
TI's MSP430 series of microcontrollers conform to these development trends. Its low power consumption makes it suitable for battery-powered devices or handheld devices. This series of single-chip computers also integrates a large number of peripheral modules into the chip, so it is also suitable for forming a relatively complete system on chip. Its rich models give designers great flexibility in choice. The MSP430 series adopts a 16-bit reduced instruction architecture, with a large number of working registers and data memory (MSP430F449 contains the largest 2KB of RAM). It can be said that the MSP430 series of microcontrollers has become a dazzling new star among many microcontrollers with these outstanding performance characteristics. Radar level meter is a typical example of radar technology applied to the civilian field. It is used in the liquid level measurement of high-pressure storage tanks in the petroleum industry and other industries. The products developed by foreign companies are expensive, and the relevant research results in China are not satisfactory. Therefore, the development of high-performance and intelligent radar level meter is of great significance to the update of liquid level measurement instruments in my country's petroleum industry. In order to meet the industrial standard of intrinsic safety, the developed radar liquid meter has extremely strict requirements on the system. Its power consumption must be less than 70mW, and the accuracy must reach 5mm. This provides an opportunity for the MSP430 series of microcontrollers to play their strengths. By selecting the most advanced MSP430F449 in this series of products, making full use of its low power consumption, high performance, and rich on-chip peripherals to build a system platform, and using special system control and signal processing mechanisms, the system index requirements are well achieved.

1 MSP430FF449简介 MSP430FF449是MSP430系列产品中最高档的型号。它采用16位RISC结构,具有丰富的片内外设和大容量的片内工作寄存器和存储器,性能价格比很高。它的特点有: %26;#183;超低的功耗:能够在1.8~3.6V的电压下工作;具有工作模式(AM)和五种低功耗模式(LPM)。在3V、1MHz时钟驱动下,各个工作模式下的供电电流典型值如表1所示。 表1 SMP430F449工作模式与耗电电流 工作模式 AM LPM0 LPM2 LMP3 LMP4 供电电流/μA 420 55 27 1.6 0.1 可见工作模式供电电流典型值低达420μA,低功耗,低功耗模式电流更是显著降低,最低为0.1μA。 在低功耗模式下,CPU可以被中断唤醒,响应时间小于6μs。 %26;#183;较强的运算功能:16位的RISC结构,丰富的寻扯方式;具有16位中断源,并且可以任意嵌套;在8MHz时钟驱动下指令周期可达 125ns;内部包含硬件乘法器和大量寄存器以及多达64K Byte和FLASH程序空间和2K Byte的RAM空间,为存储数据和进行运算提供了保证。这些特点使MSP430F449具有很强的数字信号处理能力,可以开发出高效率的源程序。 %26;#183;丰富的片上外设:包括看门狗定时器,基于定时器,比较器,16Bit定时器(TA、TB),串口0、1,液晶显示驱动器,六个8bit 的I/O端口,12位ADC(最高采样率200kHz)等。丰富的片上外设使设计者可以很方便地构建一个较为完整的系统。另外,充分利用计数器的多路任意波形产生功能和中断控制功能,保证了一些复杂的时序控制任务的完成。 %26;#183;方便高效的开发环境:MSP430F449是FLASH型器件,片内有JTAG调试接口和电可擦写的FLASH存储器,所以可以先下载程序到FLASH内,再在器件内通过软件控制程序的运行,由JTAG接口读取片内信息供设计得调试。这种方式不需要仿真器和编程器,调试十分方便。 2 雷达液位仪实现方案 2.1 雷达液位系统结构 低功耗、高精度智能雷达液位仪的系统结构如图1所示。 图3 系统硬件分为三部分:测量模块、HART通信模块和测量线。测量模块电路板包括MSP430F449控制器、直接数字频率合成器(DDS)控制的窄脉冲产生电路、脉冲收发与处理电路、A/D采样、结果显示等。这个模块完成距离的精确测量,并实时时通过HART板同上位机进行数据通信。HART板完成 MSP430F449控制器与上位进行数据通信。HART板完成MSP430F449控制器与上位机的通信、4~20mA电流的产生、电源电压的转换。测量线包括与测量板之间的机械接口、法兰和电缆。该系统还包括主控计算机上的人机交互软件,系统和主控计算机的连接采用符合工业标准的两线制,即电源线和信号线共用。 在系统工作时序的设计中,采用系统间歇工作方式,以40ms为一个周期。前1ms为电路工作时间,MSP430F449的CPU被中断唤醒后,打开电路中双路DDS、双路窄脉冲产生电路、ADC等部分电路,自身采集A/D转换后得到的数据。后39ms为电路休眠时间,MSP430F449的CPU关闭这些外围电路和片内外设,自身进入信号处理主程序,完成信号处理工作后再进入休眠模式。这种工作方式既考虑到对到系统功耗的要求,也兼顾了 MSP430F449的信号处理速度。 在信号处理机制上,由于系统要求的测量范围为0.25m~30m,精度为%26;#177;5mm,以目前的电子技术水平,如果采用直接测量一个周期发射脉冲和接收脉冲之间的时间间隔的方式,是很难达到这样的要求的。所以在信号处理机制中采用了时间比例放大技术,并且以模拟相乘的方法实现了时间轴的放大。具体的电路实现用到了DDS技术和窄脉冲产生技术。 MSP430F449在系统中完成了对系统工作时序的控制、数据采集与信号处理、结构显示、与主机通信等诸多任务。下面将对具体的设计作一介绍。

2.2 MSP430F449 Control of System Timing The intermittent working mode of the system has been introduced before. The timing control of this working mode is realized by using the multi-channel arbitrary waveform generation function and interrupt control function of the counter of MSP430F449, as well as the interrupt fast wake-up function of the CPU. After the system is reset, MSP430F449 first initializes the circuit, including setting the two 16-bit counters TA and TB inside the MSP430F449 and their interrupts, setting two DDS, setting the on-chip ADC, setting the HART board, etc. After that, the CPU of MSP430F449 turns on the counter TB to start counting, and enters the extremely low power sleep mode. The system realizes the required working timing under the control of the TB output signal. The output waveforms of TB and TA are shown in Figure 2. Among them, the output signal of counter A is set to the sampling clock source of the on-chip ADC, and the sampling frequency is set to 200kHz; the counting period of counter B is set to 40ms, and the output waveform of the corresponding channel is set to sleep. The MSP430F449 and the external circuit need to be set to work or sleep. The registers of TB that need to be set include control register, count value register, capture/compare control register, capture/compare register, etc. They define the clock source, working mode, count cycle, output mode, interrupt, etc. of TB. In the waveforms output by TB in Figure 2, TB1 is used as the system interrupt source. Interrupt 1 wakes up the CPU, and the CPU turns on the ADC to collect the echo signal and the echo data; at interrupt 2, the CPU turns off the ADC and the external circuit. TB2 and TB3 control the opening and closing of the two narrow pulse generating circuits respectively. TB4 is used as the switching signal of the dual-channel DDS. 2.3 MSP430F449 measurement method and signal processing As mentioned earlier, the innovative time ratio amplification technology is used in the signal processing mechanism. This technology amplifies the time interval between the transmitting pulse and the receiving pulse according to a certain ratio. Time ratio amplification requires another reference signal with a frequency very close to the transmitting pulse frequency. In this design, according to the needs of time ratio amplification measurement, dual-channel signals of 1MHz, 1MHz+100Hz and 1MHz, 1MHz+4MHz are generated to control the transmitting pulse and reference pulse generating circuits, and their relative phases need to be accurately controlled. These two signals are generated by controlling the dual-channel direct digital frequency synthesizer (DDS) AD9834 through MSP430F449. DDS technology is widely used for its extremely high frequency resolution, extremely short frequency conversion time, and continuous output signal phase. This design uses AD's DDS chip AD9834, which contains phase accumulator, programming register, serial I/O interface, sine lookup table, D/A converter, etc. The AD9834 frequency control word is 28 bits, the frequency resolution is 0.0186Hz when the system clock is 5MHz, and the power consumption is 20mW when the power supply voltage is 3V. AD9834 provides a low power mode, which is controlled by the output signal of TB4. The MSP430F449 communication serial I/O port controls the dual-channel DDS output frequency and relative phase. The frequency spectrum when the MSP430F449 controls the two AD9834 output signals with frequencies of 1.000119MHz and 1.000123MHz respectively is shown in Figure 3. A complete measurement process is divided into two parts: target search and precise measurement. It takes two TB cycles to complete a target search. In this stage, the frequency of the transmitted pulse is 1MHz+100Hz, and the frequency of the reference pulse is 1MHz. According to the analysis, the time scale magnification factor K=10001, the maximum measurement distance of the system is 30m, and the maximum time interval between the transmitted pulse and the received pulse is 200ns; after time scale magnification, the maximum time interval is 2.0001ms, so two sampling cycles can record all possible positions of the target. The target position is determined based on the data recorded twice and converted into phase. In the third TB cycle, the MSP430F449 enters the precise measurement stage. The AD9834 phase that generates the reference pulse clock is set by the target phase value recorded in the target search stage, and the frequency is set to 1MHz+4Hz, and the AD9834 frequency that generates the pulse clock is set to 1MHz. At this time, the corresponding scale magnification factor K=250001. Under the 200kHz sampling clock, the time resolution is 20ps, and the corresponding distance resolution is 3mm, which can meet the system distance accuracy requirements in the precise measurement stage. 2.4 MSP430F449 and HART protocol communication module The measurement results of the liquid level meter and the control signal of the PC to the liquid level meter are transmitted through the HART communication module. HART can address remote sensors. The high-speed channel open communication protocol is a communication protocol used between field intelligent instruments and control room equipment. It uses audio digital signals superimposed on 4-20mA analog signals for two-way digital communication without affecting the size of the analog signal transmitted to the control system, ensuring compatibility with existing analog systems. In this design, a simplified three-layer model structure of the HART protocol is used, namely the first physical layer, the second data link layer and the seventh application layer. The HART protocol block diagram is shown in Figure 4.

The HART communication module also adopts a low-power design scheme and selects low-power devices in the hardware design. Its hardware implementation block diagram is shown in Figure 5. The D/A converter AD421 outputs a DC signal of 4-20mA current that conforms to the two-wire system. The HART modem HT2015 and its auxiliary circuits realize the modem function of HART communication. The MSP430F449 is connected to the HART communication module through the internal integrated universal serial transceiver module UART. After the HART communication module modulates and demodulates the signal, it communicates asynchronously with the serial port of the host computer through two lines. The serial port of the computer is equipped with a HART conversion card. In addition, the HART communication module also uses the DC-DC conversion chip MAX1745 to complete the conversion of the power supply voltage and power the entire system. The software implementation of the specific protocol can be flexibly compiled by yourself. Compared with the traditional solution, this solution has the advantages of higher reliability, stronger real-time performance, and lower cost. The main technical indicators achieved by the radar level meter are: maximum measurement range of 30m, resolution of 1mm, measurement error ≤5mm, working current of 8.5mA when working at 3.3V voltage, and power consumption of 30mW.
Previous article:Detailed explanation of infrared information data processing system
Next article:Application of ultrasonic distance measurement in the field based on NEC single chip microcomputer
Recommended ReadingLatest update time:2024-11-16 19:41
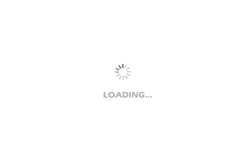
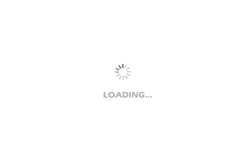
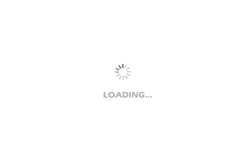
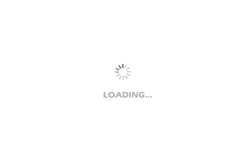
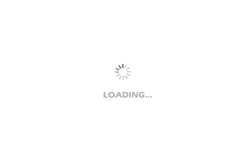
- Popular Resources
- Popular amplifiers
-
Wireless Sensor Network Technology and Applications (Edited by Mou Si, Yin Hong, and Su Xing)
-
Principles and Key Technologies of Lithium-ion Batteries (Edited by Huang Kelong, Wang Zhaoxiang and Liu Suqin)
-
Analog Engineer\'s Pocket Reference TI Chinese Edition
-
TI\'s switching power supply EMI conduction solution
Professor at Beihang University, dedicated to promoting microcontrollers and embedded systems for over 20 years.
- Innolux's intelligent steer-by-wire solution makes cars smarter and safer
- 8051 MCU - Parity Check
- How to efficiently balance the sensitivity of tactile sensing interfaces
- What should I do if the servo motor shakes? What causes the servo motor to shake quickly?
- 【Brushless Motor】Analysis of three-phase BLDC motor and sharing of two popular development boards
- Midea Industrial Technology's subsidiaries Clou Electronics and Hekang New Energy jointly appeared at the Munich Battery Energy Storage Exhibition and Solar Energy Exhibition
- Guoxin Sichen | Application of ferroelectric memory PB85RS2MC in power battery management, with a capacity of 2M
- Analysis of common faults of frequency converter
- In a head-on competition with Qualcomm, what kind of cockpit products has Intel come up with?
- Dalian Rongke's all-vanadium liquid flow battery energy storage equipment industrialization project has entered the sprint stage before production
- Allegro MicroSystems Introduces Advanced Magnetic and Inductive Position Sensing Solutions at Electronica 2024
- Car key in the left hand, liveness detection radar in the right hand, UWB is imperative for cars!
- After a decade of rapid development, domestic CIS has entered the market
- Aegis Dagger Battery + Thor EM-i Super Hybrid, Geely New Energy has thrown out two "king bombs"
- A brief discussion on functional safety - fault, error, and failure
- In the smart car 2.0 cycle, these core industry chains are facing major opportunities!
- The United States and Japan are developing new batteries. CATL faces challenges? How should China's new energy battery industry respond?
- Murata launches high-precision 6-axis inertial sensor for automobiles
- Ford patents pre-charge alarm to help save costs and respond to emergencies
- New real-time microcontroller system from Texas Instruments enables smarter processing in automotive and industrial applications
- Let's study together. This e-book is well written in Chinese.
- Where do you go to buy components? e-Network has spot products and can receive them the next day.
- RFID related CPU card
- EEWORLD University Hall----TI Cup 2019 National College Student Electronic Design Competition Topic Analysis and Technical Exchange Seminar
- Conversion relationship of various parameters of VSWR
- [Raspberry Pi Pico Review] - Unboxing + Download
- Hydrogen escape problem
- How do I convert a^(b^2) to the power of a^b?
- [Review of the RTT of the Bluesight AB32VG1 RISC-V board] 5: Tragedy caused by manually replacing the Studio file
- MSP430G2553 study notes DAY1 Knowledge reserve and device initialization