In the previous article , we have introduced the basic principles of temperature sensing. This article will continue this topic and explain the topic of system temperature monitoring.
For many system designs, it is necessary to monitor high-power components (processors, field-programmable gate arrays, field-effect transistors) to ensure system and user safety. Accuracy in temperature readings is important because it enables designers to increase performance while staying within safety limits, or reduce system cost by avoiding over-design elsewhere. Texas Instruments' (TI) portfolio of compact, high-precision temperature sensors can be placed closer to these critical components for the most accurate measurements.
How to Monitor Circuit Board Temperature
Temperature issues in circuits can affect system performance and damage expensive components. Measuring the temperature of areas of a printed circuit board (PCB) where hot spots or high-power integrated circuits (ICs) exist can help identify thermal issues so preventive or corrective action can be taken.
You may want to monitor the die temperature of a power-hungry IC (such as a central processing unit, application-specific IC, field-programmable gate array, or digital signal processor) to dynamically adjust its performance, or you may want to monitor the thermal zone around a power stage to control fan speed in a system or initiate a safe system shutdown procedure. The ultimate goal is to optimize performance and protect expensive equipment.
Heat transfer from PCB to temperature sensor
Local temperature sensors measure their own die temperature to determine the temperature of a specific area. Therefore, it is important to understand the dominant thermal conduction path between the die and the sensor's surroundings or environment. Heat is conducted primarily through two paths: through the die attach pad (DAP) connected to the package or through the package lead pins. The DAP, if present, provides the most dominant thermal conduction path between the PCB and the die.
Package with DAP
If the package type does not include a DAP, the leads and pins provide the primary thermal path.
Package without DAP
The mold compound provides an additional thermal path, but due to its low thermal conductivity, any heat transfer through the mold compound itself is slower than heat transfer through the leads or DAP.
Thermal response
The package type determines how quickly the temperature sensor responds to temperature changes. The following graph shows the relative thermal response rates of selected surface mount technology package types for different categories of temperature measurement.
Packages without mold compound (chip scale package, die size ball grid array package) and packages with DAP (quad flat no-lead [QFN] package, double flat no-lead [DFN] package) are designed for applications that require fast heat transfer from the PCB, while packages without DAP are designed for applications that require a slower response rate. The fast thermal response rate allows the temperature sensor to respond quickly to any temperature changes, providing accurate readings.
Design Guidelines - Bottom Mount
The sensor should be located as close as possible to the heat source to be monitored. Avoid perforations or cuts in the PCB between the heat-generating IC and the temperature sensor, as this may slow or prevent thermal response. If possible, mount the temperature monitor on the bottom side of the PCB directly below the heat source.
The sensor is mounted on the other side of the heat source
TI recommends using vias to quickly transfer heat from one side of the PCB to the other because vias have better copper thermal conductivity than FR-4. Use as many parallel vias or filled conduction vias as possible to transfer heat from the heat source to the temperature monitor to achieve rapid thermal equilibrium between the two ICs. QFN or DFN packages with DAP can help further shorten the thermal resistance path between the vias and the sensor die.
Design Criteria - Ground Considerations
If it is not practical or cost-effective to place the temperature sensor on the other side of the heat source, place it on the same side as close to the heat source as possible.
Shared ground helps achieve thermal balance
The most effective way to establish thermal equilibrium between the heat source and the temperature monitor is to use a ground formation. A solid ground formation should be used that extends from the heat source to the temperature sensor.
in conclusion
Temperature monitoring is critical in PCB designs with thermoelectric areas or high-power ICs. The choice of local temperature sensor must be evaluated to see if it meets the system requirements and protection scheme of the design in question.
Sensor location and high thermal conductivity paths should be considered to establish rapid thermal equilibrium between the sensor and the heat generating element.
Click here to quickly locate the TI analog column and view the latest and most comprehensive information on TI sensor products. At the same time, in the next few articles, we will focus on the design considerations of various applications, evaluate the trade-off between temperature accuracy and application size, and discuss sensor placement methods.
Previous article:HARTING Han® 1A, compact and smaller than "small"
Next article:Temperature Problems Solved for You (III) High-Performance Processor Mold Temperature Monitoring
Recommended ReadingLatest update time:2024-11-15 08:16
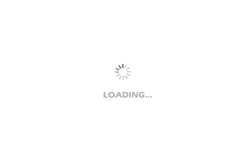
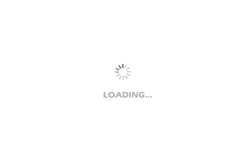
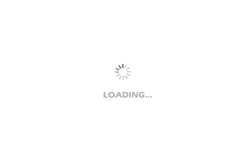
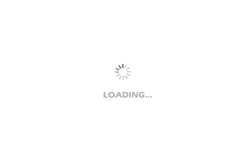
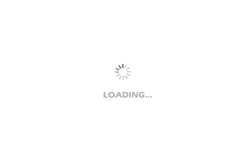
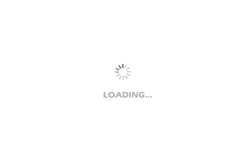
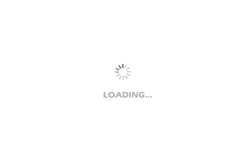
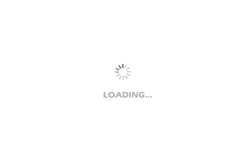
- Popular Resources
- Popular amplifiers
- CGD and Qorvo to jointly revolutionize motor control solutions
- Advanced gameplay, Harting takes your PCB board connection to a new level!
- Nidec Intelligent Motion is the first to launch an electric clutch ECU for two-wheeled vehicles
- Bosch and Tsinghua University renew cooperation agreement on artificial intelligence research to jointly promote the development of artificial intelligence in the industrial field
- GigaDevice unveils new MCU products, deeply unlocking industrial application scenarios with diversified products and solutions
- Advantech: Investing in Edge AI Innovation to Drive an Intelligent Future
- CGD and QORVO will revolutionize motor control solutions
- Focusing on promoting innovation and transformation, UHV field creates more possibilities in the era of clean energy
- Infineon Technologies Launches SECORA™ Pay Green, World’s First Contactless Payment Card Technology, Reducing Plastic Waste by Up to 100%
- LED chemical incompatibility test to see which chemicals LEDs can be used with
- Application of ARM9 hardware coprocessor on WinCE embedded motherboard
- What are the key points for selecting rotor flowmeter?
- LM317 high power charger circuit
- A brief analysis of Embest's application and development of embedded medical devices
- Single-phase RC protection circuit
- stm32 PVD programmable voltage monitor
- Introduction and measurement of edge trigger and level trigger of 51 single chip microcomputer
- Improved design of Linux system software shell protection technology
- What to do if the ABB robot protection device stops
- CGD and Qorvo to jointly revolutionize motor control solutions
- CGD and Qorvo to jointly revolutionize motor control solutions
- Keysight Technologies FieldFox handheld analyzer with VDI spread spectrum module to achieve millimeter wave analysis function
- Infineon's PASCO2V15 XENSIV PAS CO2 5V Sensor Now Available at Mouser for Accurate CO2 Level Measurement
- Advanced gameplay, Harting takes your PCB board connection to a new level!
- Advanced gameplay, Harting takes your PCB board connection to a new level!
- A new chapter in Great Wall Motors R&D: solid-state battery technology leads the future
- Naxin Micro provides full-scenario GaN driver IC solutions
- Interpreting Huawei’s new solid-state battery patent, will it challenge CATL in 2030?
- Are pure electric/plug-in hybrid vehicles going crazy? A Chinese company has launched the world's first -40℃ dischargeable hybrid battery that is not afraid of cold
- EEWORLD University ---- Practical Projects for IoT Embedded Engineers
- AC 220v to DC 24v (LM7824CT)
- Today's live broadcast! How to design high-performance servo drives using Infineon IGBT7
- STM32MP157A-DK1 Evaluation + HelloWorld and GPIO (2)
- Design Guide for RF Impedance Matching: Playing with the Smith Chart
- The difference between VCC, VDD, VEE and VSS in the circuit
- Recommendation: Displacement Sensor Selection
- What are the methods for upgrading the msp430 microcontroller program?
- c8051f040 can communication
- I accidentally saw such a board. Let's see what the chip is packaged in.