1 Overall design and working principle
The overall block diagram of the inverter power supply system is shown in Figure 1. The main circuit of the system adopts a two-stage structure of front-stage push-pull boost and rear-stage full-bridge inversion, which can avoid the use of industrial frequency transformers, effectively reduce the volume and quality of the power supply, and improve the inverter efficiency. Its working principle is: the 12 V DC input voltage is filtered, pushed-pull boosted and full-bridge rectified to a DC bus voltage of 350 V, and then converted into 220 V/50 Hz industrial frequency AC power through a full-bridge inverter circuit.
In order to reduce the impact of input voltage, the output voltage after full-bridge rectification is sampled as feedback voltage to control the controller of the front-stage push-pull boost circuit, and the duty cycle of the SG3525A output PWM waveform is adjusted to keep the voltage of the DC bus at 350 V. At the same time, the voltage on the output filter capacitor and the current on the output filter inductor are sampled, and the voltage and current dual-loop control is adopted to adjust the SPWM output of the rear-stage full-bridge inverter circuit, thereby obtaining good output waveform characteristics and stable load characteristics. [page]
2 System Hardware Design
2.1 Generation of Push-Pull Boost PWM Waveform
The DC boost circuit adopts push-pull type, which has simple structure and high efficiency. The power tubes VQ1 and VQ2 in the circuit are controlled by two complementary PWM waves generated alternately by SG3525A outputA and outputB to control the on and off. SG3525A can generate PWM waveforms of different frequency bands between 100Hz and 500kHz by adjusting external resistors and capacitors. The relationship between the frequency fPWM of its PWM wave and the external resistors RT, RD, and external capacitors CT is:
SG3525A can automatically adjust the duty cycle of the PWM wave through the feedback DC bus voltage to make the output stable. At the same time, SG3525A has the input undervoltage lockout and PWM lockout functions of the voltage. Once overcurrent or overvoltage occurs, the PWM can be quickly turned off to ensure the safety of the entire circuit.
2.2 Generation of Full-Bridge Inverter SPWM Waveform
The SPWM waveform is generated by AT90PWM2 of the AVR microcontroller series. AT90PWM2 has two 12-bit waveform generators PSC0 and PSC2, which generate two complementary SPWM signals respectively. After isolation and amplification by the driving circuit, they drive the power tubes in the full-bridge inverter. PSC0 generates the control signals for VQ3 and VQ4, and PSC2 generates the control signals for VQ5 and VQ6.
Select PSC to work in center-aligned mode, and PSCO and PSC2 to work in synchronization. Then the PSC counter starts counting from the maximum value defined by register OCRnRB, first decreases to zero and then increases to the maximum value. When the value of the PSC counter is equal to the value of register OCRnSB and OCRnSA, the level of PSCn output pins PSCOUTn0 and PSCOUTnl will be changed respectively.
The relationship between its triangular wave carrier period fSPWM and PSC counting frequency fPSC and registers OCRnRB and OCRnRA (n=0 or 2) is:
2.3 Full-bridge inverter circuit
The inverter circuit is the core component of the inverter power supply, completing the process of converting DC voltage into AC voltage. The full-bridge inverter circuit is composed of 4 IGBTs as power tubes. This circuit has the advantages of convenient control and high power tube utilization. The IR2110 drive circuit can be used. The IR2110 uses highly integrated level conversion technology, which greatly simplifies the control requirements of the logic circuit for power devices and improves the reliability of the drive circuit. In particular, the upper tube uses an external bootstrap capacitor, which greatly reduces the number of drive power supplies compared to other drivers, as shown in Figure 2.
[page]
2.4 Output LC filter circuitSince the output of the full-bridge inverter circuit is a 50Hz fundamental wave and other high and low harmonics, in order to obtain a pure sinusoidal waveform, it is necessary to consider setting up a filtering link. Because the harmonics are mainly concentrated around 1 and 2 times fSPWM, the cutoff frequency fc is set to fSPWM/5. Then:

Where, R is the equivalent load resistance of the DC side, Vout is the output current and voltage, and P is the rated power of the inverter.
3 System Software Design
3.1 Introduction to the MCU
AT90PWM2 is an AVR series MCU. The main features of this MCU are: 1) High-performance 8-bit RSIC structure, 1 MIPS/MHz, supporting a clock of up to 16 MHz; 2) 8 KB system programmable (ISP) Flash memory, supporting bootstrap programming, 512 bytes SRAM, 512 bytes EEPROM; 3) 4 PWM channels provide various PWM signals and can set dead zones; 4) 8-channel 10-bit ADC module, 1 10-bit DAC module, 2 analog comparators; 5) Up to 29 interrupt sources; 6) Support UART, SPI, I2C communication methods. Its pin function distribution diagram is shown in Figure 3.
Among them, PSCOUT00~PSCOUT21 pins are SPWM wave output pins, which are used to drive the power switch tube, and SD pin is the enable control of IR2110, which is used to open or lock the conduction of SPWM. V_MAIN, V_OUT, and I_OUT pins are used to sample bus voltage, output capacitor current, and inductor voltage respectively. The single-chip microcomputer also includes the use of LED alarm function, driving the fan to start the cooling function when overheating, ISP online download and update the driver, and reserved serial communication function.
3.2 Control strategy
This digital system adopts inductor current feedback control. The output inductor current is introduced into the control system, and a double closed-loop control is formed together with the output capacitor voltage. By sampling the output inductor current and output capacitor voltage, the control signal of the outer loop voltage error is used to control the inner loop current, and the current is adjusted to make the output voltage track the reference voltage value, thereby improving the dynamic response of the system. Due to the existence of the inner loop, the double closed-loop control system increases the bandwidth of the control system, accelerates the dynamic response of the inverter, reduces the harmonic content of the output voltage, and enhances the adaptability to nonlinear loads. The outer loop regulator can adjust the given value of the inner loop regulator according to the load change, so that the regulation system still has good quality. Therefore, the dual closed-loop control system has a strong adaptability to load changes and can greatly improve the output performance of the inverter power supply. In order to simplify the design of the voltage outer loop, the current inner loop can be regarded as a proportional link and the voltage outer loop can be regarded as a PI link. Figure 4 is a block diagram of the dual-loop control system.
[page]
3.3 Software FlowThe system software design adopts modular design, mainly including: hardware initialization module, sine table initialization module, output protection module, dual closed-loop regulation module, and interrupt processing module. The flow of the main program and SPWM interrupt processing module are shown in Figure 5(a) and Figure 5(b) respectively.
4 Experimental results
According to the above ideas, a 1 kW prototype was made. IRF3805 was used as the push-pull boost power tube, RHRP8120 was used as the rectifier diode, LRG4-PC50UD was used as the full-bridge inverter power tube, SG3525A PWM wave frequency was set to 80 kHz, SPWM wave frequency was set to 10 kHz, output filter inductor L was 2.5 mH, output filter capacitor C was 4.7 μF, and the sinusoidal AC output voltage accuracy was 220 V±1%, frequency accuracy was 50 Hz±0.1%, and THD was less than 1%. The inverter efficiency was greater than 90%, and the test waveforms at no load and full load were shown in Figure 6(a) and Figure 6(b).
5 Conclusion
A design method for a digital inverter power supply is proposed, in which the front stage is controlled by SG3535A for push-pull boost and the back stage is based on AT90PWM2 for full-bridge inverter. The waveform generator of AT90PWM2 is used to generate SPWM waveform, which effectively simplifies the circuit. The front-end negative feedback and the back-end double closed-loop regulation make the inverter power supply have high performance of output voltage characteristics. The reserved serial communication and online download functions enable the inverter power supply to communicate with the host computer and have expansion functions. The perfect protection measures can make the inverter power supply have perfect indication and automatic processing functions when a fault occurs.
Previous article:Design and implementation of ship weather instrument test system based on AVR microcontroller
Next article:Design of multi-protocol reader/writer based on AVR microcontroller
Recommended ReadingLatest update time:2024-11-17 00:38
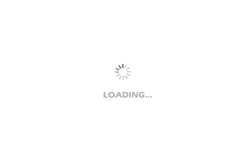
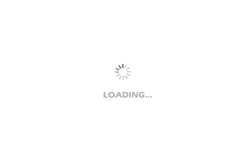
- Popular Resources
- Popular amplifiers
-
西门子S7-12001500 PLC SCL语言编程从入门到精通 (北岛李工)
-
100 Examples of Microcontroller C Language Applications (with CD-ROM, 3rd Edition) (Wang Huiliang, Wang Dongfeng, Dong Guanqiang)
-
Power Electronics Technology (Editor-in-Chief: Wang Luyang; Deputy Editor-in-Chief: Wang Hexing)
-
Building real-time machine learning systems
Professor at Beihang University, dedicated to promoting microcontrollers and embedded systems for over 20 years.
- Innolux's intelligent steer-by-wire solution makes cars smarter and safer
- 8051 MCU - Parity Check
- How to efficiently balance the sensitivity of tactile sensing interfaces
- What should I do if the servo motor shakes? What causes the servo motor to shake quickly?
- 【Brushless Motor】Analysis of three-phase BLDC motor and sharing of two popular development boards
- Midea Industrial Technology's subsidiaries Clou Electronics and Hekang New Energy jointly appeared at the Munich Battery Energy Storage Exhibition and Solar Energy Exhibition
- Guoxin Sichen | Application of ferroelectric memory PB85RS2MC in power battery management, with a capacity of 2M
- Analysis of common faults of frequency converter
- In a head-on competition with Qualcomm, what kind of cockpit products has Intel come up with?
- Dalian Rongke's all-vanadium liquid flow battery energy storage equipment industrialization project has entered the sprint stage before production
- Allegro MicroSystems Introduces Advanced Magnetic and Inductive Position Sensing Solutions at Electronica 2024
- Car key in the left hand, liveness detection radar in the right hand, UWB is imperative for cars!
- After a decade of rapid development, domestic CIS has entered the market
- Aegis Dagger Battery + Thor EM-i Super Hybrid, Geely New Energy has thrown out two "king bombs"
- A brief discussion on functional safety - fault, error, and failure
- In the smart car 2.0 cycle, these core industry chains are facing major opportunities!
- The United States and Japan are developing new batteries. CATL faces challenges? How should China's new energy battery industry respond?
- Murata launches high-precision 6-axis inertial sensor for automobiles
- Ford patents pre-charge alarm to help save costs and respond to emergencies
- New real-time microcontroller system from Texas Instruments enables smarter processing in automotive and industrial applications
- C6000 DSP - About startup method
- Altera SoC Architecture Excerpt - Altera SoC FPGA Adaptive Debug
- MSP430F149 minimum system circuit diagram
- Initial debugging of NXP beacon camera (avoid detours)
- [HPM-DIY] openmv for hpm6750 progress 1
- Weekly review information
- Calculating sound decibels
- Indian engineer sues SpaceX, alleging discrimination at work
- "Notifying employees of slacking off at work", Gome responds
- Uncover the real reason behind the explosive development of TWS headphones