Solution for multiple re-trigger storage test system using CPLD
Overview: A design scheme of a multiple retrigger storage test system based on CPLD is proposed, and the system hardware design and CPLD internal control principle are introduced in detail, and the CPLD control circuit is simulated. The system is small in size and low in power consumption. It can record multiple retrigger signals in real time. Each signal record has a negative delay. When reading out the data, the recorded waveform can be accurately reproduced without program adjustment. Therefore, the application of retrigger technology in storage test systems is of great significance.
1 Introduction
Multiple re-triggering technology is used in many occasions. For example, if a gear with 30 teeth has a gear meshing coefficient of 1.2, and the stress of one tooth is measured when it is meshed multiple times, the meshing time of one tooth only accounts for 1.2/30 of the time of the gear turning one circle, and the remaining 28.8/30 of the time is idle, and the idle state record is meaningless. For this reason, multiple re-triggering technology is developed, which uses tooth stress as the internal trigger signal, only records the useful signal after each trigger, and has a negative delay, but does not record the idle state. Until the storage space of the recording device is filled, the storage space can be effectively used to record more useful signals.
2 Overall design of multiple re-trigger storage test system
2.1 Working principle
of multiple re-trigger storage test system Figure 1 is a block diagram of the principle of multiple re-trigger storage test system. Its working principle is: after the measured signal is converted into an electrical signal by the sensor, it is input into the analog conditioning circuit, and then input into the A/D converter after amplification and filtering, the analog signal is converted into a digital signal, and then transmitted to the memory through the FIFO, and the computer reads the data through the communication interface. Among them, the conversion and read clock of the A/D converter of the storage test system, the read and write clock of the FIFO and memory, and the push address clock are all controlled and generated by the CPLD.
2.2 Implementation of negative delay
Dynamic information storage requires the real and effective recording of useful signals. According to the characteristics of the measured signal, it is necessary to record the data of the signal in a very short time before the trigger, which requires the use of negative delay technology. Negative delay is also called advance transmission, that is, the trigger acquisition time of the trigger signal is advanced for a period of time as the starting point of the transmission data. The system design uses FIFO memory to achieve negative delay. When the trigger signal does not arrive, the data output by the A/D converter is continuously written into the FIFO memory, and the data converted by the A/D converter continuously refreshes the content of the FIFO memory. Once the trigger signal arrives, the data begins to be written from the FIFO to the memory.
2.3 Selection of main components
The AD7492 A/D converter is used in this system design. This device is a 12-bit high-speed, low-power, successive approximation A/D converter. At 5 V voltage and 1 MS/s rate, its average current is only 1.72 mA and the power consumption is 8.6 mW; at 5 V voltage and 500 kS/s data transmission rate, the current consumption is 1.24 mA, so the device can meet the low power consumption requirements of the system. Since the total capacity of the memory designed in this system is 512 KB, a N08T163 memory with a capacity of 512 KB is selected. And the self-made FIFO memory is realized through the timing of the static memory, and the power consumption is about 1/10 of the same type of FIFO memory. The negative delay record of the system design is 1 KB, and the N02L163WC2A memory with a capacity of 128 KB is selected. In view of the low power consumption, small size and complex control logic of the storage test system, the EPM7128BTCl44-4 CPLD of the MAX7000B series is used as the controller. This device is a high-performance, low-power CMOS CPLD with 2500 available logic gate circuits, a pin-to-pin transmission delay of 4.0 ns, and a system operating frequency of up to 243.9 MHz.
3 Design of CPLD control circuit
The CPLD-based multiple re-trigger storage test system is mainly composed of A/D converter, memory, FIFO and controller CPLD, among which the CPLD control circuit is composed of clock, multiple re-trigger, FIFO address generation, memory address generation, memory full count, power management and computer communication modules, as shown in Figure 2.
3.1 Functions of each module of the control circuit
(1) Power management module This module mainly controls the power consumption of the system. When the system is in sleep mode, only Vcc supplies power to the CPLD; when the system enters normal working state, Vcc, VDD and VEE supply power at the same time, and the crystal oscillator works. When the sampling is completed, the system turns off VEE, the analog part enters sleep mode, and the crystal oscillator stops working. This module can meet the low power consumption requirements of the system.
(2) Clock module The 4 MHz signal provided by the crystal oscillator passes through 4 dividers to obtain clock signals of 2 MHz, 1 MHz, 500 kHz and 250 kHz respectively. These signals are combined to obtain the sampling signal convst of the A/D converter, the write signal of the FIFO, the read signal ffwr_adread of the A/D converter, and the push address signal ff_dz of the FIFO, all of which are 250 kHz.
(3) Multiple re-trigger module When the external multiple re-trigger signal m_tri arrives. The open signal generated by the D flip-flop becomes a high level, and the counter starts counting the clock signal ff_dz. It stops counting after counting every 8 KB, and generates a clear signal clr to clear the open signal, waiting for the next trigger signal. The clock signal clkl generated by the clock signal ff_dz and the open signal is used as the push address signal and write signal when writing to the memory. The open signal is inverted and connected to the memory enable terminal.
(4) The FIFO address generation module CPLD controls the address of the FIFO by the clock module ff_dz signal, and starts pushing the FIFO address at the falling edge of the clock signal ff_dz.
(5) The memory address generation module repeatedly re-triggering the module generates the clkl signal as the memory push address signal m_dz push address, writes the converted data to the memory, stops writing after writing 8 KB, and waits for the next trigger signal. The memory is full of 512. KB. Stop pushing the address and writing operations, waiting for the computer to read. When reading, every time the computer sends a reading pulse to the CPLD, the address signal advances 1 bit, and the CPLD reads 1 data from the corresponding address unit in the memory.
(6) When the memory full module receives multiple re-trigger signals m_tri, the open signal becomes high level, and becomes low level after counting 8 KB, waiting for the next trigger signal. Therefore, a counter is used to count the falling edges of the open signal. After counting 64, the memory full signal tc becomes high level.
3.2 Simulation and analysis of CPLD overall control circuit
Figure 3 is a simulation diagram of the CPLD overall control circuit. In Figure 3, the trigger signal m_tri is generated 3 times. The nopen signal shows that the memory is gated 3 times. The change of the memory address signal m_addr shows that the memory records 8 KB for each trigger signal and continuously updates the FIFO data. After the first trigger signal m_tri arrives, the nopen signal becomes low level, which means the memory is gated. At this time, the push address signal and write signal m_dz signal of the memory are generated, and the push address is given to the memory at the falling edge. The memory performs a write operation during the low level period. After the trigger signal m_tri arrives, it is counted to 8 KB, the nopen signal generates a high level to not gate the memory, and the push address signal and write signal m_dz of the memory become high level.
4 Experimental verification
The function of the test system was verified through experiments. In the experiment, the test system was loaded with 8 trigger signals and collected 8 times continuously. Since the system is designed to sample up to 64 times, if the number of re-trigger signals does not reach 64 times, a forced reading signal must be manually given to the tester to end the instrument sampling. After the multiple re-trigger signals are valid for 8 times, the manual forced reading signal causes the instrument to end sampling, and the host computer software determines whether the collected waveform amplitude corresponds to the manually adjusted amplitude. If they correspond, it indicates that the system sampling is normal.
Experimental steps: The tester is powered on, and the red light of the tester sampling status indicator is on. Connect the programming reading line to the computer, open the programming interface, set the sampling frequency of multiple re-triggering, and use the default settings for other options. After programming is completed, unplug the programming reading line, power on the tester (ON=0), and the red light starts to flash. Connect the output of the charge calibrator to the channel end on the tester panel, set the output waveform of the charge calibrator to a sine wave, and the charge amount is 2 000 PC. Output signal, give the system a trigger signal (M_TRI=1), the red light flashes for a period of time and then stops flashing, indicating that the first sampling of the system is completed. At this time, adjust the output charge of the charge calibrator to 4 000 PC. Give the system another trigger signal, repeat the previous process, change the charge amount after each sampling is completed, until the green light is on, connect the programming reading line to the computer, read the data through the host computer software, and after the data is read, the tester is powered off (OFF=0), and the power of the tester is disconnected. Figure 4 shows the waveform of multiple re-triggering. The measured charge values obtained by converting and processing the data in FIG4 are shown in Table 1. As can be seen from Table 1, the collected waveform amplitudes are consistent with the adjustment order, and the system design meets the requirements.
5 Conclusion
The CPLD-based multiple re-trigger storage test system designed in this paper has stable performance and high measurement accuracy. It can work normally in harsh environments such as high shock, and meets the system's low power consumption and miniaturization requirements, and realizes undistorted sampling and storage of signals. This system can record multiple re-trigger signals in real time, and each signal recording has a negative delay. When reading data, the recorded waveform can be accurately reproduced without program adjustment. Therefore, storage test technology has broad prospects in the measurement of multiple transient signals.
Previous article:Signal Integrity Analysis Basics Series: Eye Diagram Measurement (Part 1)
Next article:TDR Principle
Recommended ReadingLatest update time:2024-11-16 21:21
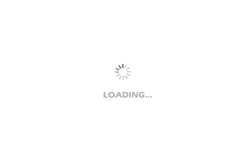
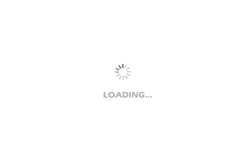
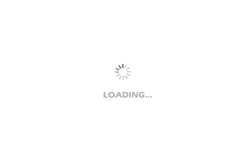
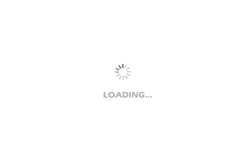
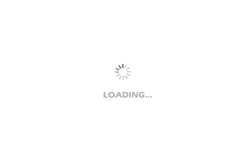
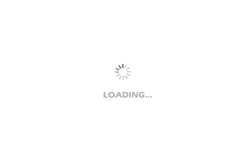
- Popular Resources
- Popular amplifiers
-
Learn CPLD and Verilog HDL programming technology from scratch_Let beginners easily learn CPLD system design technology through practical methods
-
Practical Electronic Components and Circuit Basics (4th Edition)_Explanation of basic circuit principles, introduction to electronic components, design of various circuits and practical circuit analysis
-
Real-time driver monitoring system via modal and viewpoint analysis
-
A Practical Tutorial on ASIC Design (Compiled by Yu Xiqing)
- High signal-to-noise ratio MEMS microphone drives artificial intelligence interaction
- Advantages of using a differential-to-single-ended RF amplifier in a transmit signal chain design
- ON Semiconductor CEO Appears at Munich Electronica Show and Launches Treo Platform
- ON Semiconductor Launches Industry-Leading Analog and Mixed-Signal Platform
- Analog Devices ADAQ7767-1 μModule DAQ Solution for Rapid Development of Precision Data Acquisition Systems Now Available at Mouser
- Domestic high-precision, high-speed ADC chips are on the rise
- Microcontrollers that combine Hi-Fi, intelligence and USB multi-channel features – ushering in a new era of digital audio
- Using capacitive PGA, Naxin Micro launches high-precision multi-channel 24/16-bit Δ-Σ ADC
- Fully Differential Amplifier Provides High Voltage, Low Noise Signals for Precision Data Acquisition Signal Chain
- Innolux's intelligent steer-by-wire solution makes cars smarter and safer
- 8051 MCU - Parity Check
- How to efficiently balance the sensitivity of tactile sensing interfaces
- What should I do if the servo motor shakes? What causes the servo motor to shake quickly?
- 【Brushless Motor】Analysis of three-phase BLDC motor and sharing of two popular development boards
- Midea Industrial Technology's subsidiaries Clou Electronics and Hekang New Energy jointly appeared at the Munich Battery Energy Storage Exhibition and Solar Energy Exhibition
- Guoxin Sichen | Application of ferroelectric memory PB85RS2MC in power battery management, with a capacity of 2M
- Analysis of common faults of frequency converter
- In a head-on competition with Qualcomm, what kind of cockpit products has Intel come up with?
- Dalian Rongke's all-vanadium liquid flow battery energy storage equipment industrialization project has entered the sprint stage before production
- Allegro MicroSystems Introduces Advanced Magnetic and Inductive Position Sensing Solutions at Electronica 2024
- Car key in the left hand, liveness detection radar in the right hand, UWB is imperative for cars!
- After a decade of rapid development, domestic CIS has entered the market
- Aegis Dagger Battery + Thor EM-i Super Hybrid, Geely New Energy has thrown out two "king bombs"
- A brief discussion on functional safety - fault, error, and failure
- In the smart car 2.0 cycle, these core industry chains are facing major opportunities!
- The United States and Japan are developing new batteries. CATL faces challenges? How should China's new energy battery industry respond?
- Murata launches high-precision 6-axis inertial sensor for automobiles
- Ford patents pre-charge alarm to help save costs and respond to emergencies
- New real-time microcontroller system from Texas Instruments enables smarter processing in automotive and industrial applications
- ATmega4809 Curiosity Nano Review: Development Software
- Download ARM Cortex-m3 assembly instruction summary table
- What flash space can RSL10 customers use?
- stm32f429i_eval_development schematic
- Fast Fourier Transform of Convolution and Correlation of Discrete Sequences
- Which textbook on switching power supplies is better?
- How to understand the entire LCD scanning cycle?
- ADC Sequencer Working Mode of DSP2812
- Challenge FreeRTOS learning + stm32 to implement shell tasks
- China Chip Recruitment. Listed on Shanghai Science and Technology Innovation Board, focusing on the research and development of IoT wireless communication chips and solutions. Salary open + stock