1. Use digital and networked temperature sensors to achieve online monitoring of cable trenches
1. Why should we monitor the cable trench online?
Cables can be seen everywhere in daily production and life. In electric fields, factories, and laboratories, a large number of cables are usually concentrated in cable trenches for easy wiring, maintenance, and aesthetics. As people's dependence on electricity grows, there are more and more cables in cable trenches, and the probability of fire accidents increases accordingly.
Take the electric field as an example. With the increase of unit capacity, the automation level is improved accordingly, and the amount of cables used is increasing. For a 200MW unit, various cables are up to 200-300km long. In the first phase of a power plant project, two 500MW supercritical units were used, and the amount of cables used was 3000km.
Once a cable fire occurs in a thermal power plant, it will cause serious losses. Currently, most thermal power plants under construction and operation still use flammable cables, so the problem of cable fire prevention is particularly prominent.
According to relevant statistics, in my country, there have been more than 140 cable fires in thermal power plants in the past 20 years, with a total of 75 in the seven years from 1986 to 1992. 24 power plants have experienced two or more cable fire accidents, and some power plants have experienced 4 to 6. More than 70% of cable fires caused very serious losses, of which 2/5 of the fire accidents caused extremely large losses. Between 1975 and 1985, 60 major accidents caused by cable fires occurred, causing direct and indirect losses of more than 5 billion yuan. The equipment and repair costs of the Shentou Power Plant in Shanxi Province exceeded 10 million yuan due to the cable trench fire. In 1999, the Mudanjiang Second Power Plant suffered a power outage due to a cable trench fire, resulting in direct and indirect losses of nearly 10 million yuan. In addition to power plants, there are also fire hazards in the cable trenches of machine rooms and workshops of large factories, mines, and scientific research institutions. In 2000, the monitoring room of the electron-positron collider at the Beijing Institute of High Energy Physics was forced to shut down due to a fire in a cable trench, seriously affecting the progress of scientific research.
Of the 3,285 electrical fire accidents recorded in the United States from 1965 to 1975, wire and cable fire accidents accounted for 30.5%, with direct losses of approximately $40 million.
Japan once conducted a survey on factories and enterprises such as electricity, steel, petrochemicals, and papermaking, and found that 78% of the units had experienced cable fires, of which 40% were serious accidents.
Through the analysis of electric field accidents, the direct cause of the fire in the wire trench is the aging and oxidation of the middle cable head due to long-term operation, the increasing contact resistance, the overheating of the cable head and the burning through of the insulation, which finally leads to the fire in the cable trench.
Example 1: A fire occurred in Liaoning Power Plant due to overheating of cable heads. When the firefighters were about to leave the scene after extinguishing the fire, the insulation of the cable heads broke down, and the fire reignited, burning several people on the spot and causing mass injuries.
Example 2: Fulaerji Power Plant, when the test personnel were looking for cable faults, they used the capacitor breakdown method in the morning to find them. After the lunch break, a fire broke out in the cable trench, causing a major accident. The accident could have been completely avoided if a cable online monitoring system was configured.
Example 3: The middle head of the #2 circulating water cable at Hunjiang Power Plant overheated and burned all the cables in the trench, causing a forced shutdown. It was learned that someone smelled the smell of burnt insulation in the shaft more than 80 meters away from the middle head of the faulty cable in the morning, and a fire broke out at seven o'clock in the afternoon.
Example 4: On June 28, 1998, at Mudanjiang No. 2 Power Plant, an overheated middle head of the circulating water cable of one unit ignited all the cables in the cable trench, forcing all seven units (with an installed capacity of 1.03 million kilowatts) to shut down and causing a power outage throughout the plant.
Example 5: In 2001, a fire broke out in a cable tunnel at the Shanghai Power Supply Bureau due to overheating of the middle cable head. A large area of cables was burned, resulting in a large-scale power outage in the city.
In summary, the main cause of fire in cable trench is the heating of the middle head of the power cable. According to the analysis of many accidents, it is found that the development speed from overheating of the cable head to the occurrence of the accident is relatively slow and takes a long time. The cable online monitoring system can completely prevent and eliminate the occurrence of such accidents.
Jilin Thermal Power Plant summed up this experience many years ago. It used manual inspections of the temperature of the middle head of the cable every day. It analyzed its operating conditions based on the temperature changes. It consumed a lot of manpower, but it avoided many accidents. Therefore, the cable trench online monitoring system is of great significance to the safe operation of the power plant. Although most power plants have already carried out fireproof sealing and ordinary fire alarm devices in cable trenches at a great cost, wire trench fires still occur. These measures can only reduce the scope of accidents after the wires catch fire. There is no fundamental restriction on the occurrence of fires. Online monitoring of cable trenches is an effective and feasible way to fundamentally limit the occurrence of fires in cable trenches.
2. Why are traditional analog temperature sensors not suitable for cable trench temperature measurement?
The structure of a traditional temperature test system is usually:
The temperature value of each sensor must go through the above links to enter the system. Therefore, there are the following shortcomings:
a) Hundreds or thousands of signal lines are required (a cable trench usually has 200 to 300 temperature measurement points)
b) Analog voltage signals are easily lost during transmission, affecting system accuracy, and the transmission distance is relatively short.
c) The system has many links and is difficult to maintain. The system accuracy is easily affected by the environment and is difficult to guarantee.
d) Expensive. 200~300 points requires 100,000~200,000
3. The application of new technologies makes the system more convenient
With the development of science and technology, digital and networked sensors have become the trend of technology and the mainstream of the market. The DS18B20 digital and networked temperature sensor of DALLAS Company in the United States adopts a unique idea and successfully solves the contradiction between digitalization, networking and cost. It makes it possible to establish a monitoring system that is easy to use, economical and reliable.
The LTM-8000 digital temperature and humidity environment monitoring system adopts the advanced chip technology of the American DALLAS company, combines the on-site conditions in China, and applies the technology of intelligent field bus. Only digital signals are transmitted in the whole system, and sensors and acquisition modules can be connected to the network, making the system more reliable and wiring more convenient.
Key features of a system based on digital, networked sensors:
a) Fewer cables. Sensors can be connected in series through the bus. Dozens of sensors only need one 3-core wire. This greatly reduces the number of cables on site and facilitates on-site wiring.
b) Since the sensor outputs a digital signal, there is no loss of accuracy during the transmission process and the system accuracy can be guaranteed.
c) The system has fewer links, and the output from the sensor goes directly into the collector. The system has fewer links where failures may occur and is easy to maintain.
d) The use of advanced chip technology, unique concepts, and large-scale production has greatly reduced system costs and improved reliability.
Changying Technology's LTM-8000 digital temperature and humidity environment monitoring system has been successfully applied in many fields such as power systems, petroleum, and steel. For example:
Cable trench temperature online monitoring and fire warning
Online temperature monitoring of high voltage switchgear
Online monitoring of motor and its junction box temperature
Online monitoring of bearing temperature of pumps and fans
Storage (grain silos, cold storage, oil tanks) monitoring
Air conditioning and building automation
4. System Introduction
The system configuration is divided into the following parts:
1) Host computer:
Function: Data processing and user interface
Hardware requirements: Pentium 133/32MDRAM/4.3G or above compatible computer or industrial computer.
Software: Configuration software or custom program available
2) RS232/485 communication converter LTM-8520E, with overvoltage, overcurrent, surge, isolation, and lightning protection
3) Field acquisition module LTM-8003E
Function: To achieve communication between two levels of communication networks. One level is the RS-485 network of the host computer, and the LTM-8003 module is used as a substation; the other level is the "one-line bus", and the LTM-8003 module is used as the acquisition center, and the digital sensor on the measurement cable is used as a substation.
Hardware functions: with overvoltage, overcurrent, surge, isolation, and lightning protection
4) Temperature sensor DS18B20
5. Introduction to the digital and networked temperature sensor DS18B20
The digital temperature sensor DS1820 from Dallas Semiconductor is the world's first temperature sensor that supports the "one-wire bus" interface. The unique and economical features of the one-wire bus allow users to easily build a sensor network, introducing a new concept for the construction of measurement systems. The new generation DS18B20 is smaller, more economical, and more flexible.
DS18B20, the measurement temperature range is -55°C~+125°C, the accuracy is ±0.5°C in the range of -10~+85°C, and the resolution is 0.0625. The field temperature is directly transmitted in a digital way of "one-line bus", and each one has its own address, which greatly reduces the number of cables in the system and improves the stability and anti-interference of the system. Corresponding to the traditional concept, this transistor-like sensor is equivalent to the traditional: temperature sensor + digitalization + CPU + bus protocol and interface.
2. Introduction to Digital and Networked Humidity Sensors
The American DALLAS "one-line bus" temperature sensor DS18X20 has been well received by customers for its simple hardware interface and stable performance. Changying Technology has also developed a series of products to meet the different needs of customers. However, it was also found in the application that its communication protocol is relatively complex and not very convenient to use. In addition, the needs on site are diverse, and DALLAS's product range seems insufficient. After all, DALLAS is just a device manufacturer, and there is still a gap between its products and the needs of actual applications.
Changying Technology has developed the LTM8901 digital and networked humidity sensor based on customer needs, combined with years of application experience, and adopted new chip technology to make up for the shortcomings of the DALLAS system while retaining its advantages as much as possible.
1. Disadvantages of traditional humidity sensors
Traditional humidity sensors are basically divided into resistive and capacitive types. Then they are connected to the collector through a transmitter in voltage or current mode, so:
a) The sensor has poor interchangeability. For example, Honeywell 3605L has a correction table for each sensor, so that users can make corrections according to the table. It is very inconvenient to interchange.
b) Analog voltage signals are easily lost during transmission, affecting system accuracy, and the transmission distance is relatively short.
c) The transmitter generally requires additional power supply, and the power supply accuracy is required to be high, otherwise it will affect the system accuracy.
d) The system has many links and is difficult to maintain. The system accuracy is easily affected by the environment and is difficult to guarantee.
e) The accuracy is difficult to calibrate, so sensors with slightly better accuracy are expensive. The famous VISSALA sensor with 3% accuracy costs thousands of yuan each.
f) There are at least two wires from each sensor to the transmitter, and from the transmitter to the collector. Wiring in a multi-point system is very difficult.
2. Features of the digital and networked humidity sensor LTM8901
a) Good interchangeability: due to the use of intelligent correction technology, the sensors can be interchanged at will.
b) Since the sensor outputs digital signals, there is no loss of accuracy during the transmission process, and the system accuracy can be guaranteed. In addition, the transmission distance is short.
c) It adopts low power consumption design and is powered by the collector, so no additional power supply is required.
d) The system has fewer links, and the data goes directly from the sensor to the collector. The system has fewer links where failures may occur and is easy to maintain.
e) The use of intelligent correction technology, unique concepts, and large-scale production has greatly reduced costs and improved reliability.
f) Fewer cables. Sensors can be connected in series through the bus. A dozen sensors only need one 3-core cable. This greatly reduces the number of cables on site and facilitates on-site wiring.
3. Introduction to the digital and networked humidity sensor LTM8901
a) LTM8901 application wiring interface The host computer CPU only needs to have a bidirectional I/O pin, and can communicate with LTM8901 by connecting according to the following circuit. The I/O pin of the MCU is required to be an OC gate output (or tri-state output) and have input function. Most MCU I/O pins now have this function.
b) LTM8901 Typical Characteristics
Operating temperature range: -25℃~+85℃
Humidity measurement resolution: 0.5% RH
Humidity measurement range: 1%~99%RH
Humidity measurement accuracy: ±3.0%RH (typical value)
Hysteresis: ±2.0%RH (typical)
Annual drift: ±0.5%RH (typical)
Response time: 5s (typical)
Working voltage range: 4.5~5.5V
Dimensions: 70×50×25mm3
3. Introduction to the structure of digital and networked sensor application system
1. Digital and networked sensor application system structure Usually the application system consists of three levels of network:
a) Sensor network, which consists of various sensors and is distributed within a range of 200 to 300 meters.
b) Fieldbus network, composed of various bus collectors, such as LTM8000 series temperature and humidity collection module, distributed in the range of 1000 to 2000 meters.
c) Local area network and wide area network, usually composed of various PCs and workstations, can achieve remote monitoring and control through the INTERNET.
2. Digital and networked sensor application system structure and application diagram
4. Introduction to other digital and networked sensors and related products and applications
1. Application of digital and networked counter DS2423: multi-meter household solution
Features: Only one 3-core wire is needed to transmit the data of water, electricity, gas and other meters to the unit collector.
Each unit is designed as a single chip, which is cheaper than the traditional RS485 networking method and has simpler wiring than the traditional pulse out-of-home method.
2. Application of digital and networked smoke alarms: fire monitoring
Features: Use power lines to transmit alarm signals, and multiple sensors only need two lines to connect into a network.
3. Information button DS1991
Applications: Prepaid water meters, electricity meters, parking management systems, access control systems, patrol systems
Features: It uses the same network protocol as digital and networked sensors and can be easily integrated with the community intelligent system.
Previous article:Design of high-precision digital pressure transmitter based on CAN bus
Next article:A biped walking robot based on neural network sensor
Recommended ReadingLatest update time:2024-11-16 16:55
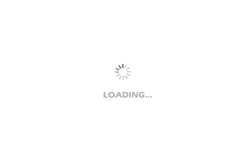
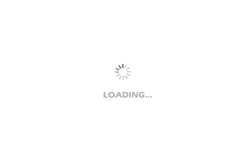
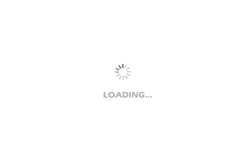
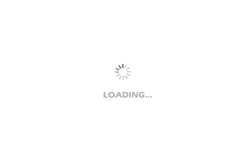
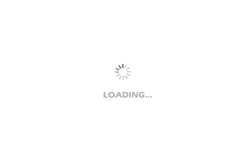
- Popular Resources
- Popular amplifiers
-
Analysis and Implementation of MAC Protocol for Wireless Sensor Networks (by Yang Zhijun, Xie Xianjie, and Ding Hongwei)
-
Introduction to Internet of Things Engineering 2nd Edition (Gongyi Wu)
-
西门子S7-12001500 PLC SCL语言编程从入门到精通 (北岛李工)
-
Modern Motor Control Technology (Wang Chengyuan, Xia Jiakuan, Sun Yibiao)
- Molex leverages SAP solutions to drive smart supply chain collaboration
- Pickering Launches New Future-Proof PXIe Single-Slot Controller for High-Performance Test and Measurement Applications
- CGD and Qorvo to jointly revolutionize motor control solutions
- Advanced gameplay, Harting takes your PCB board connection to a new level!
- Nidec Intelligent Motion is the first to launch an electric clutch ECU for two-wheeled vehicles
- Bosch and Tsinghua University renew cooperation agreement on artificial intelligence research to jointly promote the development of artificial intelligence in the industrial field
- GigaDevice unveils new MCU products, deeply unlocking industrial application scenarios with diversified products and solutions
- Advantech: Investing in Edge AI Innovation to Drive an Intelligent Future
- CGD and QORVO will revolutionize motor control solutions
- Innolux's intelligent steer-by-wire solution makes cars smarter and safer
- 8051 MCU - Parity Check
- How to efficiently balance the sensitivity of tactile sensing interfaces
- What should I do if the servo motor shakes? What causes the servo motor to shake quickly?
- 【Brushless Motor】Analysis of three-phase BLDC motor and sharing of two popular development boards
- Midea Industrial Technology's subsidiaries Clou Electronics and Hekang New Energy jointly appeared at the Munich Battery Energy Storage Exhibition and Solar Energy Exhibition
- Guoxin Sichen | Application of ferroelectric memory PB85RS2MC in power battery management, with a capacity of 2M
- Analysis of common faults of frequency converter
- In a head-on competition with Qualcomm, what kind of cockpit products has Intel come up with?
- Dalian Rongke's all-vanadium liquid flow battery energy storage equipment industrialization project has entered the sprint stage before production
- Allegro MicroSystems Introduces Advanced Magnetic and Inductive Position Sensing Solutions at Electronica 2024
- Car key in the left hand, liveness detection radar in the right hand, UWB is imperative for cars!
- After a decade of rapid development, domestic CIS has entered the market
- Aegis Dagger Battery + Thor EM-i Super Hybrid, Geely New Energy has thrown out two "king bombs"
- A brief discussion on functional safety - fault, error, and failure
- In the smart car 2.0 cycle, these core industry chains are facing major opportunities!
- The United States and Japan are developing new batteries. CATL faces challenges? How should China's new energy battery industry respond?
- Murata launches high-precision 6-axis inertial sensor for automobiles
- Ford patents pre-charge alarm to help save costs and respond to emergencies
- New real-time microcontroller system from Texas Instruments enables smarter processing in automotive and industrial applications
- "【TGF4042 Signal Generator】" Narrow pulse signal output measurement
- That green PCB board is tested with these 7 methods
- MSP430F2001IPW
- Analysis of ST MCU Model Rules
- Xunwei IMX6ULL development board builds a web server
- Where exactly is China leading in 5G?
- Audi car engine regularly stops and cannot start. Oscilloscope detection solution
- FPGA design ideas and techniques: data interface synchronization
- After __wfi is run, is the MCU still running the code?
- CC2640 Questions and Answers