1 Introduction
Profibus is an international, open, manufacturer-independent fieldbus standard, widely used in the field of industrial automation. Profibus is divided into three compatible versions according to application characteristics: Profibus-DP, Profibus-FMS, and Profibus-PA. Among them, Profibus-DP is a high-speed (data transmission rate 9.6kbit/s-12Mbit/s) economical device-level network, mainly used for communication between field controllers and distributed I/O, and can meet the time requirements of fast response of AC and DC speed regulation systems. Due to its high reliability, high performance, good real-time performance and unique design, it has been accepted by almost all manufacturers and users.
Servo motors have excellent characteristics such as compact structure, easy control, stable operation, and fast response, and have become an increasingly important force in modern industrial automation motion control. Especially in applications with a relatively high degree of automation and the need for precise control of speed, position, torque, etc., such as textile machinery, printing machinery, papermaking machinery, CNC machine tools, industrial robots and other important industries, they have been widely used. Although PROFIBUS-DP is not developed specifically for motion control like SERCOS, MACRO, and Fire Wire, in actual control, due to the widespread existence of PROFIBUS-DP, the use of PROFIBUS bus to control servos has very important practical significance.
2 PROFIBUS-DP Bus Technology
2.1 Introduction to PROFIBUS-DP
PROFIBUS is based on ISO7498 and uses the open system interconnection network OSI (open system interconnection) as a reference model to define physical transmission characteristics, bus access protocols and application functions. Its transmission rate is 9.6kbps-12Mbps, and the maximum transmission distance is 100m at 12Mbps and 400m at 1.5Mbps, which can be extended to 10km with a repeater. Up to 127 stations can be connected. PROFIBUS-DP is a high-speed and inexpensive communication connection that uses Layer 1, Layer 2 (i.e., physical layer and data link layer) and user interface layer. Layers 3 to 7 are not described. This fluid structure ensures fast and effective data transmission. It is specially designed for communication between automatic control systems and distributed I/O of equipment. The use of PROFIBUS-DP modules can replace 24V or 4-20mA serial signal transmission and reduce investment costs. The user interface provided by Direct Data Link Mapping (DDLM) makes access to the data link layer simple and convenient. Transmission can use RS-485 transmission technology or fiber optic media.
The hardware of the standard fieldbus PROFIBUS-DP consists of three parts: master device, slave device, and network. The master device is used to control data transmission on the bus, and sends information and is authorized to access the bus when no external request is provided. The slave device is a relatively simple external device relative to the master device, and is not authorized to access the bus; the network is such as the transmission medium and the network linker. The former is an electrical network composed of shielded twisted pair cables, an optical fiber network composed of plastic or glass fiber cables, or a hybrid network based on OLM conversion between the two media; the latter is such as RS-485 bus connectors, RS-485 bus terminals, RS-485 repeaters, optical link modules OLM, etc.
2.2 PROFIBUS-DP communication protocol and characteristics
The PROFIBUS-DP physical layer is the same as the first layer of the ISO/OSI reference model and adopts the EIA-RS485 protocol. Depending on the data transmission rate, two transmission media, twisted pair and optical fiber, can be selected.
Figure 1 RS485 bus segment structure diagram
The two data lines in Figure 1 are usually referred to as line A and line B, corresponding to RXD/TXD-N and RXD/TXD-P signals respectively.
The media access control (MAL) part of the PROFIBUS-DP data link layer adopts a controlled access token bus and a master-slave mode. The token bus is consistent with the IEEE8024 protocol for the local area network. The token is passed between the master stations on the bus . The master station holding the token obtains the bus control right. The master station communicates with the slave station or other master stations according to the relationship table. The master-slave data link protocol is different from the local area network standard. It conforms to the non-balanced normal response mode (NRM) in HDLC. The working characteristics of this mode are: a master station on the bus controls multiple slave stations, and the master station establishes a logical link with each slave station; the master station issues a command (Command), and the slave station responds (Respond); the slave station can send multiple frames continuously until there is no information to send, the number of transmissions is reached, or it is stopped by the master station. The transmission process of frames in the data link is divided into three stages: data link establishment, frame transmission, and data link release.
In Figure 2, F is the frame flag field (8 bits). A is the slave address field. The control field C indicates the frame type, number, command and control information. It divides the HDLC frame into three types: information frame (1), monitoring frame (S) and unnumbered frame (U). The information frame is used to transmit application data (Useful Data) and carry responses; the monitoring frame is used to monitor the normal operation on the link and make various responses to the link status (such as acknowledgment frame, request retransmission or pause, etc.); the unnumbered frame (without information field) is used to transmit various meta-numbered commands and responses, such as establishing link working mode, releasing the link and reporting special situations. The information field is composed of PKW+PZD application data. PKW is used to read and write parameter values, such as writing control words or reading status words, etc., and is generally 4B long, while PZD is used to store specific control values of the controller and set the parameters of the station or status word, and is generally 2 to 10B long. For example, PKW=P554.1 means writing a 16-bit control word to the main drive module of the inverter. Each bit of the control word represents a different control meaning. The second byte of PZD is the start and stop control bit of motors 0#~7#. FCS is the frame check field, which performs a cyclic redundancy code (CRC) check on the content of the entire frame. The HDLC frame can be up to 24B in length.
Figure 2 Format of the frame transmitted between the master and slave in normal response mode
3 Servo motor connected to PROFIBUS-DP network
Schneider's TWINLINE servo control system has a dedicated PROFIBUS-DP bus interface module in its controller. Like other PROFIBUS-DP, it can use ordinary twisted pair as the communication medium and can be easily connected to the industrial control system based on the PROFIBUS-DP bus, as shown in Figure 3.
The host computer is composed of Siemens S7-300PLC, model 6ES7315-2AG10-0AB0, which has a dedicated PROFIBUS-DP interface and an MPI communication interface, which can access 64 slave stations. The PROFIBUS-DP bus is responsible for managing all servo controllers in the entire system, including the command transmission and setting of parameters such as speed, torque, position, etc. As a window, the human-machine interface woven by the configuration software ProTool can easily monitor the entire control system and modify parameters.
TWINLINE's servo controller and servo motor use rotary encoders or photoelectric encoders to establish feedback, forming a high-precision servo control system. The servo motor uploads its operating status and information to the servo controller in real time. As a node on the PROFIBUS-DP bus, the servo controller can communicate with the PLC host and receive various operations, controls and parameter setting commands from the host computer through the bus.
Figure 3 Schematic diagram of the servo motor connected to the PROFIBUS-DP network system
4 Software Structure Design
The servo system that communicates and controls via the PROFIBUS-DP bus mainly solves the software design problem of the upper host. The following is the main design block diagram of the PLC program
Figure 4 PLC program design block diagram
The PLC program is programmed by STEP 7. The program mainly consists of several parts: OB100, OB1 and FB40.
OB100 is a warm start organization block. When the system starts, OB100 is called. It includes function FC35, namely INIT_FIELDBUS. Its main function is to initialize the opened background data block and set the input/output bus address for the servo controller.
OB1 is the main program organization block, including function FC32, function block FB40, function FC37 and background data block DB40. FC32 is CYCL_UPDATE, and its function is to regularly read and update the data from the background data block on the bus. Function block FB40 is the main program block for controlling the servo controller, which will complete the initialization and position control of the servo controller, mainly including function FC40 and function FC41. FC40 is INIT_SERVO, which mainly completes the initialization of multiple axes, that is, the initialization of multiple servo controllers. FC41 is POS_SEQ_SERVO, which is the core part of the entire servo control. Some control commands such as speed command, position command, torque command, origin return command and reading the feedback value of the servo controller from the bus are all completed by it. FC37 is FAULT_RESET, which is a reset module, clears the error information of the bus and generates a reset command to reset the servo controller. DB40 is the background data block of function block FB40.
FC30 is a sub-block of FC40, which completes the command transmission from PLC to servo controller, checks whether the command is executed correctly and handles the error. FC31 is a sub-block of FC41, which diagnoses the completion of FC41 and reports to the bus. FC33 and FC34 are also subsidiary parts of function block FB40. FC33 checks the status of the current servo controller. If it is idle, it sends a command to the bus to indicate that the next command can be sent. FC34 handles the synchronous and asynchronous error information of multiple servo controllers and generates error reports.
5 Conclusion
The introduction of the PROFIBUS-DP interface of the TWINLINE servo controller has improved the level of industrial automation motion control and made the communication and control of servo motors in industrial control networks more convenient, flexible and reliable. The actual situation has proved that this control method is effective.
PROFIBUS-DP bus and servo control system are widely used in industrial control, which provides broad application prospects for servo controllers with PROFIBUS-DP bus interface.
Previous article:Design and Application of Distributed System Based on CPCI Bus
Next article:Research on Networked Motion Control System Based on CAN Bus
Recommended ReadingLatest update time:2024-11-16 23:47
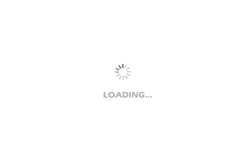
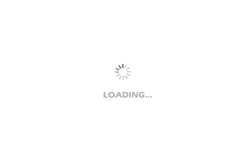
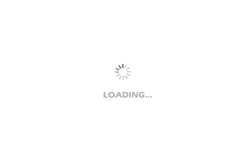
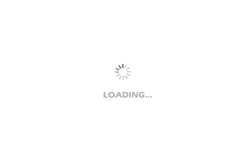
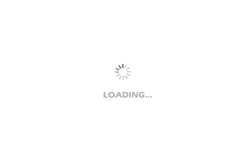
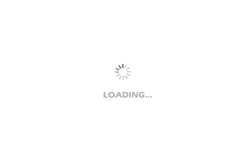
- Popular Resources
- Popular amplifiers
- Molex leverages SAP solutions to drive smart supply chain collaboration
- Pickering Launches New Future-Proof PXIe Single-Slot Controller for High-Performance Test and Measurement Applications
- CGD and Qorvo to jointly revolutionize motor control solutions
- Advanced gameplay, Harting takes your PCB board connection to a new level!
- Nidec Intelligent Motion is the first to launch an electric clutch ECU for two-wheeled vehicles
- Bosch and Tsinghua University renew cooperation agreement on artificial intelligence research to jointly promote the development of artificial intelligence in the industrial field
- GigaDevice unveils new MCU products, deeply unlocking industrial application scenarios with diversified products and solutions
- Advantech: Investing in Edge AI Innovation to Drive an Intelligent Future
- CGD and QORVO will revolutionize motor control solutions
- Innolux's intelligent steer-by-wire solution makes cars smarter and safer
- 8051 MCU - Parity Check
- How to efficiently balance the sensitivity of tactile sensing interfaces
- What should I do if the servo motor shakes? What causes the servo motor to shake quickly?
- 【Brushless Motor】Analysis of three-phase BLDC motor and sharing of two popular development boards
- Midea Industrial Technology's subsidiaries Clou Electronics and Hekang New Energy jointly appeared at the Munich Battery Energy Storage Exhibition and Solar Energy Exhibition
- Guoxin Sichen | Application of ferroelectric memory PB85RS2MC in power battery management, with a capacity of 2M
- Analysis of common faults of frequency converter
- In a head-on competition with Qualcomm, what kind of cockpit products has Intel come up with?
- Dalian Rongke's all-vanadium liquid flow battery energy storage equipment industrialization project has entered the sprint stage before production
- Allegro MicroSystems Introduces Advanced Magnetic and Inductive Position Sensing Solutions at Electronica 2024
- Car key in the left hand, liveness detection radar in the right hand, UWB is imperative for cars!
- After a decade of rapid development, domestic CIS has entered the market
- Aegis Dagger Battery + Thor EM-i Super Hybrid, Geely New Energy has thrown out two "king bombs"
- A brief discussion on functional safety - fault, error, and failure
- In the smart car 2.0 cycle, these core industry chains are facing major opportunities!
- The United States and Japan are developing new batteries. CATL faces challenges? How should China's new energy battery industry respond?
- Murata launches high-precision 6-axis inertial sensor for automobiles
- Ford patents pre-charge alarm to help save costs and respond to emergencies
- New real-time microcontroller system from Texas Instruments enables smarter processing in automotive and industrial applications
- Even if we give the complete set of drawings, Chinese people still cannot build high-end lithography machines?
- aos multithreading and mutex lock
- The biggest company in the Metaverse is also laying off employees. It is said to be bigger than Twitter.
- How to improve the frequency accuracy of the resonant circuit?
- [FS-IR02 + D1CS-D54] - 3: Electrical performance index detection (D1CS-D54)
- RF application scenarios——Q value
- Evaluate the TMDSCNCD280025C + TMDS HSECDOCK Kit for Free
- What is the function of the microcontroller's dead loop?
- Interactive Magnetic Fluid Project
- [Anxinke UWB indoor positioning module NodeMCU-BU01] No.001-unboxing test