscope probe contacts the measured point. There is a two-position switch on the oscilloscope probe. When this switch is turned to the "×1" position, the measured signal is sent to the ground without attenuation.
Oscilloscope, the voltage value read from the screen is the actual voltage value of the signal. When this switch is turned to the "×10" position, the measured signal is attenuated to 1/10, and then sent to the oscilloscope. The voltage value read from the screen multiplied by 10 is the actual voltage value of the signal.
2. Input coupling mode
There are three options for input coupling mode: AC, GND, and DC. When "GND" is selected, the scan line shows the position of the "oscilloscope ground" on the screen. DC coupling is used to measure the DC absolute value of the signal and observe extremely low frequency signals. AC coupling is used to observe AC and AC signals containing DC components. In digital circuit experiments, the "DC" mode is generally selected to observe the absolute voltage value of the signal.
2.5 Triggering
The first section pointed out that after the measured signal is input from the Y axis, a part of it is sent to the Y axis deflection plate of the oscilloscope, driving the light spot to move in the vertical direction on the fluorescent screen in proportion; the other part is diverted to the x axis deflection system to generate a trigger pulse, trigger the scanning generator, generate a repeated sawtooth wave voltage and add it to the x deflection plate of the oscilloscope, so that the light spot moves in the horizontal direction. The two are combined, and the figure drawn by the light spot on the fluorescent screen is the measured signal figure. It can be seen that the correct triggering method directly affects the effective operation of the oscilloscope. In order to obtain a stable and clear signal waveform on the fluorescent screen, it is very important to master the basic triggering function and its operation method.
1. Trigger source (Source) selection
In order to display a stable waveform on the screen, the measured signal itself or a trigger signal with a certain time relationship with the measured signal needs to be added to the trigger circuit. The trigger source selection determines where the trigger signal is supplied. There are usually three trigger sources: internal trigger (INT), power trigger (LINE), and external trigger EXT).
Internal trigger uses the measured signal as the trigger signal, which is a commonly used triggering method. Since the trigger signal itself is part of the measured signal, a very stable waveform can be displayed on the screen. In a dual-trace oscilloscope, either channel 1 or channel 2 can be selected as the trigger signal.
Power triggering uses the AC power frequency signal as the trigger signal. This method is effective when measuring signals related to the AC power frequency. It is especially effective when measuring low-level AC noise of audio circuits and thyristors.
External triggering uses an external signal as the trigger signal, which is input from the external trigger input terminal. There should be a periodic relationship between the external trigger signal and the measured signal. Since the measured signal is not used as a trigger signal, when to start scanning has nothing to do with the measured signal.
Correctly selecting the trigger signal has a great relationship with the stability and clarity of the waveform display. For example, in the measurement of digital circuits, for a simple periodic signal, it may be better to choose an internal trigger, while for a signal with a complex period and a signal with a periodic relationship with it, it may be better to choose an external trigger.
2. Trigger coupling (Coupling) mode selection
There are many ways to couple the trigger signal to the trigger circuit, the purpose is to make the trigger signal stable and reliable. Here are several commonly used ones.
AC coupling is also called capacitive coupling. It only allows triggering with the AC component of the trigger signal, and the DC component of the trigger signal is blocked. This coupling method is usually used when the DC component is not considered to form a stable trigger. However, if the frequency of the trigger signal is less than 10Hz, it will cause difficulty in triggering.
DC coupling (DC) does not block the DC component of the trigger signal. When the frequency of the trigger signal is low or the duty cycle of the trigger signal is large, it is better to use DC coupling.
When the low frequency suppression (LFR) triggers, the trigger signal is added to the trigger circuit through a high-pass filter, and the low frequency component of the trigger signal is suppressed; when the high frequency suppression (HFR) triggers, the trigger signal is added to the trigger circuit through a low-pass filter, and the high frequency component of the trigger signal is suppressed. In addition, there is a TV synchronization (TV) trigger for TV maintenance. These trigger coupling methods have their own scope of application, which needs to be experienced in use.
3. Trigger level (Level) and trigger polarity (Slope)
Trigger level adjustment is also called synchronization adjustment, which synchronizes the scan with the measured signal. The level adjustment knob adjusts the trigger level of the trigger signal. Once the trigger signal exceeds the trigger level set by the knob, the scan is triggered. Turn the knob clockwise to increase the trigger level; turn the knob counterclockwise to decrease the trigger level. When the level knob is adjusted to the level lock position, the trigger level is automatically kept within the amplitude of the trigger signal, and a stable trigger can be generated without level adjustment. When the signal waveform is complex and the level knob cannot be used to stably trigger, use the Hold Off knob to adjust the waveform holdoff time (scan pause time) to synchronize the scan with the waveform.
The polarity switch is used to select the polarity of the trigger signal. When the dial is in the "+" position, a trigger is generated when the trigger signal exceeds the trigger level in the direction of signal increase. When the dial is in the "-" position, a trigger is generated when the trigger signal exceeds the trigger level in the direction of signal decrease. The trigger polarity and trigger level jointly determine the trigger point of the trigger signal.
2.6 Sweep Mode
Sweep has three sweep modes: Auto, Norm, and Single.
Auto: When there is no trigger signal input or the trigger signal frequency is lower than 50Hz, the scan is self-excited.
Normal state: When there is no trigger signal input, the scan is in the ready state and there is no scan line. After the trigger signal arrives, the scan is triggered.
Single: The single button is similar to a reset switch. In the single scan mode, the scan circuit is reset when the single button is pressed, and the Ready light is on. A scan is generated after the trigger signal arrives. After the single scan is completed, the Ready light goes out. Single scan is used to observe non-periodic signals or single transient signals, and it is often necessary to take a picture of the waveform. The
above briefly introduces the basic functions and operations of the oscilloscope. The oscilloscope also has some more complex functions, such as delayed scan, trigger delay, XY working mode, etc., which are not introduced here. It is easy to get started with the oscilloscope, but to be truly proficient, you must master it in application. It is worth pointing out that although the oscilloscope has many functions, it is better to use other instruments and meters in many cases. For example, in a digital circuit experiment, it is much simpler to use a logic pen to determine whether a single pulse with a narrow pulse width occurs; when measuring the pulse width of a single pulse, it is better to use a logic analyzer.
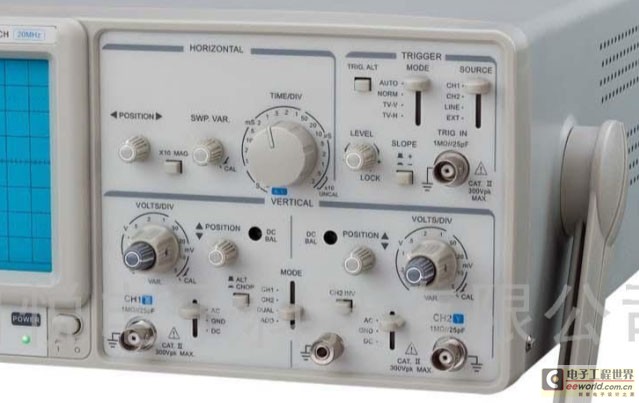
1. Panel Introduction
1. Brightness and Focus Knob
The brightness adjustment knob is used to adjust the brightness of the light trace (some oscilloscopes call it "brightness"). The brightness should be appropriate when used. If it is too bright, it is easy to damage the oscilloscope tube. The focus adjustment knob is used to adjust the focus (coarseness) of the light trace. It is best to use it when the image is clear.
2. Signal Input Channel
Common oscilloscopes are mostly dual-trace oscilloscopes, with two input channels, namely channel 1 (CH1) and channel 2 (CH2). They can be connected to the oscilloscope probes respectively, and then the oscilloscope housing is grounded, and the probes are inserted into the part to be measured for measurement.
3. Channel selection key (vertical selection)
Common oscilloscopes have five channel selection keys:
(1) CH1: Channel 1 is displayed alone;
(2) CH2: Channel 2 is displayed alone;
(3) ALT: Two channels are displayed alternately;
(4) CHOP: Two channels are displayed intermittently, used for dual-trace display when the scanning speed is slow;
(5) ADD: Signal superposition of two channels. In maintenance, channel 1 or channel 2 is often selected.
4. Vertical sensitivity adjustment knob
To adjust the vertical deflection sensitivity, the knob position should be adjusted according to the amplitude of the input signal. The value indicated by the knob (such as 0.5V/div, indicating that the amplitude of each grid in the vertical direction is 0.5V) is multiplied by the number of grids occupied by the measured signal in the vertical direction of the screen to obtain the amplitude of the measured signal.
5. Vertical movement adjustment knob
Used to adjust the position of the measured signal light trace in the vertical direction of the screen.
6. Horizontal scan adjustment knob
To adjust the horizontal speed, the knob position should be adjusted according to the frequency of the input signal. The knob value (such as 0.5ms/div, indicating that the time per grid in the horizontal direction is 0.5ms) is multiplied by the number of grids occupied by the measured signal in one cycle to obtain the period of the signal, which can also be converted into frequency.
7. Horizontal position adjustment knob
Used to adjust the position of the measured signal light trace in the horizontal direction of the screen.
8. Trigger mode selection
Oscilloscopes usually have four trigger modes:
(1) Normal (NORM): When there is no signal, there is no display on the screen; when there is a signal, it cooperates with the level control to display a stable waveform;
(2) Automatic (AUTO): When there is no signal, a light trace is displayed on the screen; when there is a signal, it cooperates with the level control to display a stable waveform;
(3) TV field (TV): used to display TV field signals;
(4) Peak automatic (PP AUTO): When there is no signal, a light trace is displayed on the screen; when there is a signal, a stable waveform display can be obtained without adjusting the level. This mode is only used in some oscilloscopes (such as CALTEK CA8000 series oscilloscopes).
9. Trigger source selection
Oscilloscope trigger sources include internal trigger sources and external trigger sources. If an external trigger source is selected, the trigger signal should be input from the external trigger source input terminal. This method is rarely used in home appliance maintenance. If you select the internal trigger source, generally select channel 1 (CH1) or channel 2 (CH2). It should be selected according to the input signal channel. If the input signal channel is selected as channel 1, the internal trigger source should also select channel 1.
II. Measurement method
1. Amplitude and frequency measurement method (taking the calibration signal of the oscilloscope as an example)
(1) Insert the oscilloscope probe into the channel 1 jack and set the attenuation on the probe to "1";
(2) Set the channel selector to CH1 and the coupling mode to DC;
(3) Insert the probe tip into the small hole of the calibration signal source. At this time, a light trace appears on the oscilloscope screen;
(4) Adjust the vertical knob and horizontal knob to stabilize the waveform displayed on the screen, and set the vertical fine-tuning and horizontal fine-tuning to the calibration position;
(5) Read the number of grids occupied by the waveform in the vertical direction, multiply it by the indicated value of the vertical attenuation knob, and get the amplitude of the calibration signal;
(6) Read the number of grids occupied by each cycle of the waveform in the horizontal direction, multiply it by the indicated value of the horizontal scan knob, and get the period of the calibration signal (the inverse of the period is the frequency);
(7) The frequency of the general calibration signal is 1kHz and the amplitude is 0.5V, which is used to calibrate the internal scanning oscillator frequency of the oscilloscope. If it is abnormal, adjust the corresponding potentiometer of the oscilloscope (internal) until it matches.
2. Oscilloscope application example (taking the measurement of 13MHz clock pulse of 788 mobile phone as an example)
The normal 13MHz clock signal in the mobile phone is a necessary condition for turning on the phone, so the 13MHz clock signal should be measured frequently during maintenance. The steps are as follows:
(1) Turn on the oscilloscope and adjust the brightness and focus knobs so that a horizontal bright line with moderate brightness and good focus is displayed on the screen;
(2) Calibrate the oscilloscope according to the above method, and then set the coupling mode to AC;
(3) Clamp the grounding clip of the oscilloscope probe to the grounding point of the mobile phone circuit board, and insert the probe into the 788 mobile phone CPU pin;
(4) Turn on the mobile phone power, press the power button, adjust the vertical scan level and the horizontal scan knob, and observe whether a stable waveform appears on the screen. If not, it generally means that there is no 13MHz signal.
Previous article:Use of spectrum analyzer
Next article:Resistance measurement circuit Conductivity measurement circuit
Recommended ReadingLatest update time:2024-11-16 20:53
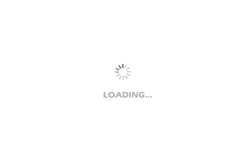
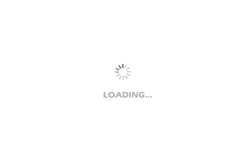
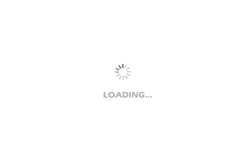
- Popular Resources
- Popular amplifiers
-
Virtualization Technology Practice Guide - High-efficiency and low-cost solutions for small and medium-sized enterprises (Wang Chunhai)
-
Principles and Applications of Single Chip Microcomputers 3rd Edition (Zhang Yigang)
-
【Follow me Season 2 Episode 2】Program source code user bigjiong
-
A review of deep learning applications in traffic safety analysis
- High signal-to-noise ratio MEMS microphone drives artificial intelligence interaction
- Advantages of using a differential-to-single-ended RF amplifier in a transmit signal chain design
- ON Semiconductor CEO Appears at Munich Electronica Show and Launches Treo Platform
- ON Semiconductor Launches Industry-Leading Analog and Mixed-Signal Platform
- Analog Devices ADAQ7767-1 μModule DAQ Solution for Rapid Development of Precision Data Acquisition Systems Now Available at Mouser
- Domestic high-precision, high-speed ADC chips are on the rise
- Microcontrollers that combine Hi-Fi, intelligence and USB multi-channel features – ushering in a new era of digital audio
- Using capacitive PGA, Naxin Micro launches high-precision multi-channel 24/16-bit Δ-Σ ADC
- Fully Differential Amplifier Provides High Voltage, Low Noise Signals for Precision Data Acquisition Signal Chain
- Innolux's intelligent steer-by-wire solution makes cars smarter and safer
- 8051 MCU - Parity Check
- How to efficiently balance the sensitivity of tactile sensing interfaces
- What should I do if the servo motor shakes? What causes the servo motor to shake quickly?
- 【Brushless Motor】Analysis of three-phase BLDC motor and sharing of two popular development boards
- Midea Industrial Technology's subsidiaries Clou Electronics and Hekang New Energy jointly appeared at the Munich Battery Energy Storage Exhibition and Solar Energy Exhibition
- Guoxin Sichen | Application of ferroelectric memory PB85RS2MC in power battery management, with a capacity of 2M
- Analysis of common faults of frequency converter
- In a head-on competition with Qualcomm, what kind of cockpit products has Intel come up with?
- Dalian Rongke's all-vanadium liquid flow battery energy storage equipment industrialization project has entered the sprint stage before production
- Allegro MicroSystems Introduces Advanced Magnetic and Inductive Position Sensing Solutions at Electronica 2024
- Car key in the left hand, liveness detection radar in the right hand, UWB is imperative for cars!
- After a decade of rapid development, domestic CIS has entered the market
- Aegis Dagger Battery + Thor EM-i Super Hybrid, Geely New Energy has thrown out two "king bombs"
- A brief discussion on functional safety - fault, error, and failure
- In the smart car 2.0 cycle, these core industry chains are facing major opportunities!
- The United States and Japan are developing new batteries. CATL faces challenges? How should China's new energy battery industry respond?
- Murata launches high-precision 6-axis inertial sensor for automobiles
- Ford patents pre-charge alarm to help save costs and respond to emergencies
- New real-time microcontroller system from Texas Instruments enables smarter processing in automotive and industrial applications
- Which formaldehyde sensor is good? Which model? If you have used it, please share and discuss.
- X-NUCLEO-IKS01A3 sensor test based on STM32F401RE development board 4 LIS2MDL magnetometer test
- Issues that need attention when initializing SPI of TI C2000 series 280049 chip
- Oh my god! As an electronic engineer, you are still using Baidu to search for information?
- TMS570 battery balance management system solution
- Celebrating Programmers Day
- Battery level detection for low power devices
- CAN IAP Example
- Millimeter wave is the technology closest to our lives
- 【MM32 eMiniBoard Review】1. Notes after setting up the development environment