1. Introduction
Our company is a pharmaceutical company that mainly produces hepatitis B vaccines. The clean environment of the production workshop is provided by the purification central air-conditioning equipment, so that the temperature, humidity and pressure difference of each room in the production workshop can meet the requirements of the national GMP regulations. Due to the change of seasons and the change of day and night, the demand for air volume in each room of the production workshop has obvious changes, and the adjustment of air volume and water flow of the water pump fan is based on the manual adjustment of the damper and throttle valve. When the demand for air volume and water flow decreases, the opening of the damper and valve decreases; when the demand for air volume and water flow increases, the opening of the damper and valve increases. Although this adjustment method is simple and easy and has become a habit, it is at the cost of increasing the loss of the pipeline network and consuming a lot of energy on the damper and valve. Moreover, when the central air conditioner is working normally, the opening of most dampers and valves is 50%-60%, which shows that the design capacity of the existing central air conditioner pump fan is much higher than the actual need, and there is a serious phenomenon of "big horse pulling a small cart", resulting in a large waste of electricity. In recent years, with the rapid development of electricity, electronic technology, and computer technology, variable frequency speed regulation technology has become more and more mature. Therefore, we installed 19 frequency converters on the company's central air-conditioning water pump fans for energy-saving transformation. Because the water pump fans are relatively dispersed, in order to reduce the intensity of the patrol work of the on-duty personnel and facilitate timely grasp of the working status of the water pump fans and find faults, we installed a frequency conversion monitoring system in the central monitoring room through the communication application of PLC and human-machine interface and frequency converter. In this way, the on-duty personnel can directly set the frequency value and start and stop each frequency converter on the human-machine interface, and can monitor the actual working current, voltage, and frequency of the water pump fan motor in real time, and have alarm functions.
2. Frequency conversion transformation plan for central air-conditioning water pump fans
1. Equipment status before transformation
(1) Air conditioning equipment status
of the gene department ① The refrigeration host is a Hitachi unit, a total of three units. ②Refrigeration pump: 11KW, 2-pole full pressure start 4 units, head 30m, outlet water temperature 6℃, return water temperature 10℃, outlet water pressure 0.35Mpa, rated current of each motor 21.8A, normal working current 16.6A. In general, two units are started and two units are spare. ③Cooling pump: 15KW, 2-pole full pressure start 4 units, head 30m, outlet water temperature 32.5℃, return water temperature 28.2℃, outlet water pressure 0.38Mpa, rated current of each motor 29.9A, normal working current 18.0A. In general, two units are started and two units are spare.
(2) Air conditioning equipment in the air conditioning room on the second floor of the old building
① The refrigeration host is a Hitachi unit, a total of two units. ②Refrigeration pump: 15KW, 3 units of 2-pole full pressure start, head 30m, outlet water temperature 6.1℃, return water temperature 9.8℃, outlet water pressure 0.36Mpa, rated current of each motor 29.9A, normal working current 21A. In general, one unit is used and two units are spare. ③Cooling pump: 15KW, 3 units of 2-pole full pressure start, head 30m, outlet water temperature 31.8℃, return water temperature 27.7℃, outlet water pressure 0.41Mpa, rated current of each motor 29.9A, normal working current 20.6A. In general, one unit is used and two units are spare.
(3) Air conditioning equipment in the sub-package air conditioning room
① The refrigeration host is a Hitachi unit, a total of two units. ②Refrigeration pump: 15KW, 2-pole full pressure start-up 3 units, head 30m, outlet water temperature 5.8℃, return water temperature 9.3℃, outlet water pressure 0.38Mpa, each motor rated current 29.9A, normal working current 20.2A. In general, two units are used as spare. ③Cooling pump: 15KW, 2-pole full pressure start-up 3 units, head 30m, outlet water temperature 31.6℃, return water temperature 27.3℃, outlet water pressure 0.40Mpa, each motor rated current 29.9A, normal working current 21.2A. In general, two units are used as spare.
(4) The company has a total of 13 air conditioning cabinets. ① There are 7 air conditioning cabinets in the gene department, including 3 22KW fan motors, 2 11KW fan motors, and 1 15KW and 18.5KW fan motors. ② There are 3 air conditioner cabinets on the old second floor, including 2 15KW fan motors and 1 11KW fan motor. ③ There are 3 air conditioner cabinets in the quality inspection department, including 2 11KW fan motors and 1 7.5KW fan motor.
2. Water pump frequency conversion transformation plan
Because the temperature difference between the inlet and outlet water of the refrigeration pump and the cooling pump is less than 5℃, it means that there is still margin for the flow of chilled water and cooling water. In addition, the normal working current of the motor is less than the rated current (5-12A), and there is obviously a phenomenon of "big horse pulling a small cart". Therefore, we use a Delta VFD-P11KW inverter and a Delta VFD-P15KW inverter for the chilled water system and cooling water system of the gene department respectively to implement one-to-three drive (as shown in Figure 1). PLC1 controls three chilled water pumps and three cooling water pumps to switch between different operations as needed (but one inverter can only drive one pump motor at a time), so that the chilled water and cooling water volumes can be flexibly, conveniently, timely, and appropriately controlled to meet the needs of the production process. Similarly, the chilled water system and cooling water system of the old second floor air-conditioning room and the sub-packaging air-conditioning room are also driven by a Delta VFD-P15KW inverter, and the control method is the same as that of the chilled water system and cooling water system of the gene department. The following is an explanation of the chilled water system of the gene department:
(1) Closed-loop control
The chilled water system of the gene department adopts full closed-loop automatic temperature difference control. A 11KW inverter is used to implement one-to-three. The specific method is: first, fully open all the air valves of the central air-conditioning water pump system, and under the premise of ensuring the chilled water volume and pressure required by the refrigeration unit, determine the lowest operating frequency of a chilled pump inverter (determined to be 35HZ during debugging), set it to the lower limit frequency and lock it. Two temperature sensors are used to collect the outlet water temperature and return water temperature on the chilled water main pipeline, and the temperature difference signal between the two is transmitted to the temperature difference controller. The temperature difference is converted into an analog quantity through PID2 adjustment and fed back to the inverter. When the temperature difference is less than or equal to the set value of 5℃, the chilled water flow can be appropriately reduced. At this time, the inverter VVVF2 runs at a reduced frequency and the motor speed slows down; when the temperature difference is greater than the set value of 5℃, the inverter VVVF2 runs at a higher frequency, the motor speed increases, and the water flow increases. The number of chilled water pumps and their increase and decrease are controlled by PLC1. In this way, the appropriate flow can be provided according to the real-time needs of the system without wasting electricity.
(2) Open-loop control
Turn the conversion switch on the control panel to the open-loop position and rotate the potentiometer clockwise to change the speed of the chilled water pump motor.
(3) Power frequency/variable frequency switching operation
In the automatic working state of the system, when the inverter fails, PLC1 controls another standby water pump motor to run at power frequency, and at the same time sends out an audible and visual alarm to remind the on-duty personnel to find and handle the fault in time. You can also turn the manual/automatic switch on the control cabinet panel to the manual position and press the corresponding start button to start the corresponding water pump motor.
Figure 1 Schematic diagram of frequency conversion transformation of central air-conditioning water pump
3. Frequency conversion transformation plan of fans
Because the fans of all wind cabinets are in full-open and normal load operation state, the cold air outlet valve is used to adjust the air volume during constant temperature adjustment. If the temperature in the production workshop room is high, the air valve will be opened wide to increase the cold air volume and reduce the temperature in the production workshop room. If the temperature in the production workshop room is low, it is necessary to close part of the air valve opening and reduce the cold air volume to maintain the cold and heat balance of the production workshop room. Therefore, the air volume sent into the production workshop is adjustable and variable. Especially during the night shift, there are few people, and there are few activities such as entering and leaving, walking, etc. The system load is very light, and the requirements for air conditioning cooling are greatly reduced. Only a small amount of cold air can maintain the positive pressure and cooling requirements of the production workshop room. Therefore, all 13 fans have undergone frequency conversion energy-saving transformation, and the frequency converter is used to adjust the air volume.
The principle diagram of the frequency conversion transformation of the central air-conditioning fan is shown in Figure 2. On the basis of the original industrial frequency control, 7 frequency conversion control cabinets are added, and 13 Delta VFD-P series inverters are used to drive 13 fan motors. The variable frequency/industrial frequency can be switched between each other. When operating under the industrial frequency method, the original operation method is not changed. When operating under the variable frequency method, the inverter automatically outputs different frequencies in different time periods. That is, the 13 inverters are controlled by the program of the time control switch. The inverter is set to operate at 45HZ from 7:30 to 23:00 from Monday to Friday, and the inverter is set to operate at 35HZ from 23:00 to 7:30 the next day from Monday to Friday and on Saturdays and Sundays (the operating frequency can be set as needed) to change the speed of the fan. At the same time, the 13 inverters are connected to the human-machine interface and PLC of the central monitoring room to realize remote human-machine monitoring.
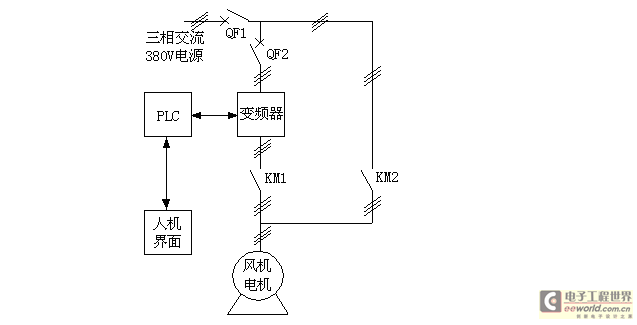
Figure 2 Schematic diagram of frequency conversion transformation of central air-conditioning
fan 3. Energy-saving effect of frequency conversion transformation of central air-conditioning water pump fan
In order to intuitively reflect the energy-saving effect after frequency conversion transformation, we conducted the following test: taking 1# Hitachi unit cooling water pump 14# (15KW) and K4 air cabinet 4# (22KW) as the objects, we installed electric meters on their respective main circuits, first operated them at industrial frequency for one week, recorded the electric meter readings at regular intervals every day, and then operated them at frequency conversion for one week, performing the same work. The data are shown in Tables 1 and 2.
Table 1: Energy-saving data statistics of 1# Hitachi unit cooling water pump

1. Data analysis of Table 1: When the power frequency is running, the load of the water pump does not change much, and its daily power consumption is about 298 degrees. When the frequency conversion is running, the daily power consumption varies greatly due to the greater influence of the external ambient temperature, but it can be seen that the daily power consumption when the frequency conversion is running is obviously less than the value when the power frequency is running. We calculate the total power consumption for a week, which is 2580-891=1689 when the power frequency is running, and 5248-4121=1127 when the frequency conversion is running. The power saving rate of the cooling water pump of the 1# Hitachi unit is: (1689-1127)/1689=33%
2. Data analysis of Table 2: Since the load of the fan does not change much every day, its power consumption is relatively stable. It can be seen that the daily power consumption is about 350 degrees when the power frequency is running. When the frequency conversion is running, the daily power consumption is about 220 degrees. Calculated with 350 and 220, the power saving rate of the K4 wind cabinet motor is: (350-220)/350 = 37%.
From the above calculation, we can know that the average energy saving rate of the water pump and fan after the frequency conversion transformation is 35%. In actual use, the power saving effect will be better.
Table 2: K4 wind cabinet energy saving data statistics
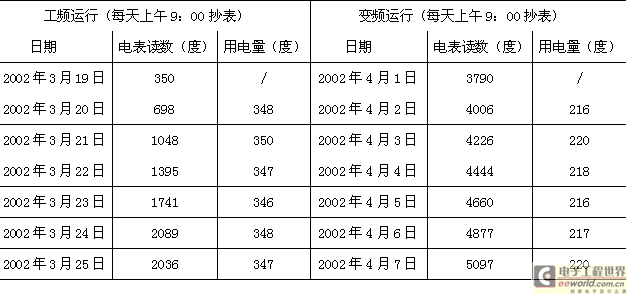
1. System hardware composition
The hardware structure diagram of the central air-conditioning pump fan frequency conversion monitoring system is shown in Figure 3. It consists of four subsystems: the company's tap water constant pressure pump, the second floor refrigeration pump of the sub-packaging department, the pump fan of the air-conditioning room on the second floor of the quality inspection department, and the pump fan of the gene department. It implements remote monitoring of 19 inverters distributed in different departments. The description of each part is as follows: ①. The inverter uses Delta VFD-P series inverters. This series of inverters has high reliability, low noise, high energy saving, sound protection functions, built-in powerful RS-485 serial communication interface, and the RS-485 serial communication protocol is open to users. ②. PLC, as a control unit, is the control core of the entire system. Delta DVP24ES01R is selected. Use its communication instructions to compile a program, download it to the PLC, and then connect it to the RS-485 serial communication interface of the inverter to achieve real-time communication with the inverter. ③. The human-machine interface adopts Hitech's PWS-3760, a 10.4-inch color model. It is a new generation of high-tech programmable terminal, an interactive workstation designed for PLC, capable of connecting and monitoring with PLCs of various brands, suitable for use in harsh industrial environments, and can replace ordinary or industrial computers. Its main features are: large screen capacity, up to 255 screens, simple screen planning; using ADP3 all-Chinese operating software, suitable for WINDOWS95/WINDOWS98 environment, rich macro instructions, simple programming; good interactivity, strong anti-interference ability, high communication reliability; high degree of automation, simple and convenient operation, low failure rate, long life, and low maintenance. Its main functions are: designers can edit various screens as needed to display the device status or system operation instructions in real time; the touch buttons on the human-machine interface can generate corresponding switch signals, or input values and characters to the PLC for data exchange, thereby generating corresponding actions to control the operation of the equipment; multiple screens can be overlapped or switched to display text, numbers, graphics, strings, alarm information, action processes, statistical data, historical records, trend charts, simple reports, etc. ④, RS-485 serial communication method: RS-485 adopts a balanced sending and receiving method, which has the advantages of long transmission distance, strong anti-interference ability and multi-station capability.
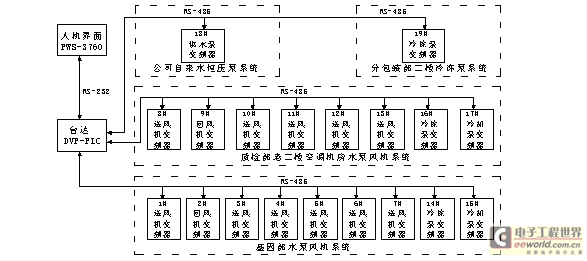
Figure 3 Hardware structure of frequency conversion monitoring system
2. Human-machine interface screen design
All screens of the human-machine interface of this system are designed by ADP3 full Chinese software, including main screen, parameter setting, operation setting, parameter display, status information, alarm information and help screens. After ADP3 software is compiled correctly, it can be downloaded from the personal computer to the human-machine interface for use. The human-machine interface and PLC are connected in a master-slave manner through RS232 communication cable. The PLC reads and writes the status control area and notification area of the human-machine interface to achieve information exchange between the two. The PLC reads the data in the status notification area of the human-machine interface to obtain the current screen number, and forces the screen to switch by writing the data in the status control area of the human-machine interface. One of the parameter display screens is shown in Figure 4.
Figure 4 Monitoring screen of 1# fan and water pump of central air conditioner in the gene department
The user needs to monitor the voltage, current and frequency of 19 water pump fans. Therefore, three groups of numerical display areas are set for them respectively to display the voltage, current and frequency values, which is achieved by using the numerical display function in the component. After the system is started, the 19 inverters periodically reply their working status to the PLC, and send them to the human-machine interface after being processed by the PLC, so that the human-machine interface can display these three groups of values in real time. The format, number of digits and precision of the value are set in the attribute box of the numerical display according to the actual situation.
3. System control method
This system requires remote monitoring of 19 inverters distributed in different departments and far away. It can automatically/manually set, modify and write frequency values and start and stop each inverter on the human-machine interface of the central monitoring room. It can monitor the actual working voltage, current and frequency of the central air conditioner water pump fan motor in real time, and has functions such as sound and light alarm. The specific control method is: use a DVP-PLC, a human-machine interface PWS-3760 and 19 VFD-P series inverters to form a real-time communication network through RS-485 serial communication (as shown in Figure 3), set the communication parameters of the 19 inverters on site, such as the control method is RS-485 communication instructions, communication address: 1-19, baud rate is 9600, communication data format, etc.; design the system PLC program, and the program flow chart is shown in Figure 5. Manual control is required to have the functions of instant setting, modification and writing frequency values and starting and stopping each inverter. Automatic control adopts two time period control, and two time period values and corresponding two frequency values can be set at any time. The current time period value is 1: 7:30 corresponding to frequency 1 45HZ, and the time period value 2: 23:00 corresponding to frequency 2 35HZ. The program design refers to the VFD-P inverter communication protocol, and some RS-485 communication instructions between PLC and inverter are used to realize remote monitoring of the system, and the report can also be printed through the printer.
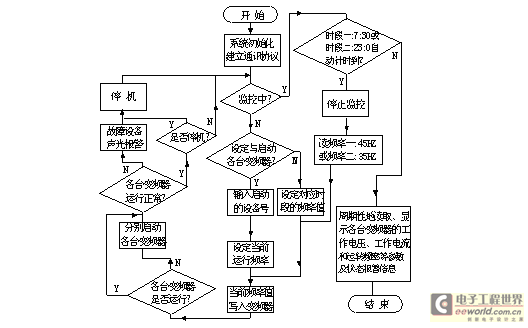
Figure 5 System Program Flowchart
V. Conclusion
The use of AC variable frequency speed regulators to carry out energy-saving transformation of the water pumps and fans of the central air-conditioning system is not only simple and convenient to operate, saves electricity and reduces production costs, but also greatly improves the operating conditions of the water pumps and fans, and reduces the maintenance of water pumps, fans, valves, etc. Since the commissioning of this variable frequency transformation project and monitoring system in May 2002, it has been in continuous operation for more than two years. The system operates reliably and stably, and the communication data is accurate and timely, which standardizes the equipment management and improves the work efficiency. The amount that needs to be changed online is the set value of the time period and frequency. The human-machine interface is used as a human-machine interaction tool, which is simple, intuitive and easy to operate. PLC is used as the central processing unit. The two are used in combination in the variable frequency monitoring system to realize the system's remote monitoring, manual instant frequency conversion and automatic time-sharing frequency conversion functions. Good results have been achieved in actual use and are worth promoting to other industries.
Previous article:Research on Photovoltaic Water Pump Inverter Based on dsPIC30F2010 Digital Signal Controller (DSC)
Next article:Energy saving analysis of frequency conversion and soft start
- Popular Resources
- Popular amplifiers
- Molex leverages SAP solutions to drive smart supply chain collaboration
- Pickering Launches New Future-Proof PXIe Single-Slot Controller for High-Performance Test and Measurement Applications
- CGD and Qorvo to jointly revolutionize motor control solutions
- Advanced gameplay, Harting takes your PCB board connection to a new level!
- Nidec Intelligent Motion is the first to launch an electric clutch ECU for two-wheeled vehicles
- Bosch and Tsinghua University renew cooperation agreement on artificial intelligence research to jointly promote the development of artificial intelligence in the industrial field
- GigaDevice unveils new MCU products, deeply unlocking industrial application scenarios with diversified products and solutions
- Advantech: Investing in Edge AI Innovation to Drive an Intelligent Future
- CGD and QORVO will revolutionize motor control solutions
- Innolux's intelligent steer-by-wire solution makes cars smarter and safer
- 8051 MCU - Parity Check
- How to efficiently balance the sensitivity of tactile sensing interfaces
- What should I do if the servo motor shakes? What causes the servo motor to shake quickly?
- 【Brushless Motor】Analysis of three-phase BLDC motor and sharing of two popular development boards
- Midea Industrial Technology's subsidiaries Clou Electronics and Hekang New Energy jointly appeared at the Munich Battery Energy Storage Exhibition and Solar Energy Exhibition
- Guoxin Sichen | Application of ferroelectric memory PB85RS2MC in power battery management, with a capacity of 2M
- Analysis of common faults of frequency converter
- In a head-on competition with Qualcomm, what kind of cockpit products has Intel come up with?
- Dalian Rongke's all-vanadium liquid flow battery energy storage equipment industrialization project has entered the sprint stage before production
- Allegro MicroSystems Introduces Advanced Magnetic and Inductive Position Sensing Solutions at Electronica 2024
- Car key in the left hand, liveness detection radar in the right hand, UWB is imperative for cars!
- After a decade of rapid development, domestic CIS has entered the market
- Aegis Dagger Battery + Thor EM-i Super Hybrid, Geely New Energy has thrown out two "king bombs"
- A brief discussion on functional safety - fault, error, and failure
- In the smart car 2.0 cycle, these core industry chains are facing major opportunities!
- The United States and Japan are developing new batteries. CATL faces challenges? How should China's new energy battery industry respond?
- Murata launches high-precision 6-axis inertial sensor for automobiles
- Ford patents pre-charge alarm to help save costs and respond to emergencies
- New real-time microcontroller system from Texas Instruments enables smarter processing in automotive and industrial applications
- [Project source code] Design and implementation of traffic lights based on FPGA
- Detailed explanation of comprehensive knowledge of PCB design and wiring using Bluetooth speakers as an example
- [National Technology N32G457 Review] MP3 voice module based on serial communication and serial screen control
- ON Semiconductor RSL10 Bluetooth Development Board Experience
- 【GD32L233C-START Review】7. PWM LED Driver
- [Original] I recently heard that ST's chips have started to increase in price. So can domestic chips rise through this opportunity?
- Free review: Domestic RISC-V Linux board Fang Xingguang VisionFive
- How to configure DM368 to make the output image horizontally mirrored when using sensor image acquisition
- Chat: How does your company control technical documents?
- [ModelSim FAQ] Can't launch the ModelSim-Altera software