July 27, 2022, Shanghai – Mobile Industrial Robots (MiR), a global leader in the mobile robot market, today released the e-book "Internal Logistics Automation in the Electronics Industry" (click the link to download the report), focusing on the trends and cutting-edge cases of internal logistics automation in the electronics industry, sharing how autonomous mobile robots (AMR – Autonomous Mobile Robot) can help the electronics manufacturing industry reduce costs and increase efficiency, and continuously improve profit margins. It also proposes that promoting the large-scale deployment of AMR in the electronics field requires focusing on three key points: software, ecology, and total cost of ownership.
MiR analysis points out that since 2020, the electronics manufacturing industry has surpassed the automotive manufacturing industry to become the largest application industry for industrial robots. From transporting components and goods, to palletizing finished products, to cutting metal casings, assembling micro components and performing quality inspections with collaborative robots, industrial autonomous mobile robots have been used throughout the entire value chain and production cycle of the electronics manufacturing industry, and the automation of internal factory logistics is a crucial part of this.
In order to seize development opportunities, the electronics industry hopes to efficiently meet market demand through automation, while also hoping to continuously reduce costs and ultimately achieve tangible profit margin growth. According to data from the Ministry of Industry and Information Technology, in 2021, the operating income profit margin of my country's electronic information manufacturing industry above designated size was 5.9%, which is still 0.9 percentage points lower than the operating income profit margin of industrial enterprises above designated size. The electronics manufacturing industry still needs to continue to tackle key issues in improving profit margins. On the one hand, it depends on the industry itself to move towards the high end of the industrial value chain, and on the other hand, it depends on automation to achieve lean management of production processes, reduce costs and increase efficiency.
Zhang Yu, Sales Director of MiR China, said: "The electronics manufacturing industry is thriving and has started large-scale deployment of industrial mobile robots. MiR has accumulated rich experience in a large number of sub-sectors and scenarios in the electronics industry. Our AMRs have been deployed in the entire electronics manufacturing industry chain, including upstream material and equipment manufacturing, midstream module manufacturing, and downstream branded complete machines. Therefore, we are very familiar with the pain points of the electronics industry and hope to contribute our strength to help the industry further lean production, reduce costs and increase efficiency."
The electronics manufacturing industry has a great demand for efficiency improvement and many pain points
First of all, in terms of production efficiency, the demand of the electronic market in the digital age is becoming increasingly refined, fragmented, and diversified, and users are increasingly demanding delivery cycles. Under the C2B model, the needs of end users force companies to "determine production based on demand" and respond to market demand in an agile manner. The traditional manpower model cannot adapt to the fast pace of flexible production. Companies must carry out a full range of automation upgrades to factory systems. Equipment must be able to efficiently adapt to various usage scenarios, facilitate flexible switching of production line tasks, and be easily connected to the factory's existing ERP, WMS and other management systems.
Secondly, in the production process of electronic components, environmental factors such as dust particles, cleanliness, and anti-static need to meet strict standards to prevent electronic components from being contaminated and damaged. Before the use of automated transportation methods, workers often needed to be "fully armed" to enter the dust-free workshop to transport materials and finished products back and forth. This is not only inefficient, but also easy to contaminate the lines and damage the parts if not careful. In addition, the internal structure of electronic products is complex, and the parts are very precise and cannot withstand external impact and bumps. Human transportation will inevitably lead to carelessness and breakage of finished products. These situations will cause additional cost waste.
In addition, the electronics manufacturing industry is a typical labor-intensive industry with heavy production tasks and long-term repetitive labor that is unattractive to talent. This not only pushes up recruitment costs and further squeezes profit margins, but also prevents employees from focusing their precious time on higher-value work. Using automation to replace heavy and trivial non-technical work such as palletizing and handling can help improve employee job satisfaction, thereby retaining talent and enabling talent transformation and upgrading.
To meet the above challenges, many companies hope to use robots to assist manual work. However, traditional AGV robots require laying wires or magnetic strips as "tracks", which limit them to fixed routes. Expanding/changing the work area is expensive and time-consuming. This not only fails to meet the needs of flexible production, but also brings high deployment costs, which makes many companies hesitate.
AMR responds to challenges, large-scale deployment requires three key points
AMR does not require laying tracks, and is easy to expand and change work areas. Employees can easily complete task programming without programming experience. AMR can autonomously navigate, call elevators, open and close doors, charge itself, and drive safely around pedestrians and obstacles. It can pick up and move materials between different production lines, units, warehouses, and floors, and deliver materials to designated locations safely and in a timely manner. With its intelligent, efficient, flexible, convenient, safe and stable features, AMR has been widely used in the electronics manufacturing industry. MiR believes that there are three key points to promote the large-scale deployment of AMR in the electronics industry .
The first is software capability , which is the core of AMR's large-scale deployment. This first refers to the software of the AMR itself. High-quality software can improve the intelligence of the AMR, making it easier for users to issue instructions more quickly, making the robot run safer, more stable, and more accurate. Secondly, as more and more companies form a situation of hundreds of AMR cluster operations, this puts higher requirements on the intelligence and coordination of AMR and dispatching systems, so more excellent AMR fleet management software is needed to support it. MiR Fleet, the fleet management software independently developed by MiR, can manage up to 100 AMRs to work together at the same time and carry out 7x24 hours of multi-site delivery. In addition, the software must also be open and can easily access various communication software, analysis software, and safety monitoring software, and allow AMR to be closely integrated with the existing ERP and WMS systems in the customer's factory.
The second is a rich and open ecosystem . The flexible production trend in the electronics industry places very high demands on the expansibility of AMR functions. MiR AMR brings together various fully and rigorously tested solutions such as frames/shelves, traction devices, lifting devices, conveyor belts, robotic arms, disinfection modules, electric stations, etc. that are continuously developed by partners through the MiRGo platform. Through MiRGo, users can get dozens of out-of-the-box solutions and hundreds of applications to extend the use and functions of AMR. In addition, AMR can also be paired with collaborative robot arms. If the autonomous navigation capability of the AMR driving chassis replaces the walking function of human legs and feet, then the collaborative robot arm replaces the function of human arms. The combination of the two further extends the application scenarios of robots.
Third, it effectively reduces the total cost of ownership for customers and brings cost benefits . In addition to considering the initial cost of purchasing automation technology, companies are increasingly considering the return on investment from the perspective of total cost of ownership, which means taking into account factors such as cost savings from improved safety and man-hours saved due to flexible solutions. MiR AMR has a short deployment time and does not require changes to the physical environment of the production line, so the deployment efficiency is very high and downtime is avoided, which brings excellent cost benefits to the company.
A Korean electronic component manufacturer has deployed two MiR100 autonomous mobile robots in the cleanroom of its Tianjin factory for internal transportation of production materials and finished products. In the past, workers had to wear a full set of cleanroom work clothes and use carts to transport materials through multiple round trips. The flow of personnel puts electronic components at risk of contamination during the production process, and some finished products will be damaged during transportation. In addition, the width of the cargo transportation channel is only 1,800 mm, and there are other automated production equipment on both sides, which undoubtedly increases safety risks.
After the MiR AMR is deployed in the workshop, the staff does not need to touch it directly. Through the MiR Fleet management software, MiR100 can be connected to the internal WMS system of the factory, directly receive commands to complete transportation tasks, and can return to the charging station to charge autonomously. In addition, the staff can easily program the MiR100 and implement "traffic control" in the workshop, dividing the robot into single-line areas, key areas and restricted areas to ensure that MiR100 will not collide in a channel with a width of only 1,800 mm. This not only realizes more efficient, hygienic and safe automated transportation, but also reduces 80% of the internal transportation labor costs, and puts human resources into more valuable positions, thereby effectively helping the factory to achieve lean management and cost reduction and efficiency improvement of internal logistics.
Previous article:Industrial Automation 2.0 Evolution: Self-Aware Motion Control
Next article:Intel's Chen Baoli: Building diversified computing power to strengthen the foundation of the digital economy
Recommended ReadingLatest update time:2024-11-16 14:43
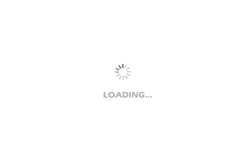
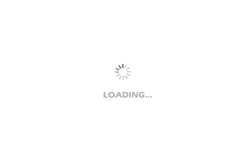
- Molex leverages SAP solutions to drive smart supply chain collaboration
- Pickering Launches New Future-Proof PXIe Single-Slot Controller for High-Performance Test and Measurement Applications
- CGD and Qorvo to jointly revolutionize motor control solutions
- Advanced gameplay, Harting takes your PCB board connection to a new level!
- Nidec Intelligent Motion is the first to launch an electric clutch ECU for two-wheeled vehicles
- Bosch and Tsinghua University renew cooperation agreement on artificial intelligence research to jointly promote the development of artificial intelligence in the industrial field
- GigaDevice unveils new MCU products, deeply unlocking industrial application scenarios with diversified products and solutions
- Advantech: Investing in Edge AI Innovation to Drive an Intelligent Future
- CGD and QORVO will revolutionize motor control solutions
- Innolux's intelligent steer-by-wire solution makes cars smarter and safer
- 8051 MCU - Parity Check
- How to efficiently balance the sensitivity of tactile sensing interfaces
- What should I do if the servo motor shakes? What causes the servo motor to shake quickly?
- 【Brushless Motor】Analysis of three-phase BLDC motor and sharing of two popular development boards
- Midea Industrial Technology's subsidiaries Clou Electronics and Hekang New Energy jointly appeared at the Munich Battery Energy Storage Exhibition and Solar Energy Exhibition
- Guoxin Sichen | Application of ferroelectric memory PB85RS2MC in power battery management, with a capacity of 2M
- Analysis of common faults of frequency converter
- In a head-on competition with Qualcomm, what kind of cockpit products has Intel come up with?
- Dalian Rongke's all-vanadium liquid flow battery energy storage equipment industrialization project has entered the sprint stage before production
- Allegro MicroSystems Introduces Advanced Magnetic and Inductive Position Sensing Solutions at Electronica 2024
- Car key in the left hand, liveness detection radar in the right hand, UWB is imperative for cars!
- After a decade of rapid development, domestic CIS has entered the market
- Aegis Dagger Battery + Thor EM-i Super Hybrid, Geely New Energy has thrown out two "king bombs"
- A brief discussion on functional safety - fault, error, and failure
- In the smart car 2.0 cycle, these core industry chains are facing major opportunities!
- The United States and Japan are developing new batteries. CATL faces challenges? How should China's new energy battery industry respond?
- Murata launches high-precision 6-axis inertial sensor for automobiles
- Ford patents pre-charge alarm to help save costs and respond to emergencies
- New real-time microcontroller system from Texas Instruments enables smarter processing in automotive and industrial applications
- Problems found during PCB rule checking
- Study and use of DSP6678 chip
- Simple and fast design of LC filter
- 【ST NUCLEO-G071RB Review】TIM-PWM
- [NXP Rapid IoT Review] Hello World project reads sensor values that are always 0
- A few questions for help
- MSP430AFE2xx series of metering analog front-end 16-bit MCU
- A brief tutorial on DSP interrupt settings
- Request a free ZVS buck regulator evaluation board
- Is there any chip that can convert analog signal (potentiometer and DC voltage) into PWM dimming signal?