The timing counting function of the 89C51 microcontroller is controlled by the special function registers TMOD and TCON.
TMOD has no bit address and cannot perform bit operations. The names and functions of each bit are as follows:
TMOD: GATE C/T1 M1 M0 GATE C/T1 M1 M0
D7 D6 D5 D4 D3 D2 D1 D0
GATE C/T1 M1 M0 controls timing timer 1;
GATE C/T0 M1 M0 controls timing timer 0;
When GATE=0, the timing counting signal is the state of the T0 pin (P3.4) or the machine cycle (C/T=0 counts the machine cycle, i.e. timing, C/T=1 counts the state of the T0 pin, i.e. counting), and the counting start switch is TR0 (0 turns off counting, 1 starts counting).
When GATE=1, the timing counting function is determined by the T0 pin (P3.4) or the machine cycle (C/T=0 counts the machine cycle, i.e. timing, C/T=1 counts the change state of the T0 pin, i.e. counting), and the counting start switch is determined by TR0 (0 turns off counting, 1 starts counting) and INT0 (pin P3.2).
M1M0 is the counting mode selection: counting is performed in TH0 and TL0.
00 is mode 0, 13-bit (8 bits of TH0 and the lower 5 bits of TL0) binary counter, which can count from 0 to 2 to the 13th power -1;
01 is mode 1, 16-bit binary counter, which can count from 0 to 2 to the 16th power -1;
10 is mode 2, 8-bit binary counter, TH0 puts the initial value of the count, counting is performed in TL0, and
the initial value in TH0 is automatically loaded into TL0 after overflow;
11 is mode 3, TH0 is an 8-bit counter, and HL0 is an 8-bit counter. The two counters are independent of each other.
T1 and T0 have the same functions.
Special function register TCON can be operated by bit, but generally does not use bit address, but uses bit function name:
Bit address: 8FH 8EH 8DH 8Ch 8Bh 8Ah 89H 88H
TCON: TF1 TR1 TF0 TR0 IE1 IT1 IE0 IT0
D7 D6 D5 D4 D3 D2 D1 D0
TF0 is T0 count flag: When the timing count overflows, this bit is automatically set to 1, and automatically cleared to 0 after the interrupt count ends.
TR0 is the count switch, when GATE=0, TR0=1 turns on the count, and 0 turns it off. When GATE=1, it controls the counter to open together with INT0, that is, GATE=1, TR0=1, INT0=1 can turn on the count, otherwise it is turned off.
In timing/counting, the value of TH0 TL0 is incremented by 1 and counts to FFFFH. If it is in timing/counting mode, TF0 is set to 1 after overflow and the counting time ends. If it is in interrupt mode, the interrupt request is set to 1 by hardware. After the counting ends, that is, after the interrupt ends, TF0 is automatically cleared to 0.
/***************Timer timing 50ms, 1 second at count 20, display 60 seconds timing (query mode)***********/
#include
#include
#define uchar unsigned char
#define uint unsigned int
0x3f,0x06,0x5b,0x4f,0x66,0x6d,0x7d,0x07,0x7f,0x6f
};
int t,k,dat;
void delay(int ms)
{
while(ms--)
{
int i;
for(i=0;i<30;i++);
}
}
void Timer0()
{
if(TF0==1)//Query TF0 and it is 1, which means the count is full and the count is ended.
{
t++;
TH0=0x3c;//Here is to reload the initial value after the count is full. You can also use TH0=(65536-5000)/256
TL0=0xb0;//After the count overflows, count again from here, or TL0=(65536-5000)%256
/*If it is troublesome to calculate the initial value first, you can also use the maximum value of 16-bit binary 65536-timer count times to assign TH0 and TL0. For example, if the timing is 40ms, you need to count 4000 machine cycles, you can use
TH0=(65536-4000)/256; TL0=(65536-4000)%*/
TF0=0;
}
//Clear overflow flag
}
void T1s()
{
if(t==20)//Count once for 50ms, 20 times for 1 second
{t=0;
dat++;
if(dat==60)//60 times is 1 minute
dat=0;
}
}
{
TMOD=0x01;
/*This setting (0000 0101) T0's GATE=0, C/T is 0, M1M0 is 01.
GATE=0, turn off INT0 (P3.2) pin's control of counting start, only TR0 controls the start.
C/T=0, timing function, count the number of machine cycles.
M1M0=01, select counting mode 1, 16-bit binary counter, count from TH0 TL0 to FFFFH, and
then overflow. If it is timing/counting mode, set TF0 to 1 after overflow, and the counting timing ends. If it is
interrupt mode, clear 0, hardware sets TF0 to 1, counting ends, that is, interrupt ends, and TF0 is automatically cleared to 0.
Turn on counter 0 interrupt and set ET0=1, EA=1 */
TH0=0x3c;//Set the initial value of the counter to count for 50ms and start counting from 3CB0H
TL0=0xb0;//Start counting from the setting here for the first time
TR0=1;
while(1)
{
Timer0();
T1s();
P0=yu[dat%10];
delay(1);
P2=0x01;
delay(1);
P2=0x00;
P0=yu[dat/10];
delay(1);
P2=0x02;
delay(1);
P2=0x00;
}
}
/*******Timer/Counter 0 interrupt application, the digital tube display increases by 1 every time the key is pressed (interrupt mode)*************/
#include
#include
#define uchar unsigned char
#define uint unsigned int
0x3f,0x06,0x5b,0x4f,0x66,0x6d,0x7d,0x07,0x7f,0x6f
};
int k;
void delay(int ms)
{
while(ms--)
{
int i;
for(i=0;i<30;i++);
}
}
void ddd() interrupt 1
{
TH0=0xff;//Here is the initial value of the count after the count is full
TL0=0xfa;//After the count overflows, the count starts again from here
delay(5);
if(TF0==0)//When the count is interrupted, TF0 is set to 1 by hardware, responds to the interrupt and starts counting, and automatically clears to 0 after the count overflows, ending the count.
{ //Therefore, after responding to the interrupt, querying the status of TF0 can determine whether the interrupt count has ended
if(k==99)
k=0;
else
k++;
}
}
{
TMOD=0x05;
/*This setting (0000 0101) T0's GATE=0, C/T is 1, M1M0 is 01.
GATE=0, turn off INT0 (P3.2) pin's control of count start, only TR0 controls start.
C/T=1, count function, count pin T0 (P3.4) state changes.
M1M0=01, select counting mode 1, 16-bit binary counter, count from TH0 TL0 to FFFFH, and then overflow. If it is timing/counting mode, TF0 will be set to 1 after overflow, and the counting timing will end. If it is interrupt mode, it will be cleared to 0. Hardware will set TF0 to 1, and the counting will end, that is, the interrupt will end, and TF0 will be automatically cleared to 0. Turn on counter 0 interrupt and set ET0=1, EA=1 */[page]
TH0=0xff;//Set the initial value of the counter
TL0=0xfc;//Start counting from the setting here for the first time
ET0=1;
TR0=1;
EA=1;
while(1)
{
P0=yu[k%10];
delay(1);
P2=0x01;
delay(1);
P2=0x00;
P0=yu[k/10];
delay(1);
P2=0x02;
delay(1);
P2=0x00;
}
} /******Count in query mode #include
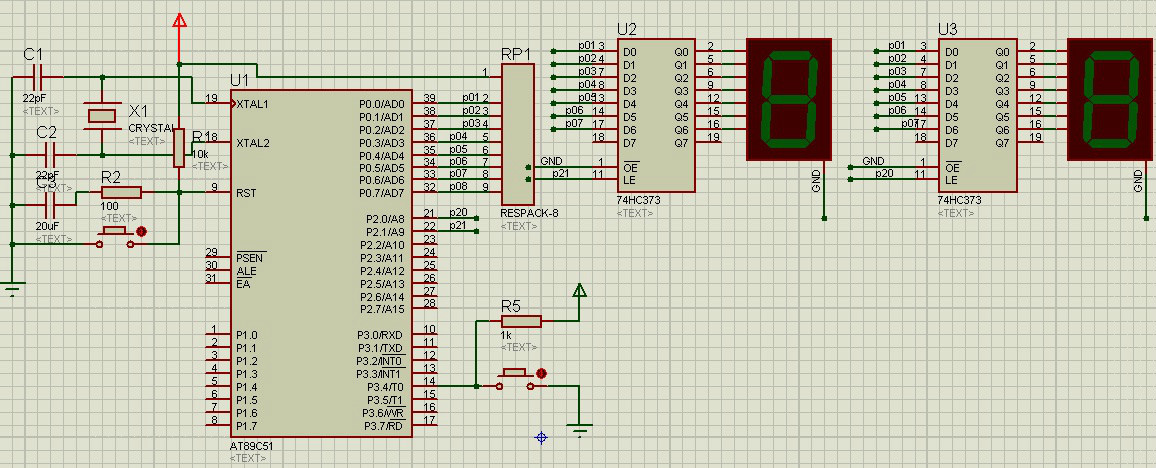
0x3f,0x06,0x5b,0x4f,0x66,0x6d,0x7d,0x07,0x7f,0x6f
};
int k;
void delay(int ms)
{
while(ms--)
{
int i;
for(i=0;i<30;i++);
}
}
void jishu()
{
if(TF0==1)//Query TF0, it is 1, indicating that the count is full and the count is over.
{
TH0=0xff;//Here is the initial value of the count after the count is full
TL0=0xff;//After the count overflows, the count starts again from here
delay(5);
if(k==99)
k=0;
else
k++;
}
TF0=0; //Clear overflow flag
}
{
TMOD=0x05;
/*This setting (0000 0101) T0's GATE=0, C/T is 1, M1M0 is 01.
GATE=0, turn off INT0 (P3.2) pin's control of count start, only TR0 controls start.
C/T=1, count function, count pin T0 (P3.4) state changes.
M1M0=01, select counting mode 1, 16-bit binary counter, count from TH0 TL0 to FFFFH, and then overflow. If it is timing/counting mode, TF0 will be set to 1 after overflow, and the counting timing will end. If it is interrupt mode, it will be cleared to 0. Hardware will set TF0 to 1, and the counting will end, that is, the interrupt will end, and TF0 will be automatically cleared to 0. Turn on counter 0 interrupt and set ET0=1, EA=1 */
TH0=0xff;//Set the initial value of the counter
TL0=0xff;//Start counting from the setting here for the first time
TR0=1;
while(1)
{
jishu();
P0=yu[k%10];
delay(1);
P2=0x01;
delay(1);
P2=0x00;
P0=yu[k/10];
delay(1);
P2=0x02;
delay(1);
P2=0x00;
}
}
/**********************Design stopwatch and display using timing interrupt********************************/
#include
#include
#define uchar unsigned char
#define uint unsigned int
0x3f,0x06,0x5b,0x4f,0x66,0x6d,0x7d,0x07,0x7f,0x6f
};
int k,dat;
void delay(int ms)
{
while(ms--)
{
int i;
for(i=0;i<30;i++);
}
}
void ddd() interrupt 1
{
TH0=(8192-4000)-(8192-4000)%32;//Here is the reload initial value after the count is full
TL0=(8192-4000)%32;//After the count overflows, the count starts again from here
delay(5);
if(TF0==0)//When the count is interrupted, TF0 is set to 1 by hardware, responds to the interrupt and starts counting, and is automatically cleared to 0 after the count overflows, ending the counting.
{ //Therefore, after responding to the interrupt, querying the status of TF0 can determine whether the interrupt count has ended
if(k==250)
{k=0;
dat++;}
else
k++;
//Close T0 counter, TR0=0 sentence cannot be in the main program, it must be in the query function or interrupt function, otherwise it cannot be stopped.
}
}
{
TMOD=0x00;
/*This setting (0000 0101) T0's GATE=0, C/T is 1, M1M0 is 01.
GATE=0, turn off INT0 (P3.2) pin's control of count start, only TR0 controls start.
C/T=1, count function, count pin T0 (P3.4) state changes.
M1M0=01, select counting mode 1, 16-bit binary counter, count from TH0 TL0 to FFFFH, if it is in timing/counting mode, set TF0 to 1 after overflow, and the counting timing ends. If it is in interrupt mode, it is cleared to 0, and the hardware sets TF0 to 1, the counting ends, that is, the interrupt ends, and TF0 is automatically cleared to 0. Turn on counter 0 interrupt and set ET0=1, EA=1 */
TH0=0xa3; //Set the initial value of the counter
TL0=0x00; //Start counting from the setting here for the first time
ET0=1;
TR0=1;
EA=1;
while(1)
{
P0=yu[dat%10];
delay(1);
P2=0x01;
delay(1);
P2=0x00;
delay(1);
P2=0x02;
delay(1);
P2=0x00;
delay(1);
P2=0x04;
delay(1);
P2=0x00;
( 1 ) ; P2
= 0x08 ;
delay ( 1 ) ; P2
= 0x00 ;
}
}
=== ... P0,a mov P2,#02h nop nop mov P2,#00h mov a,b movc a,@a+dptr mov P0,a mov P2,#01h nop nop mov P2,#00h sjmp disp T0ZD:mov TL0,#00h mov TH0,#83h cpl p1.7 cjne r7,#250D,zzz mov r7,#00h cjne r3,#60h,ddd mov r3,#00h ddd: inc r3 zzz: inc r7 reti org 0300h db 3fh,06h,5bh,4fh,66h,6dh,7dh,07h,7fh,6fh end ===================================================
Previous article:4x4 keyboard program written using 51 single chip interrupt
Next article:About 51 single chip microcomputer two-machine communication
- Popular Resources
- Popular amplifiers
- Learn ARM development(16)
- Learn ARM development(17)
- Learn ARM development(18)
- Embedded system debugging simulation tool
- A small question that has been bothering me recently has finally been solved~~
- Learn ARM development (1)
- Learn ARM development (2)
- Learn ARM development (4)
- Learn ARM development (6)
Professor at Beihang University, dedicated to promoting microcontrollers and embedded systems for over 20 years.
- LED chemical incompatibility test to see which chemicals LEDs can be used with
- Application of ARM9 hardware coprocessor on WinCE embedded motherboard
- What are the key points for selecting rotor flowmeter?
- LM317 high power charger circuit
- A brief analysis of Embest's application and development of embedded medical devices
- Single-phase RC protection circuit
- stm32 PVD programmable voltage monitor
- Introduction and measurement of edge trigger and level trigger of 51 single chip microcomputer
- Improved design of Linux system software shell protection technology
- What to do if the ABB robot protection device stops
- Detailed explanation of intelligent car body perception system
- How to solve the problem that the servo drive is not enabled
- Why does the servo drive not power on?
- What point should I connect to when the servo is turned on?
- How to turn on the internal enable of Panasonic servo drive?
- What is the rigidity setting of Panasonic servo drive?
- How to change the inertia ratio of Panasonic servo drive
- What is the inertia ratio of the servo motor?
- Is it better for the motor to have a large or small moment of inertia?
- What is the difference between low inertia and high inertia of servo motors?
- Looking forward to Huawei's operating system!
- What is the input voltage of the power chip that steps down the 24V battery to 5V?
- Why can't the segment code LCD screen be lit up when driving with STML152?
- Disassembling Nokia Bluetooth Headset BH501 from over 10 years ago
- Analysis of the types of pads and design standards in PCB design
- The pitfalls encountered when playing with TMS320F28379D
- Add RTT log output to common projects. Simple configuration. It is very easy to use.
- AC Current Sensor = AC Current Transducer = AC Current Transducer
- The control motor is found to have insufficient stroke. Please provide a solution.
- [Flower carving DIY] Interesting and fun music visualization series project (27) - Magnetic stirring LED water rotating lamp